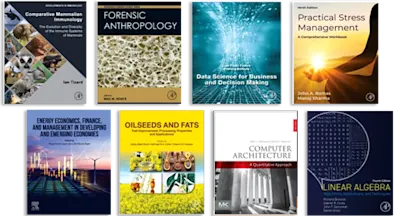
Rotary Kilns
Transport Phenomena and Transport Processes
- 2nd Edition - November 21, 2015
- Imprint: Butterworth-Heinemann
- Author: Akwasi A. Boateng
- Language: English
- Paperback ISBN:9 7 8 - 0 - 1 2 - 8 0 3 7 8 0 - 5
- eBook ISBN:9 7 8 - 0 - 1 2 - 8 0 3 8 5 3 - 6
Rotary Kilns—rotating industrial drying ovens—are used for a wide variety of applications including processing raw minerals and feedstocks as well as heat-treating hazardous wa… Read more
Purchase options
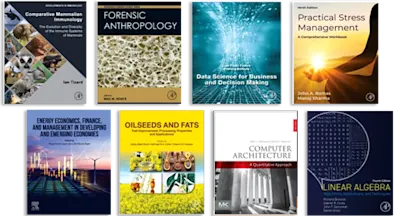
Rotary Kilns—rotating industrial drying ovens—are used for a wide variety of applications including processing raw minerals and feedstocks as well as heat-treating hazardous wastes. They are particularly critical in the manufacture of Portland cement. Their design and operation is critical to their efficient usage, which if done incorrectly can result in improperly treated materials and excessive, high fuel costs. This professional reference book will be the first comprehensive book in many years that treats all engineering aspects of rotary kilns, including a thorough grounding in the thermal and fluid principles involved in their operation, as well as how to properly design an engineering process that uses rotary kilns.
This new edition contains an updated CFD section with inclusion of recent case studies and in line with recent developments covers pyrolysis processes, torrefaction of biomass, application of rotary kilns in C02 capture and information on using rotary kilns as incinerators for hydrocarbons.
- Provides essential information on fluid flow, granular flow, mixing and segregation, and aerodynamics during turbulent mixing and recirculation
- Gives guidance on which fuels to choose, including options such as natural gas versus coal-fired rotary kilns
- Covers principles of combustion and flame control, heat transfer and heating and material balances
- New edition contains information on pyrolysis processes with low temperatures and torrefaction of biomass. It also covers calcination of petcoke, how rotary kilns are used as incinerators for chlorinated hydrocarbons.
- Includes updated material on CFD simulation of kiln gas and solids flow with a selection of recent case studies.
Professional Mechanical Engineers working in heating and drying processes; Chemical Engineers; Materials Engineers.
- Dedication
- Foreword to the First Edition
- Foreword to the Second Edition
- Preface to the First Edition
- Preface to the Second Edition
- 1. The Rotary Kiln Evolution and Phenomenon
- 1.1. The Rotary Kiln Evolution
- 1.2. Types of Rotary Kilns
- 2. Basic Description of Rotary Kiln Operation
- 2.1. Bed Phenomenon
- 2.2. Geometrical Features and Their Transport Effects
- 2.3. Transverse Bed Motion
- 2.4. Experimental Observations of Transverse Flow Behavior
- 2.5. Axial Motion
- 2.6. Dimensionless Residence Time
- 3. Freeboard Aerodynamic Phenomena
- 3.1. Fluid Flow in Pipes: General Background
- 3.2. Basic Equations of Multicomponent Reacting Flows
- 3.3. Development of a Turbulent Jet
- 3.4. Confined Jets
- 3.5. Swirling Jets
- 3.6. Precessing Jets
- 3.7. The Particle-Laden Jet
- 3.8. Dust Entrainment
- 3.9. ID Fan
- 4. Granular Flows in Rotary Kilns
- 4.1. Flow of Granular Materials (Granular Flows)
- 4.2. The Equations of Motion for Granular Flows
- 4.3. Particulate Flow Behavior in Rotary Kilns
- 4.4. Overview of the Observed Flow Behavior in a Rotary Drum
- 4.5. Particulate Flow Model in Rotary Kilns
- 4.6. Model Results and Validation
- 4.7. Application of the Flow Model
- 5. Mixing and Segregation
- 5.1. Modeling of Particle Mixing and Segregation in Rotary Kilns
- 5.2. Bed Segregation Model
- 5.3. The Governing Equations for Segregation
- 5.4. Boundary Conditions
- 5.5. Solution of the Segregation Equation
- 5.6. Numerical Solution of the Governing Equations
- 5.7. Validation of the Segregation Model
- 5.8. Application of Segregation Model
- 6. Combustion and Flame
- 6.1. Combustion
