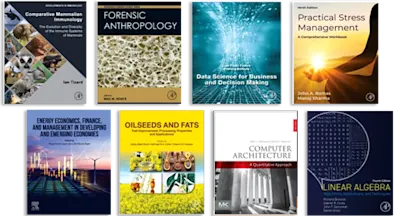
Toughening Mechanisms in Composite Materials
- 1st Edition - May 28, 2015
- Imprint: Woodhead Publishing
- Editors: Qing-Hua Qin, Jianqiao Ye
- Language: English
- Paperback ISBN:9 7 8 - 1 - 7 8 2 4 2 - 2 7 9 - 2
- eBook ISBN:9 7 8 - 1 - 7 8 2 4 2 - 2 9 1 - 4
Toughening Mechanisms in Composite Materials aims to provide a comprehensive and technically detailed coverage of composites and their toughening mechanisms. Unique in its direct… Read more
Purchase options
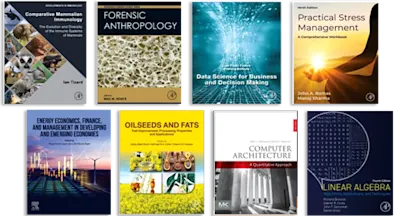
Toughening Mechanisms in Composite Materials aims to provide a comprehensive and technically detailed coverage of composites and their toughening mechanisms. Unique in its direct and comprehensive approach, the book presents fundamental knowledge on composites’ toughening mechanisms as well as a comprehensive treatment of numerical methods. This volume summarizes the current state-of-the-art and presents the most recent research outcomes in the field. It details the development of each of the techniques, beginning with basic principles, and new concepts are illustrated with examples wherever possible.
- Covers particle-reinforced composites, fibre-reinforced composites and other toughening mechanisms
- Analyses toughening mechanisms in a broad range of composite materials
- Developments in nanotube toughened composites and toughened graphene ceramic composites are examined
Professional engineers in industry and academia, research scientists, workers and students in applied mechanics and materials engineering, physicists and materials scientists.
- List of contributors
- Woodhead Publishing Series in Composites Science and Engineering
- 1: Introduction to the composite and its toughening mechanisms
- Abstract
- 1.1 Basic concepts
- 1.2 Historical developments
- 1.3 Classification and applications
- 1.4 Effective mechanical behavior of composites
- 1.5 Toughening mechanisms of composites
- Part One: Toughening mechanisms for particle-reinforced composites
- 2: Silicon nitride based ceramic composites toughened by rare-earth oxide additives
- Abstract
- Acknowledgments
- 2.1 Introduction
- 2.2 Preparing Si3N4-based ceramics and the role of RE oxide additives
- 2.3 Toughening of Si3N4-based ceramics
- 2.4 The influence of RE oxide additives on the toughening of Si3N4-based materials
- 2.5 Future trends
- 2.6 Sources of further information
- 3: Toughening mechanisms in epoxy/graphene platelets composites
- Abstract
- 3.1 Introduction
- 3.2 Graphene and its derivatives
- 3.3 Fabrication, structure, properties, and toughening mechanisms of epoxy composites containing GnPs of ~10 nm in thickness
- 3.4 Fracture mechanisms of epoxy/GnPs nanocomposites—fabricated by a thermal-sonication approach
- 3.5 Toughening mechanism of epoxy composites containing long-chain modified GnPs of ~ 3 nm in thickness
- 3.6 Fabrication, structure, property, and toughening mechanism of epoxy composites containing GnPs, which are reactively modified
- 3.7 Conclusions and challenges
- 4: Toughening mechanisms in nanoparticle polymer composites: experimental evidences and modeling
- Abstract
- 4.1 Introduction
- 4.2 Discussion on the effect of the “scale”: micro mechanisms and nano mechanisms
- 4.3 “Micro” mechanisms: crack deflection, crack pinning, and matrix deformation
- 4.4 “Nano” mechanisms: debonding, plastic void growth, and shear banding
- 4.5 Modeling the toughening improvements in nanoparticle-filled polymers
- 4.6 Conclusions
- 2: Silicon nitride based ceramic composites toughened by rare-earth oxide additives
- Part Two: Toughening mechanisms for particle-reinforced composites
- 5: Toughening mechanisms for the fiber of middle-large-aspect-ratio-reinforced composites
- Abstract
- Acknowledgments
- 5.1 Introduction
- 5.2 Computational models for materials reinforced by parallel fibers of finite length
- 5.3 Computational results, toughening mechanism, and homogenization
- 5.4 Conclusions and future trends
- 6: Damage-tolerant composite structures by Z-pinning
- Abstract
- 6.1 Introduction
- 6.2 Manufacture of Z-pinned polymer matrix composites and effects on mesostructure
- 6.3 Structure–property relationships
- 6.4 Modeling approaches for design of Z-pinned structures
- 6.5 Concluding remarks
- 7: Toughening mechanisms for whisker-reinforced composites
- Abstract
- 7.1 Introduction
- 7.2 A green whisker-reinforced cementitious composite
- 7.3 Material processing and toughening methods
- 7.4 Mechanical properties and testing
- 7.5 Effect of parameters on the mechanical properties
- 7.6 Application and future trends
- 8: Toughening mechanisms for glass fiber-reinforced polyamide composites
- Abstract
- 8.1 Introduction
- 8.2 Manufacturing conditions
- 8.3 Effect of environmental conditions
- 8.4 Impact and energy absorption properties
- 8.5 Polyamide clay/nanocomposites
- 8.6 Applications in the automotive industry
- 8.7 Conclusions
- 5: Toughening mechanisms for the fiber of middle-large-aspect-ratio-reinforced composites
- Part Three: Other toughening mechanisms for composite materials
- 9: Toughening mechanisms in Zanchor-reinforced composites
- Abstract
- 9.1 Introduction
- 9.2 Zanchor process and materials
- 9.3 Fracture behavior under mode I loading
- 9.4 Toughening mechanisms under mode I loading
- 9.5 Fracture behavior under mode II loading
- 9.6 Toughening mechanisms under mode II loading
- 9.7 Conclusions
- 10: Interlayer toughening mechanisms of composite materials
- Abstract
- Acknowledgment
- 10.1 Introduction: interlayer toughening methods
- 10.2 Materials, process, and characterization
- 10.3 How does the mechanism work?
