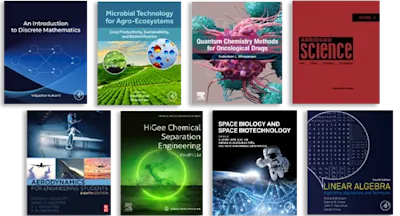
Weld Quality: The Role of Computers
Proceedings of the International Conference on Improved Weldment Control with Special Reference to Computer Technology Held in Vienna, Austria, 4–5 July 1988 under the Auspices of the International Institute of Welding
- 1st Edition - February 16, 2016
- Author: Sam Stuart
- Language: English
- Paperback ISBN:9 7 8 - 1 - 4 8 3 1 - 1 4 4 2 - 2
- eBook ISBN:9 7 8 - 1 - 4 8 3 1 - 4 6 8 4 - 3
Weld Quality: The Role of Computers documents the proceedings of the International Conference on Improved Weldment Control with Special Reference to Computer Technology, held in… Read more
Purchase options
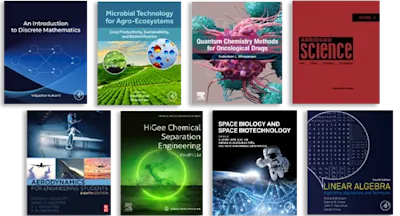
Weld Quality: The Role of Computers documents the proceedings of the International Conference on Improved Weldment Control with Special Reference to Computer Technology, held in Vienna, Austria, 4-5 July 1988, under the auspices of the International Institute of Welding. The topics of the four sessions are: (I) Design, Calculation and Prediction Models For Metallurgical Processes/Conception; (II) Inspection and In-Service Monitoring; (III) Fabrication, Quality Assurance; and (IV) Expert Systems, Data Banks and Future Possibilities. Session I includes papers on the use of computer technology to establish the quality of the welded joints; computer-aided design system for design of fillet welds with optimum shape; and the use of numerical simulation software for predetermination and optimization of the mechanical resistance of brazed joints. The papers in Session II cover topics such as acoustic emission testing; eddy current inspection system for weld testing; and holographic imaging of weld cracks. Session III includes papers on a computer controlled friction welding system and a CAQ-system for welding workshops. The presentations in Session IV include an approach for writing conventional software and expert systems for welding engineers and an expert system for robotic welding.
Preface
Foreword
List of Papers
Session I Design, Calculation and Prediction Models for Metallurgical Processes
I.1 Improved Weld Quality with Special Reference to Computer Technology. The Design Function
Abstract
Introduction
The Process of Design
Sources of Uncertainty in Experimental Results
Sources of Uncertainty in Practice
Provision of Design Data by Computer Technology
Expert Systems in Design
Conclusion
References
I.2 Computer-Aided Design System for Fillet Welded Joints
Introduction
Conclusions
References
I.3 Design Stress for Plate and Shell Welded Connections: Concept, Definition and Improvement
Abstract
Keywords
Introduction
Stress Analysis
Stress Concentration and Hot Spot Stress
Computer, Numerical Analysis and Design Stress
Conclusion
References
I.4 Optimization by Numerical Simulation of the Brazed Joint's Mechanical Resistance
Abstract
Keywords
I - Data
II - Method of Analysis
III - Brazed Assembly in Plane Stresses: Extremely Thin Joint
IV - Asymmetrical, Hypothesis, and Data
V - Brazed Joint Where the Joint is Parallel to the Stresses
I.5 Mathematical Description of HAZ Behavior of Low-Alloyed Structural Steels
Abstract
Keywords
Introduction
HAZ-Simulation Studies on Low-Alloyed Steel Type 19MnA16
HAZ-Description Using Parametric Equations
Mathematic Modeling of the Microstructural Changes in the HAZ
Discussion and Conclusions
References
I.6 Weld Formation Simulation and Optimization of Stainless Steel Automatic Argon Tungsten Arc Welding Conditions
Conclusions
References
I.7 A Computer Model for Estimating the Risk of Sensitization When Welding Stainless (18/8) Steels
Abstract
Keywords
Introduction
Heat Transfer during Welding
Sensitization Damage Parameter
