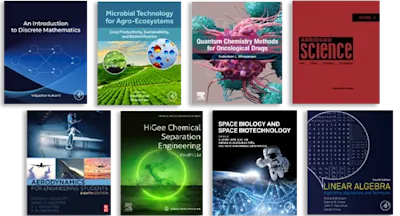
Vacuum Deposition onto Webs, Films and Foils
- 2nd Edition - June 21, 2011
- Author: Charles Bishop
- Language: English
- eBook ISBN:9 7 8 - 1 - 4 3 7 7 - 7 8 6 8 - 7
Roll-to-roll vacuum deposition is the technology that applies an even coating to a flexible material that can be held on a roll and provides a much faster and cheaper method of bu… Read more
Purchase options
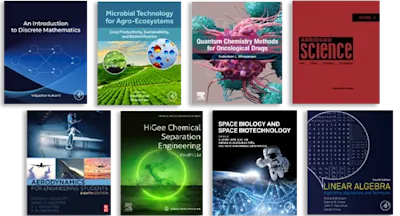
Roll-to-roll vacuum deposition is the technology that applies an even coating to a flexible material that can be held on a roll and provides a much faster and cheaper method of bulk coating than deposition onto single pieces or non-flexible surfaces, such as glass.
This technology has been used in industrial-scale applications for some time, including a wide range of metalized packaging (e.g. snack packets). Its potential as a high-speed, scalable process has seen an increasing range of new products emerging that employ this cost-effective technology:
- solar energy products are moving from rigid panels onto flexible substrates, which are cheaper and more versatile
- in a similar way, electronic circuit ‘boards’ can be produced on a flexible polymer, creating a new range of ‘flexible electronics’ products
- flexible displays are another area of new technology in vacuum coating, with flexible display panels and light sources emerging
Charles Bishop has written this book to meet the need he identified, as a trainer and consultant to the vacuum coatings industry, for a non-mathematical guide to the technologies, equipment, processes and applications of vacuum deposition. His book is aimed at a wide audience of engineers, technicians and production management. It also provides a guide to the subject for sectors in which vacuum deposition is a novel technology, such as solar energy and flexible electronics.
- Bishop’s non-mathematical explanation of vacuum deposition technologies will empower a wide range of technicians, production managers and engineers in related disciplines to improve performance and maximize productivity from vacuum coating systems
- Provides the knowledge and understanding needed to specify systems more effectively and enhance the dialogue between non-specialists and suppliers / engineers
- Provides those in the rapidly expanding fields of solar energy, display panels and flexible electronics with the know-how to unlock the potential of vacuum coating to transform their processes and products
Professionals and practitioners in the vacuum coating / vacuum metalizing industry: Engineers and technicians (systems, quality, process, maintenance), production managers, machinery designers and engineers and vendor sales and tech support staff. Engineers and managers in the main industry sectors utilizing vacuum coating: food packaging, electronics, pigment manufacturing, solar energy. Recommended reading for university courses dealing with vacuum deposition: vacuum deposition, surface engineering, vacuum engineering and applications, display technology, thin film processes and characterization
