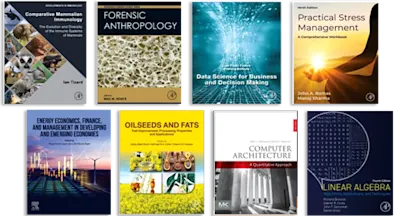
Treatise on Process Metallurgy, Volume 2: Process Phenomena
- 1st Edition - November 22, 2013
- Imprint: Elsevier
- Editor: Seshadri Seetharaman
- Language: English
- Paperback ISBN:9 7 8 - 0 - 0 8 - 1 0 1 3 4 7 - 2
- Hardback ISBN:9 7 8 - 0 - 0 8 - 0 9 6 9 8 4 - 8
- eBook ISBN:9 7 8 - 0 - 0 8 - 0 9 6 9 8 5 - 5
Process metallurgy provides academics with the fundamentals of the manufacturing of metallic materials, from raw materials into finished parts or products. Coverage is divided i… Read more
Purchase options
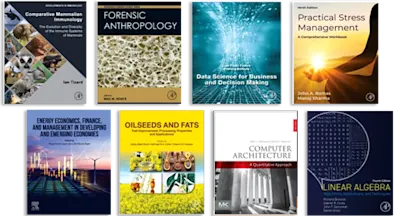
Process metallurgy provides academics with the fundamentals of the manufacturing of metallic materials, from raw materials into finished parts or products.
Coverage is divided into three volumes, entitled Process Fundamentals, encompassing process fundamentals, extractive and refining processes, and metallurgical process phenomena; Processing Phenomena, encompassing ferrous processing; non-ferrous processing; and refractory, reactive and aqueous processing of metals; and Industrial Processes, encompassing process modeling and computational tools, energy optimization, environmental aspects and industrial design.
The work distils 400+ years combined academic experience from the principal editor and multidisciplinary 14-member editorial advisory board, providing the 2,608-page work with a seal of quality.
The volumes will function as the process counterpart to Robert Cahn and Peter Haasen’s famous reference family, Physical Metallurgy (1996)--which excluded process metallurgy from consideration and which is currently undergoing a major revision under the editorship of David Laughlin and Kazuhiro Hono (publishing 2014). Nevertheless, process and extractive metallurgy are fields within their own right, and this work will be of interest to libraries supporting courses in the process area.
- Synthesizes the most pertinent contemporary developments within process metallurgy so scientists have authoritative information at their fingertips
- Replaces existing articles and monographs with a single complete solution, saving time for busy scientists
- Helps metallurgists to predict changes and consequences and create or modify whatever process is deployed
For teaching and research faculty, upper level undergraduate students, graduate students, and post-doctoral research associates in metallurgy and materials science and technology and related areas of study (physics, chemistry and biomedical science) as well as researchers and staff members of government and industrial research laboratories. Particularly useful for more experienced research workers who require an overview of fields comparatively new to them, or with which they wish to renew contact after a gap of some years.
Dedication
Preface
Editor in Chief
Co-Editors-in-Chief
Contributors to Volume 2
Acknowledgement
The Review Committee
Chapter 1. Interfacial Phenomena in High Temperature Metallurgy
Chapter 1.1. Surfaces and Interfaces
Abstract
1.1.1 Definition of Surfaces and Interfaces
1.1.2 Gibbs Adsorption Isotherm
1.1.3 Langmuir’s Isotherm
References
Chapter 1.2. Surface Tension and Contact Angle
Abstract
1.2.1 Surface Tension
1.2.2 Contact Angle
1.2.3 Wetting
References
Chapter 1.3. Experiments
Abstract
1.3.1 Sessile Drop
1.3.2 Maximum Bubble Pressure
1.3.3 Pendent Drop
1.3.4 Drop Weight
1.3.5 Detachment Method
1.3.6 Liquid Surface Contour Method
1.3.7 Capillary Rise Method
1.3.8 Levitating Drop
Appendix A Software for Evaluation of Surface Tension from Sessile Drop
References
Chapter 1.4. Surface Tension Models
Abstract
1.4.1 Modeling of Surface Tension of Liquid Pure Metals and Molten Salts
1.4.2 Modeling of Surface Tension of Liquid Alloys
