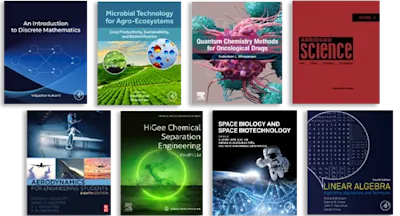
Thermoplastics and Thermoplastic Composites
Technical Information for Plastics Users
- 1st Edition - April 26, 2007
- Author: Michel Biron
- Language: English
- eBook ISBN:9 7 8 - 0 - 0 8 - 0 4 8 9 8 0 - 3
Thermoplastics represent appx 90% by weight of all plastics consumed world-wide. We know them mainly in the form of polythenes, polyolefins, polystyrenes, nylons and acrylics.… Read more
Purchase options
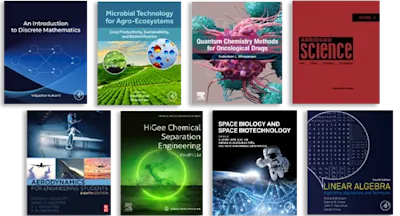
Thermoplastics represent appx 90% by weight of all plastics consumed world-wide. We know them mainly in the form of polythenes, polyolefins, polystyrenes, nylons and acrylics. Under different heating conditions and by varying the composition of the plastic it is possible to make many different products with differing properties.This is a decision-making tool and source-book of information for plastics users, providing detailed accounts of the materials used, their economics,the selection of appropriate materials, and the use of thermoplastic resins and their composites. By having this book to hand, you will use the right material in the right way to produce the right product.
· Provides a quick and pragmatic approach to selecting thermoplastics for the non-specialist plastics user· Offers detailed accounts of thermoplastics including economic and technological elements· Clear and easy to understand illustrated with figures, tables and graphs throughout
Users, designers, specifiers and manufacturers of plastic parts in the automotive, transport, aeronautical, sports and leisure, consumer goods and packaging industries. Research and Development departments; academic departments.
Chapter 1Outline of the actual situation of plastics compared to conventional materials1.1 Polymers: the industrial and economic reality compared to traditional materials1.1.1 Plastic and metal consumptions1.1.2 Mechanical properties1.1.2.1. Intrinsic mechanical properties1.1.2.2. Specific mechanical properties1.1.3 Thermal and electrical properties1.1.4 Durability1.1.5 Material costs1.1.5.1. Cost per weight of various materials1.1.5.2. Cost per volume of various materials1.1.5.3. [Performance/cost per litre] ratios of various materials1.2 What are thermoplastics, TPE, thermosets, composites and hybrids?1.2.1 Thermoplastics1.2.2 Thermoplastic elastomers -TPE1.2.3 Thermosets1.2.4 Polymer composites1.2.5 Hybrid materials1.3 Plastics: an answer to the designer’s main problems1.3.1 Economic requirements1.3.2 Technical requirements1.3.3 Marketing requirements1.3.4 Environmental requirements1.3.5 Some weaknesses of the polymer materials1.4 Outline of the technical and economic possibilities of processing1.4.1 Thermoplastic processing1.4.1.1. Moulding the solid thermoplastics1.4.1.2. Extrusion and connected processes1.4.1.3. Calendering1.4.1.4. Blow moulding1.4.1.5. Moulding the liquid thermoplastics1.4.1.6 Secondary processing1.4.1.7 Brief economic comparison of some processing costs1.4.1.8 Repair possibilities: a significant thermoplastic advantage for large parts1.4.2 Thermoset processing1.4.2.1. Moulding the solid thermosets1.4.2.2. Moulding the liquid thermosets1.4.2.3. Secondary processing1.4.3 Composite processing1.4.3.1. Primary processes1.4.3.2. Secondary processing1.4.3.3. Repair possibilities: a significant composite advantage1.4.4 Hybrid processing1.5 Environmental constraints1.5.1 Toxicity and pollution1.5.2 The recycling of polymers1.6 The final material/process/cost compromiseChapter 