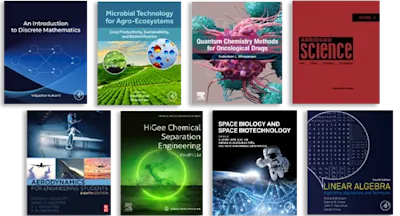
Sulfuric Acid Manufacture
Analysis, Control and Optimization
- 2nd Edition - July 11, 2013
- Authors: Matt King, Michael Moats, William G. Davenport
- Language: English
- Hardback ISBN:9 7 8 - 0 - 0 8 - 0 9 8 2 2 0 - 5
- eBook ISBN:9 7 8 - 0 - 0 8 - 0 9 8 2 2 6 - 7
By some measure the most widely produced chemical in the world today, sulfuric acid has an extraordinary range of modern uses, including phosphate fertilizer production, ex… Read more
Purchase options
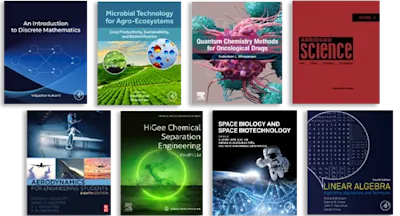
By some measure the most widely produced chemical in the world today, sulfuric acid has an extraordinary range of modern uses, including phosphate fertilizer production, explosives, glue, wood preservative and lead-acid batteries. An exceptionally corrosive and dangerous acid, production of sulfuric acid requires stringent adherence to environmental regulatory guidance within cost-efficient standards of production.
This work provides an experience-based review of how sulfuric acid plants work, how they should be designed and how they should be operated for maximum sulfur capture and minimum environmental impact. Using a combination of practical experience and deep physical analysis, Davenport and King review sulfur manufacturing in the contemporary world where regulatory guidance is becoming ever tighter (and where new processes are being required to meet them), and where water consumption and energy considerations are being brought to bear on sulfuric acid plant operations. This 2e will examine in particular newly developed acid-making processes and new methods of minimizing unwanted sulfur emissions.
The target readers are recently graduated science and engineering students who are entering the chemical industry and experienced professionals within chemical plant design companies, chemical plant production companies, sulfuric acid recycling companies and sulfuric acid users. They will use the book to design, control, optimize and operate sulfuric acid plants around the world.
- Unique mathematical analysis of sulfuric acid manufacturing processes, providing a sound basis for optimizing sulfuric acid manufacturing processes
- Analysis of recently developed sulfuric acid manufacturing techniques suggests advantages and disadvantages of the new processes from the energy and environmental points of view
- Analysis of tail gas sulfur capture processes indicates the best way to combine sulfuric acid making and tailgas sulfur-capture processes from the energy and environmental points of view
- Draws on industrial connections of the authors through years of hands-on experience in sulfuric acid manufacture
Preface
1. Overview
1.1 Catalytic oxidation of SO2 to SO3
1.2 H2SO4 production
1.3 Industrial flowsheet
1.4 Sulfur burning
1.5 Metallurgical offgas
1.6 Spent acid regeneration
1.7 Sulfuric acid product
1.8 Recent developments
1.9 Alternative processes
1.10 Summary
References
Suggested reading
2. Production and consumption
2.1 Uses
2.2 Acid plant locations
2.3 Price
2.4 Summary
References
Suggested reading
3. Sulfur burning
3.1 Objectives
3.2 Sulfur
3.3 Molten sulfur delivery
3.4 Sulfur atomizers and sulfur burning furnaces
3.5 Product gas
3.6 Heat recovery boiler
3.7 Summary
References
Suggested reading
4. Metallurgical offgas cooling and cleaning
4.1 Initial and final SO2 concentrations
4.2 Initial and final dust concentrations
4.3 Offgas cooling and heat recovery
4.4 Electrostatic collection of dust
4.5 Water scrubbing (Tables 4.5 and 4.6)
4.6 H2O(g) removal from scrubber exit gas (Tables 4.5 and 4.6)
4.7 Summary
References
Suggested reading
5. Regeneration of spent sulfuric acid
5.1 Spent acid compositions
5.2 Spent acid handling
5.3 Decomposition
5.4 Decomposition furnace product
5.5 Optimum decomposition furnace operating conditions
5.6 Preparation of offgas for SO2 oxidation and H2SO4 making
