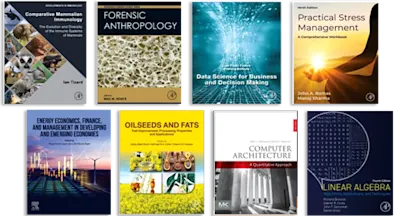
Science and Technology of Liquid Metal Coolants in Nuclear Engineering
- 1st Edition - August 25, 2022
- Imprint: Woodhead Publishing
- Author: Thiagarajan Gnanasekaran
- Language: English
- Paperback ISBN:9 7 8 - 0 - 3 2 3 - 9 5 1 4 5 - 6
- eBook ISBN:9 7 8 - 0 - 3 2 3 - 9 5 8 6 7 - 7
Science and Technology of Liquid Metal Coolants in Nuclear Engineering is a comprehensive consolidation of the latest research and knowledge on liquid metal coolants. Over the… Read more
Purchase options
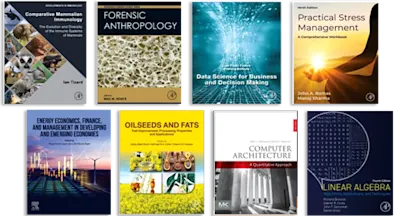
Science and Technology of Liquid Metal Coolants in Nuclear Engineering is a comprehensive consolidation of the latest research and knowledge on liquid metal coolants. Over the last decades, various new technologies have been developed for the liquid metal coolants of fast breeder and fusion reactors and accelerator driven systems. Details of pumps and instrumentation used in these coolants and their operating principles are included to provide the reader with a well-rounded understanding of the topic and to guide on the operation of different liquid metal coolant systems.
Methods for the safe handling and control of impurity levels in these coolants are clearly discussed, along with alkali metal fires and their management, including methods for safe disposal of sodium waste.
- Discusses the thermophysical and chemical properties of liquid metals described with their microscopic origin
- Includes methods for the safe handling of liquid metal coolants and their purification and management
- Discusses pumps and instrumentation principles and design
Researchers and graduates of advanced nuclear reactor systems, fast breeder reactors, fusion reactors, and accelerator driven systems; those designing and handling liquid metal coolants; those coming to the topic from adjacent fields. Nuclear facility construction engineers
Chapter-1 Thermophysical properties of liquid metals and choice of liquid metal coolants for advanced nuclear systems
Introduction
Metallic bonding and the state of liquid metals
Cohesive energy of liquid metals
Structure of liquid metals
Surface energy of liquids and the phenomenon of wetting
Surface energies of liquid metals and alloys
Surface energies of metallic solids
Wetting in liquid metal systems
Inert wetting
Reactive wetting
Viscosity of liquid metals
Electrical conductivity of metallic materials
Electrical conductivity of crystalline metals
Electrical conductivity of amorphous solid and liquid metals
Thermal conductivity of materials
Thermal conductivity of solid-state materials
Thermal conductivity of liquid metals
Molar heat capacity of liquid metals
Vapour pressure of liquid metals
Magnetic properties of metals
Magnetic properties of solid-state materials
1.10.1.1. Diamagnetism
1.10.1.2 Paramagnetism
(a) Simple ionic system
(b) Simple metals
1.10.1.3 Ferromagnetism
1.10.2 Magnetic properties of molten metals
1.11 Nuclear properties of the candidate liquid metal coolants
1.12 Choice of liquid metal coolants for the advanced nuclear systems
1.12.1 Fast breeder reactors
1.12.2 Tokomak Fusion reactor – choice of lithium and Pb-Li eutectic as coolant and tritium breeder
1.12.3 Accelerator driven system - choice of lead and lead-bismuth eutectic as spallation target and coolant
References
Chapter-2 Chemical properties of liquid metal coolants
2.0 Introduction
2.1 Alkali metal coolants
2.1.1 Production of alkali metal coolants
2.1.2 Preparation of high purity alkali metals
2.1.3 Chemical reactions of alkali metals and NaK alloys
2.1.3.1 Reactions with air and oxygen
2.1.3.2 Reactions with nitrogen
2.1.3.3 Reactions with hydrogen and water
2.1.3.4 Reactions with graphite and carbon bearing materials
2.1.3.5 Mutual interactions between dissolved impurities in liquid alkali metals
2.2 Heavy liquid metal coolants
2.2.1 Production of lead, bismuth, LBE and eutectic PbLi alloy
2.2.2 Reactions of lead, bismuth and LBE with air, oxygen, hydrogen and water
2.2.3 Reactions of Pb-Li eutectic with oxygen, water vapour, hydrogen and nitrogen