2The plastics industry: economic overview2.1 Overview of the global plastics industry to day and to morrow2.2 Market shares of the various thermoplastic families versus total thermoplastics in the main industrialized countries2.3 Market shares of composites2.4 Market shares for the main application sectors2.5 Importance of the various processing modes2.6 Consumption trends2.6.1 Thermoplastics2.6.2 Composites2.7 The North American market2.8 The West European market2.9. The China market2.10 Structure of the plastic processing industry2.11. Plastic costs2.11.1 Raw material costs2.11.2 Examples of additive costs2.11.3 Reinforcement costs2.11.4 Processing costs2.11.5. Some good reasons to use plastics and a few examples of success stories2.12 Survey of main markets2.12.1 Packaging2.12.1.1. Films for packaging2.12.1.2. Bottles and other containers2.12.1.3. Foams2.12.2 Building & civil engineering2.12.2.1 Building exterior2.12.2.2 Building interior2.12.2.3 Pipes and tubing2.12.2.4. Geomembranes, geotextiles, geogrids2.12.3 Automobile & transportation2.12.4 Electricity & electronics2.12.5 Household, entertainment & office appliances2.12.6 Mechanical engineering2.12.7 Sports and leisure2.12.8 Medical market2.12.9 Furniture & bedding2.12.10 AgricultureChapter 3Basic criteria for the selection of thermoplastics3.1 Evaluation of plastic properties3.1.1 Thermal behaviour3.1.2 Low temperature behaviour3.1.3 Density3.1.4 Mechanical properties3.1.5 Long-term mechanical properties3.1.6 Long-term light and UV resistance3.1.7 Chemical resistance by immersion or contact3.1.8 Electrical properties3.1.9 Gas permeability3.1.10 Flammability3.1.11 Optical properties3.2 Evaluation of plastic structural properties3.3 ISO standards concerning polymer testing3.3.1 Moulding of test specimens3.3.2 Mechanical properties3.3.3 Thermomechanical properties3.3.4 Long-term properties3.3.5 Fluid contact behaviour3.3.6 Electrical properties3.3.7 Oxygen index, flammability, smoke generation3.3.8 Optical properties3.4 Analysis and diagnostic equipment3.5 Material selection3.6 Precision of the moulded parts3.7 Schematic comparison of thermoplastic and composite properties3.8 Upgrading and customisation of raw polymers3.8.1 Thermoplastic alloying 3.8.2 Compounding with additives 3.8.2.1 Mechanical property upgrading and customization: toughening, reinforcement, 3.8.2.2 Ageing protection: additives, films3.8.2.3 Sensorial properties3.8.2.4 Specific properties: specific grades and specific additives3.8.2.5 The cost cuttersChapter 4Detailed accounts of thermoplastic resins4.1 Polyethylene or polythene (PE)4.1.1 General properties4.1.2 Thermal behaviour4.1.3 Optical properties4.1.4 Mechanical properties4.1.5 Ageing4.1.6 Electrical properties4.1.7 Joining, decoration4.1.8 Crosslinked polyethylene4.1.9 Foams4.1.10 Industrial fibres4.1.11 Specific ISO standards concerning polyethylenes4.1.12 Trade name examples4.1.13 Property tables4.2 Polypropylene (PP)4.2.1 General properties4.2.2 Thermal behaviour4.2.3 Optical properties4.2.4 Mechanical properties4.2.5 Ageing4.2.6 Electrical properties4.2.7 Joining, decoration4.2.8 Foams4.2.9 Specific ISO standards concerning polypropylenes4.2.10 Trade name examples4.2.11 Property tables4.3 Other polyolefins (PO)4.3.1 Polybutene-1 or polybutylene-1 (PB)4.3.2 Polymethylpentene (PMP)4.3.3 Cyclic Olefin Copolymers or Cyclic Olefin Polymers (COC or COP)4.4 Polyolefin and non polyolefin copolymers4.4.1 Ethylene-vinylacetate copolymers (EVA, E/VAC, EVAC, VAE, EVM)4.4.2 