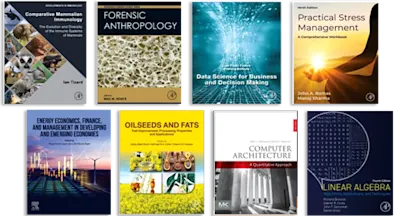
Process Risk and Reliability Management
Operational Integrity Management
- 1st Edition - April 9, 2010
- Imprint: William Andrew
- Author: Ian Sutton
- Language: English
- Hardback ISBN:9 7 8 - 1 - 4 3 7 7 - 7 8 0 5 - 2
- eBook ISBN:9 7 8 - 1 - 4 3 7 7 - 7 8 0 6 - 9
In the last twenty years considerable progress has been made in process safety, particularly in regard to regulatory compliance. Many companies are now looking to go beyond me… Read more
Purchase options
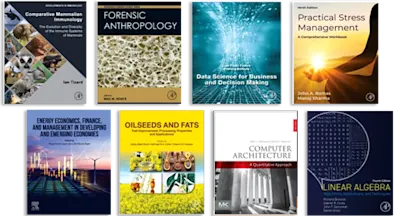
In the last twenty years considerable progress has been made in process safety, particularly in regard to regulatory compliance. Many companies are now looking to go beyond mere compliance; they are expanding their process safety management (PSM) programs to improve performance not just in safety, but also in environmental compliance, quaility control and overall profitability. Techniques and principles are illustrated with numerous examples from chemical plants, refineries, transportation, pipelines and offshore oil and gas.
This book helps executives, managers and technical professionals achieve not only their current PSM goals, but also to make the transition to a broader operational integrity strategy. The book focuses on the energy and process industries- from refineries, to pipelines, chemical plants, transportation, alternative energy and offshore facilities. The techniques described in the book can also be applied to a wide range of non-process industries.
The book is both thorough and practical. It discusses theoretical principles in a wide variety of areas such as management of change, risk analysis and incident investigation, and then goes on to show how these principles work in practice, either in the design office or in an opperating facility.
- Learn how to develop process safety, operational integrity and operational excellence programs
- Go beyond traditional hazards analysis and risk management programs to explore a company's entire range of procedures, processes and mangement issues
- Understand how to develop a culture of process safety and operational excellence that goes beyond simple rule complience
Managers and technical staff in the oil and gas industry: refineries, pipelines, transportation, offshore facilities. Managers and engineers in the process industries.
Chapter 1 - Operational Integrity Management
Introduction Operational Integrity / ExcellenceProcess Safety Management Major Events Examples Example 1 - Facility Design Example 2 - Process Flow Example 3 - Heat Exchanger Example 4 - Risk Management Workflow External Standard GuidanceRisk Analysis Plan and Implement Audit / Deltas Success / Continuous Improvement Fundamentals of PSM Safe Limits Set Point ValuesOperating, Safe and Emergency LimitsNon-Prescriptive Performance / Risk BasedProcess - Not Occupational - SafetyMeasurement Strategies Involvement and ThoroughnessHolisticDefinition of Process Safety ManagementTrends Health, Safety & Environmental Programs Environmental / SustainabilityHealth Safety Quality Management Statistical Process ControlISO 9000 / 14001Six SigmaRisk Hazards Consequence / LikelihoodBow-Tie Method Presence of PersonsSingle Contingency EventsEconomies of Scale Subjective Nature of Risk Degree of Control Familiarity with the Hazard Direct Benefit Personal Impact Natural vs. Man-Made Risks Recency of Events Perception of the Consequence TermComprehension TimeQuantification of RiskFrequencyPredicted FrequencyProbabilityLikelihood and Failure RateError / Statistical Significance Confidence Failure / FaultIndependence and RandomnessAcceptable RiskAs Low as Reasonably Practical - ALARP De Minimis Risk Citations / "Case Law"RAGAGEP Indexing MethodsRisk Matrices Consequence Matrix Worker SafetyPublic Safety and Health Environmental Impact Economic Loss Frequency Matrix Risk Matrix Chapter 2 - Culture and Employee Involvement Introduction Elements of Culture On-Going and Consistent Words and Actions External Evaluation Learning from Incidents Attention to Basics Historical Development1. Safety as a Value2. Codes and Standards3. Workers Compensation4. Occupational Safety5. Systems Analysis6. Regulations 7. Management Systems 8. Behavior-Based Safety 9. Safety Culture Warning Flags over Your OrganizationFlag One - Unrealistic Stretch Goals Production Creep Production Records Initiative Overload Flag Two - Excessive Cost Reduction Reduction of "Non-Essentials" Reductions in Work Force The "Big Crew Change"Flattened Organizations Aging Infrastructure Out-SourcingNot Enough Time for Detailed WorkProject Cutbacks Flag Three - Belief That "It Cannot Happen Here"Lack of Direct Experience Good Occupational Safety Performance Lack of Imaginative Thinking Failure to Learn from Near-Misses Failure to Draw on Experience ElsewhereFlag Four - Excessive Belief in Rule Compliance Flag Five - Ineffective Information FlowCritical Safety Information Is Buried, Lost or DilutedTeam Player CultureFear of LitigationMergers, Acquisitions and DivestituresFlag Six - Ineffective Audit Process Softened News to Senior Managers Failure to Identify Root Causes Inadequate Follow Up Developing a Strong Culture Mission StatementGuiding Tenets Detailed Program Workforce and Stakeholder Involvement Workforce Involvement Safety Committees Involvement in OIM Elements Difficulties with Workforce Involvement Inefficiencies Unwillingness to Accept Change Labor / Management Relations Stakeholder OutreachContractorsTypes of ContractorSelection of a Contract Company Contractor TrainingSafety MeetingsPost-Contract Evaluation Chapter 3 - Hazards Identification IntroductionHazards Management ProcessStep 1. Identify the Hazards Creative / Imaginative TechniquesExperience-Based Logical / Rational Step 2. Risk RankStep 3. Eliminate or Substitute the HazardStep 4. Remove the PeopleStep 5. Reduce the ConsequenceStep 6. Reduce the Likelihood Step 7. Install SafeguardsOrganization of a Hazards Analysis Charge / Scope Letter Abandoned Equipment Preparations Logistics Meeting Protocol Location of the Meeting Projection of Notes Documentation Requirements Security of the Information Time Required Kick-Off and Close-Out Meetings HAZID / Major Hazards ScreeningThe TeamLeader / Facilitator Process Knowledge Stimulate Thinking Creative Thinking Casual Remarks "If We Had Unlimited Money" Generalizations Team Management Knowledge of Actual Incidents Lawyer-Like Behavior Persona Personal Preparation Engineering StandardsThe Scribe Operations / Maintenance Expert Process and Instrument Experts SpecialistsUse of Sophisticated LanguageThe One-Minute Engineering DepartmentResults of the AnalysisFindings Recommendations Action Items Risk Register Finding Number and Date Hazard Source Consequence(s) / Likelihood / Risk Follow-Up The Hazards Analysis Report Completeness of the NotesCross-ReferenceAnonymityFindings TerminologyCompleteness"Non-Findings"AppearancePicturesReport DistributionCommunication with the Public Table of Contents 1. Disclaimer2. Executive Summary3. Objectives of the Analysis 4. Summary of Findings5. Method Used6. Risk Ranking7. The Team8. Regulations 9. Attachments 10. Meeting Notes Development of the ReportStep 1. Notes Clean-Up Step 2. Team Review Step 3. Draft Report Step 4. Client ReviewStep 5. Final Report Step 6. Risk RegisterLegal IssuesNeed to Act on Findings Informal NotesInternal Communication Special