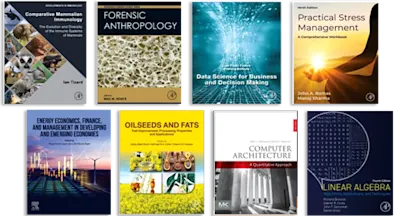
Tribology and Fundamentals of Abrasive Machining Processes
- 3rd Edition - November 16, 2021
- Imprint: William Andrew
- Authors: Bahman Azarhoushang, Ioan D. Marinescu, W. Brian Rowe, Boris Dimitrov, Hitoshi Ohmori
- Language: English
- Paperback ISBN:9 7 8 - 0 - 1 2 - 8 2 3 7 7 7 - 9
- eBook ISBN:9 7 8 - 0 - 1 2 - 8 2 3 7 7 8 - 6
This new edition draws upon the fundamentals of abrasive machining processes and the science of tribology to understand, predict, and improve abrasive machining processes. Each of… Read more
Purchase options
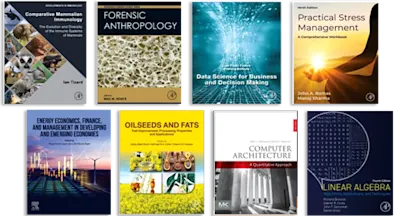
This new edition draws upon the fundamentals of abrasive machining processes and the science of tribology to understand, predict, and improve abrasive machining processes. Each of the main elements of the abrasive machining system is looked at alongside the tribological factors that control the efficiency and quality of the processes described. The new edition has been updated to include a variety of industrial applications. Grinding and conditioning of grinding tools are dealt with in particular detail, and solutions are proposed for many of the most commonly experienced industrial problems, such as poor accuracy, poor surface quality, rapid tool wear, vibrations, workpiece burn, and high process costs. The entire book has been rewritten and restructured, with ten completely new chapters. Other new features include:
- Extensive explanations of the main abrasive machining processes such as grinding (including reciprocating and creep-feed grinding, high-speed high-efficiency deep grinding, external and internal cylindrical grinding, and centerless grinding), honing, superfinishing, lapping, polishing, and finishing
- Discussions of the new classes of abrasives, abrasive tools, and bonding materials
- New case studies and troubleshooting on the most common grinding practices
- New coverage on grinding tool conditioning, mechanical dressing, and nonmechanical dressing processes
- Detailed explanations of the effects of process input parameters (such as cutting parameters, workpiece material and geometry, and abrasive tools) on process characteristics, workpiece quality, tool wear, and process parameters (such as cutting forces and temperature as well as achievable material removal rate)
- Updated topics regarding process fluids for abrasive machining and fluid delivery
Part One: Science of abrasive machining and tribology (introduction)
1. Abrasives
Bahman Azarhoushang
2. Abrasive tools
Bahman Azarhoushang
3. Abrasive machining processes
Bahman Azarhoushang
4. Tribosystems of abrasive machining processes
Amir Daneshi and Bahman Azarhoushang
Part Two: Principles of abrasive machining processes
5. Kinematics of bonded abrasive machining processes
Ali Zahedi and Bahman Azarhoushang
6. Material removal mechanisms of bonded abrasive machining (forces, friction, and energy)
Bahman Azarhoushang and Mohammadali Kadivar
7. Contact mechanics
Bahman Azarhoushang and Ali Zahedi
8. Grinding wheel macrodesign and microtopography
Bahman Azarhoushang
9. Grinding tool conditioning
Bahman Azarhoushang and Heike Kitzig-Frank
10. Principles of grinding processes
Bahman Azarhoushang and Heike Kitzig-Frank
11. Cutting temperature and energy partition in grinding
Mohammadali Kadivar and Bahman Azarhoushang
12. Kinematics and material removal mechanisms of loose abrasive machining
Mohammadali Kadivar and Bahman Azarhoushang
Part Three: Tool wear, induced surface integrity of workpiece material, and machineability of materials
13. Mechanisms of tool wear
Bahman Azarhoushang and Amir Daneshi
14. Thermal aspects of abrasive machining processes
Bahman Azarhoushang and Mohammadali Kadivar
15. Workpiece surface roughness
Bahman Azarhoushang and Amir Daneshi
16. Machineability of materials
Amir Daneshi and Bahman Azarhoushang
Part Four: Process fluids and tribochemistry of abrasive machining
17. Process fluids for abrasive machining
Bahman Azarhoushang
18. Fluid delivery
Bahman Azarhoushang
19. Tribochemistry of abrasive machining
Ali Zahedi and Bahman Azarhoushang
- Edition: 3
- Published: November 16, 2021
- Imprint: William Andrew
- Language: English
BA
Bahman Azarhoushang
IM
Ioan D. Marinescu
WR
W. Brian Rowe
BD
Boris Dimitrov
HO