Ethylene-vinyl alcohol copolymers (EVOH)4.4.3 Ethylene-methacrylate ionomers (EMA)4.4.4 Ethylene-acid and ethylene-ester copolymers (EBA, EGMA, EMAH, EEA, EAA…)4.5 Chlorinated polyethylene (CPE, CM)4.6 Polyvinyl chloride (PVC)4.6.1 General properties4.6.2 Thermal behaviour4.6.3 Optical properties4.6.4 Mechanical properties4.6.5 Ageing4.6.6 Electrical properties4.6.7 Joining, decoration4.6.8 Foams4.6.9 Specific ISO standards concerning PVC4.6.10 Trade name examples4.6.11 Property tables4.7 Chlorinated PVC (PVC-C or CPVC)4.7.1 General properties4.7.2 Thermal behaviour4.7.3 Mechanical properties4.7.4 Ageing4.7.5 Electrical properties4.7.6 Joining, decoration4.7.7 Specific ISO standards concerning PVC-C4.7.8 Trade name examples4.7.9 Property tables4.8 Polyvinylidene chloride (PVDC)4.8.1 General properties4.8.2 Thermal behaviour4.8.3 Mechanical properties4.8.4 Ageing4.8.5 Trade names4.8.6 Property tables4.9 Other vinyl polymers4.9.1 Polyvinyl alcohol (PVAL or PVOH)4.9.2 Polyvinyl butyrate (PVB) 4.9.3 Polyvinyl acetate (PVAC)4.10 Polystyrene (PS, SB, SMA)4.10.1 General properties4.10.2 Thermal behaviour4.10.3 Optical properties4.10.4 Mechanical properties4.10.5 Ageing4.10.6 Electrical properties4.10.7 Joining, decoration4.10.8 Crosslinked polystyrene (X-PS or PS-X)4.10.9 Foams (EPS - Expandable polystyrene)4.10.10 Specific ISO standards concerning polystyrene4.10.11 Trade name examples4.10.12 Property tables4.11 Acrylonitrile-butadiene-styrene (ABS), methylmethacrylate-acrylonitrile-butadiene-styrene (MABS)4.11.1 General properties4.11.2 Thermal behaviour4.11.3 Optical properties4.11.4 Mechanical properties4.11.5 Ageing4.11.6 Electrical properties4.11.7 Joining, decoration4.11.8 Specific ISO standards concerning ABS and MABS4.11.9 Trade name examples4.11.10 Property tables4.12 Styrene acrylonitrile (SAN), acrylate rubber modified styrene acrylonitrile (ASA), acrylonitrile EPDM styrene (AES or AEPDS), acrylonitrile chlorinated polyethylene styrene (ACS)4.12.1 General properties4.12.2 Thermal behaviour4.12.3 Optical properties4.12.4 Mechanical properties4.12.5 Ageing4.12.6 Electrical properties4.12.7 Joining, decoration4.12.8 Specific ISO standards concerning SAN, ASA, AEPDS and ACS4.12.9 Trade name examples4.12.10 Property tables4.13 Polyamides or nylons (PA)4.13.1 Polyamides 66 and 6 (PA 66 and PA 6)4.13.1.1 General properties4.13.1.2 Thermal behaviour4.13.1.3 Optical properties4.13.1.4 Mechanical properties4.13.1.5 Ageing4.13.1.6 Electrical properties4.13.1.7 Joining, decoration4.13.1.8 Specific ISO standards concerning polyamides4.13.1.9 Trade name examples4.13.1.10 Property tables4.13.2 Polyamides 11 and 12 (PA 11 and PA 12)4.13.2.1 General properties4.13.2.2 Thermal behaviour4.13.2.3 Optical properties4.13.2.4 Mechanical properties4.13.2.5 Ageing4.13.2.6 Electrical properties4.13.2.7 Joining, decoration4.13.2.8 Specific ISO standards concerning polyamides4.13.2.9 Trade name examples4.13.2.10 Property tables4.13.3 Linear polyamides intermediate between PA 6 or 66 and PA 11 or PA 12: PA 610 and PA 612 4.13.4 Polyamide 46 (PA 46)4.13.5 Semi-aromatic polyamide, polyphthalamide (PPA), polyarylamide (PAA), transparent amorphous polyamide (PA-T)4.13.6 Cast nylon4.14 Thermoplastic polyesters (PET, PBT, PETG, PCT, PTMT, PETP, PBTP, PCTG, PCTA, PTT)4.14.1 General properties4.14.2 Thermal behaviour4.14.3 Optical properties4.14.4 Mechanical properties4.14.5 Ageing4.14.6 Electrical properties4.14.7 Joining, decoration4.14.8 Specific ISO