5.7 Summary
References
Suggested Reading
6. Dehydrating air and gases with strong sulfuric acid
6.1 Chapter objectives
6.2 Dehydration with strong sulfuric acid
6.3 Dehydration reaction mechanism
6.4 Residence times
6.5 Recent advances
6.6 Summary
References
7. Catalytic oxidation of SO2 to SO3
7.1 Objectives
7.2 Industrial SO2 oxidation
7.3 Catalyst necessity
7.4 SO2 oxidation “heatup” path (Chapter 11)
7.5 Industrial multicatalyst bed SO2 oxidation (Tables 7.2–7.7)
7.6 Industrial operation (Table 7.2)
7.7 Recent advances
7.8 Summary
References
8. SO2 oxidation catalyst and catalyst beds
8.1 Catalytic reactions
8.2 Maximum and minimum catalyst operating temperatures
8.3 Composition and manufacture
8.4 Choice of size and shape
8.5 Catalyst bed thickness and diameter
8.6 Gas residence times
8.7 Catalyst bed temperatures
8.8 Catalyst bed maintenance
8.9 Summary
References
Suggested reading
9. Production of H2SO4(ℓ) from SO3(g)
9.1 Objectives
9.2 Sulfuric acid rather than water
9.3 Absorption reaction mechanism
9.4 Industrial H2SO4 making (Tables 9.3–9.8)
9.5 Choice of input and output acid compositions
9.6 Acid temperature
9.7 Gas temperatures
9.8 Operation and control
9.9 Double contact H2SO4 making (Tables 19.3 and 23.2)
9.10 Intermediate versus final H2SO4 making
9.11 Summary
References
Suggested reading
Break
10. Oxidation of SO2 to SO3—Equilibrium curves
10.1 Catalytic oxidation
10.2 Equilibrium equation
10.3 KE as a function of temperature
10.4 KE in terms of % SO2oxidized
10.5 Equilibrium % SO2 oxidized as a function of temperature
10.6 Discussion
10.7 Summary
10.8 Problems
Reference
11. SO2 oxidation heatup paths
11.1 Heatup paths
11.2 Objectives
11.3 Preparing a heatup path—The first point
11.4 Assumptions
11.5 A specific example
11.6 Calculation strategy
11.7 Input SO2, O2, and N2 quantities
11.8 Sulfur, oxygen, and nitrogen molar balances
11.9 Enthalpy balance
11.10 Calculating level L quantities
11.11 Matrix calculation
11.12 Preparing a heatup path
11.13 Feed gas SO2 strength effect
11.14 Feed gas temperature effect
11.15 Significance of heatup path position and slope
11.16 Summary
11.17 Problems
12. Maximum SO2 oxidation: Heatup path-equilibrium curve intercepts
12.1 Initial specifications
12.2 % SO2 oxidized-temperature points near an intercept
12.3 Discussion
12.4 Effect of feed gas temperature on intercept
12.5 Inadequate % SO2 oxidized in first catalyst bed
12.6 Effect of feed gas SO2 strength on intercept
12.7 Minor influence—Equilibrium gas pressure
12.8 Minor influence—O2 strength in feed gas
12.9 Minor influence—CO2 in feed gas
12.10 Catalyst degradation, SO2 strength, and feed gas temperature
12.11 Maximum feed gas SO2 strength
12.12 Exit gas composition ≡ intercept gas composition
12.13 Summary
12.14 Problems
13. Cooling first catalyst bed exit gas
13.1 First catalyst bed summary
13.2 Cooldown path
13.3 Gas composition below equilibrium curve
13.4 Summary
13.5 Problem
Hints
14. Second catalyst bed heatup path
14.1 Objectives
14.2 % SO2 oxidized redefined
14.3 Second catalyst bed heatup path
14.4 A specific heatup path question
14.5 Second catalyst bed input gas quantities
14.6 S, O, and N molar balances
14.7 Enthalpy balance
14.8 Calculating 760 K (level L) quantities
14.9 Matrix calculation and result
14.10 Preparing a heatup path
14.11 Discussion
14.12 Summary
14.13 Problem
15. Maximum SO2 oxidation in a second catalyst bed
15.1 Second catalyst bed equilibrium curve equation
15.2 Second catalyst bed intercept calculation
15.3 Two bed SO2 oxidation efficiency
15.4 Summary
15.5 Problems
Hints
16. Third catalyst bed SO2 oxidation
16.1 2-3 Cooldown path
16.2 Heatup path
16.3 Heatup path-equilibrium curve intercept
16.4 Graphical representation
16.5 Summary
16.6 Problems
17. SO3 and CO2 in feed gas
17.1 SO3
17.2 SO3 effects
17.3 CO2
17.4 CO2 effects
17.5 Summary
17.6 Problems
18. Three catalyst bed acid plant
