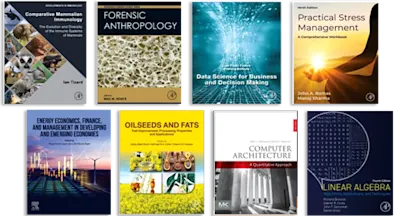
Pulp and Paper Industry
Energy Conservation
- 1st Edition - January 20, 2016
- Imprint: Elsevier
- Author: Pratima Bajpai
- Language: English
- Hardback ISBN:9 7 8 - 0 - 1 2 - 8 0 3 4 1 1 - 8
- eBook ISBN:9 7 8 - 0 - 1 2 - 8 0 3 4 2 8 - 6
Pulp and Paper Industry: Energy Conservation presents a number of energy-efficient technologies and practices that are cost-effective and available for implementation today. Em… Read more
Purchase options
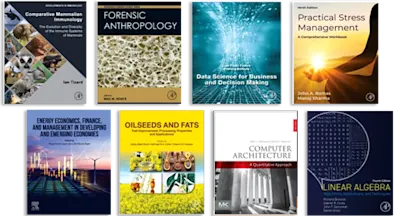
Pulp and Paper Industry: Energy Conservation presents a number of energy-efficient technologies and practices that are cost-effective and available for implementation today. Emerging energy-efficient technologies and future prospects in this field are also dealt with. Qualitative and quantitative results/data on energy savings for various steps of pulp and paper making process are presented. There is no specific book on this topic. This will be a comprehensive reference in the field.
- Thorough and in-depth coverage of energy-efficient technologies and practices in paper and pulp industry
- Presents cost-effective and available for implementation today technologies
- Discusses Biotechnological processes, especially enzymatic processes in the pulp and paper industry to reduce the energy consumption and improve the product quality
- Presents qualitative and quantitative results/data on energy savings for various steps of pulp and paper making process
Pulp and Paper technologist/ Engineers, Paper manufacturers, Paper mill personnel, Senior Paper Scientists and R&D Professionals, Academics, Analysts and Consultants
- Preface
- List of Abbreviations
- Chapter 1: General Background
- Abstract
- Chapter 2: Global Pulp and Paper Production and Consumption
- Abstract
- Chapter 3: Pulp and Paper Production Processes and Energy Overview
- Abstract
- 3.1. Process Description
- 3.2. Greenhouse Gas Emission Sources
- 3.3. Energy Overview
- Chapter 4: Energy Conservation Measures for Raw Material Preparation
- Abstract
- 4.1. Cradle Debarker
- 4.2. Ring-Style Debarkers
- 4.3. Chip Conditioning
- 4.4. Chip-Conveying Systems
- 4.5. Use of Secondary Heat Instead of Steam in Debarking
- 4.6. Automatic Chip Handling and Thickness Screening
- 4.7. Bar-Type Chip Screens
- 4.8. Fine-Slotted Wedge Wire Baskets
- Chapter 5: Energy Conservation Measures for Chemical Pulping
- Abstract
- 5.1. Batch Digester Modification
- 5.2. Continuous Digester
- 5.3. Digester Blow/Flash Heat Recovery
- 5.4. Using Flash Heat in a Continuous Digester to Preheat Chips
- 5.5. Optimization of the Dilution Factor Control
- 5.6. Use of Evaporator Condensates on Decker Showers
- 5.7. Use of Two Pressure Level Steaming of Batch Digesters to Maximize Back-Pressure Power Generation
- 5.8. Use of Digester Additives to Increase Yield
- 5.9. Use of Extended Delignification and Oxygen Delignification
- Chapter 6: Energy Conservation Measures for Bleaching
- Abstract
- 6.1. Improved Brown Stock Washing
- 6.2. Washing Presses
- 6.3. Ozone Bleaching
- 6.4. Heat Recovery
- 6.5. Optimization of the Filtrate Recycling Concept for Optimum Chemical and Energy Use
- Chapter 7: Energy Conservation Measures for Chemical Recovery
- Abstract
- 7.1. Black Liquor Solids Concentration
- 7.2. Lime Kiln Oxygen Enrichment
- 7.3. Lime Kiln Modification
- 7.4. Lime Kiln Electrostatic Precipitators
- 7.5. Improved Composite Tubes for Recovery Boilers
- 7.6. Quaternary Air Injection
