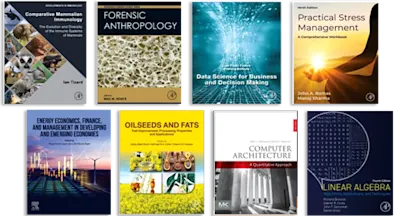
Residual Stresses in Friction Stir Welding
- 1st Edition - November 22, 2013
- Imprint: Butterworth-Heinemann
- Authors: Nilesh Kulkarni, Rajiv S. Mishra, John A. Baumann
- Language: English
- Paperback ISBN:9 7 8 - 0 - 1 2 - 8 0 0 1 5 0 - 9
- eBook ISBN:9 7 8 - 0 - 1 2 - 8 0 0 7 3 2 - 7
This book describes the fundamentals of residual stresses in friction stir welding and reviews the data reported for various materials. Residual stresses produced during ma… Read more
Purchase options
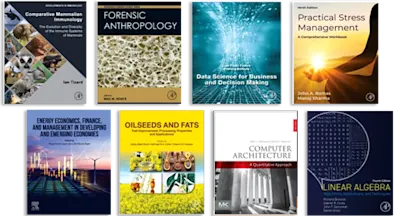
This book describes the fundamentals of residual stresses in friction stir welding and reviews the data reported for various materials. Residual stresses produced during manufacturing processes lead to distortion of structures. It is critical to understand and mitigate residual stresses. From the onset of friction stir welding, claims have been made about the lower magnitude of residual stresses. The lower residual stresses are partly due to lower peak temperature and shorter time at temperature during friction stir welding. A review of residual stresses that result from the friction stir process and strategies to mitigate it have been presented. Friction stir welding can be combined with additional in-situ and ex-situ manufacturing steps to lower the final residual stresses. Modeling of residual stresses highlights the relationship between clamping constraint and development of distortion. For many applications, management of residual stresses can be critical for qualification of component/structure.
- Reviews magnitude of residual stresses in various metals and alloys
- Discusses mitigation strategies for residual stresses during friction stir welding
- Covers fundamental origin of residual stresses and distortion
Researchers, welding engineers, materials processing engineers, design engineers and students
Preface to the Friction Stir Welding and Processing Book Series
Chapter 1. Introduction
1.1 Residual Stresses
1.2 Implication of RS
Chapter 2. A Brief Introduction to FSW
Chapter 3. RS in FSW Process
3.1 Materials Studied
3.2 RS in Aluminum Alloys
3.3 RS in Other Materials
3.4 Summary of RS in Ferrous and Nonferrous Materials
Chapter 4. Effect of RS on Properties
4.1 Mechanical Properties
4.2 Stress-Corrosion Cracking
Chapter 5. Parameters Affecting RS
5.1 The Effect of Tool Traverse Speed
5.2 The Effect of Tool Rotation Rate
5.3 Sample Size for Measurement of RS
Chapter 6. Characterization of RS
Chapter 7. Model for Understanding Residual Stress Development in Friction Stir-Welded Structures
7.1 Description of the Model
7.2 Computational Validation of the Model
7.3 Differences in RS in Fusion Welding and FSW
Chapter 8. Mitigation of RS During FSW
8.1 The Effect of Heat Sink (Thermal Tensioning) on the Residual Stress
8.2 The Effect of Mechanical Tensioning on the Residual Stress
8.3 The Effect of Roller Tensioning on the Residual Stress
8.4 The Effect of Laser and Shot Peening on RS
Chapter 9. Simulation of FSW for RS and Distortions
Chapter 10. Summary, Conclusions, and Future Direction
References
- Edition: 1
- Published: November 22, 2013
- Imprint: Butterworth-Heinemann
- Language: English
NK
Nilesh Kulkarni
RM
Rajiv S. Mishra
Prof. Rajiv Mishra (Ph.D. in Metallurgy from University of Sheffield) is a Regents Professor at the University of North Texas and founder of Optimus Alloys LLC. He is a Fellow of ASM International. He is a past-chair of the Structural Materials Division of TMS and served on the TMS Board of Directors (2013-16). He has authored/co-authored more than 450 papers in peer-reviewed journals and proceedings and is principal inventor of four U.S. patents. His current Google Scholar h-index is 95 and his papers have been cited more than 43000 times. He has co-authored three books; (1) Friction Stir Welding and Processing, (2) Metallurgy and Design of Alloys with Hierarchical Microstructures, (3) High Entropy Materials: Processing, Properties, and Applications. He has edited or co-edited fifteen TMS conference proceedings. He was an associate editor of Journal of Materials Processing Technology and is the founding editor of a short book series on Friction Stir Welding and Processing published by Elsevier and has co-authored seven short books in this series. He is a recipient of TMS-SMD Distinguished Scientist Award in 2020 and TMS-MPMD Distinguished Scientist Award in 2024. He is an adjunct professor in the department of Materials Science and Engineering at North Carolina State University. Most recently, he has founded Optimus Alloys LLC for commercialization of research efforts and serves as the Chief Scientific Advisor. Optimus Alloys is focused on process-specific alloy design for additive manufacturing of high-performance components.
JB