standards concerning polyesters4.14.9 Trade name examples4.14.10 Property tables4.15 Acrylics (PMMA, PMI, SMMA, MBS)4.15.1 General properties4.15.2 Thermal behaviour4.15.3 Optical properties4.15.4 Mechanical properties4.15.5 Ageing4.15.6 Electrical properties4.15.7 Joining, decoration4.15.8 Foams4.15.9 Specific ISO standards concerning acrylics4.15.10 Trade name examples4.15.11 Property tables4.16 Polycarbonates (PC)4.16.1 General properties4.16.2 Thermal behaviour4.16.3 Optical properties4.16.4 Mechanical properties4.16.5 Ageing4.16.6 Electrical properties4.16.7 Joining, decoration4.16.8 Specific ISO standards concerning polycarbonates4.16.9 Trade name examples4.16.10 Property tables4.17 Polyoxymethylene, polyacetal, acetal or polyformaldehyde (POM)4.17.1 General properties4.17.2 Thermal behaviour4.17.3 Optical properties4.17.4 Mechanical properties4.17.5 Ageing4.17.6 Electrical properties4.17.7 Joining, decoration4.17.8 Specific ISO standards concerning acetals4.17.9 Trade name examples4.17.10 Property tables4.18 Polyphenylene oxide, polyphenylene ether (PPO, PPE)4.18.1 General properties4.18.2 Thermal behaviour4.18.3 Optical properties4.18.4 Mechanical properties4.18.5 Ageing4.18.6 Electrical properties4.18.7 Joining, decoration4.18.8 Specific ISO standards concerning PPE4.18.9 Trade name examples4.18.10 Property tables4.19 Fluorinated thermoplastics: perfluorinated thermoplastics (PTFE or TFE, PFA, FEP), copolymers (ETFE), partially fluorinated (PVDF, PVF), chlorofluoroethylene (PCTFE) and copolymer (ECTFE)4.19.1 Perfluorinated thermoplastics (PTFE or TFE, PFA, FEP)4.19.2 Tetrafluoroethylene and ethylene copolymer (ETFE)4.19.3 Polychlorotrifluoroethylene (PCTFE)4.19.4 Ethylene chlorotrifluoroethylene copolymer (ECTFE)4.19.5 Polyvinylidene fluoride (PVDF)4.19.6 Polyvinyl fluoride (PVF)4.20 Cellulosics (CA, CAB, CP)4.21 Polysulfone, polyarylsulfone, polyethersulfone, polyphenylenesulfone, (PSU, PAS, PESU, PPSU)4.21.1 General properties4.21.2 Thermal behaviour4.21.3 Optical properties4.21.4 Mechanical properties4.21.5 Ageing4.21.6 Electrical properties4.21.7 Joining, decoration4.21.8 Foam4.21.9 Trade name examples4.21.10 Property tables4.22 Polyphenylene sulphide or polyphenylene sulfide, (PPS)4.22.1 General properties4.22.2 Thermal behaviour4.22.3 Optical properties4.22.4 Mechanical properties4.22.5 Ageing4.22.6 Electrical properties4.22.7 Joining, decoration4.22.8 Trade name examples4.22.9 Property tables4.23 Polyetheretherketones, polyetherketones and polyaryletherketones (PEEK, PEK, PAEK)4.23.1 General properties4.23.2 Thermal behaviour4.23.3 Optical properties4.23.4 Mechanical properties4.23.5 Ageing4.23.6 Electrical properties4.23.7 Joining, decoration4.23.8 Trade name examples4.23.9 Property tables4.24 Polyetherimide (PEI)4.24.1 General properties4.24.2 Thermal behaviour4.24.3 Optical properties4.24.4 Mechanical properties4.24.5 Ageing4.24.6 Electrical properties4.24.7 Joining, decoration4.24.8 Trade name examples4.24.9 Property tables4.25 Polyamide-imide (PAI)4.25.1 General properties4.25.2 Thermal behaviour4.25.3 Optical properties4.25.4 Mechanical properties4.25.5 Ageing4.25.6 Electrical properties4.25.7 Joining, decoration4.25.8 Trade name examples4.25.9 Property tables4.26 Polyimides (PI)4.26.1 General properties4.26.2 Thermal behaviour4.26.3 Optical properties4.26.4 Mechanical properties4.26.5 Ageing4.26.6 Electrical properties4.26.7 Joining, decoration4.26.8 Foams4.26.9 Trade name examples4.26.10 Property tables4.27 Liquid crystal