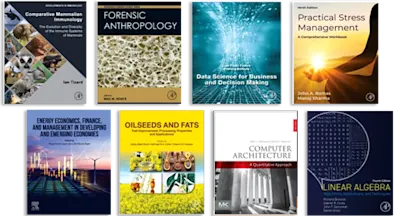
Reliability, Maintainability and Risk
Practical Methods for Engineers
- 9th Edition - March 21, 2017
- Imprint: Butterworth-Heinemann
- Author: David J. Smith
- Language: English
- Paperback ISBN:9 7 8 - 0 - 0 8 - 1 0 2 0 1 0 - 4
- eBook ISBN:9 7 8 - 0 - 0 8 - 1 0 2 0 2 2 - 7
Reliability, Maintainability and Risk: Practical Methods for Engineers, Ninth Edition, has taught reliability and safety engineers techniques to minimize process design, operation… Read more
Purchase options
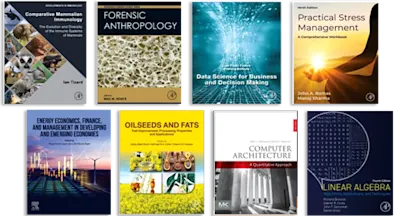
Reliability, Maintainability and Risk: Practical Methods for Engineers, Ninth Edition, has taught reliability and safety engineers techniques to minimize process design, operation defects, and failures for 35 years.
For beginners, the book provides tactics on how to avoid pitfalls in this complex and wide field. For experts in the field, well-described, realistic, and illustrative examples and case studies add new insight and assistance. The author uses his 40 years of experience to create a comprehensive and detailed guide to the field, also providing an excellent description of reliability and risk computation concepts.
The book is organized into five parts. Part One covers reliability parameters and costs traces the history of reliability and safety technology, presenting a cost-effective approach to quality, reliability, and safety. Part Two deals with the interpretation of failure rates, while Part Three focuses on the prediction of reliability and risk.
Part Four discusses design and assurance techniques, review and testing techniques, reliability growth modeling, field data collection and feedback, predicting and demonstrating repair times, quantified reliability maintenance, and systematic failures, while Part 5 deals with legal, management and safety issues, such as project management, product liability, and safety legislation.
- Additional chapter on helicopter and aviation safety record
- Coverage of models for partial valve stroke test, fault tree logic and quantification difficulties
- More detail on use of tools such as FMEDA and programming standards like MISRA
Part 1: Understanding Reliability Parameters and Costs
Chapter 1: The History of Reliability and Safety Technology
- Abstract
- 1.1. Failure Data
- 1.2. Hazardous Failures
- 1.3. Predicting Reliability and Risk
- 1.4. Achieving Reliability and Safety-Integrity
- 1.5. The RAMS-Cycle
- 1.6. Contractual and Legal Pressures
- 1.7. Reliability versus Functional Safety
Chapter 2: Understanding Terms and Jargon
- Abstract
- 2.1. Defining Failure and Failure Modes
- 2.2. Failure Rate and Mean Time Between Failures
- 2.3. Interrelationships of Terms
- 2.4. The Bathtub Distribution
- 2.5. Down Time and Repair Time
- 2.6. Availability, Unavailability and Probability of Failure on Demand
- 2.7. Hazard and Risk-Related Terms
- 2.8. Choosing the Appropriate Parameter
Chapter 3: A Cost-Effective Approach to Quality, Reliability and Safety
- Abstract
- 3.1. Reliability and Optimum Cost
- 3.2. Costs and Safety
- 3.3. The Cost of Quality
Part 2: Interpreting Failure Rates
Chapter 4: Realistic Failure Rates and Prediction Confidence
- Abstract
- 4.1. Data Accuracy
- 4.2. Sources of Data
- 4.3. Data Ranges
- 4.4. Confidence Limits of Prediction
- 4.5. Manufacturers’ Data (Warranty Claims)
- 4.6. Overall Conclusions
Chapter 5: Interpreting Data and Demonstrating Reliability
- Abstract
- 5.1. The Four Cases
- 5.2. Inference and Confidence Levels
- 5.3. The Chi-Square Test
- 5.4. Understanding the Method in More Detail
- 5.5. Double-Sided Confidence Limits
- 5.6. Reliability Demonstration
- 5.7. Sequential Testing
- 5.8. Setting Up Demonstration Tests
Chapter 6: Variable Failure Rates and Probability Plotting
- Abstract
- 6.1. The Weibull Distribution
- 6.2. Using the Weibull Method
- 6.3. More Complex Cases of the Weibull Distribution
- 6.4. Continuous Processes
Part 3: Predicting Reliability and Risk
Chapter 7: Basic Reliability Prediction Theory
- Abstract
- 7.1. Why Predict RAMS?