2.3 Solubility of metallic and non-metallic species in liquid metals
2.4 Kinetics of precipitation and dissolution of solutes in liquid metals
2.4.1 Kinetics of precipitation of solutes in liquid sodium
2.4.2 Kinetics of dissolution of solutes in liquid metals
2.4.2.1 Dissolution of sodium oxide into liquid sodium
2.4.2.2 Dissolution of sodium hydroxide into liquid sodium
2.4.2.3 Dissolution of lead monoxide into liquid lead and LBE
References
Chapter-03 Handling of liquid metal coolants – purification, chemical characterization, metal fires and their extinguishment methods, disposal of liquid metal wastes
3.0 Introduction
3.1 Handling alkali metals
3.1.1 Handling sodium metal
3.1.2 Handling lithium metal
3.1.3 Handling NaK alloy
3.1.4 Storage of alkali metals
3.2 Handling lead, LBE and Pb-Li eutectic alloys
3.3 Purification of liquid metal coolants
3.3.1 Purification of liquid metals in heat transfer circuits
3.3.1.1 Filtration
3.3.1.2 Cold trapping
3.3.1.3 Hot trapping
3.3.1.4 Controlling concentration of dissolved oxygen in heavy metals
i. Control by equilibration with gas phase sources
ii. Control by equilibration with solid PbO source
iii. Control by electrochemical oxygen pumping
3.3.2 Removal of radioactive impurity elements from liquid metal coolants
3.3.2.1 Removal of tritium from liquid lithium circuits
3.3.2.2 Nuclide traps for liquid sodium coolant
3.3.2.3 Removal of polonium from liquid lead and LBE coolants
3.4 Chemical characterization of liquid metals
3.4.1 Samplers for liquid metal systems
3.4.1.1 Samplers for liquid alkali metals
i. Samplers for use in the secondary sodium circuits of FBRs and experimental sodium loops
ii. Samplers for use in the primary sodium circuits of FBRs
3.4.1.2 Samplers for use in heavy liquid metal circuits
3.4.2 Chemical analysis of impurities in alkali metals
3.4.3 Chemical analysis of impurities in heavy liquid metals
3.5 Alkali metal fires and fire extinguishers
3.5.1 Sodium fires
3.5.1.1 Sodium pool fires
3.5.1.2 Sodium spray fire
3.5.2 Lithium fires
3.5.3 Methods of extinguishing alkali metal fires
3.6 Disposal of sodium
3.6.1 Disposal of small quantities of sodium and residual sodium from the components
3.6.1.1 Disposal of sodium by reacting with water
3.6.1.2 Disposal of residual sodium by using alcohols
3.6.1.3 Removal of residual sodium by gas phase reactants
3.6.1.4 Methods to form concentrated waste by reacting with oxygen or slags from metallurgical processes
3.6.2 Disposal of very large quantities of sodium
3.7 Regeneration of cold traps of sodium systems
References
Chapter-04 Pumps and Instrumentation for liquid metal circuits
4.0 Introduction
4.1 Pumps for liquid metal circuits
4.1.1 Centrifugal pumps
4.1.2 Electromagnetic pumps
4.1.2.1 Electromagnetic conduction pumps
a. DC conduction pumps
b. AC conduction pumps
4.1.2.2 Electromagnetic induction pumps
a. Flat Linear Induction Pump (FLIP)
b. Annular Linear Induction Pump (ALIP)
c. Flow-through ALIP
d. Reflux-type ALiP
4.1.2.3 Factors influencing the choice of electromagnetic pumps
4.2 Level measurements in liquid metals
4.2.1 Conductivity-based level probes
a. Discrete level probes
b. Continuous level probes
4.2.2 Level probes based on principles of induction
a. Continuous level probes
b. Discrete level probes
c. Ex-vessel level probes
4.3 Flow measurements in liquid metal circuits
4.3.1 Methods based on electromagnetic principles
4.3.1.1 Flow measurements in small diameter pipes
a. Permanent magnet flow meters (PMFM)
b. Lorentz force velocity meter
4.3.1.2 Flow measurements in large diameter pipes
a. Bypass type PMFM
b. Probe type PMFM
c. Side-wall flow meter
d. Eddy current flow meter (or flux distortion flow meter)
4.3.2 Flow meters based on ultrasonic principles
4.3.2.1 Ultrasonic doppler velocimetry based flow meter
4.3.2.2 Transit time based ultrasonic flow meter
4.4 Viewing of components immersed in liquid metals
4.4.1 Design of ultrasonic transducers for use in liquid metal circuits and their general characteristics
