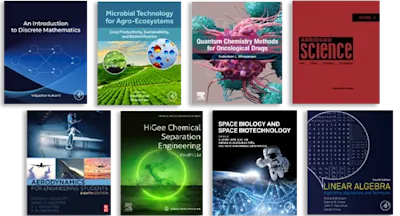
Sintering: From Empirical Observations to Scientific Principles
- 1st Edition - March 18, 2014
- Author: Randall German
- Language: English
- Hardback ISBN:9 7 8 - 0 - 1 2 - 4 0 1 6 8 2 - 8
- eBook ISBN:9 7 8 - 0 - 1 2 - 4 0 1 6 7 7 - 4
As sintering applications march toward a $30 billion global business, the models for sintering have progressed, but generally follow behind observation. Documentation of the st… Read more
Purchase options
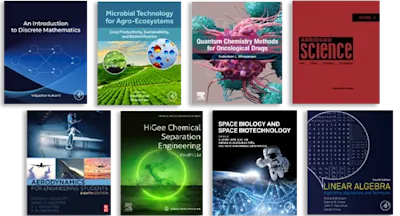
As sintering applications march toward a $30 billion global business, the models for sintering have progressed, but generally follow behind observation. Documentation of the steps needed to build to a quantitative and predictive theory are often missed. Sintering: From Empirical Observations to Scientific Principles partitions sintering applications and observations to show critical turning points required to establish modern sintering as a predictive science.
This book, written by the most cited author in his field, is laced with people, organizations, critical steps, and important formulations in a mixture of history, personalities, and applications. Exploring how insights in seemingly unrelated fields sparked progress, it is also a teaching tool to show where there is success, where there are problems, and how to organize teams to leapfrog to new applications or plateaus of use. Randall German's Sintering: From Empirical Observations to Scientific Principles is a platform for directly addressing the critical control parameters in these new research and development efforts.
- Shows how the theories and understanding of sintering were developed and improved over time, and how different products were developed, ultimately leading to important knowledge and lessons for solving real sintering problems
- Covers all the necessary infrastructure of sintering theory and practice, such as atomic theory, surface energy, microstructure, and measurement and observation tools
- Introduces the history and development of such early sintered products as porcelain, tungsten lamp filaments, bronze bearings, steel automotive components, platinum crucibles and more
Sintering professionals and researchers; product/process engineers; faculty, upper-level undergraduates, and graduate students of mechanical, materials, and metallurgical engineering.
Dedication
Preface
Chapter One. Introduction
Context
Perspectives
Definitions
Sintering Techniques
Knowledge
Key Resources
References
Chapter Two. History of Sintering
Historical Milestones
Early Sintered Products
Interdependent Developments
Key Lessons from Sintering History
References
Chapter Three. Infrastructure Developments
Qualitative Sintering Theory
Emergence of Quantitative Sintering Concepts
Infrastructure Development
Experimental Tools
Organizational Advances
Integration
Status of Sintering Theory
References
Chapter Four. Measurement Tools and Experimental Observations
Changes During Sintering
Particle Bonding
Mechanical Properties
Dimensional Change
Density, Densification, Porosity
Conductivity
Magnetic Properties
Surface Area and Gas Permeability
Pore Structure
Microstructure
Thermal Properties
Summary
References
Chapter Five. Early Quantitative Treatments
Introduction
Onset of Sintering Science
Copper Sintering
References
Chapter Six. Geometric Trajectories during Sintering
Overview
Stages of Sintering
Interface Curvature and Energy
Microstructure Changes
Macrostructure Changes–Component Size and Shape
Surface Area Trajectory
Summary
References
Chapter Seven. Thermodynamic and Kinetic Treatments
Curvature Gradients and Stress
Atmospheric Reactions
Mass Transport Mechanisms
Kinetic Relations
Processing Variables
Summary
References
Chapter Eight. Microstructure Coarsening
Introduction
Grain Coarsening
Pore Structure Changes
Coarsening Interactions
Summary
References
Chapter Nine. Sintering With a Liquid Phase
Overview
Conceptual Developments
Microstructure Development
Preliquid Stage
Liquid Formation
Solution-Reprecipitation
Final Stage Solid Skeletal Sintering
Transient Liquids
Supersolidus Sintering
Reactive Liquids
Infiltration Sintering
Activated Liquid Phase Sintering
Practical Aspects
Summary
References
Chapter Ten. Sintering With External Pressure
Role of External Pressure
Thermal Softening
Pressure Effects
Diffusion and Creep
Multiple Mechanism Densification Rates
Density and Mechanism Maps
Microstructure Evolution
Pressure Application Techniques
Densification Limitations
References
Chapter Eleven. Mixed Powders and Composites
Importance
Physical Interactions
Chemical Interactions
Solubility Role
Co-fire, Laminated, and Bimaterial Sintering
Summary
References
Chapter Twelve. Rapid Heating Approaches
Introduction
Early Demonstrations
Nanoscale Options
Rapid Heating Techniques
Exothermic
Supplemental Pressure
Prospects
References
Chapter Thirteen. Nanoscale Sintering
Overview
Role of Particle Size
Sintering Temperature
Unchanged Thermodynamics
Time-Temperature-Particle Size
Models versus Experiment
Solution Windows
Two-Step Sintering
Opportunities
References
Chapter Fourteen. Computer Models
Introduction
Procedures
Data Requirements
Atomistic Calculations
Reshaping Models
Physical Event Models
Monte Carlo Methods
Continuum Models and Finite Element Analysis
Discrete Element Method
Master Sintering Curve
Neural Networks
Summary Comments
References
Chapter Fifteen. Sintering Practice
Critical Metrics
Control Parameters
Atmosphere
Equipment
Cycles
Costs
Examples
Summary
References
Chapter Sixteen. Future Prospects for Sintering
Linkages
New Materials
New Applications
New Processes
Concluding Remarks
References
Index
- Edition: 1
- Published: March 18, 2014
- Language: English
RG
Randall German
include the Tesla Medal, Nanyang Professorship, Japan Institute for Materials Research
Lectureship, Penn State Engineering Society Outstanding Research Award and Premiere
Research Award, Distinguished Research Award from the Japan Society for Powder Metallurgy,
Kuczynski Prize, and Samsonov Prize. He is listed in several Who's Who and serves as an editor
or key reader for more than 20 journals and held several director positions, including two terms
with APMI, and served on the Fellows Awards Committee of two professional societies.
He has supervised 100 theses, published over 960 articles, 25 patents, and 16 books, including Mathematical Relations in Particulate Materials Processing (2008), Powder Metallurgy and Particulate Materials Processing (2005), Liquid Phase Sintering (1985), Sintering Theory and Practice (1996), and Powder Injection Molding - Design and Applications (2003). He has edited 19 books and co-chaired more than 30 conferences.
Professor German's research and teaching deal with the net-shape fabrication of engineering materials via sintering techniques as used in powder metallurgy, cemented carbides, and ceramics.