- 6.2. Mole and Mass Fractions
- 6.3. Combustion Chemistry
- 6.4. Practical Stoichiometry
- 6.5. Adiabatic Flame Temperature
- 6.6. Types of Fuels Used in Rotary Kilns
- 6.7. Coal Types, Ranking, and Analysis
- 6.8. Petroleum Coke Combustion
- 6.9. Scrap Tire Combustion
- 6.10. Pulverized Fuel (Coal/Coke) Firing in Kilns
- 6.11. Pulverized Fuel Delivery and Firing Systems
- 6.12. Estimation of Combustion Air Requirement
- 6.13. Reaction Kinetics of Carbon Particles
- 6.14. Fuel Oil Firing
- 6.15. Combustion Modeling
- 6.16. Flow Visualization Modeling (Acid–Alkali Modeling)
- 6.17. Mathematical Modeling Including CFD
- 6.18. Gas-Phase Conservation Equations Used in CFD Modeling
- 6.19. Particle-Phase Conservation Equations Used in CFD Modeling
- 6.20. Emissions Modeling
- 6.21. CFD Evaluation of a Rotary Kiln Pulverized Fuel Burner
- 7. Freeboard Heat Transfer
- 7.1. Overview of Heat Transfer Mechanisms
- 7.2. Conduction Heat Transfer
- 7.3. Convection Heat Transfer
- 7.4. Conduction–Convection Problems
- 7.5. Shell Losses
- 7.6. Refractory Lining Materials
- 7.7. Heat Conduction in Rotary Kiln Wall
- 7.8. Radiation Heat Transfer
- 7.9. Radiation Shape Factors
- 7.10. Radiation Exchange between Multiple Gray Surfaces
- 7.11. Radiative Effect of Combustion Gases
- 7.12. Heat Transfer Coefficients for Radiation in the Freeboard of a Rotary Kiln
- 7.13. Radiative Exchange from the Freeboard Gas to Exposed Bed and Wall Surfaces
- 7.14. Radiative Heat Transfer among Exposed Freeboard Surfaces
- 8. Heat Transfer Processes in the Rotary Kiln Bed
- 8.1. Heat Transfer between the Covered Wall and the Bed
- 8.2. Modified Penetration Model for Rotary Kiln Wall-to-Bed Heat Transfer
- 8.3. Effective Thermal Conductivity of Packed Beds
- 8.4. Effective Thermal Conductivity in Rotating Bed Mode
- 8.5. Thermal Modeling of Rotary Kiln Processes
- 8.6. Description of the Thermal Model
- 8.7. One-Dimensional Thermal Model for Bed and Freeboard
- 8.8. Two-Dimensional Thermal Model for the Bed
- 8.9. The Combined Axial and Cross-Sectional Model—The Quasi-Three-Dimensional Model for the Bed
- 8.10. Solution Procedure
- 8.11. Model Results and Application
- 8.12. Single-Particle Heat Transfer Modeling for Expanded Shale Processing
- 9. Mass and Energy Balance
- 9.1. Chemical Thermodynamics
- 9.2. Gibbs Free Energy and Entropy
- 9.3. Global Heat and Material Balance
- 9.4. Thermal Module for Chemically Reactive System
- 9.5. Mass Balance Inputs
- 9.6. Chemical Compositions
- 9.7. Energy Balance Inputs
- 9.8. Site Survey—Measured Variables
- 9.9. Shell Heat Loss Calculations
- 9.10. Calcination Module Calculation
- 9.11. Combustion
- 9.12. Energy Balance Module
- 9.13. Sensible Energy for Output Streams
- 10. Rotary Kiln Minerals Process Applications
- 10.1. Lime Making
- 10.2. Limestone Dissociation (Calcination)
- 10.3. The Rotary Lime Kiln
- 10.4. The Cement-Making Process
- 10.5. The Cement Process Chemistry
- 10.6. Rotary Cement Kiln Energy Usage
- 10.7. Mineral Ore Reduction Processes in Rotary Kilns
- 10.8. The Rotary Kiln Lightweight Aggregate-Making Process
- 10.9. The Rotary Kiln Pyrolysis/Carbonization
- 11. Rotary Kiln Petroleum Coke Calcination Process: Some Design Considerations
- 11.1. Introduction
- 11.2. The Rotary Calcining Integrated System
- 11.3. Direct-Fired Kiln Characteristics
- 11.4. Mass Balance
- 11.5. Thermal Balance and Energy Use
- 11.6. Volatile Matter
- 11.7. Dust Output and Pickup
- 11.8. Fixed Carbon Recovery and Burnout
- 11.9. Kinetics and Product Quality
- 11.10. Direct-Fired Pet-Coke Kiln Temperature Profiles
- 11.11. Design Structure
- 11.12. Computational Fluid Dynamic Modeling (Pyroscrubber)
- 12. Rotary Kiln Environmental Applications
- 12.1. Basic Regulatory Framework for Waste Burning Kilns
- 12.2. Hazardous Waste Incineration
- 12.3. Dual Use—Combustion Systems
- 12.4. Carbon Emissions, Reduction, and Capture
- Appendix
- Index
- Edition: 2
- Published: November 21, 2015
- Imprint: Butterworth-Heinemann
- Language: English
AB