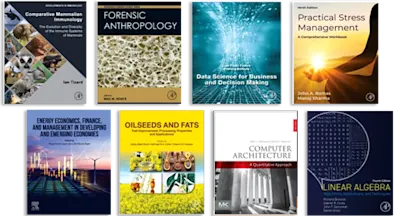
Rare Metal Extraction by Chemical Engineering Techniques
International Series of Monographs on Chemical Engineering
- 1st Edition - July 15, 2014
- Imprint: Pergamon
- Author: W. D. Jamrack
- Editor: P. V. Danckwerts
- Language: English
- eBook ISBN:9 7 8 - 1 - 4 8 3 1 - 8 0 5 6 - 4
Rare Metal Extraction by Chemical Engineering Techniques describes the use of chemical engineering techniques in the extraction and purification of rare metals such as uranium,… Read more
Purchase options
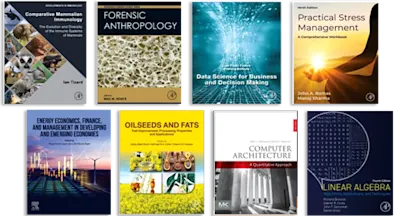
Rare Metal Extraction by Chemical Engineering Techniques describes the use of chemical engineering techniques in the extraction and purification of rare metals such as uranium, thorium, and zirconium as well as hafnium, titanium, beryllium, and vanadium. The various chemical extraction stages from ore to metal are discussed. Comprised of nine chapters, this book begins with an examination of ore breakdown processes including dilute acid leaching and the breakdown of concentrated acids, alkalis, and fluorides as well as chlorination. The reader is then introduced to ion-exchange purification; solvent extraction; and dryway conversion processes. Subsequent chapters focus on metal production by high-temperature reduction techniques; molten salt electrolytic processes; and iodide decomposition processes. The final chapter includes a selection of complete flowsheets for the extraction and purification rare metals from ores. This monograph will be of value to metallurgists, chemical engineers, chemists, and others who are interested in the extraction of rare metals.
Preface
1. Introduction
2. Ore Breakdown Processes
Dilute Acid Leaching
Batch Leaching
Continuous Co-Current Leaching
Continuous Counter-Current Leaching
Percolation Leaching
Leaching Equipment
Ore Treatment Prior to Leaching
Solid-Liquid Separation
Flocculating Agents
Acid Leaching of Uranium Ores
Acid Leaching of Thorite
Concentrated Acid Breakdown
Breakdown Equipment
Sulphuric Acid Breakdown of Monazite
Sulphuric Acid Breakdown of Beryl
Uranium and Vanadium Ore Opening by Concentrated Acid
Alkali Breakdown
Breakdown Equipment
Alkali Breakdown of Monazite
Alkali Breakdown of Zircon
Alkali Treatment of Ferroniobium
Alkali Breakdown of Beryl
Dilute Alkali Carbonate Leaching
Comparison with Dilute Acid Leaching
Application to Uranium and Vanadium Extraction
Chlorination Breakdown
Mineral Chlorination Technique
Plant Constructional Materials
Plant Design
Chlorination of Titanium Ores
Chlorination of Zircon
Chlorination of Monazite
Chlorination of Ferrovanadium
Chlorination of Niobium
Application to Other Ores
Fluoride Breakdown Processes
Fluorination Breakdown of Beryl
Fluoride Breakdown of Zircon
References
3. Ion-Exchange Purification
Theory
Methods of Application
Frontal Analysis Technique
Elution Analysis Technique
Anionic Complexes of Rare Metals
Chemical Composition and Structure of Resins
Cationic Resins
Anionic Resins
Selective Resins
Commercial Resins
Process Design
Optimization of Absorption Stage
Elution Optimization
Scaling-Up
Preservation of Resin
Process Control
Design of Elution Analysis Processes
Ion-Exchange Plant
Columns
Continuous Counter-Current Ion-Exchange
Uranium Extraction by Ion-Exchange
Chemistry of Absorption
Elution
Uranium Extraction Plant
Impurities and Resin Poisons
Precipitation
Ion-Exchange from Carbonate Leach Liquors
Moving Bed Process
Resin-in-Pulp Process
Extraction of Thorium by Ion-Exchange
Extraction from Uranium Barren Liquor
Nitrate and Chloride Systems
Removal of Uranium in a Carbonate System
Cellulose Phosphate Process
Purification of Zirconium by Ion-Exchange
Cation-Exchange of Impurities
Cation-Exchange Separation of Zirconium and Hafnium
Anion-Exchange Separation of Zirconium and Hafnium
Separation of Niobium and Tantalum by Ion-Exchange
Extraction of Vanadium by Ion-Exchange
Acid Process
Carbonate Processes
References
4. Solvent Extraction
Theory
Solvent Systems
Distribution Coefficient
Multiple Batch Extraction
Counter-Current Batch Extraction
Continuous Counter-Current Extraction
Equilibrium Diagrams
Solvent Extraction Plant
Extraction Mechanism
Extraction Columns
