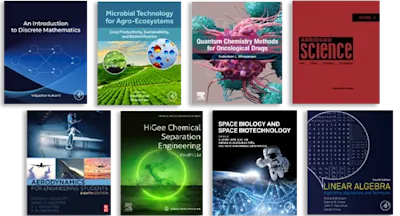
Strategic Planning for the Sustainable Production of Biofuels
- 1st Edition - March 8, 2019
- Authors: José Maria Ponce-Ortega, José Ezequiel Santibañez-Aguilar
- Language: English
- Paperback ISBN:9 7 8 - 0 - 1 2 - 8 1 8 1 7 8 - 2
- eBook ISBN:9 7 8 - 0 - 1 2 - 8 1 8 1 7 9 - 9
Strategic Planning for the Sustainable Production of Biofuels presents several optimization models for the design and planning of sustainable biorefinery supply chains, including… Read more
Purchase options
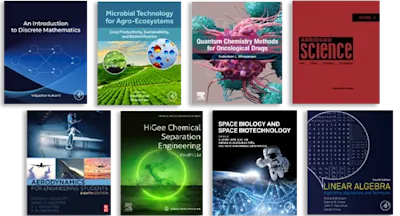
Strategic Planning for the Sustainable Production of Biofuels presents several optimization models for the design and planning of sustainable biorefinery supply chains, including issues surrounding the potential of biomass feedstocks in multiple harvesting sites, availability and seasonality of biomass resources, different potential geographical locations for processing plants that produce multiple products using diverse production technologies, economies of scale for production technologies, demands and prices of multiple products, locations of storage facilities, and a number of transportation modes. Sustainability considerations are incorporated into the proposed models by including simultaneous economic, environmental and social performance in the evaluation of the supply chain designs.
- Covers different optimization models for the strategic planning of biorefining systems
- Includes the GAMS and MATLAB codes for solving various problems
- Considers sustainability criteria in the presented models
- Presents different approaches for obtained trade-off solutions
- Provides general software that can be used for solving different problems
Gradueate and undergraduate students, researches, teachers, and different dessicion makers in the area of bioenergy. Also, this book can be used as a textbook for courses about supply chains, optimization and bioenergy in different engineering courses
Chapter 1. Introduction1.1 Importance of biofuels and biorefineries1.2 Strategic planning1.3 Optimization1.4 Sustainability1.5 Description of the book1.6 References
Chapter 2. Involving environmental aspect in the strategic planning of a biomass conversion system2.1 Introduction2.2 Outline of the optimization model2.3 Mathematical model2.3.1 Mass balances2.3.2 Maximum availability for feedstocks2.3.3 Maximum product demand2.3.4 Maximum processing limits2.3.5 Objective functions2.3.6 Economic objective2.3.7 Environmental objective2.4 Solution strategy2.5 Case study2.6 Sensitivity analysis2.7 Concluding remarks2.8 Nomenclature for Chapter 22.8.1 Parameters2.8.2 Variables2.8.3 Indexes2.9 References
Chapter 3. Optimal planning and site selection for distributed multiproduct biorefineries involving economic, environmental and social objectives3.1 Introduction 3.2 Problem statement3.3 Model formulation3.3.1 Mass balances for harvesting sites3.3.2 Mass balance for processing hubs (secondary plants)3.3.3 Raw material in hubs3.3.4 Products in hubs3.3.5 Mass balance for the main plant3.3.6 Raw material in the main plant3.3.7 Product in the main plant3.3.8 Mass balances for the markets3.3.9 Constraints for total product sales3.3.10 Storage constraint3.3.11 Transportation constraints3.3.12 Processing constraints3.3.13 Availability constraints3.3.14 Star and end storage constraints3.3.15 Objective functions3.3.15.1 Economic objective function3.3.15.2 Environmental objective function3.3.15.3 Social objective function3.3.16 Remarks for the model3.4 Case study3.5 Discussion3.6 Concluding remarks3.7 Nomenclature3.7.1 Sets3.7.2 Indexes3.7.3 Parameters3.7.4 Variables3.7.5 Binary variables3.7.6 Boolean variables3.8 References
Chapter 4. Distributed biorefining networks for the valued-added processing of water hyacinth4.1 Introduction4.2 Outline of the model formulation4.3 Model formulation for Chapter4 4.3.1 Mass balance for the harvesting of water hyacinth4.3.2 Availability for the harvested water hyacinth4.3.3 Mass balance for the splitters before the processing plants4.3.4 Balances for mixers before the processing facilities4.3.5 Balances for the technologies used in the processing facilities4.3.6 Balances for the mixers before the central processing facilities4.3.7 Balances for the technologies of central processing facilities4.3.8 Balances for the splitters after the central processing facilities4.3.9 Balances for the splitters after the central processing facilities4.3.10 Balances for the markets4.3.11 Demands for the consumers 4.3.12 Balances for the water treatment in each source4.3.13 Water treatment technologies in each source4.3.14 Mass balance for the splitters after the water treatment4.3.15 Mass balance for the mixers before each water consumer4.3.16 Component balance for the mixers before each water consumer4.3.17 Demand for water consumers4.3.18 Constraints for the water quality for each consumer4.3.19 Operational cost for the processing facilities4.3.20 Capital cost for the processing facilities4.3.21 Operational cost for the central processing facilities4.3.22 Capital cost for the water treatment units4.3.23 Operational cost for the water treatment units4.3.24 Capital cost for the water treatment units4.3.25 Harvesting cost4.3.26 Water transportation cost4.3.27 Biomass transportation cost4.3.28 Product transportation cost4.3.29 Total operational cost4.3.30 Total capital cost4.3.31 Total sales4.3.32 Total annual cost (negative of total net profit)4.3.33 Percentage of eliminated water hyacinth4.4 Remarks for the model of Chapter 44.5 Results4.6 Concluding remarks 4.7 Nomenclature4.7.1 Parameters4.7.2 Variables4.7.3 Binary variables4.8 References
