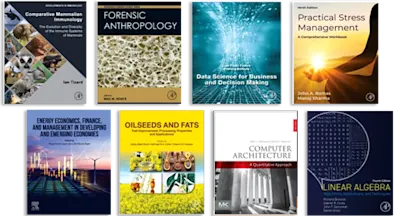
Unit Operations in Cane Sugar Production
- 1st Edition, Volume 4 - October 22, 2013
- Imprint: Elsevier Science
- Author: J.H. Payne
- Language: English
- eBook ISBN:9 7 8 - 1 - 4 8 3 2 - 8 9 7 5 - 5
An indispensable, practical guide for everyone involved in the processing of sugar cane. Confined to essentials, the book is a compact and concise delineation of the unit… Read more
Purchase options
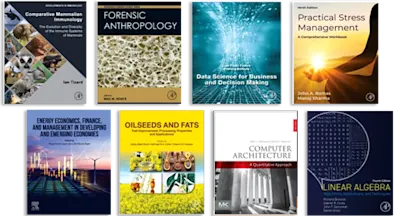
An indispensable, practical guide for everyone involved in the processing of sugar cane. Confined to essentials, the book is a compact and concise delineation of the unit processes in the manufacture of raw sugar from sugar cane, giving recommended procedures for achieving optimum results.
PrefaceAcknowledgmentsChapter 1. Factory Control Procedures Schedule for Measuring, Sampling and Analysis Daily Report Form Weekly Report Form Recovery and Loss FormChapter 2. Cane Cleaning Thinning Rock, Gravel and Sand Removal Schematic Diagram Washing Fibrous Trash Removal Operation Cane Salvager Efficiency of Cleaning Water Reuse Waste Disposal Losses ReferencesChapter 3. Milling Cane Preparation Two-Roll Crushers Mills Feeding Devices Overfeed Roll Underfeed Roll Pressure Feeder Two-Roll Feeder Grooving Circumferential Grooves Juice (Messchaert) Grooves Chevron Grooves Operation Mill Settings Maceration Hydraulic Loading Speed General Effects Control Juice Density Curves Mill Juice Curve, Graph ReferencesChapter 4. Diffusion Introduction Cane Preparation Juice Displacement Silver Ring Diffuser Diagram, Silver Ring Diffuser Diffuser Gradients, Graph Bagasse Dewatering Press Juice Treatment Press Juice Percolation, Graph Operation Permeability Bed Depth and Diffuser Speed Diffuser Flow Balance, Graph Cell Rupture Draft and Dilution Press Return Juice Flow Percent Fiber, Diagram Temperature Bagasse Dewatering Diffuser Flooding Control ReferencesChapter 5. Bagasse Moisture Effect on Extraction Effect on Fuel ValueChapter 6. The Impact of Extraneous Matter on Milling and Diffusion Milling DiffusionChapter 7. A Comparison of Diffusion and Milling with Respect to Recovery and LossesChapter 8. Clarification Polyelectrolytes Magnesium Oxide Phosphatation Sulfitation Juice Heaters Rotary Vacuum Filters Bagasse Fines Filter Station, Diagram Operating Action Diagram Mixing Fines with Settlings Pickup Vacuum Wash Vacuum Washing Speed Cake Pol Cake Quantity Clarifiers Flashing Settling Space Operation of Multi-Compartment Clarifiers Holdover Juice Clarified Juice Screening ReferencesChapter 9. Evaporation Multiple Effects Vapor Bleeding Capacity Operation Automatic Control Condenser and Vacuum System Condensate Removal Noncondensible Gas Scaling Entrainment Malfunctions Evaporator Calculations ReferencesChapter 10 Commercial Sugar Crystallization Vacuum Pan Crystallization A-Massecuite Purity Refractometer Solids Saturation Diagram Purity Refractometer Solids 1.2 Supersaturation Diagram Purity Refractometer Solids Boiling Point, 1.3 Supersaturation, Nomograph B-Massecuite Crystal Content and Pan Drops Vacuum Pan Design Procedures Quantity of Massecuites ReferencesChapter 11. Low Grade Sugar Crystallization Crystallization by Cooling