Types of Hazards AnalysisTemporary and Transient Operations Non-Process Applications Decommissioning / DemolitionRevalidation Hazards AnalysesBenefits and Limitations of Hazard AnalysesStrengths Providing Time to Think Challenging Conventional Thinking Cross-Discipline Communication Education Development of Technical Information Economic Payoff Limitations and Concerns Imprecision in Defining TermsMultiple ContingenciesComplexities and Subtle Interactions Dynamic ConditionsCommon Cause EventsKnowledge of Safe Operating LimitsLack of QuantificationTeam QualityPersonal ExperienceBoredom Confusion with Design Reviews False Confidence Equipment OrientationInterfacesHuman Error The Hazard and Operability Method (HAZOP)Step 1. Node Selection and Purpose Selection of Nodes Pressure Breaks Step 2. Process Guideword / Safe Limits Step 3. Identification of Hazards and their Causes Step 4. "Announcement" of the Hazard Step 5. Consequences Step 6. Identification of SafeguardsStep 7. Predicted Frequency of the HazardStep 8. Risk Rank Step 9. Findings Step 10. Next Process Guideword / Node Checklists Checklist Categories Guidewords Structure of a ChecklistThe What-If MethodNode / Functional Area Review Equipment and Function Review Utility Systems Batch Processes Operating Procedures Layout Reviews What-If / Checklist MethodFailure Modes & Effects AnalysisTRIZIndexing MethodsInterface Hazards AnalysisHazards Analysis on ProjectsCommon HazardsProcess HazardsHigh Flow Low / No Flow Reverse Flow Misdirected Flow High Pressure High TemperatureBlocked-In Pump Polymerization External Fire Low Pressure Low Temperature High Level Wrong Composition Corrosion Chemical EmbrittlementStatic ElectricityHazards of UtilitiesCommon Cause Failure Process ContaminationElectrical Power Failure Nitrogen Reverse Flow to a Utility Header Use of Hoses Survivability of UtilitiesHazards of WaterWater in Hydrocarbon TanksWater in Very Hot Liquid Static ElectricityWater and FirefightingHazards of SteamSteaming Vessels during TurnaroundReboiler LeakWet Steam Hazards of Ice Line Freezing Hydrates Hazards of Compressed Gas Gas Cylinders Pigging Incident Hazards of Air Flammable MixtureBlowing a Line Clear Hazards of External Events Flooding Lightning Earthquakes Hazards of Equipment and Instruments Furnace Firing Fired Heater Burnout Multiple Uses of EquipmentDistributed Control SystemsHazards of Piping, Valves and Hoses Piping Pipe Class TransitionHydraulic Hammer Pig Launchers and Receivers Pressure in Relief Headers Overload of Overhead Vacuum LinesUnderground Piping Vents and Bleeders Hoses Hoses and Truck Pull-Away Hose Run Over Hose Failure Backflow PreventorValvesBlocked-In Pressure Relief ValveVents and BleedersFail-Safe Control ValvesCritical Control Valves in ManualShared Relief Valve Block Valves below Relief Valves SDV Bypass Human ErrorErrors of Intent Errors of Action Mistakes Slips Fixation Error in an Emergency Chapter 4 - Consequence and Likelihood AnalysisIntroductionConsequence AnalysisSafetyHealthEnvironmentalEconomicEffect of a Release FiresFlammable Range Ignition Temperature / Energy Spontaneous Combustion Ignition SourcesVacuum Trucks Radiant Heat Static Electricity Lightning Pyrophorics / Iron Sulfide Flammability Hazard Ranking Passive Fire Protection / Fireproofing ExplosionsPhysical ExplosionsVapor Cloud Explosions Deflagrations and DetonationsBlast EffectsBLEVEs Dust Explosions Toxic Gas ReleasesGas Release Modeling Effect of Toxic Gases Probit Equations Short-Term Exposure LimitsEmergency Response Planning Guidelines (ERPGs)Immediately Dangerous to Life and Health Permissible Exposure Limits (PEL) Threshold Limit Values (TLV) Short Term Exposure Limit (STEL) Levels of