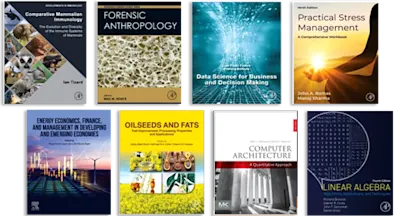
Residual Stresses in Composite Materials
- 2nd Edition - June 24, 2021
- Imprint: Woodhead Publishing
- Editor: Mahmood M. Shokrieh
- Language: English
- Paperback ISBN:9 7 8 - 0 - 1 2 - 8 1 8 8 1 7 - 0
- eBook ISBN:9 7 8 - 0 - 1 2 - 8 1 8 8 1 8 - 7
The residual stress is a common phenomenon in composite materials. They can either add to or significantly reduce material strength. Because of the increasing demand for… Read more
Purchase options
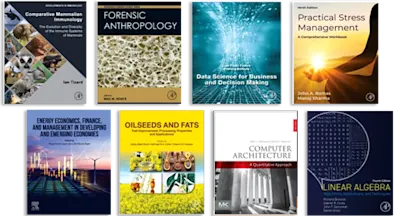
The residual stress is a common phenomenon in composite materials. They can either add to or significantly reduce material strength. Because of the increasing demand for high-strength, lightweight materials such as composites and their wide range of applications; it is critical that the residual stresses of composite materials are understood and measured correctly.
The first edition of this book consists of thirteen chapters divided into two parts. The first part reviews destructive and non-destructive testing (NDT) techniques for measuring residual stresses. There are also additional chapters on using mathematical (analytical and numerical) methods for the calculation of residual stresses in composite materials. These include the simulated hole drilling method, the slitting/crack compliance method, measuring residual stresses in homogeneous and composite glass materials using photoelastic techniques, and modeling residual stresses in composite materials. The second part of the book discusses measuring residual stresses in different types of composites including polymer and metal matrix composites. The addition of nanoparticles to the matrix of polymeric composites as a new technique for the reduction of residual stresses is also discussed.
In the Second Edition of this book, each of the original chapters of the first edition has been fully updated, taking into account the latest research and new developments. There are also five new chapters on the theoretical and experimental studies of residual stresses in the composite integrated circuits; residual stresses in additive manufacturing of polymers and polymer matrix composites; residual stresses in metal matrix composites fabricated by additive manufacturing; the eigenstrain based method for the incremental hole-drilling technique; and the estimation of residual stresses in polymer matrix composites using the digital image correlation technique.
Residual Stresses in Composite Materials, Second Edition, provides a unique and comprehensive overview of this important topic and is an invaluable reference text for both academics and professionals working in the mechanical engineering, civil engineering, aerospace, automotive, marine, and sporting industries.
The first edition of this book consists of thirteen chapters divided into two parts. The first part reviews destructive and non-destructive testing (NDT) techniques for measuring residual stresses. There are also additional chapters on using mathematical (analytical and numerical) methods for the calculation of residual stresses in composite materials. These include the simulated hole drilling method, the slitting/crack compliance method, measuring residual stresses in homogeneous and composite glass materials using photoelastic techniques, and modeling residual stresses in composite materials. The second part of the book discusses measuring residual stresses in different types of composites including polymer and metal matrix composites. The addition of nanoparticles to the matrix of polymeric composites as a new technique for the reduction of residual stresses is also discussed.
In the Second Edition of this book, each of the original chapters of the first edition has been fully updated, taking into account the latest research and new developments. There are also five new chapters on the theoretical and experimental studies of residual stresses in the composite integrated circuits; residual stresses in additive manufacturing of polymers and polymer matrix composites; residual stresses in metal matrix composites fabricated by additive manufacturing; the eigenstrain based method for the incremental hole-drilling technique; and the estimation of residual stresses in polymer matrix composites using the digital image correlation technique.
