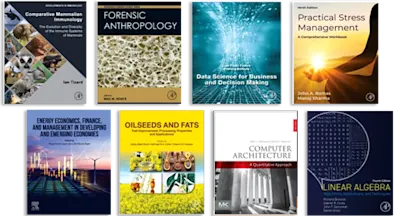
Process Safety Management and Human Factors
A Practitioner’s Experiential Approach
- 1st Edition - November 18, 2020
- Imprint: Butterworth-Heinemann
- Editor: Waddah S. Ghanem Al Hashmi
- Language: English
- Paperback ISBN:9 7 8 - 0 - 1 2 - 8 1 8 1 0 9 - 6
- eBook ISBN:9 7 8 - 0 - 1 2 - 8 1 8 1 1 0 - 2
Process Safety Management and Human Factors: A Practitioner's Experiential Approach addresses human factors in process safety management (PSM) from a reflective learning approa… Read more
Purchase options
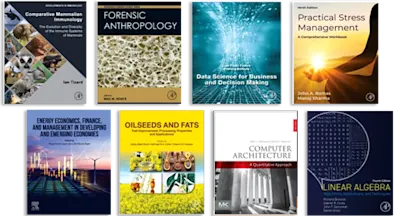
- Covers the evolution and background of process safety management
- Shows how to integrate and augment process safety management with operational excellence and health, safety and environment management systems
- Focuses on human factors in process safety management
- Includes many real-life case studies from the collective experience of the book's authors
Plant and Operational Managers; Senior PSM experts; HSE and Safety Engineers; HSE Managers; Industrial/Occupational Ergonomists/Hygienists; Industrial/Occupational Physiologists working in the field of Safety and Organisational Safety Culture Development; Technical, Asset Integrity and Process Optimization Specialists and Managers. Human Factors Practitioners
