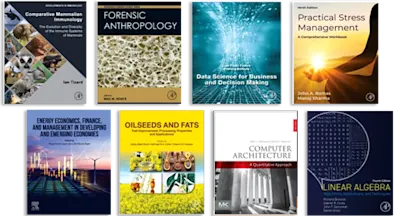
Treatise on Process Metallurgy, Volume 3: Industrial Processes
- 1st Edition - December 9, 2013
- Imprint: Elsevier
- Editor: Seshadri Seetharaman
- Language: English
- eBook ISBN:9 7 8 - 0 - 0 8 - 0 9 6 9 8 9 - 3
Process metallurgy provides academics with the fundamentals of the manufacturing of metallic materials, from raw materials into finished parts or products. Coverage is divided i… Read more
Purchase options
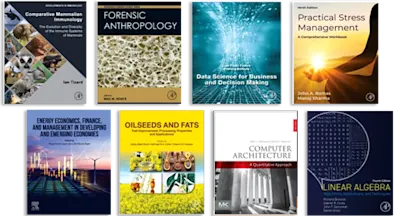
Process metallurgy provides academics with the fundamentals of the manufacturing of metallic materials, from raw materials into finished parts or products.
Coverage is divided into three volumes, entitled Process Fundamentals, encompassing process fundamentals, extractive and refining processes, and metallurgical process phenomena; Processing Phenomena, encompassing ferrous processing; non-ferrous processing; and refractory, reactive and aqueous processing of metals; and Industrial Processes, encompassing process modeling and computational tools, energy optimization, environmental aspects and industrial design.
The work distils 400+ years combined academic experience from the principal editor and multidisciplinary 14-member editorial advisory board, providing the 2,608-page work with a seal of quality.
The volumes will function as the process counterpart to Robert Cahn and Peter Haasen’s famous reference family, Physical Metallurgy (1996)--which excluded process metallurgy from consideration and which is currently undergoing a major revision under the editorship of David Laughlin and Kazuhiro Hono (publishing 2014). Nevertheless, process and extractive metallurgy are fields within their own right, and this work will be of interest to libraries supporting courses in the process area.
- Synthesizes the most pertinent contemporary developments within process metallurgy so scientists have authoritative information at their fingertips
- Replaces existing articles and monographs with a single complete solution, saving time for busy scientists
- Helps metallurgists to predict changes and consequences and create or modify whatever process is deployed
For teaching and research faculty, upper level undergraduate students, graduate students, and post-doctoral research associates in metallurgy and materials science and technology and related areas of study (physics, chemistry and biomedical science) as well as researchers and staff members of government and industrial research laboratories. Particularly useful for more experienced research workers who require an overview of fields comparatively new to them, or with which they wish to renew contact after a gap of some years.
Dedication
Preface
Editor in Chief
Co-Editors-in-Chief
Contributors to Volume 3
Acknowledgement
The Review Committee
Part A
Chapter 1. Iron and Steel Technology
Chapter 1.1. Ironmaking
Abstract
1.1.1 Introduction
1.1.2 The Ironmaking Blast Furnace
1.1.3 Iron-Bearing Materials and Additives
1.1.4 Reducing Agents
1.1.5 Counter-Current Movements of Burden and Gas
1.1.6 Blast Furnace Reactions
1.1.7 Energy Consumption and Blast Furnace Performance
1.1.8 Process Instrumentation and Control
1.1.9 Future Trends in Ironmaking
References
Chapter 1.2. The Direct Reduction of Iron
Abstract
1.2.1 Introduction
1.2.2 Raw Materials
1.2.3 DR Processes
1.2.4 Applications of DRI
1.2.5 Energy and Emissions
1.2.6 Concluding Remarks
Glossary
References
Further Reading
Chapter 1.3. Hot Metal Pretreatment
Abstract
1.3.1 Introduction
1.3.2 Desulfurization
1.3.3 Dephosphorization
1.3.4 Desiliconization
1.3.5 Influence of Hot Metal Pretreatment on Scrap Melting Capacity
1.3.6 Hot Metal Heating Device
References
Chapter 1.4. Converter Steelmaking
Abstract
1.4.1 Introduction
1.4.2 History of Development of Converter Steelmaking
1.4.3 Basic Oxygen Furnace
1.4.4 Basic Oxygen Steelmaking
1.4.5 Converter Processes for Stainless Steelmaking
1.4.6 On the Physicochemical Basis of Oxygen Steelmaking
1.4.7 Future Aspects of Oxygen Converter Process
References
Chapter 1.5. Electric Furnace Steelmaking
Abstract