Preface
1. What Is a Vacuum?
1.1. What Is a Vacuum?
1.2. What Is a Gas?
1.3. Pressure
1.4. Partial Pressure
1.5. Vapor Pressure
1.6. Saturated Vapor Pressure
1.7. Why Do We Need a Vacuum?
1.8. Mean Free Path
2. Products Using Vacuum Deposited Coatings
2.1. Metallized Packaging Film
2.2. Capacitor Films
2.3. Optical Data Storage Tapes
2.4. Holographic Coatings
2.5. Flake Pigments
2.6. Barrier Coatings
2.7. Transparent Conducting Oxides
2.8. Energy Conservation Windows
2.9. Solar Cells
2.10. Solar Absorbers
2.11. Flexible Circuits
2.12. Optical Variable Devices
2.13. Magnetic Electronic Article Surveillance Tags
2.14. Pyrotechnics
2.15. Thin Film Batteries
3. Pressure Measurement
3.1. Bourdon Gauge
3.2. Pirani and Thermocouple Gauges
3.3. Capacitance Manometer
3.4. Penning or Cold Cathode Ionization Gauge
3.5. Ion or Hot Cathode Ionization Gauge
4. Pumping
4.1. Rotary or Roughing Pumps
4.2. Roots Pumps or Blowers
4.3. Diffusion Pumps
4.4. Turbomolecular Pumps
4.5. Getter or Sputter Ion Pump
4.6. Cryopumps
4.7. Cryopanels
4.8. Pumping Strategy
4.9. System Pumping
4.10. Filtering
4.11. Conclusions
5. Process Diagnostics and Coating Characteristics
5.1. Reflectance (R), Transmittance (T), and Absorptance (A) Measurements
5.2. Optical Density
5.3. Conductivity/Resistivity
5.4. Online Resistance Monitoring
5.5. Transparent Conducting Coatings
5.6. Residual Gas Analyzers
5.7. Plasma Emission Monitors
5.8. Thickness
5.9. Barrier
5.10. Pinholes
5.11. Artificial Intelligence and Neural Network Control Systems
5.12. Chemometrics
5.13. Surface Energy Measurements
5.14. Emissivity
5.15. Lambda Probe/Sensor/Gauge
5.16. X-ray Fluorescence Sensor
5.17. Atomic Absorption Spectroscopy
6. Leaks, Water Vapor, and Leak Testing
6.1. Real Leaks
6.2. Imaginary Leaks
6.3. Outgassing and Water Vapor
6.4. Leak Detection
7. Mass Spectrometers, Helium Leak Detectors, and Residual Gas Analyzers
8. Substrates and Surface Quality
8.1. Substrates
8.2. Polymer Surface Quality
8.3. Polymer Substrate Cleaning
8.4. Polymer Surface Etching
8.5. Higher Specification Polymer Substrates
8.6. Metal Web and Surface Quality
8.7. Metal Surface Contamination and Cleaning
8.8. Paper
8.9. Foams, Nonwovens, and Textiles
8.10. Cores
8.11. Packaging
8.12. Cost Benefit
9. Adhesion and Adhesion Tests
9.1. The “Sellotape” Test
9.2. Adhesion Tests
9.3. Adhesion and Surface Analysis
10. Surface Treatment of Webs and Foils
10.1. Atmospheric Treatments
10.2. Cleaning and Sealing
10.3. Cleaning
10.4. System Design Considerations
11. Polymer Coating Basic Information
11.1. Polymer Coating Processes
11.2. Coating Options
11.3. Radiation Cured Polymers—Acrylates
11.4. Comments
12. Nucleation, Coalescence, and Film Growth
12.1. Thin Film–Thick Film
12.2. Nucleation
12.3. Coalescence
12.4. Network and Percolation Threshold
12.5. Holes
12.6. Film Growth
12.7. Energy
12.8. Electrical and Optical Performance
12.9. Nodule Formation
12.10. Crystal Structure
12.11. Deposition Rules of Thumb
13. Pattern Metallization
13.1. Atmospheric Patterning
13.2. In-Vacuum Patterning
14. The DC Glow Discharge or Plasma
14.1. The Townsend Discharge
14.2. The Breakdown Voltage
14.3. The Transition Region
14.4. The Normal Glow Discharge
14.5. The Abnormal Glow Discharge
14.6. The Arc
14.7. Triodes and Magnetically Enhanced Plasmas
15. Electron Beam (E-beam) Evaporation
15.1. Filaments and Electron Emission
15.2. E-beam Control
15.3. Power Supply
15.4. Crucibles and Feed Systems
15.5. System Design
16. Thermal Evaporation
16.1. Boats
16.2. Wire Feeding
16.3. Wire
16.4. Spitting and Pinholes
16.5. Thin Film Measurement
16.6. Power Supplies and Control
16.7. Coating Uniformity
16.8. Coating Strategy