4.4.2 Characteristics of an ultrasound wave generated by a flat piezoelectric crystal
4.4.3 Resolution in ultrasonic imaging of components immersed in liquid metals
4.4.3.1 Axial resolution
4.4.3.2 Lateral resolution
4.4.4 Ultrasonic scanning system for FBRs
4.5 Detectors for liquid metal leaks
4.5.1 Wire-type leak detectors
4.5.2 Sandwich and multilayer type leak detectors
4.5.3 Spark-plug type leak detectors
4.5.4 Mutual inductance type leak detectors
4.5.5 Fibre-optics based leak detectors
4.5.6 Sodium-togas leak detectors
4.5.6.1 Smoke detectors
4.5.6.2 Sodium ionization detector (SID)
4.5.6.3 Sensors based on Na-ion conducting solid electrolyte
4.5.6.4 Sampling and chemical analysis of aerosols containing sodium bearing species
4.6 On-line Impurity monitors for liquid metal coolants
4.6.1 Impurity monitors for liquid sodium systems
4.6.1.1 Plugging indicator
4.6.1.2 Resistivity meter
4.6.1.3 Monitors for on-line measurement of hydrogen in sodium circuits
A. Monitors for measuring hydrogen dissolved in liquid sodium
I. Monitors operating in dynamic mode
II. Monitors operating in equilibrium mode
B. Monitors for measuring hydrogen in argon cover gas
4.6.1.4 Monitors for on-line measurement of carbon levels in liquid sodium
4.6.1.4.1 Diffusion based monitors
a. UNC carbon meter
b. Harwell, HEDL and ANL Carbon monitors
4.6.1.4.2 Electrochemical carbon monitors
a. Monitors using molten carbonate electrolytes
b. Monitors using solid-oxide electrolyte with either CO+ CO2 mixture or CO2
4.6.1.5 Monitors for on-line measurement of oxygen in sodium
4.6.2 Monitors for lithium circuits
4.6.3 Monitors for liquid Pb-17Li alloy circuits
4.6.4 Oxygen monitors for heavy liquid metal coolant circuits
References
Chapter-05 Corrosion and mass transfer in liquid metal systems
5.0 Introduction
5.1 General factors that determine corrosion mass transfer of structural materials in liquid metals systems
5.1.1 Solubility of the components of the structural alloys in liquid metals
5.1.2 Role of dissolved non-metallic impurities in corrosion and mass transfer
5.1.3 Influence of the liquid metal flow velocity and position of the corroding section in the hot leg
5.2 Corrosion and mass transfer in liquid sodium systems
5.2.1 Solubility of alloying elements of structural steels and non-metallic impurities in liquid sodium
5.2.2 Thermochemical aspects of Na-M-O systems (M= alloying elements of structural steels) and their influence on corrosion mechanisms
5.2.3 Carbon transport in sodium-steel systems
5.3 Corrosion and mass transfer in liquid lithium systems
5.3.1 Corrosion of steels
5.3.1 Corrosion of vanadium alloys
5.4 Corrosion and mass transfer of steels in liquid lead and lead-bismuth eutectic systems
5.4.1 Corrosion by direct dissolution
5.4.2 Corrosion under oxidizing conditions
5.4.3 Erosion-corrosion
5.4.4 Mitigation of corrosion in lead and LBE circuits
5.5 Corrosion and mass transfer in lead-lithium circuits
5.5.1 Corrosion of austenitic steels by Pb-Li
5.5.2 Corrosion of reduced activity ferritic-martensitic (RAFM) steels
5.6 Wetting of structural materials by liquid metals
5.6.1 Wetting by liquid alkali metals
5.6.2 Wetting by Pb-Li alloy
5.6.3 Wetting by Pb and LBE alloys
References
Epilogue Future perspectives and research needs
Annexures:
Annexure-01 Radial Distribution function and structure of liquid metals
Annexure-02 Ferromagnetism in materials
Annexure-03 Basics of heat transfer in liquid metals
Annexure-04 Thermochemical aspects of dissolution of solutes in liquid metals
Annexure-05 Kinetics of precipitation of solutes from solutions
Annexure-06 Magnetic effects of current and inductance
Annexure-07 Propagation of sound in matter
Annexure-08 Piezoelectricity and piezoelectric crystals
Annexure-09 Solid electrolytes and their applications as chemical sensors
Annexure-10 Lessons learnt from past incidents and the recommended safety measures while handling liquid metal systems
- Edition: 1
- Published: August 25, 2022
- Imprint: Woodhead Publishing
- Language: English
TG