18.1 Calculation specifications
18.2 Example calculation
18.3 Calculation results
18.4 Three catalyst bed graphs
18.5 Minor effect—SO3 in feed gas
18.6 Minor effect—CO2 in feed gas
18.7 Minor effect—Bed pressure
18.8 Minor effect—SO2 strength in feed gas
18.9 Minor effect—O2 strength in feed gas
18.10 Summary of minor effects
18.11 Major effect—Catalyst bed input gas temperatures
18.12 Discussion of book’s assumptions
18.13 Summary
Reference
19. After-H2SO4-making SO2 oxidation
19.1 Double contact advantage
19.2 Objectives
19.3 After-H2SO4-making calculations
19.4 Equilibrium curve calculation
19.5 Heatup path calculation
19.6 Heatup path-equilibrium curve intercept calculation
19.7 Overall SO2 oxidation efficiency
19.8 Double/single contact comparison
19.9 Summary
19.10 Problems
Reference
20. Optimum double contact acidmaking
20.1 Total % SO2 oxidized after all catalyst beds
20.2 Four catalyst beds
20.3 Improved efficiency with five catalyst beds
20.4 Input gas temperature effect
20.5 Best bed for Cs catalyst
20.6 Triple contact acid plant
20.7 Summary
Reference
21. Enthalpies and enthalpy transfers
21.1 Input and output gas enthalpies
21.2 H2SO4 making input gas enthalpy
21.3 Heat transfers
21.4 Heat transfer rate
21.5 Summary
21.6 Problems
22. Control of gas temperature by bypassing
22.1 Bypassing principle
22.2 Objective
22.3 Gas to economizer heat transfer
22.4 Heat transfer requirement for 480 K economizer output gas
22.5 Changing heat transfer by bypassing
22.6 460 K Economizer output gas
22.7 Bypassing for 460, 470, and 480 K economizer output gas
22.8 Bypassing for 470 K economizer output gas while input gas temperature is varying
22.9 Industrial bypassing
22.10 Summary
22.11 Problems
23. H2SO4 making
23.1 Objectives
23.2 Mass balances
23.3 SO3 input mass
23.4 H2O(g) input from moist acid plant input gas
23.5 Water for product acid
23.6 Calculation of mass water in and mass acid out
23.7 Interpretations
23.8 Summary
23.9 Problem
24. Acid temperature control and heat recovery
24.1 Objectives
24.2 Calculation of output acid temperature
24.3 Effect of input acid temperature
24.4 Effect of input gas temperature
24.5 Effect of input gas SO3 concentration on output acid temperature
24.6 Adjusting output acid temperature
24.7 Acid cooling
24.8 Target acid temperatures
24.9 Recovery of acid heat as steam
24.10 Steam production principles
24.11 Double-packed bed absorption tower
24.12 Steam injection
24.13 Sensible heat recovery efficiency
24.14 Materials of construction
24.15 Summary
24.16 Problems
References
25. Making sulfuric acid from wet feed gas
25.1 Chapter objectives
25.2 WSA feed Gas
25.3 WSA flowsheet
25.4 Catalyst bed reactions
25.5 Preparing the oxidized gas for H2SO4(ℓ) condensation
25.6 H2SO4(ℓ) condenser
25.7 Product acid composition
25.8 Comparison with conventional acidmaking
25.9 Appraisal
25.10 Alternatives
25.11 Summary
References
Suggested reading
26. Wet sulfuric acid process fundamentals
26.1 Wet gas sulfuric acid process SO2 oxidation
26.2 Injection of nanoparticles into cooled process gas
26.3 Sulfuric acid condensation
26.4 Condenser temperature choices
26.5 Condenser acid composition up the glass tube
26.6 Condenser re-evaporation of H2O(ℓ)
26.7 Condenser acid production rate
26.8 Condenser appraisal
26.9 Summary
References
Suggested reading
27. SO3 gas recycle for high SO2 concentration gas treatment
27.1 Objectives
27.2 Calculations
27.3 Effect of recycle extent
27.4 Effect of recycle gas temperature on recycle requirement
27.5 Effect of gas recycle on first catalyst SO2 oxidation efficiency
27.6 Effect of first catalyst exit gas recycle on overall acid plant performance
27.7 Recycle equipment requirements
27.8 Appraisal
27.9 Industrial SO3 gas recycle
27.10 Alternatives to gas recycle
27.11 Summary
References
28. Sulfur from tail gas removal processes
28.1 Objectives
28.2 Environmental standards