Concern (EPA) Acutely Toxic Concentration / Levels (New Jersey/Delaware) Substance Hazards IndexHazardous ChemicalsCarbon Monoxide (CO) Nitrogen (N2) Sulfur Dioxide (SO2)Hydrogen Sulfide (H2S) Chlorine (Cl2)Frequency Analysis The Pareto Principle Importance Ranking Fault Tree Analysis GatesOR GateAND GateVOTING GateEventsTop Event Intermediate Events Base Events House Event Top-Down Development of a Fault Tree1. Define the Top Event 2. Build the Tree 3. Identify the Cut Sets 4. Eliminate Repeat Sets 5. Eliminate Repeat Events in a Set 6. Eliminate Redundant Events 7. Quantify the Risk Mathematics of an OR Gate Mathematics of an AND GateMathematics of a Voting Gate Cut Set Quantification 8. Risk RankEvent ContributionImportant FewUnimportant ManyPower of the AND GateImportance Equalization Cost-Benefit AnalysisImportance Ranking Using Cut SetsBirnbaum Factor MethodFussel-Vesely MethodPerturbation Method Common Cause EventsUtility Failure Instruments on Manual Instrument PluggageVibrationExternal Events Maintenance Availability Human Error / Untrained Personnel Generic Fault Trees Generic Safety Fault TreeGeneric Reliability Fault Tree Discussion of the Fault Tree MethodQualitative Fault Tree Analysis Event Tree AnalysisQuantification of an Event Tree Scope of EventCombining Event Trees and Fault Trees Short Sequence of Events Many Events Partial Success Discrete Event Analysis Non-Linearities and Complexities Conveying Statistical UncertaintyMonte Carlo Simulation Random Number Generators Seed Numbers Speeding the Simulation Markov ModelsImportance RankingTop-Down / Bottom-Up ApproachTop-Down Bottom-UpQualitative InsightsLimitations to QuantificationMathematical Understanding Value-Laden Assumptions Lack of Exhaustivity Human Behavior Data Quality SafeguardsSafeguard Level 1: Normal Operations Safeguard Level 2: Procedural Safeguards Safeguard Level 3: Safety Instrumented Systems Safeguard Level 4: Mechanical Safeguards Safeguard Level 5: Passive Safeguards Safeguard Level 6: Emergency ResponseLayer of Protection Analysis The LOPA ProcessSingle Scenarios IPLs Specific Independent Dependable Auditable Human Response Implementing LOPA Team Makeup Timing Tools Procedures and Inspections Risk Criteria PFDs Failure Rate Data Chapter 5 - Technical Information and Industry Standards IntroductionTechnical Information: Table of ContentsProcess DescriptionMaterial Safety Data Sheets (MSDS)The Safety DiamondEngineering InformationBlock Flow Diagrams Process Flow Diagrams Piping & Instrument Diagrams Materials of Construction Table Industry StandardsTypes of Standard Regulations Codes and Industry Standards Development of a StandardNational Fire Protection Association (NFPA)American Petroleum Institute American Chemistry Council / Responsible Care(TM) Center for Chemical Process Safety American Society of Mechanical Engineers American National Standards Institute (ANSI)International Organization for Standardization (ISO)Company Standards Industry Information Open Literature RAGAGEP Chapter 6 - Asset Integrity IntroductionSiting and LayoutBlocks and RoadsEquipment Layout and SpacingPumpsUtilitiesPiping and ValvesDrainageBuildingsArea ClassificationElectrical Equipment Ground Fault Circuit InterruptersFireproofing Pressure Vessels Maximum Allowable Working PressureEffect of Temperature Reflux Vessels Small Pipe Connections and Isolation Pressure Tests Tightness Tests Strength Tests Test Media Testing Procedures Storage Tanks Operation Vapor Recovery Systems Pumps Protective Instrumentation Pump Casing Seals and Packing Minimum Flow Bypass Pump Isolation Compressors Liquid Knockout on the Compressor Suction Relief ValvesCompressor IsolationShutdown and Alarm SystemsHeat