polymers (LCP)4.27.1 General properties4.27.2 Thermal behaviour4.27.3 Optical properties4.27.4 Mechanical properties4.27.5 Ageing4.27.6 Electrical properties4.27.7 Joining, decoration4.27.8 Trade name examples4.27.9 Property tables4.28 Polybenzimidazole (PBI)4.28.1 General properties4.28.2 Thermal behaviour4.28.3 Optical properties4.28.4 Mechanical properties4.28.5 Ageing4.28.6 Electrical properties4.28.7 Trade name examples4.28.8 Property tables4.29 Alloys4.29.1 ABS/PC alloys4.29.2 ASA/PC alloys4.29.3 ABS/PA alloys4.29.4 Polypropylene/polyamide PP/PA alloys4.29.5 Thermoplastic polyester alloys4.29.6 ABS/PVC alloys4.29.7 Polysulfone-based alloys4.29.8 Polyphenylene sulphide-elastomer alloys4.29.9 Polyetherimide/polycarbonate alloys (PEI/PC)4.29.10 Other alloys4.30 Thermoplastic elastomers (TPE)4.30.1. Thermoplastic styrenics TPS (SBS, SEBS, SIS, SEPS…)4.30.2. Thermoplastic olefinics TPO (PP/EPDM…)4.30.3. Thermoplastic vulcanizates TPV (PP/EPDM-V, PP/NBR-V, PP/IIR-V…)4.30.3.1. PP/EPDM-V 4.30.3.2. PP/NBR-V 4.30.3.3. PP/IIR-V 4.30.4. TPE/PVC 4.30.5. Thermoplastic polyurethanes TPU 4.30.6. Melt processible rubber (MPR)4.30.7. Thermoplastic polyester elastomers (TPEE or COPE)4.30.8. Polyether block amides (PEBA)Chapter 5 Thermoplastic processing5.1. Moulding thermoplastics5.1.1 Injection moulding5.1.1.1. Standard injection moulding5.1.1.2. Injection micro-moulding5.1.1.3. Co-injection, over-moulding5.1.1.4. Gas assisted injection moulding5.1.2 Blow moulding5.1.3 Compression moulding5.1.4 Rotational moulding or rotomoulding5.1.5 Slush moulding5.1.6. Casting5.1.7. RIM5.1.8.Dipping5.1.9 Spraying5.2 Extrusion and connected processes5.2.1. Extrusion5.2.2 Blown film extrusion5.3. Calendering5.4. Coating5.4.1. Extrusion coating5.4.2 Roll dipping, spreading5.4.3 Powdering, electrostatic deposition5.4.4 Solvent casting of films5.4.5 Laminating5.5. Foaming5.5.1. Moulding of expandable beads5.5.2. Structural foam injection5.5.3 Extrusion of thermoplastics containing blowing agents5.5.4 Direct gas extrusion process5.5.5 Liquid foam process5.6. Composite processing5.6.1. Processing of short fibre reinforced thermoplastics5.6.2. Processing of LFRT or LFT -long fibre (reinforced) thermoplastics: Injection, compression moulding, extrusion-compression, composite insert moulding5.6.3. Stamping and compression moulding of GMT sheets5.6.4. Prepreg draping and consolidation by vacuum or pressure bag moulding, autoclave…5.6.5. Filament and tape winding5.6.6. Continuous processes: Pultrusion and derived processes5.6.7. Sandwich composites…5.6.8. Hybrids5.7. Curing of thermoplastics5.8. Secondary processing5.8.1. Thermoforming5.8.2. Machining of thermoplastics and composites5.8.3. Boilermaking 5.8.4. Inserts, outserts5.8.4.1. Inserts5.8.4.2. Installation of inserts5.9. Finishing5.9.1 Cleaning and surface treatments5.9.1.1. Cleaning of plastic parts5.9.1.2. Surface treatments of plastic parts5.9.2. Decoration, marking5.10. Assembly of fabricated parts5.10.1. Welding5.10.2. Adhesive bonding5.10.3. Mechanical assembly5.11 Repair possibilities: a significant thermoplastic advantage for large parts5.12. AnnealingChapter 6 Thermoplastic composites6.1 Definitions6.2 Reminder of some basic principles6.3 Composite mechanical performances according to the reinforcement type6.3.1 Reinforcement by randomly distributed short fibres6.3.2 Reinforcement by arranged continuous fibres6.3.2.1. Unidirectional reinforcement6.3.2.2. Reinforcement with two orthogonal layers6.3.3 General