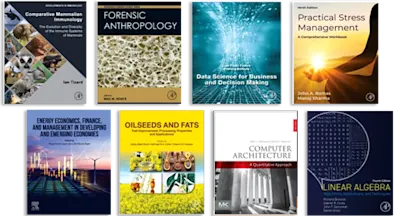
Treatise on Process Metallurgy
Volume 3: Industrial Processes
- 2nd Edition - March 18, 2024
- Imprint: Elsevier
- Editors: Seshadri Seetharaman, Roderick Guthrie, Alexander McLean, Sridhar Seetharaman, H. Y. Sohn
- Language: English
- Hardback ISBN:9 7 8 - 0 - 3 2 3 - 8 5 3 7 3 - 6
- eBook ISBN:9 7 8 - 0 - 3 2 3 - 8 5 8 9 6 - 0
Treatise on Process Metallurgy: Volume Three, Industrial Processes provides academics with the fundamentals of the manufacturing of metallic materials, from raw materials into fini… Read more
Purchase options
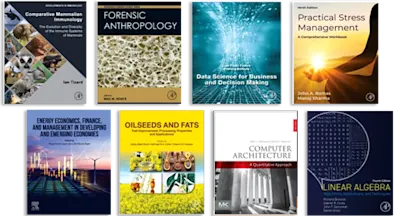
Treatise on Process Metallurgy: Volume Three, Industrial Processes provides academics with the fundamentals of the manufacturing of metallic materials, from raw materials into finished parts or products. In these fully updated volumes, coverage is expanded into four volumes, including Process Fundamentals, encompassing process fundamentals, structure and properties of matter; thermodynamic aspects of process metallurgy, and rate phenomena in process metallurgy; Processing Phenomena, encompassing interfacial phenomena in high temperature metallurgy, metallurgical process phenomena, and metallurgical process technology; Metallurgical Processes, encompassing mineral processing, aqueous processing, electrochemical material and energy processes, and iron and steel technology, non-ferrous process principles and production technologies, and more.
The work distills the combined academic experience from the principal editor and the multidisciplinary four-member editorial board.
- Provides the entire breadth of process metallurgy in a single work
- Includes in-depth knowledge in all key areas of process metallurgy
- Approaches the topic from an interdisciplinary perspective, providing broad range coverage on topics
Chapter 1: Iron and Steel Technology
1.1. Iron and Steel Making: Introduction
1.2 Ironmaking
1.3 The Direct Reduction of Iron
1.4 Hot Metal Pretreatment
1.5 Converter Steelmaking
1.6 Electric Furnace Steelmaking
1.7 Secondary Steelmaking
1.8 Inclusion Engineering
1.9 Tundish Technology
1.10 Continuous Casting of Steel
1.11 Mould Fluxes
1.12 Production of Ferroalloys
Chapter 2: Non-Ferrous Process Principles and Production Technologies
2.1 Non-Ferrous Process Principles
2.1.1 Pyrometallurgical Principles
2.1.2 Hydrometallurgical Principles
2.1.2.1 Physical Chemistry
2.1.2.2 Processing Principles
2.1.3 Principles of Biohydrometallurgy
2.1.4 Electrometallurgical Principles
2.2 Copper Production
2.2.1 Principles of Copper Production
2.2.2 Industrial Technologies for Copper Production
2.3 Nickel and Cobalt Production, Process Principles and flowsheet
2.4 Lead and Zinc Production
2.5 Aluminum Production
2.6 Silicon Production-Principles and industrial production
2.7 Rare Earth, Refractory Metals and Reactive Metal Production
2.8 Platinum Group Metals Production
- Edition: 2
- Published: March 18, 2024
- Imprint: Elsevier
- Language: English
SS
Seshadri Seetharaman
RG
Roderick Guthrie
AM
Alexander McLean
SS
Sridhar Seetharaman
Sridhar Seetharaman is the Fulton Professor of Industrial Decarbonization at Arizona State University. He received his undergraduate degree from the Royal Institute of Technology and his PHD from MIT. He is a Distinguished Member and Fellow of the Association for Iron and Steel Technology.
HS