1.4.3 Modeling of Surface Tension of Molten Ionic Materials Including Molten Slag
1.4.4 Evaluation of Interfacial Tension Between Liquid Steel and Molten Slag
1.4.5 Application of Constrained Gibbs Energy Minimization Approach to Evaluate Surface Tension of Liquid Alloys
References
Chapter 1.5. Interfacial Free Energy and Wettability
Abstract
1.5.1 Wettability
1.5.2 Interfacial Free Energy Between Solid and Liquid Phases in Metals and Alloys
1.5.3 Interfacial Tension Between Liquid Steel and Molten Slag
References
Chapter 1.6. Some Aspects of Electrochemistry of Interfaces
Abstract
1.6.1 Basics of Electrochemistry of Interfaces
1.6.2 Electrocapillary Phenomena
References
Chapter 1.7. Interfacial Convection and Its Effect on Material Processing
Abstract
1.7.1 Some Basics of the Interfacial Convection
1.7.2 Effect of Interfacial Flow in Liquid–Liquid Reactions
1.7.3 Effect of Interfacial Flow in Liquid–Gas Reactions
1.7.4 Effect of Interfacial Flow in Liquid–Solid Reactions
1.7.5 Effect of Interfacial Flow in Solidification Processes and Crystal Growth
References
Chapter 1.8. Stability of Interface Between Liquid Steel and Molten Slag
Abstract
References
Chapter 1.9. Applications of Interfacial Phenomena in Process Metallurgy
Abstract
1.9.1 Marangoni Flow During the Welding Process
1.9.2 Engulfing of Small Droplets of Molten Slag into Liquid Steel
1.9.3 Erosion or Dissolution of Refractories
1.9.4 Separation of Metallic Droplets from Slags
1.9.5 Engulfing Nonmetallic Inclusions and Gas Bubbles into Solidified Interface
1.9.6 Gas Bubble Formation in Liquid Steel
1.9.7 Nucleation During Solidification
1.9.8 Slag Foaming
References
Chapter 2. Metallurgical Process Phenomena
Chapter 2.1. The Importance of Metallurgical Process Phenomena
Abstract
Chapter 2.2. Kinetics of Gas–Liquid and Liquid–Liquid Reactions
Abstract
2.2.1 Introduction
2.2.2 Rate-Controlling Process
2.2.3 The Difference Between Thermodynamics and Kinetics
2.2.4 Gas-Phase Mass Transfer
2.2.5 Free Vaporization
2.2.6 Liquid-Phase Mass Transfer
2.2.7 Heat Transfer Control
2.2.8 Chemical Kinetics
2.2.9 Mixed Control
2.2.10 Concluding Remarks
References
Chapter 2.3. Bubbles in Process Metallurgy
Abstract
2.3.1 Introduction
2.3.2 Bubble Formation
2.3.3 Bubble Shapes
2.3.4 Plume Shape
2.3.5 Mixing Time
2.3.6 Bubble Rupture
2.3.7 Bubbling–Jetting Transition
2.3.8 Modeling
References
Chapter 2.4. Foams and Foaming
Abstract
2.4.1 Foaming in Metallurgical Processes
2.4.2 Foaming Index
2.4.3 Slag Foaming in Industrial Processes
References
Chapter 2.5. Applications
Abstract
2.5.1 Rate Phenomena in Direct Ironmaking
2.5.2 Ladle Desulfurization Kinetics
2.5.3 Rate Phenomena in Vacuum Degassing
2.5.4 Rate Phenomena in AOD Stainless Steel Production
2.5.5 Inclusion Flotation in Argon-Stirred Steel
References
Chapter 3. Some Applications of Fundamental Principles to Metallurgical Operations
Abstract
3.0 Introductory Comments: Some Perspectives on the Process of Innovation
References
Chapter 3.1. Some Metallurgical Considerations Pertaining to the Development of Steel Quality
Abstract
Acknowledgments
3.1.1 Introduction
3.1.2 Generation of Steel Quality
3.1.3 Preservation of Steel Quality
3.1.4 Evaluation of Steel Quality
3.1.5 Summary
References
Chapter 3.2. Refractory Corrosion During Steelmaking Operations
Abstract
3.2.1 Introduction
3.2.2 Theoretical Considerations
3.2.3 Corrosion Testing of Refractories
3.2.4 Corrosion of Oxide–Carbon Refractories
3.2.5 Summary
References
Chapter 3.3. Application of Slag Engineering Fundamentals to Continuous Steelmaking
Abstract
3.3.1 Introduction
3.3.2 Continuous Steelmaking: An Overview
3.3.3 Continuous Steelmaking Based on the Use of DRI
3.3.4 Fundamental Considerations