approximate method for strength estimation6.4 Composite Matrices6.4.1. Recall of some basic characteristics of thermoplastic matrices6.4.2 Influence of the matrix on the composite properties6.5 Reinforcements6.5.1 Fibres6.5.1.1. Glass fibres for polymer reinforcement6.5.1.2. Carbon fibres (CF) for polymer reinforcement6.5.1.3. Aramid fibres (AF) for polymer reinforcement6.5.1.4. Comparison of the three main types of fibres6.5.1.5. Sustainable natural vegetal fibres6.5.1.6. Other mineral fibres6.5.1.7. Other textile fibres6.5.1.8. Industrial fibres6.5.2 The different fibre forms used for reinforcement6.5.3 Foams for sandwich technology6.5.4 Honeycombs6.5.5 Plywood and wood6.5.6 Influence of the core on the sandwich properties6.5.7 Nanofillers6.6 Intermediate semi-manufactured materials6.6.1 Glass mat thermoplastics (GMTs)6.6.2. Prepregs6.6.3 Property examples of intermediate semi-manufactured composites6.6.4 Advanced all-polymer prepregs or self-reinforced polymers6.7 Examples of composite characteristics6.7.1 Basic principles6.7.2 Nanocomposites6.7.3 Short fibre composites6.7.3.1. Significant parameters6.7.3.2. Short glass fibres6.7.3.3. Short carbon fibres6.7.3.4. Short aramid fibres6.7.4 Long fibre reinforced plastics: LFRT6.7.5 “Continuous” fibre composites6.7.6 Sandwich composites6.7.7 Conductive compositesChapter 7Future prospects for thermoplastics and thermoplastic composites7.1 The Laws and requirements of the market7.2 Thermoplastic and thermoplastic composite answers and assets7.3 Markets: what drives what? The forces driving development7.3.1 Consumption trends7.3.2 Requirements of the main markets7.4 Cost savings7.4.1 Material costs7.4.2 Hybrids7.4.3 Processing costs7.4.3.1. Example of compounding integrated on the process line 7.4.3.2. Translation towards other conventional, new or modified processes7.4.3.3. Integrating finishing in the process7.4.3.4 Low-cost tool examples7.5 Material upgrading and competition7.5.1 Carbon nanotubes (CNT)7.5.2 Molecular reinforcement7.5.3 Polymer nanotubes7.5.4 Nanofillers7.5.5 Short fibre reinforced thermoplastics to compete with LFRT7.5.6 Thermoplastic and thermoset competition7.5.7 3D reinforcements compete with 2D7.5.8 Carbon fibres compete with glass fibres7.5.9 New special performance polymers7.6 The immediate future seen through recent patents7.6.1 Analysis of patents by polymer type7.6.2 Analysis of patents by reinforcement type7.6.3 Analysis of patents by structure and process type7.7 The immediate future seen through recent awards7.8 Environmental concerns7.8.1 Recycling of thermoplastics and thermoplastic composites7.8.1.1. Collection and pre-treatment of wastes7.8.1.2. The main recycling routes7.8.1.3. Composite specifics7.8.1.4. Thermoplastics and thermoplastic composite recyclates: mechanical and calorific properties7.8.1.5. Recycling costs7.8.2 Sustainable and biodegradable thermoplastics7.8.3 Sustainable standard and high-performance reinforcements7.8.4 Examples of sustainable composites
- Edition: 1
- Published: April 26, 2007
- Language: English
MB
Michel Biron
Michel Biron is a plastics consultant based in Les Ulis, France, and is a Graduate Chemist Engineer from the Institut National Supérieur de Chimie Industrielle
de Rouen and Polymer Specialist from the Institut Français du Caoutchouc. He has authored numerous technical papers and books on plastics.
Affiliations and expertise
Plastics Consultant, Les Ulis, FranceRead Thermoplastics and Thermoplastic Composites on ScienceDirect