ExchangersShell and Tube Heat Exchangers Air-Cooled Exchangers Cooling Towers Air Preheaters Boilers Piping and ValvesMaterials InsulationGaskets Threaded Piping Thermal Expansion Identification and Labeling of PipesValvesTrapped Liquids Plugs Valve Seat Material Self-Closing Valves Check Valves Emergency Isolation ValvesTesting and Inspection Pressure Relief DevicesPressure Safety Relief ValvesShared Relief Valves Venting from Relief Valves Block Valves below Relief Valves Testing and InspectionThermal Relief ValvesRupture Disks Hatches / DoorsFlame ArrestorsThermal Flame ArrestorsWater Seal-Type Flame Arrestors Velocity-Type Flame Arrestors Detonation Arrestors Flares Instrumentation and Control Systems Alarms Alarm ManagementInterlocks and Trips Safety Instrumented SystemsDesign Issues Fire Protection Quantitative Analysis Testing and Inspection Internal Combustion Engines Starter Systems Intake, Exhaust and Fuel Systems BuildingsProcess BuildingsTemporary Buildings Control Buildings Control Building Laboratories WarehousesInside StorageInspection ProgramsInspection FrequencyInspection RecordsQuality ControlRisk-Based InspectionAnalyze Risk Determine Costs Allocate Resources Chapter 7 - Reliability, Availability and MaintainabilityIntroductionBenefits of a RAM ProgramReliability and SafetyDefinitionsReliability Availability Effectiveness Maintainability Failure ModesEquipment Description Primary, Secondary and Command FailuresCatastrophic, Degraded and Incipient FailuresReal Failures / Necessary Replacements Failure RatesConstant / Exponential Distribution Lognormal Distribution Bathtub Curve Early Failures Constant Failure Rate Wear-Out Failures Reliability Block Diagrams Active / Standby Redundancy Quantification of Block Diagrams Failure Rate Data Conditional Probability / Bayes' TheoremEvaluation of Tests Sequential Observations Combining Data SourcesChapter 8 - Operations, Maintenance and Safety IntroductionSafe Work Practices Housekeeping Minimizing Contact with Air Tank Filling and Emptying Catching Samples Flame Propagation through Drains Spills and Overflows Hot Taps Unplugging a Line NORM (Naturally Occurring Radioactive Material)Machinery SafetyMachine Guards Lifting Stairways and LaddersStairways and Railings Fixed LaddersBehavior Based Safety Observed Hazard Card Five by Five Policy Lone Worker Policy Energy Control ProceduresRemoval of the Hazard Positive Isolation Temporary PlugsIsolation TechniquesLevel 1 - Closed Valve Level 2 - Closed Valve with Open BleederLevel 3 - Double Block and BleedLevel 4 - Block and Bleed with Line BreakLevel 5 - Block, Bleed and Spectacle BlindLevel 6 - Double Block and Bleed with Blind Level 7 - Double Block and Bleed with Line Break Electrical Isolation First Break Policy Lockout / Tagout Group Lockout Car Seals Padlocks Tags Administrative Controls Work Permits General Work Permits Issuance of Permits Changes in Conditions Multiple Work PermitsHot Work PermitsConfined Space EntryPreparation Drain LiquidsPurge and Ventilate Steam Air Test The Entry Permit PersonnelEntrant Supervisor Manway Attendant Gas Tester Maintenance Repair Condition-Based MaintenanceScheduled MaintenanceReliability Centered Maintenance Tie-Ins Maintenance Task Organization Step 1 - Plan the Work Step 2 - Conduct a Job Hazards AnalysisStep 3 - Issue a Work Permit Step 4 - Shutdown and Isolate EquipmentStep 5 - Perform the Work Step 6 - Close Out the Work SignsProhibitionMandatory ActionWarningSafe ConditionFire Safety Color Coding For Exposed Piping Personal Protective Equipment (PPE) Head ProtectionHand ProtectionClothing Fire Resistant Clothing Impervious Clothing Foot ProtectionEye Protection Respiratory Protection Air-Purifying