Computer Solution and Results
References
I.8 The Design of Submerged Arc Weld Deposits for High-Strength Steels
Abstract
Keywords
Introduction
Experimental
Results and Discussion
Conclusions
Acknowledgments
References
Session II Inspection and in-Service Monitoring
II.1 Acoustic Emission Testing (AET) Experience with an Integral Nondestructive Inspection Method for Pressure Vessels
Abstract
Keywords
Introduction
Inspection System
Application of Technology
From TÜV Vienna Performed Tests
Conclusion
References
II.2 Computer Aided Design of Eddy Current Weld Inspection, Optimization of a Multifrequency Approach
Abstract
Keywords
Introduction
2. Principle of the Eddy Current Method
3. Eddy Current Procedures
References
II.3 Holographic Imaging of Cracks in Welds
Abstract
Keywords
Introduction
The Concept of Holography: Backpropagation of Scalar Wavefields
Holographic Imaging with Elastic Waves
References
II.4 Robot for Real Time Radiographic Inspection of Circonferential Weld with Computer Processing of the Whole System
Abstract
Introduction
Inconvénients de la Radiographie Conventionnelle
Contraintes Liees a l'Implantation de la Radioscopie sur Barge de Pose
Description du Systeme de Controle
Resultats
Session III Fabrication, Quality Assurance
III.1 Development of a Microprocessor-Based System to Determine Resistance-Spot-Weldability and Perform Electrode-Life-Tests Automatically
Abstract
Key Words
Introduction
Initial Results
Goals and Future Prospects
III.2 Friction Welding — Computer-Aided Quality Inspection
Abstract
Keywords
Introduction
Computer Controlled Friction Welding
Principles of Computer-Aided Process Monitoring
Experimentals
Conclusion
References
III.3 Support of Quality Assurance Activities and Weld Inspection by Means of Computer-Aided Data Acquisition and Documentation
Abstract
Keywords
Introduction
Possibilities of Computer-Aided Data Acquisition (CAQ)
CAQ in the Organization of Non-Automated NDE Weld Inspection
CAQ in the Production of Longitudinally Welded Stainless Steel Tubes
Session IV Expert Systems, Data Banks and Future Possibilities
IV.1 The Welding Institute Approach to Writing Information Software for Welding Engineers
Summary
Keywords
Introduction
Software Packages
Welderqual
Weldspec
Weldvol and Weldcost
Preheat
Expert Systems
Expert Systems in Welding
Future Work
References
IV.2 Base de Données Pour le Soudage Adaptatif en MIG Pulsé
Resume
Mots Cles
Introduction
Conditions Experimentales
Methodologie de Constitution de la Base de Données
Les Resultats Experimentaux
Discussion sur les Resultats
Conclusion
References
Remerciements
IV.3 Experimental Design System for Solving the Problems of Welding Operational Parameters Optimization
IV.4 Expert System Improves the Robotic Welding Procedure
Abstract
Keywords
Introduction
Possible Replacement of Welder's Tasks by Artificial Intelligence
Description of the Welding Expert System
The Expert System in the Welding Control Loop
Future Developments
Conclusions
References
IV.5 Welding Expert System: From the Welsys Experience
Abstract
Keywords
Introduction
Motivation
Aims of the Project
Organization
First Year Activities
What We Learned from the First Year Activity
Second Year Activities
What We Learned from the Second Year Activities
What We Suggest from this Experience
References
IV.6 Weldex: An Expert System for Designers
Abstract
Keywords
Introduction
Artificial Intelligence Approach for Welding Technology
System Architecture and Functional Design of "Weldex" System
Conclusion
References
Posters
Evaluation of Residual Stress States in Welded Parts — Using Ultrasonic Techniques
Abstract
Keywords
What are the Major Difficulties? - What Has Been Achieved?