3.3.5 Slag Design Steps
3.3.6 Process Analysis
References
Chapter 3.4. Kinetics of Assimilation of Additions in Liquid Metals
Abstract
List of Nomenclature
Greek symbols
Subscripts
Superscripts
3.4.1 Introduction
3.4.2 Fundamentals of Assimilation
3.4.3 Routes of Assimilation
3.4.4 Exothermic Phenomena During Assimilation
3.4.5 Recovery
3.4.6 Conclusions
References
Chapter 4. Metallurgical Process Technology
Chapter 4.1. Process Kinetics, Fluid Flow, and Heat and Mass Transfer, in Process Metallurgy
Abstract
4.1.1 Theory of Fluid Flows
4.1.2 The Continuity and Momentum Equations
4.1.3 Newtonian Liquids
4.1.4 Electromagnetically Driven Flows
4.1.5 Physical Modeling
4.1.6 Physical and Computational Models
4.1.7 Computational Fluid Dynamics
References
Chapter 4.2. Turbulence Modeling and Implementation
Abstract
Nomenclature
4.2.1 Introduction
4.2.2 Turbulence Models
4.2.3 Conclusions
References
Chapter 4.3. Computational Fluid Mechanics
Abstract
Nomenclature
4.3.1 Introduction
4.3.2 Applications of CFD in Process Metallurgy
4.3.3 Conclusions
References
Chapter 4.4. Solidification
Abstract
4.4.1 Application of Textured Copper Substrates for Enhancing Heat Fluxes
4.4.2 Solidification in Conventional Fixed-Mold Machines
References
Chapter 4.5. Computational and Physical Modeling of Solidification in CCC and TSC
Abstract
4.5.1 Proposed New Mechanism for the Formation of OMs
4.5.2 Conclusions
References
Chapter 4.6. Single Phase, Two Phase, and Multiphase Flows, and Methods to Model these Flows
Abstract
Nomenclature
4.6.1 Introduction
4.6.2 Multiphase Flow Regimes
4.6.3 Example: Modeling of Inert Gas Shrouding in a Tundish (Three-Phase Flow Involving Gas Bubbles, Liquid Steel, and Slag)
References
Chapter 4.7. The Design of a New Casting Process: From Fundamentals to Practice
Abstract
4.7.1 Continuous Casting Machines for the Steel Industry
4.7.2 Fluid Flows, Solidification, and Heat Transfer in Moving Mold Machines
4.7.3 Theoretical Heat Fluxes, Based on Perfect and Imperfect, Thermal Contact
4.7.4 Solidification and Strip Microstructures in NNSC
4.7.5 Horizontal Single-Belt Casting Processes
4.7.6 Fluid Flows: Design of Metal Delivery Systems
4.7.7 The Potential of the HSBC Caster: From Fundamentals to Practice
4.7.8 Conclusions
References
Chapter 4.8. Conclusion
Abstract
Chapter 5. Computational Thermodynamics, Models, Software and Applications
Chapter 5.1. Thermodynamics
Abstract
5.1.1 Calphad Method
5.1.2 Dilute Metallic Solution
5.1.3 Model for Oxide Solid Solutions
5.1.4 The Reciprocal Ionic Liquid Model
5.1.5 Quasichemical Models
5.1.6 The Cell Model
5.1.7 The Central Atoms Model and Generalized Central Atom Model
5.1.8 The Modified Quasichemical Model
5.1.9 Modified Quasichemical Model for Matte
5.1.10 Thermodynamic Packages and Databases
References
Chapter 5.2. Slag Viscosity Model
Abstract
5.2.1 FactSage Structural Viscosity Model for Multicomponent Slag
5.2.2 Viscosity of Slags
5.2.3 Appendices
References
Chapter 5.3. Applications
Abstract
List of Symbols
Acknowledgments
5.3.1 Applications to Steelmaking ProcessES
5.3.2 Application of Advanced Modeling in Nonferrous Metallurgy
References
Chapter 5.4. Process Modeling
Abstract
List of Symbols for Section 5.4.3
5.4.1 Production of Metallurgical Grade Silicon in an Electric Arc Furnace
5.4.2 Modeling TiO2 Production by Explicit Use of Reaction Kinetics
5.4.3 Non-equilibrium Modeling for the LD-Converter
5.4.4 Simulation of the RH–OB and BOF Processes Using the Effective Equilibrium Reaction Zone Model
5.4.5 Rotary Cement Kiln Model
5.4.6 Kinetic Simulation of Ladle Refining and Smelting Using Software
References
Index
- Edition: 1
- Published: November 22, 2013
- Imprint: Elsevier
- Language: English
SS