16.9. Reactive Thermal Evaporation of Aluminum Oxide
17. Radiant-Heated, Induction-Heated, and Other Sources
17.1. Radiant-Heated Sources
17.2. Radiation Shields
17.3. Induction-Heated Sources
17.4. Magnetic Levitation Aluminum Deposition Source
17.5. Jet Vapor Sources
17.6. Molecular Beam Epitaxy Sources
18. Chemical Vapor Deposition/Polymerization onto Webs
18.1. Substrate Temperature
18.2. Power
18.3. Pressure
18.4. Substrate Bias
18.5. Fluorinated Plasma Polymerization
18.6. Carbon–Fluorine Plasmas
18.7. CVD of Barrier Coatings
18.8. Atmospheric Plasma Deposition
19. Atomic Layer Deposition
20. Magnetron Sputtering Source Design and Operation
20.1. DC Planar Magnetron Sputtering Source
20.2. Balanced and Unbalanced Magnetron Sputtering
20.3. Anodes
20.4. Radio Frequency Sputtering
20.5. Arcing and Control of Arcs
20.6. Water Cooling
20.7. End Effects
20.8. Troubleshooting Magnetron Sputtering Sources
21. Magnetron Sputtering Source Design Options
21.1. Single or Dual Magnetron Sputtering Source
21.2. Anode Included or Not
21.3. Balanced or Unbalanced Magnetic Fields
21.4. Fixed or Variable Magnetic Performance
21.5. Internal or External Fitting
21.6. Direct or Indirect Cooling
21.7. Single or Multiple Materials
21.8. Linked or Isolated Cathodes
21.9. Cost Implications
21.10. Coating Uniformity
21.11. Magnets
21.12. Planar or Rotatable?
21.13. Power Supply Choices
22. Reactive Sputter Deposition
22.1. Target Preconditioning
22.2. Control Options
22.3. Hysteresis Loop
22.4. Monitors
22.5. Time Constants
22.6. Pumping
22.7. Control of Arcs
22.8. RF Sputtering
22.9. Other Processes
23. Machine Specification and Build Issues—Risk Analysis—Process
23.1. Risk Analysis: Process
23.2. Mistake-Proofing or Fool-Proofing
23.3. Project Management
23.4. Safety
23.5. Costs
23.6. Machine Specification
23.7. Maintenance and Spares
24. Heat Load on the Webs/Foils
24.1. Introduction
24.2. Cooling Webs
24.3. Free Span Deposition
24.4. Heated Substrates
24.5. Potential Winding Problems
24.6. Characteristic Winding Problems Associated with Too Much Heat
24.7. Heating Webs
25. Process Variables
25.1. Drum Surface Roughness
25.2. Polymer Surface Roughness
25.3. Material Properties
25.4. Deposition Rate and Winding Speed
25.5. Water Content of Polymer
25.6. Drum Temperature
25.7. Single or Double Side Coating
25.8. Source Type
25.9. Heat Load Calculations
25.10. Heat Transfer Coefficient
26. Mechanical Design
26.1. Pumping
26.2. Nonuniform Pumping
26.3. Shields
27. Winding Webs in Vacuum
27.1. System Design
27.2. Tension Measurement: Load Cells
27.3. Alignment and Spacing
27.4. Materials
27.5. Other Related Items and Materials
27.6. Substrates: Thermally and Dimensionally Variable
27.7. Safety
27.8. Key Points on Winding
28. Machine Building Trends
28.1. Metallizers
28.2. Speciality Vacuum Coaters
29. System Design
29.1. System Choices
29.2. Batch Versus Air-to-Air Processing
29.3. Source Choices
29.4. Summary
30. Hazards
30.1. Risk Assessment
30.2. Mechanical
30.3. Electrical
30.4. Thermal
30.5. Chemical
30.6. Material Interactions
30.7. Deposition Material and By-products
30.8. Hazardous Gases
30.9. Cold Traps and Cryopumps
30.10. Cleaning Hazards
30.11. Ergonomic and Miscellaneous
31. Troubleshooting
31.1. Troubleshooting Vacuum
31.2. Troubleshooting Process
31.3. Troubleshooting Winding Problems
31.4. Troubleshooting Adhesion
31.5. Troubleshooting—Loss of Barrier
31.6. Troubleshooting—Common Problems and Diagnostic Tools
31.7. Thermal Evaporation by Resistance-Heated Boats
31.8. Electron Beam Deposition
31.9. Magnetron Sputtering
32. Final Thoughts
Index
- Edition: 2
- Published: June 21, 2011
- Language: English
CB