Viscosity-Temperature Relations, Saturated Molasses, Graph Crystallizer Design Operation Continuous Crystallizer Flow Diagram Vacuum Pan Crystallization Molasses Refractometer Solids at 1.2 Supersaturation Table Vacuum Pan Design Procedures ReferencesChapter 12. Generalizations and Data on Sucrose Crystallization Generalizations Temperature Supersaturation Viscosity Purity Recirculation of Final Molasses Low Grade Seeding Seedslurry Crystal Yield Exhaustion Data Single Crystal Measurements Crystal Growth Rate, Table Effect of Purity on Crystallization Rate, Figure Variables Governing Molasses Exhaustion, Figure 3-Massecuite, 1-High Pol Sugar Boiling System, Figure ReferencesChapter 13. Centrifugation Batch Machines Commercial Sugar Low Grade Sugar Continuous Machines Commercial Sugar Low Grade Sugar Operation Batch Machines, Commercial Sugar Batch Machines, Low Grade Sugar Continuous Machines, Low Grade SugarChapter 14. Final Molasses ReferencesChapter 15. Recovery Factors 96 DA Sugar Recovery % Pol in Syrup, Table Molasses % Pol in Syrup, Table Molasses % 96 DA Sugar, TableChapter 16. Sugar Quality Pol Crystal Size and Uniformity Color Crystal Whole Sugar Filterability Moisture AshChapter 17. Sugar and Molasses Handling Sugar MolassesChapter 18. Steam Generation Boiler Design Control Boiler Efficiency Boiler Water Boiler Water Treatment Operation Bagasse Air Supply Boiler Water Oil Firing Stack Emission Bagasse Drying Fibrous Trash Fuel ReferencesChapter 19. Use of Steam Steam Pressures Steam Balance Process Steam Requirements Evaporation Juice Heating Sugar Boiling Total Process Steam Required Power Relations of Steam Operation ReferencesChapter 20. Instrumentation Indicating Instruments Temperature Pressure Flow Level Specific Purpose Instruments Controllers OperationChapter 21. Equipment Maintenance Guidelines for Maintenance Scheduling Conveyors Knives Shredder Mills Diffuser System Boilers Turbines Generators Electric Motors Gear Reducers Scales Heaters Clarifiers Filters Pans Centrifugals Crystallizers Pumps Tanks Piping Valves Fans InstrumentsChapter 22. General Rules of Thumb for Appraising Factory Operations and Operational Targets General Rules of Thumb for Appraising Factory Operations Cane Tops Fibrous Trash Bagasse Mixed Juice Filter Cake Syrup Massecuites Low Grade Sugar Sugar Final Molasses Operational Targets Cane Preparation Imbibition Bagasse Last Expressed Juice Filter Cake Syrup Massecuites Sugar Final Molasses Undetermined LossChapter 23. Cane Structure Cross Section Drawing Juice Fiber Varieties ReferencesChapter 24. Regional Variations in Sugar Cane Processing Control Milling Diffusion Clarification Sugar Boiling Steam Generation and Utilization ManpowerChapter 25. Engineering Specifications Vessels Non-Pressure Tanks Pressure Vessels Juice Heaters Evaporators Vacuum Pans Piping Valves Gate Valves Butterfly Valves Diaphragm Valves Globe Valves Check Valves Pressure Reducing Valves Control Valves Pumps Electrical Motors Low Voltage Switchgear Gears Turbines BoilersSelected Reference Books for the TechnologistIndex
- Edition: 1
- Volume: 4
- Published: October 22, 2013
- Imprint: Elsevier Science
- Language: English
Read Unit Operations in Cane Sugar Production on ScienceDirect