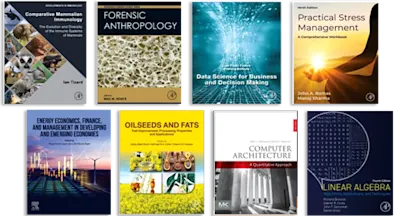
Abbreviated Guide
Pneumatic Conveying Design Guide
- 1st Edition - May 12, 2014
- Imprint: Butterworth-Heinemann
- Author: David Mills
- Language: English
- Paperback ISBN:9 7 8 - 0 - 4 0 8 - 0 4 7 3 1 - 9
- eBook ISBN:9 7 8 - 1 - 4 8 3 1 - 8 2 8 0 - 3
Abbreviated Guide: Pneumatic Conveying Design Guide describes the selection, design, and specification of conventional pneumatic conveying systems. The design procedure uses… Read more
Purchase options
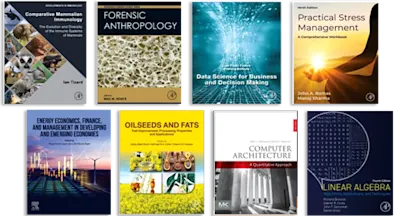
Abbreviated Guide: Pneumatic Conveying Design Guide describes the selection, design, and specification of conventional pneumatic conveying systems. The design procedure uses previous test data on the materials to be conveyed. The book also discusses system economics, operating costs, the choice of appropriate components or systems, system control, and system flexibility. The design system involves the type of conveying system for installation, the pipeline parameters, and also the plant components. System selection covers the properties of the material to be conveyed, plant layout, material properties, as well as whether an open system or a closed system is more appropriate. In pipeline design, the engineer should consider the bore of the pipeline, the air requirements in terms of delivery pressure and volumetric flow rate. Based on this data, he can determine the rating of the air mover to achieve the optimal material flow rate. From the pipeline design study, the engineer can then evaluate all the necessary operating parameters at each pipeline bore to identify plant component specifications. He can then compute for the costs of the components and operating costs of the system. Engineers, technicians, and investigators involved in industrial pneumatic conveyance will find the book highly useful.
1.1. Introduction 1.1.1. Decision Stages 1.1.2. System Selection [Ch. 2, 4, 10, 14] 1.1.3. Pipeline Design [Ch. 5, 9] 1.1.4. Specification of Components1.2. System Selection [Ch. 2, 4, 10, 14] 1.2.1. General 1.2.2. Closed Systems 1.2.3. Open Systems [Ch. 12] 1.2.4. Positive Pressure Systems [Ch. 2] 1.2.5. Negative Pressure (Vacuum) Systems [Ch. 2, 3] 1.2.6. Combined Negative and Positive Pressure Systems [Ch. 6] 1.2.7. Dual Negative and Positive Pressure Systems 1.2.8. Innovatory Systems [Ch. 2, 12]1.3. Pipeline Design 1.3.1. General 1.3.2. Conveying Air Velocity [Ch. 6] 1.3.2.1. Conveying Line Inlet Air Velocity 1.3.2.2. Volumetric Air Flow Rate 1.3.2.3. Conveying Line Inlet Air Pressure 1.3.2.4. The Influence of the Conveying Variables 1.3.3. Logic Diagrams [Ch. 5] 1.3.3.1. Material Conveying Characteristics [Ch. 4, 7] 1.3.4. Using a Logic Diagram [Ch. 5] 1.3.4.1. Specify Mass Flow Rate of Material (mp) 1.3.4.2. Specify Conveying Distance [Ch. 9] 1.3.4.3. Material Conveying Characteristics [Ch. 7, 9] 1.3.4.4. Scale to Distance and Geometry [Ch. 9, 14] 1.3.4.5. Can Material Mass Flow Rate be Achieved? 1.3.4.6. Calculate Power Requirements of Air Mover [Ch. 5, 6, 14] 1.3.4.7. Scale to Different Pipeline Bore [Ch. 5, 9, 14] 1.3.4.8. Specify Pipeline Bore 1.3.4.9. Specify Air Requirements [Ch. 6] 1.3.4.10. Delivery Pressure [Ch. 1, 3, 9, 10] 1.3.5. Choice of Air Mover [Ch. 6] 1.3.5.1. Power Requirements 1.3.6. Other Considerations 1.3.6.1. System Uprating [Ch. 11] 1.3.6.2. Alternative Conveying Distances [Ch. 5] 1.3.6.3. Alternative Materials [Ch. 5]1.4. Specification of Components [Ch. 2, 3, 6] 1.4.1. General 1.4.2. Economic Considerations [Ch. 14] 1.4.3. Mode of Operation 1.4.4. Material Feeding Devices [Ch. 3] 1.4.4.1. Selection Considerations [Ch. 10] 1.4.4.2. Types of Feeding Device [Ch. 2, 3] 1.4.5. Air Mover [Ch. 6] 1.4.5.1. Specification of Air Requirements 1.4.5.2. Choice of Air Mover 1.4.5.3. Control Requirements 1.4.5.4. Use of Plant Air 1.4.5.5. Positive Pressure Systems [Ch. 2] 1.4.5.6. Negative Pressure (Vacuum) Systems [Ch. 2] 1.4.5.7. Combined Negative and Positive Pressure Systems [Ch. 2] 1.4.6. Gas-Solid Separation System [Ch. 3] 1.4.6.1. Choice of Gas-Solid Separation System 1.4.6.2. Gravity Settling Chambers 1.4.6.3. Cyclone Separators 1.4.6.4. Fabric Filters 1.4.6.5. System ConsiderationsAppendix A.1. Reference A. 2. Nomenclature A.2.1. Symbols A.2.2. Prefixes A.2.3. Subscripts A.2.4. Non-dimensional Group A.3. Conversion Factors A.4. Formulae A.5. IllustrationsPneumatic Conveying Design Guide IndexIndex
- Edition: 1
- Published: May 12, 2014
- Imprint: Butterworth-Heinemann
- Language: English
DM
David Mills
David Mills has worked in the field of pneumatic conveying for over forty years. From 1998 – 2006 he was Professor of Bulk Solids Handling at Glasgow Caledonian University. He has published over 170 papers in the field, and has been working as an independent consultant in pneumatic conveying since 1996.
Affiliations and expertise
Independent Consultant on Pneumatic Conveying, UKRead Abbreviated Guide on ScienceDirect