1.5.1 Introduction to Electric Steelmaking
1.5.2 Raw Materials, Availability, Scrap Classes, Scrap Trading
1.5.3 Furnace Construction
1.5.4 Melting Practice and Metallurgy
1.5.5 Energy Balance of EAF Process, Electric Energy, Chemical Heating, Preheating, Postcombustion
1.5.6 Special Furnace Constructions
1.5.7 Environmental and Safety Issues
1.5.8 Future Aspects
References
Chapter 1.6. Secondary Steelmaking
Abstract
1.6.1 Introduction
1.6.2 Deoxidation
1.6.3 Desulfurization
1.6.4 Degassing
1.6.5 Decarburization
1.6.6 Dephosphorization
1.6.7 Heating
1.6.8 Alloying
1.6.9 Summarizing Discussion
References
Chapter 1.7. Inclusion Engineering
Abstract
1.7.1 Introduction
1.7.2 Nonmetallic Inclusions in Steel
1.7.3 Formation, Growth, and Removal of Inclusions
1.7.4 Inclusion Engineering in Practical Steelmaking—A Case of Ball-Bearing Steel
1.7.5 Special Methods for Ultra-Clean Steels
1.7.6 Future Trends
References
Chapter 1.8. Continuous Casting of Steel
Abstract
1.8.1 Introduction
1.8.2 Types of Continuous Casting Machines
1.8.3 Basic Equipment in Continuous Casting
1.8.4 Fundamentals of Solidification in Continuous Casting
1.8.5 Modeling of Microstructures
1.8.6 Defects
References
Chapter 1.9. How Mold Fluxes Work
Abstract
Symbols, Units, and Abbreviations
1.9.1 Introduction
1.9.2 Lubrication of Shell by Mold Flux
1.9.3 Heat Transfer in the Mold
1.9.4 Using Mold Fluxes to Adjust Process Variables
1.9.5 Effect of Casting Variables on Mold Flux Performance
1.9.6 Properties of Mold Fluxes
1.9.7 Selection of Mold Fluxes
1.9.8 Using Mold Fluxes to Minimize Defects and Process Problems
References
Chapter 1.10. Production of Ferroalloys
Abstract
Acknowledgments
1.10.1 Classification, Manufacture, and Use of Ferroalloys
1.10.2 Thermodynamics in the Production of Main Ferroalloys
1.10.3 Ferrochromium Smelting Technology
1.10.4 Reduction of Manganese Oxides and Production of Manganese Alloys
1.10.5 General Process Description
References
Chapter 2. Non-Ferrous Process Principles and Production Technologies
Chapter 2.1. Copper Production
Abstract
Nomenclature used in Section 2.1.1
Greek
Subscript
Superscript
2.1.1 Principles of Copper Production
2.1.2 Industrial Technologies for Copper Production
2.1.3 Refractories in Copper Production
Glossary used in Section 2.1.1
References
Chapter 2.2. Nickel and Cobalt Production
Abstract
2.2.1 Synopsis
2.2.2 Occurrences
2.2.3 Extraction of Nickel and Cobalt from Laterite Ores
2.2.4 Extraction of Nickel and Cobalt from Sulfide Ores
2.2.5 Production of Nickel and Cobalt from Sulfide Intermediates
2.2.6 Cobalt from Central African Copper–Cobalt Ores
2.2.7 Recovering Nickel and Cobalt from End-of-Use Scrap
2.2.8 Summary
References
Chapter 2.3. Lead and Zinc Production
Nomenclature
2.3.1 Lead Production
2.3.2 Zinc Production
References
Chapter 2.4. Process Modeling in Non-Ferrous Metallurgy
Abstract
Nomenclature
2.4.1 General Approach to Process Modeling
2.4.2 Thermodynamic Equilibrium Process Modeling
2.4.3 Reaction Engineering Models
2.4.4 CFDs Modeling
Glossary for Section 2.4.2
Glossary for Section 2.4.3
Glossary for Section 2.4.4
References
Chapter 2.5. Aluminum Production
Abstract
Nomenclature
2.5.1 Hydrometallurgy of the Bayer Process
2.5.2 Electrometallurgy of Aluminum
2.5.3 Aluminum Recycling
Glossary
References
Chapter 2.6. Silicon Production
Abstract
2.6.1 Introduction
2.6.2 Polysilicon Production Processes
2.6.3 Conclusions and Future Trends
Relevant Websites
Glossary
References
Chapter 2.7. Hydrometallurgical Processing
Abstract
Nomenclature
2.7.1 Introduction to Hydrometallurgical Processing
2.7.2 Application of Hydrometallurgical Fundamentals
2.7.3 Gold Processing
2.7.4 Copper Processing
2.7.5 Zinc Processing
Glossary
References
Chapter 2.8. Biohydrometallurgy
Abstract
Nomenclature
2.8.1 Introduction
2.8.2 Growth, Metabolism, and Kinetics
2.8.3 Mineral Degradation/Metal Extraction
2.8.4 Summary of Biohydrometallurgy Commercialization History
2.8.5 Commercially Oriented Processes for Biooxidation
2.8.6 Process and Waste Water Treatment Applications
Glossary
References
