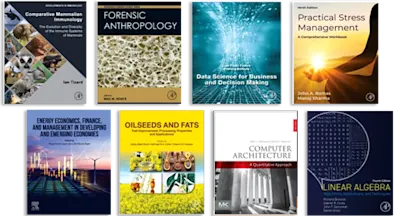
Steel and Its Heat Treatment
- 2nd Edition - November 13, 2013
- Imprint: Butterworth-Heinemann
- Author: Karl-Erik Thelning
- Language: English
- Hardback ISBN:9 7 8 - 0 - 4 0 8 - 0 1 4 2 4 - 3
- Paperback ISBN:9 7 8 - 1 - 4 8 3 1 - 3 1 0 0 - 9
- eBook ISBN:9 7 8 - 1 - 4 8 3 1 - 6 3 4 2 - 0
Steel and Its Heat Treatment, Second Edition presents information, research, and developments in the heat treatment of steel. The book contains chapters that discuss the… Read more
Purchase options
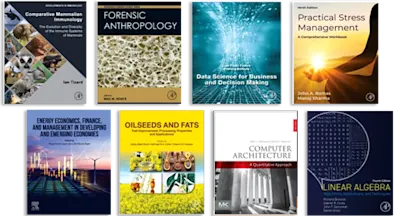
Steel and Its Heat Treatment, Second Edition presents information, research, and developments in the heat treatment of steel. The book contains chapters that discuss the fundamentals of TTT-diagrams and hardening mechanisms, injection metallurgy and continuous casting, annealing processes, strain aging and temper brittleness. Existing CCT-diagrams are subjected to critical review, the mechanisms controlling hardenability are discussed, and the detailing of the properties of boron constructional steels, micro-alloyed steels and dual-phase steels are also included. Metallurgists, metal workers, and engineers will find the book very useful.
PrefaceInternational Designations and Symbols1 Fundamental Metallographic Concepts 1.1 The Transformations and Crystal Structures of Iron 1.2 The Iron-Carbon Equilibrium Diagram 1.2.1 Heating 1.2.2 Cooling 1.3 Time-Temperature-Transformation 1.3.1 Heating 1.3.2 Cooling 1.3.3 Formation of Pearlite 1.3.4 Formation of Bainite 1.3.5 Formation of Martensite 1.3.6 Retained Austenite 1.3.7 TTT Diagrams and CCT Diagrams 1.4 Decomposition of Martensite and Retained Austenite on Tempering 1.5 Diffusion 1.5.1 The Nature of Diffusion 1.5.2 Factors That Influence the Rate of Diffusion 1.5.3 Calculation of Diffusion Distance 1.6 Dislocations 1.7 Grain Size 1.7.1 Grain Boundaries 1.7.2 Methods of Determining Grain Size 1.7.3 Examples of Grain Size Determinations 1.8 Hardening Mechanisms in Steel 1.8.1 Solution Hardening 1.8.2 Grain Size Effect Hardening 1.8.3 Dispersed-Phase Hardening 1.8.4 Work Hardening 1.8.5 Other Hardening Mechanisms2 Materials Testing 2.1 the Hardness Test 2.1.1 The Brinell Test 2.1.2 The Vickers Test 2.1.3 The Knoop Test 2.1.4 The Rockwell Test 2.1.5 The Scleroscope Test 2.1.6 Conversion Tables for Various Scales of Hardness 2.2 The Tensile Test 2.2.1 Comparison Between Mechanical Properties Obtained According to Different Specifications 2.3 The Impact Test 2.4 The Torsion Impact Test 2.5 The Fatigue Test 2.5.1 Fatigue in General 2.5.2 Test Procedure 2.5.3 Different Types of Fatigue Fracture 2.5.4 Goodman Diagram 2.5.5 Endurance Limit—Ultimate Tensile Strength 2.5.6 Surface Finish 2.5.7 Influence of Change of Section 2.5.8 Ways of Increasing the Endurance Limit 2.6 The Creep Test 2.7 Brittle and Ductile Fractures 2.8 Fracture Toughness 2.8.1 the Implication of Fracture Toughness3 Alloying Elements in Steel and New Steelmaking Processes 3.1 Solids 3.1.1 Austenite-Forming Elements 3.1.2 Ferrite-Forming Elements 3.1.3 Multi-Alloyed Steels 3.1.4 Carbide-Forming Elements 3.1.5 Carbide Stabilizers 3.1.6 Nitride-Forming Elements 3.1.7 Effect on Ferrite Hardness 3.1.8 Effect on Grain Growth 3.1.9 Effect on the Eutectoid Point 3.1.10 Effect on the Temperature of Martensite Formation 3.1.11 Effect on the Formation of Pearlite and Bainite During the Isothermal Transformation 3.1.12 Effect