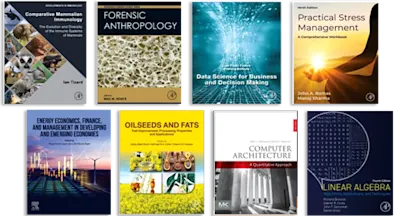
Stretch Blow Molding
- 2nd Edition - November 22, 2011
- Imprint: William Andrew
- Author: Ottmar Brandau
- Language: English
- Hardback ISBN:9 7 8 - 1 - 4 3 7 7 - 3 5 2 7 - 7
- eBook ISBN:9 7 8 - 1 - 4 3 7 7 - 3 5 2 9 - 1
Stretch blow molding is the blow molding process used to produce bottles of the strength required for carbonated drinks. In this handbook, Ottmar Brandau introduces the te… Read more
Purchase options
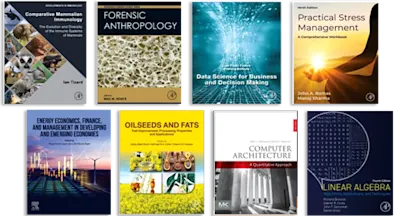
Stretch blow molding is the blow molding process used to produce bottles of the strength required for carbonated drinks. In this handbook, Ottmar Brandau introduces the technology of stretch blow molding, explores practical aspects of designing and running a production line and looks at practical issues for quality control and troubleshooting. As an experienced engineer, manager and consultant, Brandau’s focus is on optimizing the production process, improving quality and reducing cycle time.
This book is a thoroughly practical handbook that provides engineers and managers with the toolkit to improve production and engineering aspects in their own businesses--saving money, increasing output and improving competitiveness by adopting new technologies.
- Learn the tricks of the trade from an experienced engineer and manager
- Save money: Practical strategies to optimize the production process, improve quality and reduce cycle times
- Gain knowledge and understanding of the latest technological and best practice developments in stretch blow molding
1. A Short History of Stretch Blow Molding
2. Material Basics
2.1. Manufacture and States of PET
2.2. Crystallization of PET
2.3. Drying of PET
2.4. Behavior in the Injection Mold
2.5. Behavior in the Blow Mold
2.6. Acetaldehyde (AA) in PET Bottles
3. Reheat Stretch Blow Molding Machines
3.1. Overview
3.2. Semi-automatic Machines
3.3. Linear Shuttle-type Machines
3.4. Linear Continuous Motion Machines
3.5. Rotary Machines
4. Machine Details
4.1. Ovens
4.2. Transfer Functions
4.3. Blow Wheel/Blow Clamp
5. Blow Molds
5.1. Design
5.2. Making a Mold
5.3. Venting
6. Fundamentals of the Blow Process
6.1. Process Overview
6.2. Stretch Ratios
6.3. Types of Heat Transfer
6.4. Light Absorption Characteristics of PET
6.5. Optimum Preform Temperature
7. The Blowing Process
7.1. Reheating Preforms
7.2. Blowing Bottles
8. Injection Stretch Blow Molding Machines
8.1. Four-station Machines
8.2. Machine Controls
8.3. Injection Controls
8.4. Interaction between Injection and Blow
8.5. Conditioning
8.6. Container Blowing
8.7. Hot Runners
8.8. Integrated Two-stage Stretch Blow Molding
Chapter 9. Special Applications
9.1. Simulation of the Blow Process
9.2. Stretch Blow Molding of Oriented Polypropylene
9.3. Plant-based Plastics
9.4. Blow Process for Hot-fill Applications
9.5. Preferential Heating
9.6. Direct Feeding of Preforms into the Blow Machine
9.7. Vision Inspection
9.8. Barrier-enhancing Technologies
9.9. Blow-and-Trim Process
9.10. CSD Bottle-base Failures
9.11. Recycling of PET Bottles
9.12. Preform Esthetics in the Two-stage Process
Chapter 10. Troubleshooting of Blowing Problems
10.1. General Guidelines
10.2. Starting a New Process
10.3. Troubleshooting of Specific Problems
10.4. Defects Particular to Single-stage Molding
10.5. Summary of Preform Quality Checks
Chapter 11. Economics
11.1. Container Types
11.2. Business Models
11.3. Tooling Costs
11.4. Light-weighing of Bottles and Caps
11.5. Resin Prices
11.6. Bottle Production Costs
11.7. Starting with a New Product
11.8. Recommended Laboratory Equipment for RSBM Plants
11.9. Western vs. Asian Machinery
Chapter 12. Preform Design for Single and Two-stage Processing
12.1. Two-stage Process Injection Molding
12.2. Single-stage Process Injection Molding
12.3. Goals and Conditions
12.4. The Mechanics of Preform Design
12.5. Putting it All Together
Chapter 13. Auxiliary Equipment
13.1. Compressors
13.2. Chillers
13.3. Conveyors and Bottle Storage Devices
Chapter 14. Training of Operators
14.1. Current State of Training
14.2. Obstacles to Training Programs
14.3. Re-thinking Abstract Concepts
14.4. Language Structure
14.5. Converting Formulas into Common English Sentences
14.6. Substituting Uncommon Arithmetical Operators
14.7. Presentation Style
14.8. Translating Graphs into Common-day Language
14.9. Choosing Easy-to-Understand Drawings
14.10. Computer Simulations
14.11. Comprehensive Coverage
14.12. Trainees Involvement
14.13. Assessments
14.14. In-plant or Off-plant Training
14.15. Conclusion
- Edition: 2
- Published: November 22, 2011
- Imprint: William Andrew
- Language: English
OB