- 7.7. Recovery Boiler Deposition Monitoring
- 7.8. Convert Evaporation to Seven-Effect Operation (Install Additional Evaporator Effect)
- 7.9. Performing Evaporator Boilout With Weak Black Liquor
- 7.10. Converting Recovery Boiler to Nondirect Contact and Implementing High Solids Firing
- 7.11. Condensate Stripping
- 7.12. Installation of a Methanol Rectification and Liquefaction System
- 7.13. Tampella Recovery System
- Chapter 8: Energy Conservation Measures for Mechanical Pulping
- Abstract
- 8.1. Energy Efficient TMP Processes
- 8.2. Pressurized Groundwood Pulping
- 8.3. Heat Recovery in Thermomechanical Pulping
- 8.4. Improvements in Chemithermomechanical Pulping
- 8.5. Refiner Improvements
- 8.6. Efficient Repulping Rotors
- 8.7. Continuous Repulping
- 8.8. Countercurrent Coupling of Paper Machine and Mechanical Pulping White Water Systems
- Chapter 9: Energy Conservation Measures for Recovered Fiber Processing
- Abstract
- 9.1. Drum Pulpers
- 9.2. Heat Recovery from Deinking Effluent
- 9.3. Supply of Waste Heat from Other Process Areas to Deinking Plant
- 9.4. Implementation of Closed Heat and Chemical Loop
- 9.5. Increased Use of Recycled Pulp
- 9.6. Fractionation of Recycled Fiber
- Chapter 10: Energy Conservation Measures for Stock Preparation and Papermaking
- Abstract
- 10.1. Shoe (Extended Nip) Press
- 10.2. Advanced Dryer Controls
- 10.3. Optimization of Water Removal in Forming and Pressing
- 10.4. High Consistency Forming
- 10.5. CondebeltTM Drying Process
- 10.6. Hot and Superhot Pressing
- 10.7. Gap Formers
- 10.8. Direct Drying Cylinder Firing
- 10.9. Paper Machine Vacuum System Optimization
- 10.10. Energy Savings Through Heat Recovery Systems
- 10.11. Implementation of Efficient Control Systems for the Machine Steam and Condensate Systems to Eliminate Excessive Blowthrough and Steam Venting During Machine Breaks
- 10.12. Optimization of Pocket Ventilation Temperature
- 10.13. Control of Dew Point
- 10.14. Closing Hoods and Optimizing Ventilation
- 10.15. Infrared Drying and Moisture Profiling
- 10.16. Dry Sheet Forming
- Chapter 11: Emerging Technologies
- Abstract
- 11.1. Gas-Fired Paper Dryer
- 11.2. Air Impingement Drying
- 11.3. Steam Impingement Drying
- 11.4. Impulse Drying
- 11.5. Infrared Drying
- 11.6. Multiport Dryer
- 11.7. Boost Dryer
- 11.8. Advanced Fibrous Fillers
- 11.9. Microwave Drying
- 11.10. Aq-vane Technology
- 11.11. Displacement Pressing
- 11.12. Laser Ultrasonic Stiffness Sensor
- 11.13. New Flotation Deinking Processes
- 11.14. Surfactant Spray Deinking
- 11.15. Pulsed Power Technology for Decontamination of Recycled Paper
- 11.16. Directed Green Liquor Utilization Pulping
- 11.17. Membrane Concentration of Black Liquor
- 11.18. Dual-Pressure Reheat Recovery Boiler
- 11.19. Borate Autocausticizing
- 11.20. Steam Cycle Washing
- 11.21. Black Liquor Gasification
- 11.22. LignoBoost™
- 11.23. Extraction of Hemicellulose Before Chemical Pulping
- 11.24. Utilization of Residuals in Concrete Production
- 11.25. Chemical Pretreatment With Oxalic Acid for Mechanical Pulping
- 11.26. Biopretreatment for Mechanical Pulping
- 11.27. Enzymatic Prebleaching
- 11.28. Enzymatic Refining
- 11.29. Enzymes for Drainage Improvement
- 11.30. Enzymatic Deinking
- 11.31. Enzymatic Debarking
- 11.32. Enzymatic Removal of Shives
- 11.33. Enzymes for Reduction of Vessels in Tropical Hardwoods
- Chapter 12: Future Perspectives
- Abstract
- Index
- Edition: 1
- Published: January 20, 2016
- Imprint: Elsevier
- Language: English
PB