on Resistance to Tempering 3.2 Gases 3.2.1 Hydrogen 3.2.2 Nitrogen 3.2.3 Oxygen 3.3 New Steelmaking Processes 3.3.1 Vacuum Remelting 3.3.2 Electroslag Refining 3.3.3 Vacuum Degassing 3.3.4 The Bofors Method of Sulphur Removal 3.3.5 Injection Metallurgy 3.3.6 Effect of Sulphur on the Properties of Steel 3.3.7 Continuous Casting4 Hardenability 4.1 General Remarks 4.2 The Grossmann Hardenability Test 4.2.1 Calculation of Di-Values from the Chemical Composition 4.3 The Jominy End-Quench Hardenability Test 4.3.1 Calculation of Jomimy Curves from the Chemical Composition 4.3.2 Practical Applications of Jomimy Curves 4.4 Practical Application of the TTT and the CCT Diagrams 4.4.1 How Should TTT Diagrams be Used? 4.4.2 Various Types of CCT Diagram 4.4.3 A New Generation of CCT Diagrams 4.4.4 Mechanisms that Control Hardenability 4.4.5 Computing CCT Diagrams From TTT Diagrams 4.5 Practical Application of Hardenability 4.5.1 High Hardenability 4.5.2 Low Hardenability 4.6 The Influence of the Depth of Hardening on the Stress Pattern5 Heat Treatment—General 5.1 Annealing 5.1.1 Spheroidizing Anneal or Annealing for Maximum Softness 5.1.2 Recrystallization Annealing 5.1.3 Stress-Relief Annealing 5.1.4 Isothermal Annealing 5.1.5 Quench Annealing 5.1.6 Homogenizing Annealing 5.1.7 Hydrogen Annealing 5.1.8 Hydrogen Expulsion 5.2 Normalizing 5.3 Hardening 5.3.1 Heating Media 5.3.2 Rate of Heating 5.3.3 Hardening Temperature 5.3.4 Holding Time at Temperature 5.3.5 Methods of Cooling 5.3.6 Quenching Media 5.3.7 Quenching Equipment 5.4 Tempering 5.4.1 Heating to Temperature 5.4.2 Rate of Heating 5.4.3 Holding Time 5.4.4 Double Tempering 5.4.5 Self-Tempering (Auto-Tempering) 5.4.6 Temper Brittleness 5.5 Transformation of Retained Austenite 5.6 Precipitation Hardening 5.7 Strain-Ageing 5.8 Straightening 5.9 Machining Allowances6 Heat Treatment—Special 6.1 Hardening and Tempering of Tool Steels 6.1.1 Carbon Steels and Vanadium-Alloyed Steels 6.1.2 Low-Alloy Cold-Work Steels 6.1.3 Low-Alloy Cold-Work and Hot-Work Steels 6.1.4 High-Alloy Cold-Work Steels 6.1.5 Hot-Work Steels 6.1.6 High-Speed Steels 6.2 Hardening and Tempering of Conventional Constructional Steels 6.2.1 Definitions 6.2.2 Plain Carbon Steels 6.2.3 Alloy Steels 6.2.4 Stainless Steels 6.2.5 Spring Steels 6.2.6 Ultra High-Strength Steels 6.2.7 Hadfield Steel 6.3 Hardening and Tempering of Boron-Alloyed Steels 6.3.1 Boron Steels in General 6.3.2 Chemical Composition of Boron Steels 6.3.3 Hardening Mechanism of Boron Steels 6.3.4 Evaluation of the Effects of Boron on Hardenability 6.3.5 Effect of Titanium on the Properties of Boron Steels 6.3.6 Heat Treatment of Boron Steels 6.3.7 Properties of Boron Steels and Cr-Mo Steels—A Comparison 6.3.8 Fields of Applications for Boron Steels 6.4 Heat Treatment of High-Strength Low-Alloy Constructional (HSLA) Steels 6.4.1 High-Strength Low-Alloy Steels in General 6.4.2 Weldable High-Strength Low-Alloy Steels. Steel Grades and Quality Classes 6.4.3 Dual-Phase Steels 6.4.4 High-Strength Low-Alloy Pearlitic Steels 6.5 Case Hardening 6.5.1 Definitions 6.5.2 Grades of Steel 6.5.3 Methods of Carburizing 6.5.4 Influence of Heat Treatment and Steel Composition on Case Depth, Surface Hardness, Core Hardness and Microstructure 6.5.5 Fatigue Strength of Case-Hardened Steel 6.5.6 Recommendations for Case Hardening 6.5.7 Case Hardening of Tool Steels 6.5.8 Protection Against Carburization (Selective Carburizing) 