Residual Stresses in Composite Materials, Second Edition, provides a unique and comprehensive overview of this important topic and is an invaluable reference text for both academics and professionals working in the mechanical engineering, civil engineering, aerospace, automotive, marine, and sporting industries.
- Presents the latest developments on theoretical and experimental studies of residual stresses in composites
- Reviews destructive and non-destructive testing (NDT) techniques for measuring residual stresses
- Discusses residual stresses in the polymer matrix, metal matrix, and ceramic matrix composites
- Considers the addition of nanoparticles to the matrix as a new technique for reduction of residual stresses in polymeric composites
- Introduces the latest advancements of research on the residual stresses in additive-manufactured polymer and metal matrix composites
Academics and professionals working in the mechanical engineering, civil engineering, aerospace, automotive, marine and sporting industries
Part I: Measurement and modelling
1. The importance of measuring residual stresses in composite materials
2. Destructive techniques in the measurement of residual stresses in composite materials: an overview
3. Non-destructive testing (NDT) techniques in the measurement of residual stresses in composite materials: an overview
4. Measuring residual stresses in composite materials using the simulated hole drilling method
5. Measuring residual stresses in composite materials using the slitting/crack compliance method
6. Modeling residual stresses in composite materials
Part II: Residual stresses in different types of composite
7. Understanding residual stresses in polymer matrix composites
8. Understanding residual stresses in metal matrix composites
9. Toughening and strengthening mechanisms in ceramic nanocomposites
10. Understanding residual stresses in thick polymer composite laminates
11. The cured shape prediction of bistable laminates
12. Reduction of residual stresses in polymer composites using nano-additives
Part III: Advanced Topics
13. Incremental hole-drilling measurement of residual stresses through the thickness of composite microelectronics components
14. Residual stresses in additive manufacturing of polymers and polymer matrix composites
15. The eigenstrain-based method for the incremental hole-drilling technique
16. Estimation of residual stresses in polymer-matrix composites using digital image correlation
1. The importance of measuring residual stresses in composite materials
2. Destructive techniques in the measurement of residual stresses in composite materials: an overview
3. Non-destructive testing (NDT) techniques in the measurement of residual stresses in composite materials: an overview
4. Measuring residual stresses in composite materials using the simulated hole drilling method
5. Measuring residual stresses in composite materials using the slitting/crack compliance method
6. Modeling residual stresses in composite materials
Part II: Residual stresses in different types of composite
7. Understanding residual stresses in polymer matrix composites
8. Understanding residual stresses in metal matrix composites
9. Toughening and strengthening mechanisms in ceramic nanocomposites
10. Understanding residual stresses in thick polymer composite laminates
11. The cured shape prediction of bistable laminates
12. Reduction of residual stresses in polymer composites using nano-additives
Part III: Advanced Topics
13. Incremental hole-drilling measurement of residual stresses through the thickness of composite microelectronics components
14. Residual stresses in additive manufacturing of polymers and polymer matrix composites
15. The eigenstrain-based method for the incremental hole-drilling technique
16. Estimation of residual stresses in polymer-matrix composites using digital image correlation
- Edition: 2
- Published: June 24, 2021
- Imprint: Woodhead Publishing
- Language: English
MS
Mahmood M. Shokrieh
Mahmood M. Shokrieh is a distinguished Professor at the School of Mechanical Engineering, Iran University of Science and Technology (IUST), Tehran, Iran. He is the founder of the Iran Scientific Composites Association and Iran Industrial Composites Association. He is the director of the Composites Research Laboratory (CRL) of the School of Mechanical Engineering of IUST. He is the Chief Editor of the Journal of Science and Technology of Composites, published by IUST. His research interests include mechanics of composite materials; mechanics of nano-composites; stress and failure analysis of composite materials; fatigue analysis of composite materials; experimental methods in composite materials; and finite element analysis.
Affiliations and expertise
Professor, Composites Research Laboratory, School of Mechanical Engineering, Iran University of Science and Technology (IUST), Tehran, IranRead Residual Stresses in Composite Materials on ScienceDirect