RespiratorsSupplied Air Respirators Chemical Canister RebreathersPortable Gas Detectors Office SafetyOutside OperationsOutside Storage Coal and Coke StorageDrum StorageDrainageFire Protection and Prevention CylindersLoading RacksDrum StorageEmergency Showers and EyewashesComponents of an Emergency ShowerFreeze Protection Heat Protection Visibility and Accessibility Alarms InspectionCommissioning and Start-Up Construction Complete Commissioning Operational Readiness ReviewTypes of Review Review Not Required Small Projects / Engineering Changes Medium Size Projects Large Projects Restart ReviewsOrganizational Responsibility Time Required Team Structure Using the Elements of OIM Knowledge Management Operating Procedures Asset Integrity / Reliability Training / Performance Chapter 9 - Operating Procedures IntroductionDefinition of Operating Procedures Operations Written Instructions Design or Operating Intent Definition of Maintenance Procedures TerminologyEngineering the SolutionQuick Assessment of Operating ProceduresThe UsersExperienced Technicians Less Experienced Technicians Engineering / Management DCS / SCADA ProgrammersAuditors, Regulators and InspectorsTranslatorsElements of OIM Workforce Involvement Knowledge Management Hazard Identification and Risk Management Management of Change Operational Readiness Emergency ManagementInformation ManualTypes of Operating ProcedureSteady-State Operating ProceduresTypes of Steady-State Procedure Shift ChangeStart-Up ProceduresShutdown ProceduresLevels of ShutdownStand-ByUnit ShutdownProcess Shutdown Emergency ShutdownTurnaround Trouble Shooting Procedures Elements of Troubleshooting Procedures Guidance - Not Instructions Structure of Troubleshooting ProceduresTemporary Operating ProceduresBatch ProceduresStandard Operating ProceduresMaintenance ProceduresJob Safe PracticesThe Operating ManualSoftware AnalogyModular DesignConnecting the ModulesIf / Then / Else Instructions Modular Operating Manual Data Base StructureTop-Down DevelopmentPrototypingLimitations of ModularityDesign of an Operating ManualAdding and Removing ModulesNumbering the Modules Module DesignThe Title Block Procedure Name Module NumberPurpose of the ProcedureRevision NumberDate of Revision Covered Persons Company / Facility Safe Upper and Lower Limits Special Safety Items Equipment InformationTraining The Operating Task Instructions Step Number Column Person Action Discussion / Illustration The Authorization Block Written By Approval - Superintendent Approval - Manager Authorization Sheet Overall Module Links to Other Procedures and Manuals Links to Technical Information Training Two-Page Modules Content DevelopmentLevel of DetailLevel 1 - Overview / ChecklistsLevel 2 - Equipment DescriptionLevel 3 - Valve DetailSources of InformationExisting ProceduresTechnician Interviews Engineering InformationVendor Manuals Process Hazards AnalysesThe Procedures-Writing TeamWriting and PublishingProject Organization1. Define the Scope of WorkPhysical Area / Equipment Covered UsersTypes of ProcedureJob Task AnalysisDesign of the Manual Regulations / Standards Writer's Guide2. Create the TeamSteering CommitteeProject ManagerProject Lead Technicians Technology ExpertInterviewer-Writers Publisher / Webmaster 3. Develop a Detailed PlanSchedule and Progress Metric BudgetPrepare the SOPs4. Collect InformationOperator Interviews Existing Procedures / Vendor Manuals Logbooks5. Write the ProceduresDraft ReleasesPlan to Throw One Away - You Will Anyway 6. Review and Sign 7. Publish Potential DifficultiesPoorly Defined Goals Too Many People Extended Review Cycle Lack of Signatures Maintaining the ProceduresProcedures Modification ProcessOrganizationWriting GuidelinesVigorous