- 7.2. Probability Theory
- 7.3. Reliability of Series Systems
- 7.4. Redundancy Rules
- 7.5. General Features of Redundancy
- Exercises
Chapter 8: Methods of Modeling
- Abstract
- 8.1. Block Diagrams and Repairable Systems
- 8.2. Common Cause (Dependent) Failure
- 8.3. Fault Tree Analysis
- 8.4. Event Tree Diagrams
Chapter 9: Quantifying the Reliability Models
- Abstract
- 9.1. The Reliability Prediction Method
- 9.2. Allowing for Diagnostic Intervals
- 9.3. FMEDA (Failure Mode and Diagnostic Analysis)
- 9.4. Human Factors
- 9.5. Simulation
- 9.6. Comparing Predictions with Targets
Chapter 10: Risk Assessment (QRA)
- Abstract
- 10.1. Frequency and Consequence
- 10.2. Perception of Risk, ALARP and Cost per Life Saved
- 10.3. Hazard Identification
- 10.4. Factors to Quantify
Part 4: Achieving Reliability and Maintainability
Chapter 11: Design and Assurance Techniques
- Abstract
- 11.1. Specifying and Allocating the Requirement
- 11.2. Stress Analysis
- 11.3. Environmental Stress Protection
- 11.4. Failure Mechanisms
- 11.5. Complexity and Parts
- 11.6. Burn-In and Screening
- 11.7. Maintenance Strategies
Chapter 12: Design Review, Test and Reliability Growth
- Abstract
- 12.1. Review Techniques
- 12.2. Categories of Testing
- 12.3. Reliability Growth Modeling
Chapter 13: Field Data Collection and Feedback
- Abstract
- 13.1. Reasons for Data Collection
- 13.2. Information and Difficulties
- 13.3. Times to Failure
- 13.4. Spreadsheets and Databases
- 13.5. Best Practice and Recommendations
- 13.6. Analysis and Presentation of Results
- 13.7. Manufacturers’ data
- 13.8. Anecdotal Data
- 13.9. Examples of Failure Report Forms
- 13.10. No-Fault-Found (NFF)
Chapter 14: Factors Influencing Down Time
- Abstract
- 14.1. Key Design Areas
- 14.2. Maintenance Strategies and Handbooks
Chapter 15: Predicting and Demonstrating Repair Times
- Abstract
- 15.1. Prediction Methods
- 15.2. Demonstration Plans
Chapter 16: Quantified Reliability Centered Maintenance
- Abstract
- 16.1. What is QRCM?
- 16.2. The QRCM Decision Process
- 16.3. Optimum Replacement (Discard)
- 16.4. Optimum Spares
- 16.5. Optimum Proof Test
- 16.6. Condition Monitoring
Chapter 17: Systematic Failures, Especially Software
- Abstract
- 17.1. Random versus Systematic Failures
- 17.2. Software-related Failures
- 17.3. Software Failure Modeling
- 17.4. Software Quality Assurance (Life Cycle Activities)
- 17.5. Modern/Formal Methods
- 17.6. Software Checklists
Part 5: Legal, Management and Safety Considerations
Chapter 18: Project Management and Competence
- Abstract
- 18.1. Setting Objectives and Making Specifications
- 18.2. Planning, Feasibility and Allocation
- 18.3. Program Activities
- 18.4. Responsibilities and Competence
- 18.5. Functional Safety Capability
- 18.6. Standards and Guidance Documents
Chapter 19: Contract Clauses and Their Pitfalls
- Abstract
- 19.1. Essential Areas
- 19.2. Other Areas
- 19.3. Pitfalls
- 19.4. Penalties
- 19.5. Subcontracted Reliability Assessments
Chapter 20: Product Liability and Safety Legislation
- Abstract
- 20.1. The General Situation
- 20.2. Strict Liability
- 20.3. The Consumer Protection Act 1987
- 20.4. Health and Safety at Work Act 1974
- 20.5. Insurance and Product Recall
Chapter 21: Major Incident Legislation
- Abstract
- 21.1. History of Major Incidents
- 21.2. Development of major incident legislation
- 21.3. Safety reports
- 21.4. Offshore Safety Cases
- 21.5. Problem Areas
- 21.6. Rail
- 21.7. Corporate Manslaughter and Corporate Homicide
Chapter 22: Integrity of Safety-Related Systems
- Abstract
- 22.1. Safety-Related or Safety-Critical?
- 22.2. Safety-Integrity Levels (SILs)
- 22.3. Programable electronic systems (PESs)
- 22.4. Current guidance
- 22.5. Framework for Certification
Chapter 23: A Case Study: The Datamet Project
- Abstract
- 23.1. Introduction
- 23.2. The Datamet Concept
- 23.3. The Contract
- 23.4. Detailed Design
- 23.5. Syndicate Study
- 23.6. Hints
Chapter 24: A Case Study: Gas Detection System
- Abstract
- 24.1. Safety-Integrity Target
- 24.2. Random Hardware Failures
- 24.3. ALARP
- 24.4. Architectures
- 24.5. Life-Cycle Activities
- 24.6. Functional Safety Capability
Chapter 25: A Case Study: Pressure Control System
- Abstract
- 25.1. The Unprotected System
- 25.2. Protection System
- 25.3. Assumptions
- 25.4. Reliability Block Diagram
- 25.5. Failure Rate Data
- 25.6. Quantifying the Model
- 25.7. Proposed Design and Maintenance Modifications
- 25.8. Modeling Common Cause Failure (Pressure Transmitters)
- 25.9. Quantifying the Revised Model
- 25.10. ALARP
- 25.11. Architectural Constraints
Chapter 26: Helicopter Incidents and Risk Assessment
- Abstract
- 26.1. Helicopter Incidents
- 26.2. Risk Assessment - Floatation Equipment
- 26.3. Effect of Pilot Experience on Incident Rate
Appendix 1: Glossary
Appendix 2: Percentage Points of the Chi-Square Distribution
Appendix 3: Microelectronic Failure Rates
Appendix 4: General Failure Rates
Appendix 5: Failure Mode Percentages
Appendix 6: Human Error Probabilities
Appendix 7: Fatality Rates
Appendix 8: Answers to Exercises
Appendix 9: Bibliography
Appendix 10: Scoring Criteria for BETAPLUS Common Cause Model
Appendix 11: Example of HAZOP
Appendix 12: HAZID Checklist
Appendix 13: Markov Analysis of Redundant Systems
Appendix 14: Calculating the GDF
- Edition: 9
- Published: March 21, 2017
- Imprint: Butterworth-Heinemann
- Language: English
DS