Chapter 2.9. Rare Earth, Titanium Group Metals, and Reactive Metals Production
2.9.1 Rare Earth Metals
2.9.2 Titanium Group Metals (Ti, Zr, and Hf)
2.9.3 Reactive Metals
References
Chapter 2.10. Platinum Group Metals Production
2.10.1 Introduction
2.10.2 Uses of PGMs [,]
2.10.3 Sources of Raw PGMs
2.10.4 Material Flow of PGMs
2.10.5 Smelting and Refining of PGMs
2.10.6 Recycling of PGMs
2.10.7 Conclusions
References
Part B
Chapter 3. Metallurgical Production Technology
Chapter 3.1. Process Concept for Scaling-Up and Plant Studies
Abstract
3.1.1 Introduction
3.1.2 Physical Modeling
3.1.3 Challenges in Scaling-Up of a Process in Process Metallurgy
3.1.4 Scaling-Up and Scaling-Down Operations in Process Metallurgy
3.1.5 Applications
3.1.6 Case Study One
3.1.7 Case Study Two
3.1.8 Conclusions
References
Chapter 3.2. Project Technology and Management
Abstract
3.2.1 Introduction
3.2.2 Project Identification
3.2.3 Project Feasibility Analysis
3.2.4 Choice of Technology
3.2.5 Choice of Location
3.2.6 Cost of Project
3.2.7 Appraisal Criteria
3.2.8 Social Cost–Benefit Analysis
3.2.9 Planning, Scheduling, and Resources Management
3.2.10 Challenges of a Metallurgical Project
Appendix A Project Investment Costs with a Classification
Appendix B
Appendix C Operating Costs and Revenue
Appendix D Cash Flow Projections
Appendix E Sources and Applications
Further Reading
Chapter 3.3. Metallurgical Production Plant—Energy and Environment
Abstract
Acknowledgments
3.3.1 Planning for Energy Efficiency
References
Chapter 3.4. Intellectual Property Rights and the Technology Transfer Process
Abstract
3.4.1 Introduction
3.4.2 Intellectual Property Rights
3.4.3 International Framework Governing IPR
3.4.4 Patents
3.4.5 Inventorship, Ownership, Compensation
3.4.6 Technology Transfer and Commercialization of Patents
3.4.7 Case Study 1
3.4.8 Case Study 2
Case Study 1. Extraction of Rare Earths for Advanced Applications
1 Introduction
2 The Resources
3 Extraction of Rare Earths from Minerals
4 Extraction of Rare Earth Metals
5 Applications of Rare Earths
6 The Base Rare Earth Market
7 Conclusions
References
Further Reading
Case Study 2. Ferrous Metallurgical Process Industry: Visakhapatnam Steel Plant – From Conceptualization to Commissioning
1 Introduction
2 Overview
3 Background
4 Plant Location and Project Report
5 Revised Detailed Project Report: Salient Features
6 Production Technology
7 Commissioning Sequence for Major Units of VSP
Chapter 4. Environmental Aspects and the Future of Process Metallurgy
Chapter 4.1. Sustainability
Abstract
4.1.1 Introduction
4.1.2 The Long-Term Supply of Minerals and Metals
4.1.3 The Long-Term Demand for Minerals and Metals
4.1.4 Toward Zero Waste
4.1.5 Toward Sustainability
References
Chapter 4.2. Energy Resources, Its Role and Use in Metallurgical Industries
Abstract
4.2.1 Introduction
4.2.2 Energy and Environment Relationship
4.2.3 Energy Use in Steel Plants
4.2.4 Energy Use in Aluminum Plants
4.2.5 Possible Solutions to the Problems Caused by Energy Use
4.2.6 Alternate Energy Sources for Metallurgical Use
4.2.7 Conclusions
List of Relevant Websites
References
Chapter 4.3. Methods to Evaluate Environmental Aspects of Materials
Abstract
Acronyms used in Section 4.3.1
4.3.1 Life Cycle Assessment and Related Methodologies
4.3.2 Material Flow Analysis
References
Chapter 4.4. Processes for Recycling
4.4.1 Metals from Slag
4.4.2 Retention of Metals and Metals Recovery
4.4.3 Ironmaking and Steelmaking Slags
4.4.4 Ironmaking and Steelmaking Dusts
References
Chapter 4.5. Future of Process Metallurgy
Abstract
Nomenclature Used in Section 4.5.2
Acknowledgments to Section 4.5.2
4.5.1 Control of CO2 Emission
4.5.2 Future Steelmaking Process
4.5.2.2 From Nonferrous Flash Smelting to Flash Ironmaking: Development of an Ironmaking Technology with Greatly Reduced CO2 Emissions and Energy Consumption
4.5.2.3 FINEX® Process—Process of Promise
4.5.2.4 Rotary Hearth Furnace Process
4.5.2.5 Thermodynamics of Hydrogen Iron- and Steelmaking
Glossary Used in Section 4.5.2
References
Index
- Edition: 1
- Published: December 9, 2013
- Imprint: Elsevier
- Language: English
SS