WritingMinimalist WritingShort, Pithy Instructions Avoid Repetition of InstructionsOmit Needless WordsOmit AdverbsShort and Old WordsAvoid Wordy Phrases and Padded SyllablesWriting StyleImperative TenseActive VoiceReading Grade Level List Instructions Singly Implied InstructionsBulleted Lists Conditional Instructions Positive / Negative Instructions VocabularyIdentification of EquipmentConsistencyShould / Would / CouldThe Word "You"The Word "This" TautologiesArabic NumeralsAdverbs and AdjectivesArticlesHumorSpellingLatinate AbbreviationsApostrophes Ambiguous Words Cobblestone WritingRepetition of Messages Danger, Warning, Caution, Note Proofreader Marks Illustrations Photographs P&IDs Iconic Flow Diagrams Maps / Plot Plans PublishingColorWhite SpaceFontsParagraph FormattingEmphasis TechniquesHeadingPage NumberingSingle-Sided versus Double-Sided Printing Indexing GlossaryThe BinderMultiple LanguagesChapter 10 - Training and Competence IntroductionElements of a Training ProgramOrientationInitial / Basic TrainingSite TrainingAbnormal Situation ManagementRefresher TrainingProcedures and Training Management of a Training ProgramTraining MatrixBudget Allocation Measuring ProgressEconomics of TrainingProcess Simulators and Emulators Testing and Certification Chapter 11 - Emergency Management and SecurityIntroduction Human Response Human Error RateFixation Heroism and Buddy LoyaltyTrouble ShootingLevels of EmergencyCause of EmergencyEmergency OperationsLocal Emergency ResponseGeneral Emergency ResponseRecovery Operations Investigation and Follow UpEmergency Planning Organization and PersonnelEmergency Response ManualEmergency Procedures Emergency Response Training Communications Fire and Gas Detection Fire Detection Fire Eyes / Flame DetectorsSmoke Detectors Heat Detectors Fusible Links Low Oxygen Detectors Combustible Gas DetectorsManual Call PointsToxic Gas ReleasesFire FightingSingle Fire ConceptDeluge SystemsFire Zones Fire Water Water Capacity and RatesSources of Fire WaterTesting Fire Water Pumps and DriversJockey Pumps Main Fire Pumps Fixed Water Spray SystemsAutomatic Sprinkler Systems Fire Water Monitors Fire Water Distribution SystemMaterials of Construction Layout Valves HydrantsOther Fire Fighting MediaHalon Steam Foam SystemsCarbon Dioxide SystemsHeavy Equipment Portable Fire Extinguishers Location Types Water Extinguishers Carbon Dioxide Extinguishers Dry Chemical Extinguishers Personnel Protective Equipment Bunker Gear / Turnout Clothing Proximity Suits Breathing ApparatusSecurityMembers of the PublicVandalismTheft ActivistsSabotageTerrorismVisible SecurityPopulation DensityHigh Profile Chemicals Security Vulnerability AnalysesRings of ProtectionImproving SecurityCulture Inherent SafetyAccess SecurityPersonnel ScreeningEquipment ModificationsResponse to a Threatening CallChapter 12 - Incident Investigation and Root Cause Analysis Introduction Management LevelLine SupervisionFacility ManagementExecutive ManagementIndustry Regulations and StandardsIncident Investigation and Analysis Philosophy Trust and CandorListen to the FactsCause and EffectTechnical ExpertiseRoot Cause AnalysisProject ManagementBlame and Fault-FindingManagement Trust Early Reporting of Bad News Management Pressure No Good Deed Goes UnpunishedCommunicationsDefinitions Incident Accident Near Miss / Hit Potential Incident High Potential Incident Six-Step Investigation and Analysis ProcessStep 1 - Initial Investigation Step 2 - Evaluation and Team FormationStep 3 - Information GatheringStep 4 - Timeline DevelopmentStep 5 - Root Cause AnalysisStep 6 - Report and Recommendations1. Initial InvestigationThe "Go Team" Drug and Alcohol TestingIncident Report Form First Management Report 