Chapter 5. Optimization of the supply chain associated to the production of bioethanol from residues of the agave from the tequila process in Mexico5.1 Introduction5.2 Problem statement5.3 Model formulation5.3.1 Mass balances in agave cultivating areas5.3.2 Maximum available agave5.3.3 Mass balance in the tequila industry5.3.4 Residues of agave bagasse from the tequila industry5.3.5 Mass balance in distributed processing plants for bioethanol production5.3.6 Distribution of products from processing plants to markets5.3.7 Product demands5.3.8 Cost of the distributed bioethanol processing plants5.3.9 Transportation cost for stalks to distributed and central plants5.3.10 Transportation cost from the tequila industries to distributed and central bioethanol processing plants5.3.11 Transportation cost for products5.3.12 Objective function5.4 Case study5.4.1 Scenario A (Economic Solution with a constraint of 1% for the bioethanol demand in each consumption site)5.4.2 Scenario B. (Solution without constraint for the demand of bioethanol in the markets)5.4.3 Scenario C (Increasing the cultivation area)5.5 Concluding remarks5.6 Nomenclature5.6.1 Indexes5.6.2 Sets5.6.3 Parameters5.6.3 Variables5.6 References
Chapter 6. Financial risk assessment and optimal planning of biofuels supply chains under uncertainty6.1 Introduction6.2 Problem statement6.3 Mathematical model formulation for Chapter 66.4 Objective 1: Expected profit6.5 Objective 2: Worst case for the net annual profit6.6 Results and discussion6.6.1 Distribution of raw material price without correlation6.6.2 Case with correlated values6.7 Concluding remarks6.8 Nomenclature6.8.1 Variables6.8.2 Binary variables6.8.3 Parameters
Chapter 7. Stochastic design of biorefinery supply chains considering economic and environmental objectives7.1 Introduction7.2 Problem statement7.3 Mathematical formulation7.3.1 Availability of raw material7.3.2 Mass balances in the suppliers7.3.3 Mass balances in the processing facilities7.3.4 Mass balances in the markets7.3.5 Demand constraint7.3.6 Relationships for the input-output of the distributed material7.3.7 Transportation limits and transportation costs7.3.8 Processing stages in the processing facilities7.3.9 Processing constraints for the first stage7.3.10 Processing constraints for the second stage7.3.11 Storage modelling7.3.12 Revenue for selling of products7.3.13 Raw material production cost7.3.14 Economic objective function7.3.15 Environmental objective7.4. Solution approach7.4.1 Definition of the superstructure7.4.2 Identification of the parameters under uncertainty7.4.3 Sampling for uncertain parameters7.4.4 Solving of the associated deterministic optimization problem7.4.5 Comparison between different supply chain topologies7.4.6 Changing of the upper limit for the environmental impact7.4.7 Standardized regression coefficients7.5. Case study7.6. Computer-Aided Tools7.7. Results and discussion7.8. Concluding remarks for Chapter7 7.10. Nomenclature7.10.1 Indexes7.10.2 Variables7.10.3 Parameters7.11 References
Chapter 8. Mixed-integer dynamic optimization or planning distributed biorefineries8.1 Introduction8.2 Problem statement8.3 Mixed-integer dynamic mathematical optimization model8.3.1 Raw material inventory in suppliers8.3.2 Raw material inventory in processing facilities8.3.3 Raw material inventory in main processing facility8.3.4 Product inventory in processing facilities8.3.5 Product inventory in main processing facility8.3.6 Product inventory in distribution centers8.3.7 Continuity of the inventories at the beginning and at the end of the time horizon8.3.8 Raw material orders from facilities to suppliers8.3.9 Raw material orders from main facility to suppliers8.3.10 Product orders from distribution centers to facilities8.3.11 Product orders from distribution centers to main facility8.3.12 Product orders from consumers to distribution centers8.3.13 Continuity of the inventories at the beginning and at the end of the horizon8.3.14 Availability of raw material8.3.15 Constraints for the demand8.3.16 Constraints to control the orders from consumers to distribution centers8.3.17 Constraints for transported flow rate at the outlet and inlet locations8.3.18 Transportation limits8.3.19 Processing8.3.20 Economies of scale for processing facilities8.3.21 Storage modeling8.3.22 Operating cost8.3.23 Total capital cost8.3.24 Transportation cost8.3.25 Storage cost 8.3.26 Net annual Profit8.3.27 Control product demand8.4 Nonlinear model predictive control approach8.5 Solution approach for the MIDO problem8.6 Results8.7 Conclusions8.8 Nomenclature8.8.1 Parameters8.8.2 Binary variables8.8.3 Variables8.9 References
AppendicesAppendix A - GAMS code for the model of Chapter 2Appendix B – GAMS code for the model of Chapter 3Appendix C – GAMS code for the model of Chapter 4Appendix D – GAMS code for the model of Chapter 6Appendix E – GAMS code for the model of Chapter 7Appendix F – GAMS code for the model of Chapter 8
- Edition: 1
- Published: March 8, 2019
- Language: English
JP
José Maria Ponce-Ortega
JS