28.3 Acid plant tail gas characteristics
28.4 Industrial acid plant tail gas treatment methods
28.5 Technology selection (after Hay et al., 2003)
28.6 Capital and operating costs
28.7 Summary
References
29. Minimizing sulfur emissions
29.1 Industrial catalytic SO2+0.5O2→SO3 oxidation
29.2 Methods to lower sulfur emissions
29.3 Summary
References
Suggested reading
30. Materials of construction
30.1 Chapter objectives
30.2 Corrosion rate factors for sulfuric acid plant equipment
30.3 Sulfuric acid plant materials of construction
30.4 Summary
References
31. Costs of sulfuric acid production
31.1 Investment costs
31.2 Production costs
31.3 Summary
References
Appendix A. Sulfuric acid properties
A.1 Sulfuric acid specific gravity at constant temperature
A.2 Specific gravity of sulfuric acid at elevated temperatures
A.3 Sulfuric acid freezing points
A.4 Oleum specific gravity
A.5 Electrical conductivity of sulfuric acid
A.6 Absolute viscosity of sulfuric acid
Appendix B. Derivation of equilibrium equation (10.12)
B.1 Modified equilibrium equation
B.2 Mole fractions defined
B.3 Feed and oxidized gas molar quantities
B.4 Mole fractions in oxidized gas
B.5 Equation applicability
B.6 Equilibrium equation
B.7 Equilibrium constant and molar quantities
B.8 Equilibrium and ΦE
Appendix C. Free energy equations for equilibrium curve calculations
C.1 Production of SO3(g) from SO2(g) and O2(g)
C.2 Production of H2SO4(g) from SO3(g) and H2O(g)
Appendix D. Preparation of Fig. 10.2’s equilibrium curve
D.1 Integer temperature calculations
D.2 Second and third catalyst bed equilibrium curves
Appendix E. Proof that volume%=mol% (for ideal gases)
E.1 Definitions
E.2 Characterization of partial volumes
E.3 Equality of volume% and mol%
Appendix F. Effect of CO2 and Ar on equilibrium equations (none)
F.1 CO2
F.2 Ar
F.3 Conclusions
Appendix G. Enthalpy equations for heatup path calculations
G.1 An example—Enthalpy of SO3(g) at 600 K
G.2 Preparation of equations
References
Appendix H. Matrix solving using Tables 11.2 and 14.2 as examples
Appendix I. Enthalpy equations in heatup path matrix cells
I.1 Example results
Appendix J. Heatup path-equilibrium curve: Intercept calculations
J.1 Calculation strategy
J.2 Worksheet
J.3 Intercept worksheet preparation instructions
J.4 Goal Seek instructions
J.5 Another example
Appendix K. Second catalyst bed heatup path calculations
Appendix L. Equilibrium equation for multicatalyst bed SO2 oxidation
L.1 Proof
L.2 Inapplicability
Appendix M. Second catalyst bed intercept calculations
M.1 Calculation strategy
M.2 Specifications (Fig. 14.2)
M.3 Worksheet
M.4 Goal Seek instructions
Appendix N. Third catalyst bed heatup path worksheet
Appendix O. Third catalyst bed intercept worksheet
Appendix P. Effect of SO3 in Fig. 10.1’s feed gas on equilibrium equations
P.1 Molar balances
P.2 Total kg mol of oxidized gas
P.3 Mole fractions in oxidized gas
P.4 New equilibrium equation
P.5 % SO2 oxidized in equilibrium equation
P.6 Equilibrium % SO2 oxidized as a function of temperature
Appendix Q. SO3-in-feed-gas intercept worksheet
Appendix R. CO2- and SO3-in-feed-gas intercept worksheet
Appendix S. Three-catalyst-bed “converter” calculations
S.1 First catalyst bed calculations (cells A1 through M47)
S.2 Second catalyst bed calculations (cells AA1 through AM47)
S.3 Third catalyst bed calculations (cells BA1 through BM47)
Appendix T. Worksheet for calculating after-intermediate-H2SO4-making heatup path-equilibrium curve intercepts
Appendix U. After-H2SO4-making SO2 oxidation with SO3 and CO2 in input gas
U.1 Equilibrium equation with SO3 in after-H2SO4-making input gas
U.2 H2SO4 making input gas quantity specification
U.3 H2SO4 making exit gas quantity calculation
U.4 Calculation of H2SO4 making exit gas volume percents
U.5 Worksheet construction and operation
U.6 Calculation of % SO2 oxidized after all catalyst beds