Mixer-Settlers
Centrifugal Extractors
Auxiliary Equipment
Purification of Uranium by Solvent Extraction
Extraction from Ore Leach Liquors
Final Solvent Purification of Uranium
Purification of Thorium by Solvent Extraction
U.K. Process
U.S. Processes
Extraction from Sulphate Solutions
Purification of Zirconium by Solvent Extraction
Hexone-Thiocyanate Process
TBP Process
Purification of Niobium by Solvent Extraction
Hexone Process
TBP Process
References
5. Dryway Conversion Processes
Static Bed Reactors
Stirred Bed Reactors
Rotating Kiln Reactors
Vibrating Tray Reactors
Moving Bed Reactors
Fluidized Bed Reactors
Production of Uranium Tetrafluoride by the Static Bed Method
Production of Thorium Fluoride by the Stirred Bed Process
Production of Uranium Tetrafluoride by the Fluidized Bed Process
U.S. Process
U.K. Process
References
6. Metal Production by High Temperature Reduction Techniques
Theory
Reduction of Oxides
Reduction of Halides
Type of Product
Reaction Conditions
Ingot Production Processes
Form of Reactants
Reduction Plant
Residue Recovery
Calcium Reduction of Uranium Tetrafluoride
Magnesium Reduction of Uranium Tetrafluoride
Magnesium Reduction of Beryllium Fluoride
Calcium Reduction of Vanadium Oxides
Calcium Reduction of Thorium Tetrafluorides
Metal Powder Production Processes
Reductions in Absence of Metal Vapour
Reactions in Presence of Metal Vapour
Powder Recovery
Calcium Reduction of Uranium Dioxide
Calcium Reduction of Thorium Dioxide
Sodium Reduction of Potassium Heptafluoniobate
Hydrogen Reduction of Niobium Trichloride
Metal Sponge Production Processes
Purification of Reagents
Reduction Plant
Sponge Recovery
Magnesium Reduction of Titanium Tetrachloride
Sodium Reduction of Titanium Tetrachloride
Magnesium Reduction of Zirconium Tetrachloride
Magnesium Reduction of Vanadium Trichloride
Magnesium Reduction of Niobium and Tantalum Pentachlorides
References
7. Molten Salt Electrolytic Processes
Comparison with Metal Reduction
Inert Salts
Cell Atmosphere
Electrolysis Plant
Introduction of Rare Metal Salt
Electrolytic Purification
Recovery of Metal Product
Electrolysis of Beryllium Chloride
Production of Uranium Metal by Electrolysis
Zirconium Electrolysis from a Chloride-Fluoride Melt
Production of Thorium Metal by Electrolysis
Production of Titanium Metal by Electrolysis
References
8. Iodide Decomposition Processes
Reaction Conditions
Plant and Equipment
Product Purity
Alternative Feed Materials
Recycling of Residues
Continuous Operation
Production of Titanium by Iodide Decomposition
Production of Zirconium by Iodide Decomposition
Production of Thorium by Iodide Decomposition
References
9. Flowsheets from Ore to Metal
Uranium
Extraction of Uranium (Acid Leach, Ion-Exchange, Fluidization and Magnesium Reduction Process)
Extraction of Uranium (Carbonate Leach, Precipitation, Calcium Reduction of Oxide Process)
Thorium
Extraction of Thorium (Acid Breakdown, Electrolysis Process)
Extraction of Thorium (Alkaline Breakdown, Oxide Reduction, Process)
Zirconium
Extraction of Zirconium (Chlorination, Hexone Purification, Electrolysis Process)
Extraction of Zirconium (Alkaline Breakdown, TBP Purification, Kroll Reduction Process)
Hafnium
Extraction of Hafnium (Zirconium by-Product, Oxide, Carbide, Iodide Decomposition Process)
Titanium
Extraction of Titanium (Chlorination, Distillation, Sodium Reduction Process)
Niobium
Extraction of Niobium (Chlorination, Hydrogen Purification, Magnesium Reduction Process)
Extraction of Niobium (Alkali Dissolution, Solvent Extraction, Sodium Reduction Process)
Tantalum
Extraction of Tantalum (Fluoride Dissolution, Recrystallization of Double Fluoride, Sodium Reduction Process)
Vanadium
Extraction of Vanadium (Chlorination, Distillation, Magnesium Reduction Process)
Beryllium
Extraction of Beryllium (Sulphuric Acid Breakdown, Chlorination and Electrolysis Process)
Extraction of Beryllium (Fluoride Breakdown, Magnesium Reduction of Beryllium Fluoride Process)
Index
- Edition: 1
- Published: July 15, 2014
- Imprint: Pergamon
- Language: English
PD
P. V. Danckwerts
Affiliations and expertise
University of Cambridge, UKRead Rare Metal Extraction by Chemical Engineering Techniques on ScienceDirect