- 10.4 Changes in mechanical behavior
- 10.5 Applications and future trends
- 11: Toughening mechanisms of nanoparticle-reinforced polymers
- Abstract
- 11.1 Introduction
- 11.2 Toughening concepts
- 11.3 Toughening in polymers
- 11.4 Toughening micromechanisms
- 11.5 Changes in mechanical properties and performances
- 11.6 Future trends
- 11.7 Concluding remarks
- 12: Toughening mechanisms in dental composites
- Abstract
- 12.1 Introduction
- 12.2 Development of dental composites
- 12.3 Future trends
- 13: Mechanical behavior of extra-strong CNT fibers and their composites
- Abstract
- Acknowledgment
- 13.1 Introduction
- 13.2 Mechanical performance of CNT composites
- 13.3 Mechanical performance of covalent CNT assemblies
- 13.4 Mechanical performance of non covalent CNT assemblies
- 13.5 Concluding remarks
- 14: Toughening mechanisms for fiber-reinforced polymer-reinforced concrete beams
- Abstract
- 14.1 Introduction
- 14.2 Experimental study of the bond mechanism between FRP and concrete
- 14.3 Numerical study of bond mechanism between FRP and concrete
- 14.4 Summary and conclusion
- 9: Toughening mechanisms in Zanchor-reinforced composites
- Index
- Edition: 1
- Published: May 28, 2015
- Imprint: Woodhead Publishing
- Language: English
Qing-Hua Qin
Dr. Qinghua Qin received his Bachelor of Engineering degree (1982) in Mechanical Engineering from Chang An University, China and obtained his Master of Science degree (1984) and PhD (1990) in applied mechanics from Huazhong University of Science and Technology (HUST), China. He joined the faculty of the Department of Mechanics at HUST from 1984 until he left for the University of Stuttgart (Germany) with the DAAD/K.C. Wong research fellowship in 1994. From 1995 to 1997, he returned to China as a postdoctoral associate at Tsinghua University.
He was awarded the Queen Elizabeth II Fellowship from the Australian Research Council (ARC) in 1997 and a Professorial Fellowship of ARC in 2002 at The University of Sydney, Australia and stayed there till December 2003. He has been a Professor at the Research School of Engineering of the Australian National University, Australia from 2004 to 2021. He is now working at the Department of Engineering, Shenzhen MSU-BIT University, China. He is also appointed a guest professor at HUST since 2000 and Tianjin University since 2006.
Affiliations and expertise
Professor, Department of Engineering, Shenzhen MSU-BIT University; International University Park Road, Longgang, Shenzhen, Guangdong, ChinaJY
Jianqiao Ye
Jianqiao Ye is Professor and Chair of Mechanical Engineering at Lancaster University, UK and a member of the Lancaster Intelligent, Robotic and Autonomous Systems Centre (LIRA).
His research covers a broad range of both academic and industrial interests, including failure and damage of fibre reinforced composites, advanced steel-concrete composite structures, geopolymer, lighter and green cementitious materials, cement and concrete carbonation, offshore oil and gas structures and vibration energy harvesting. He has worked on testing, numerical modelling and optimization of a wider range of materials and structures, which has been extended to the applications of a range of analytical instruments such as X-Ct, SEM, XRD, EDS and data-driven techniques such as metamodelling, machine learning and digital twins.
Affiliations and expertise
Professor and Chair, Mechanical Engineering, Lancaster University, UKRead Toughening Mechanisms in Composite Materials on ScienceDirect