References
A CAD/CAM Tool for Structural Welding
Abstract
Keywords
Introduction
Computer-Aided Design System for Estimation of Fatigue Life of Welded Joints under Low-Cycle Loading
References
Comparison of Methods for the Description of the Thermal Cycle during Welding
References
Microcomputer Control of Resistance Welding Quality
Abstract
Keywords
Introduction
Vöz-M1 Control System
References
Self-Tuning Regulator for the Selected MAG Technology Process
Abstract
Keywords
Foregoing Approach to MAG Process Control
New Approach to Process Control
Characteristics of the Selected MAG Technology
Conclusions
References
"Synchronous Welding", an Automatic Technique for MIG Welding
Abstract
Keywords
Introduction
Principle Characteristics of System
Implications
Computer Control of Welding Parameters for Improvement of Weld Quality
Abstract
Keywords
Introduction
Experimental
Discussion
References
Adaptive Control of MIG/MAG Welding — Feedback System for Weld Penetration Control
Abstract
Keywords
Adaptive Control of Pulse MIG/MAG Welding
Feedback Control of Weld Penetration (Pan, 1987b)
Reference
HPS — A High-Resolution Process-Orientated Seam Tracking System for In-Production Quality Assurance
Abstract
Keywords
Introduction
The Seam Tracking System "HPS"
Off-line Mobile Robot for Welding of Horizontal Fillets in Girder Structures
Automation in the Welding of Large Framed Cylinders
Abstract
Keywords
Introduction
Seam Tracking
System Control
Synchronous Welding
Summary
References
Recent Seam Tracking Equipment Development for Electron Beam Welding
Abstract
Keywords
Introduction
New Detector Design
Seam Tracking System
References
S.A.O. MIG-MAG: Prise en Compte des Phénomènes de Transfert D'arc
Resume
Mots Cles
Introduction
Description et Fonctionnement du Systeme
Exemples d'Application
Conclusion
The Development of a Microcomputer-Based Control System of the Machine for Ultra Thin Sheets Welding
Abstract
Keywords
Introduction
Constitution and Function of the Control System
Software Design and Debugging
Elimination of the HF Interference
Conclusions
References
Adjustment of Model of Arc Sensor for Adaptive Welding Robot
References
Development of an Automated Process Control for Mechanized Underwater Welding
Abstract
Keywords
Introduction
Description
Mode of Operation
Preliminary Experiments
Nondestructive Residual Stress and Hardness Evaluation at Weldments by Means of 3MA (Micromagnetic, Multiparameter, Microstructure and Stress Analysis)
Abstract
Keywords
3MA Testing Unit. Theorie of Operation
What Has Been Achieved? Difficulties
References
Alok-an Automated ut-System with Microprocessor Controlled Data Acquisition, Signal Processing and Computer Aided Defect Reconstruction — Applications in Weld Inspection
Abstract
Keywords
Introduction
Data Acquisition and Compression
Data Evaluation
Polyscope: Measuring System Developed for the Characterization of Weld Defects
Abstract
Introduction
Materiel Mis en Oeuvre et Logiciels
Fonctionnement
Conclusion
References
Quality Monitoring and Control System for Resistance Spot Welding Process
Abstract
Keywords
Instruction
System Hardware
System Software
System Functions
Experiments for Welding Procedures
Contrôle de la Qualité en Temps Réel dans la Domaine du Soudage par Résistance
Resume
Mots Cles
Introduction
1) Causes de "Non Qualite"
2) Moyens de Maintenir un Niveau de Qualite Acceptable
3) Principe de Controle de Qualite en Temps Reel
4) Les Applications en Production
5) Techniques Auto-Adaptatives, Qualite et Limite
Ultrasonic Weld Inspection with Synthetic Aperture Focusing Techniques (SAFT)
Abstract
Keywords
Introduction
Test Facilities
Experiments
Expert System Welda: A Welding Design Advisor for Trial Manufacture
Abstract
Keywords
Outline of the System
Rules and Control
Knowledge-Based Systems for Flaw Assessment
Abstract
Keywords
Introduction
A Text Animator for the New PD 6493
Charpy/Fracture Toughness Correlations for Ferritic Steels
Discussion
Investigation of Potential Application of Television in Microprocessor Systems for Consumable-Electrode Arc Welding Control
Conclusions
A New Type of TIG Welding Power Source with Artificial Intelligence
Abstract
Study on Real Time Quality Control of Resistance Spot Welding
Author Index
Subject Index
- Edition: 1
- Published: February 16, 2016
- Language: English
SS
Sam Stuart
Dr. Sam Stuart is a physiotherapist and a research Fellow within the Balance Disorders Laboratory, OHSU. His work focuses on vision, cognition and gait in neurological disorders, examining how technology-based interventions influence these factors. He has published extensively in world leading clinical and engineering journals focusing on a broad range of activities such as real-world data analytics, algorithm development for wearable technology and provided expert opinion on technology for concussion assessment for robust player management. He is currently a guest editor for special issues (sports medicine and transcranial direct current stimulation for motor rehabilitation) within Physiological Measurement and Journal of NeuroEngineering and Rehabilitation, respectively.
Affiliations and expertise
Senior Research Fellow, Department of Sport, Exercise and Rehabilitation, Northumbria University, UK
Honorary Physiotherapist, Northumbria Healthcare NHS Foundation Trust, North Shields, UKRead Weld Quality: The Role of Computers on ScienceDirect