Appendix V. Moist air in H2SO4 making calculations
V.1 Calculation
Appendix W. Calculation of H2SO4 making tower mass flows
W.1 Input and output gas specifications
W.2 Input SO3(g) equation
W.3 Input and output acid composition equations
W.4 Total mass balance equation
W.5 Sulfur balance equation
W.6 Solving for flows
W.7 Effect of output acid mass% H2SO4 on input and output acid flows
Appendix X. Equilibrium equations for SO2, O2, H2O(g), N2 feed gas
X.1 Equilibrium equations
X.2 Modified equilibrium equations
X.3 Mole fractions defined
X.4 Feed and oxidized gas molar quantities
X.5 Preparing Eqs. (X.1) and (X.2) from Eqs. (X.19) and (X.21)
Appendix Y. Cooled first catalyst bed exit gas recycle calculations
Y.1 Exit gas temperature without recycle
Y.2 Recycle calculation setup
Y.3 Recycle matrix (Table Y.2)
Y.3.2 Result
Y.4 Recalculation to steady state
Y.5 Different feed and recycle temperatures
Y.6 Third catalyst bed exit gas recycle calculations
Answers to numerical problems
Chapter 10
Chapter 11
Chapter 12
Chapter 13
Chapter 14
Chapter 15
Chapter 16
Chapter 17
Chapter 19
Chapter 21
Chapter 22
Chapter 23
Chapter 24
Index
- Edition: 2
- Published: July 11, 2013
- Language: English
MM
Michael Moats
WD
William G. Davenport
Professor William George Davenport is a graduate of the University of British Columbia and the Royal School of Mines, London. Prior to his academic career he worked with the Linde Division of Union Carbide in Tonawanda, New York. He spent a combined 43 years of teaching at McGill University and the University of Arizona.
His Union Carbide days are recounted in the book Iron Blast Furnace, Analysis, Control and Optimization (English, Chinese, Japanese, Russian and Spanish editions).
During the early years of his academic career he spent his summers working in many of Noranda Mines Company’s metallurgical plants, which led quickly to the book Extractive Metallurgy of Copper. This book has gone into five English language editions (with several printings) and Chinese, Farsi and Spanish language editions.
He also had the good fortune to work in Phelps Dodge’s Playas flash smelter soon after coming to the University of Arizona. This experience contributed to the book Flash Smelting, with two English language editions and a Russian language edition and eventually to the book Sulfuric Acid Manufacture (2006), 2nd edition 2013.
In 2013 co-authored Extractive Metallurgy of Nickel, Cobalt and Platinum Group Metals, which took him to all the continents except Antarctica.
He and four co-authors are just finishing up the book Rare Earths: Science, Technology, Production and Use, which has taken him around the United States, Canada and France, visiting rare earth mines, smelters, manufacturing plants, laboratories and recycling facilities.
Professor Davenport’s teaching has centered on ferrous and non-ferrous extractive metallurgy. He has visited (and continues to visit) about 10 metallurgical plants per year around the world to determine the relationships between theory and industrial practice. He has also taught plant design and economics throughout his career and has found this aspect of his work particularly rewarding. The delight of his life at the university has, however, always been academic advising of students on a one-on-one basis.
Professor Davenport is a Fellow (and life member) of the Canadian Institute of Mining, Metallurgy and Petroleum and a twenty-five year member of the (U.S.) Society of Mining, Metallurgy and Exploration. He is recipient of the CIM Alcan Award, the TMS Extractive Metallurgy Lecture Award, the AusIMM Sir George Fisher Award, the AIME Mineral Industry Education Award, the American Mining Hall of Fame Medal of Merit and the SME Milton E. Wadsworth award. In September 2014 he will be honored by the Conference of Metallurgists’ Bill Davenport Honorary Symposium in Vancouver, British Columbia (his home town).