6.5.9 Choice of Case-Hardening Depth 6.6 Carbonitriding 6.6.1 Definition 6.6.2 Theoretical Background 6.6.3 Practical Results 6.6.4 Conclusions 6.7 Nitriding 6.7.1 Determination of Depth of Nitriding 6.7.2 Methods of Nitriding 6.7.3 Comparison Between Gas and Salt-Bath Nitriding 6.7.4 Nitridability 6.7.5 Nitriding Different Types of Steel 6.7.6 Properties of Nitrided Steels 6.8 Bonding 6.9 Induction Hardening 6.9.1 Fundamental Principles 6.9.2 Steel Grades for Induction Hardening 6.9.3 Equipment for Induction Hardening 6.9.4 Working Coils and Fixtures 6.9.5 Procedure During Induction Hardening 6.9.6 Determination of Depth of Hardening 6.9.7 the Influence of Various Factors on Hardness and Depth of Hardening 6.9.8 Examples of Induction-Hardened Machine Components 6.9.9 Advantages and Disadvantages of Induction Hardening 6.10 Flame Hardening 6.10.1 Methods of Flame Hardening 6.10.2 Hardness and Depth of Hardening 6.10.3 Examples of Flame-Hardened Machine Components and Tools7 Dimensional Changes During Hardening and Tempering 7.1 Dimensional Changes During Hardening 7.1.1 Thermal Stresses 7.1.2 Transformation Stresses 7.2 Dimensional Changes During Tempering 7.2.1 Changes in Volume 7.2.2 Changes in Stress Conditions 7.3 Examples of Dimensional Changes During the Hardening and Tempering of Tool Steels 7.3.1 Plain-Carbon Steels 7.3.2 Low-Alloy Steels 7.3.3 High-Alloy Cold-Work Steels 7.3.4 Hot-Work Steels 7.3.5 High-Speed Steels 7.4 Dimensional Changes During Case Hardening 7.5 Dimensional Changes During Nitriding 7.6 Ageing 7.7 Designing for Heat Treatment8 Tables 8.1 Weight Tables for Steel Bars Table 8.1 Round and Square Bars. Metric Units Table 8.2 Hexagonal and Octagonal Bars. Metric Units Table 8.3 Flat Bars, Width 10 to 40 Mm. Metric Units Table 8.4 Flat Bars, Width 45 to 130 Mm. Metric Units Table 8.5 Flat Bars, Width 140 to 350 Mm. Metric Units Table 8.6 Round and Square Bars. Inch Units Table 8.7 Hexagonal and Octagonal Bars. Inch Units Table 8.8 Flat Bars, Width 3/8 to 1/2 in. Inch Units Table 8.9 Flat Bars, Width 15/8 to 5 in. Inch Units Table 8.10 Flat Bars, Width 51/2 to 15 in. Inch Units 8.2 Conversion Tables for Temperature Table 8.11 Conversion Table for °Celsius (Centigrade) and °Fahrenheit 8.3 Conversion Tables for Size Table 8.12 Inches to Millimetres Table 8.13 Decimals of an Inch to Millimetres 8.4 Conversion Tables for Weight (Mass) Table 8.14 Pounds to Kilograms Table 8.15 British Units to Kilograms 8.5 Conversion Tables for Stress (Pressure) Table 8.16 Tons Per Square Inch to Kiloponds Per Square Millimetre Table 8.17 Tons Per Square Inch to Newtons Per Square Millimetre Table 8.18 Kiloponds Per Square Millimetre to Newtons Per Square Millimetre Table 8.19 Pounds Per Square Inch to Kiloponds Per Square Millimetre 8.6 Conversion Tables for Energy Table 8.20 Kilopond Metres to Footpounds Table 8.21 Footpounds to Kilopond Metres Table 8.22 Kilopond Metres to Joules Table 8.23 Footpounds to Joules 8.7 Conversion Table for Fracture Toughness Units Table 8.24 Fracture Toughness Units 8.8 Conversions for Some Common Units Table 8.25 Common SI Units to British Units Table 8.26 Common Non-SI Metric Units to British Units Table 8.27 Non-SI Metric Units to SI Units 8.9 Elements Table 8.28 Atomic Number and Atomic WeightIndex
- Edition: 2
- Published: November 13, 2013
- Imprint: Butterworth-Heinemann
- Language: English
Read Steel and Its Heat Treatment on ScienceDirect