1. Introduction to process safety management in a practical context
1.1 Prelude
1.2 Introduction
1.3 The rise of process safety management
1.4 Process safety management and human factors
References
2. Introduction to human factors and the human element
2.1 Introduction
2.2 Terminology and scope
2.3 Why and how human factors are important
2.4 Managing human failures
2.5 Safety critical tasks
2.6 Human factors in design
2.7 Conclusions
References
3. Leadership and process safety management
3.1 Introduction
3.2 Process safety elements: leadership
3.3 Understanding the leadership challenges
3.4 Process safety leadership: a model
3.5 Monitoring and managing process safety management performance
3.6 Way forward and chapter concluding remarks
Further reading
4. The awareness of risk, complacency, and the normalization of deviance
4.1 Introduction
4.2 Toward understanding deviation
4.3 What does complacency mean for process safety?
4.4 Complacency and the normalization of deviance
4.5 The elements of Situational Complacency
4.6 David’s story
4.7 Conclusions
4.8 Final thoughts
References
5. Competence assurance and organizational learning
5.1 Introduction
5.2 Assuring human performance
5.3 Competence and human performance
5.4 Wider organizational learning
5.5 Concluding remarks
References
6. Integration of human factors in hazard identification and risk assessment
6.1 Introduction
6.2 Human factors engineering in design and operational phases
6.3 Task design
6.4 Procedures
6.5 Human resources
6.6 Physical exposures
6.7 Fitness for duty
6.8 Incident investigation
6.9 Safety culture
6.10 Conclusions
Further Reading
7. Inherent safety impact in complying process safety regulations and reducing human error
7.1 Introduction
7.2 The causes of accidents in chemical process industries
7.3 Inherently safer design in process safety management
7.4 Reduction of human error through inherent safety
7.5 Case study
7.6 Conclusion
References
8. Asset and mechanical integrity management
8.1 Preamble
8.2 Process safety model
8.3 People_process_technology alignment to achieve process safety excellence
8.4 Asset integrity management
8.5 Industry case studies
8.6 Human factors
8.7 Way forward and chapter concluding remarks
References
9. Management of change
9.1 Introduction
9.2 The cases for change
9.3 Scope of a management of change
9.4 Change versus "replacement-in-kind"
9.5 Management of change review process
9.6 Management of change closure
9.7 Management of organizational change
9.8 "Minor" change
9.9 Concluding thoughts: modern trends in risk tolerance
References
10. Management of risk through safe work practices
10.1 Introduction
10.2 Human factors in risk management
10.3 Behavioral safety
10.4 Human performance gaps
10.5 Risk management through safe work practices: safe system of work, operating procedures, and safe work practices
10.6 Overview: establishing an effective safe system of work
10.7 Developing an internal document management system and document
framework
10.8 Safety programs
10.9 Summary
References
11. Process safety information, hazard control, and communication
11.1 Introduction
11.2 Process safety information element
11.3 Implementation framework for process safety information
11.4 Human errors applicable to process safety information
11.5 Concluding remarks
Acknowledgment
References
12. Prestart-up and shutdown safety reviews
12.1 Introduction
12.2 Why is a prestart-up safety review required?
12.3 Prestart-up safety review considerations
12.4 Key roles and responsibilities in prestart-up safety reviews
12.5 Prestart-up safety review team
12.6 Prestart-up safety review team composition
12.7 Prestart-up safety review team leader
12.8 Process safety management assessments
12.9 Implementing a prestart-up safety review
12.10 Generating and approval of the prestart-up safety review plan
12.11 Executing the prestart-up safety review
12.12 Field and physical inspections
12.13 Approval of the prestart-up safety review report and corrective actions
12.14 Corrective action management
12.15 Prestart-up safety review completion and closure
12.16 Conclusion
Appendix 1
Reference
13. Contractor management
13.1 Introduction
13.2 Overview of contract life cycle
13.3 Reasons for contracting work
13.4 Developing the scope of work
13.5 Internal/external prequalification
13.6 Site visit verification
13.7 References checks
13.8 Selection of contractors: criteria and weighting and contractor selection criteria
13.9 Stakeholder weighting assignments
13.10 Health, safety, and environment evaluation
13.11 Veto rights
13.12 Commercial assessment
13.13 Risk ranking of contractors
13.14 Contract execution
13.15 Contract/project kick-off
13.16 Contractor premobilization
13.17 HSE Alignment Workshops
13.18 Site-specific training implemented
13.19 Contractor mobilized
13.20 Contractor performance management
13.21 HSE audit: 30 days’ postmobilization
13.22 Leadership visibility
13.23 Listening moments
13.24 Contractor audits
13.25 Corrective action management
13.26 Contractor relationship management
13.27 Contract closeout
References
14. Emergency response management and control
14.1 Introduction
14.2 Why have emergency response plan
14.3 Scope of the Incident Management System or emergency response plan
14.4 Integrated "all-hazards" approach
14.5 Organizational principles of all-hazards approach
14.6 Emergency response priorities
14.7 Emergency management principles
14.8 Objectives-driven response
14.9 Incident action plans
14.10 Common and consistent terminology
14.11 Manageable span of control
14.12 Organizational response structure
14.13 Scalable response
14.14 Response triggers
14.15 Managing incident response through the utilization of the planning cycle
14.16 Business continuity
14.17 Plan linkage
14.18 Application of the Incident Management System in varying response frameworks
14.19 Single command
14.20 Coordinated command
14.21 Coordinated command structure
14.22 Expectations and assumptions for the effective operation of the ERP or IMS
14.23 Human factors in emergency response planning
14.24 Concluding remarks
Further reading
15. Human performance within process safety management compliance assurance
15.1 Introduction
15.2 Sociotechnical systems and human failure
15.3 Gaps within process safety management assurance
15.4 How to assure human performance
15.5 Concluding remarks
References
16. Regulating PSM and the impact of effectiveness
16.1 Introduction
16.2 Purpose of regulations
16.3 Prescriptive and performance-based regulations
16.4 Impact of effectiveness of PSM regulations
16.5 Challenges of having too many regulators
16.6 Chapter concluding remarks
References
17. Readying the organization for change: communication and alignment
17.1 Introduction
17.2 Key elements of organizational readiness and alignment
17.3 Creating a shared PSM vision
17.4 Sharing the vision
17.5 Aligning the organization—organizational change management
17.6 Conducting the stakeholder impact assessment
17.7 Managing organizational change
17.8 Communication methodologies
17.9 Seven best practices in organizational change management
17.10 Summary
References
18. Do we really learn from loss incidents?
18.1 Introduction
18.2 Barriers to learning
18.3 How to learn more effectively from external incidents
18.4 How to make effective recommendations
18.5 Concluding remarks: lessons from history
Acknowledgement
References
Further readings
19. Gauging the effectiveness of implementation and measuring the performance of PSM activities
19.1 Introduction
19.2 PSM assurance
19.3 Design of PSM
19.4 Supervision of PSM
19.5 Verification of PSM
19.6 Metrics for PSM
19.7 Audits of PSM
19.8 Verification workshops
19.9 Validation
19.10 Management review meetings
19.11 Operational intelligence
19.12 Closing thoughts
References
20. Human errors, organization culture, and leadership
20.1 Introduction
20.2 Human error and organizational culture
20.3 The human paradoxes leading to incidents
20.4 Closing thoughts
Epilogue
Appendix 1: Sample PSSR checklist and report
Appendix 2: Reference list and international standards and codes
- Edition: 1
- Published: November 18, 2020
- Imprint: Butterworth-Heinemann
- Language: English
WG