2. Evaluation and Team FormationEvaluation Team Formation Outside InvestigatorsCorporate Support Team Members Charter / Terms of ReferenceTeam Member Qualifications3. Information GatheringInterviews Interview Guidelines Regulatory / Legal InterviewsWitness Interviews Interviewer Attributes Documentation Engineering InformationOperating Information Vendor Data Field Information Damage Assessment Photographs and DVDs Closed Circuit TelevisionInstrument Records Testing / Lab Analysis 4. Timeline Development Timeline Steps Timeline Construction Conditions Multiple TimelinesTimeline Table Background Information 5. Root Cause Analysis Levels of Root Cause Types of Root Cause AnalysisArgument by Analogy: Story TellingSafeguardsCategorizationSystem AnalysisWhy Trees Fault Tree Analysis Linkage of Fault Trees to the TimelineCommon Cause Events6. Report and RecommendationsLevels of RecommendationReport StructureIssuing the ReportInformation Security and Chain of CustodyRecord RetentionRemoving EvidenceFile Systems Incident / Risk RegisterFeedbackIncident Data BasesNational Response Center (NRC)Accidental Release Information Program (ARIP) Database CFOI (Census of Fatal Occupational Injuries) Major Accident Reporting System (MARS) Marsh & McLennan Reviews Annual Loss Prevention SymposiaProcess Safety Beacon Government AgenciesChapter 13 - Management of Change Introduction Benefits of Management of ChangeIncreased Production, Productivity and Quality Maintenance Expense and Safety Environmental Performance Personal ReputationDefinition of MOCDeviation beyond Limits Impact on other Process Safety Elements Critical Changes In-Kind / Not-In-Kind Change Same Specification Same Service and Materials of ConstructionSame Storage and Handling Process Procedural Replacement Process Chemistry Instrumentation and Control SystemsTypes of Change Initiated Equipment ChangeLarge and Small Changes Turnarounds Field Change Non-Initiated Equipment ChangeOvert Change Covert Change Temporary Changes Emergency Changes Organizational Change Reorganization Management by ContractorsInformal Aspects of MOCThe Management of Change Process Section A - Initiator Request Initiator Sponsor Request Process Management of Change Form - Section A Section B - First Review In-Kind / Not-In-Kind Change Selecting the First Reviewers Management of Change Form - Section BSection C - Detailed Evaluation Review Process MOC Coordinator Review Team Builders Project Team Software Reviewers Qualifications Recommendations Management of Change Form - Section CSection D - Formal Approval Management of Change Committee Process Hazards Analysis Variance ProceduresSection E - New Limits / Process Safety UpdateSection F - Notification Section G - Implementation Section H - Follow-UpChapter 14 - Audits and AssessmentsIntroduction Formal Audits Reasons for Audits Accident Follow-UpRegulatory / Standards Compliance Voluntary Check Insurance and Business Security Audit Standards Regulations Industry Standards Internal Standards Audit Personnel Outside AuditorsInternal AuditorsTeam CompositionAuditor AttributesInterview SkillsTechnical KnowledgeWriting Skills Demeanor The Host CompanyFirst ImpressionsEmployees Planning the Audit GoalsDetermine the Audit StandardScope Budget ScheduleOne-Point ContactPre-Audit ActivitiesAudit Forms Conducting the Audit Auditor Preparation Kick Off Meeting Plant Tour Information Collection Interviews On-Site InspectionClose-Out MeetingReport Letter of Certification Audit Verification Findings Follow Up Unannounced Audits Lagging and Leading Indicators Lagging Indicators Leading Indicators Limitations <
- Edition: 1
- Published: April 9, 2010
- Imprint: William Andrew
- Language: English
IS