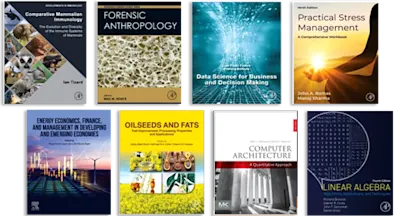
Pressure Vessel Design Manual
- 4th Edition - December 26, 2012
- Imprint: Butterworth-Heinemann
- Authors: Dennis R. Moss, Michael M. Basic
- Language: English
- Paperback ISBN:9 7 8 - 0 - 1 2 - 8 1 0 0 2 2 - 6
- Hardback ISBN:9 7 8 - 0 - 1 2 - 3 8 7 0 0 0 - 1
- eBook ISBN:9 7 8 - 0 - 1 2 - 3 8 7 0 0 1 - 8
Pressure vessels are closed containers designed to hold gases or liquids at a pressure substantially different from the ambient pressure. They have a variety of applications in in… Read more
Purchase options
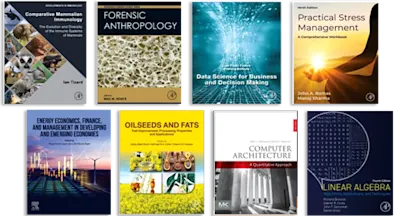
Pressure vessels are closed containers designed to hold gases or liquids at a pressure substantially different from the ambient pressure. They have a variety of applications in industry, including in oil refineries, nuclear reactors, vehicle airbrake reservoirs, and more. The pressure differential with such vessels is dangerous, and due to the risk of accident and fatality around their use, the design, manufacture, operation and inspection of pressure vessels is regulated by engineering authorities and guided by legal codes and standards. Pressure Vessel Design Manual is a solutions-focused guide to the many problems and technical challenges involved in the design of pressure vessels to match stringent standards and codes. It brings together otherwise scattered information and explanations into one easy-to-use resource to minimize research and take readers from problem to solution in the most direct manner possible.
- Covers almost all problems that a working pressure vessel designer can expect to face, with 50+ step-by-step design procedures including a wealth of equations, explanations and data
- Internationally recognized, widely referenced and trusted, with 20+ years of use in over 30 countries making it an accepted industry standard guide
- Now revised with up-to-date ASME, ASCE and API regulatory code information, and dual unit coverage for increased ease of international use
Entry and mid-level Mechanical Engineers who specify, design, operate, install, inspect or manufacture pressure vessels and related equipment in a process, chemical, civil, petroleum or nuclear engineering setting. Job titles include: Pressure Vessel Design Engineers, Reliability Engineers, Fixed or Principal Equipment Engineers, Maintenance Engineers, Piping Engineers, Plant Engineers, and Commissioning Engineers
Preface to the 4th Edition
1. General Topics
Design Philosophy
Stress Analysis
Stress/Failure Theories
Failures in Pressure Vessels
Loadings
Stress
Thermal Stresses
Discontinuity Stresses
Fatigue Analysis for Cyclic Service
Creep
Cryogenic Applications
Service Considerations
Miscellaneous Design Considerations
Items to be Included in a User’s Design Specification (UDS) for ASME VIII-2 Vessels
References
2. General Design
Procedure 2-1: General Vessel Formulas [1,2]
Procedure 2-2: External Pressure Design
Procedure 2-3: Properties of Stiffening Rings
Procedure 2-4: Code Case 2286 [1,8,21]
Procedure 2-5: Design of Cones
Procedure 2-6: Design of Toriconical Transitions [1,3]
Procedure 2-7: Stresses in Heads Due to Internal Pressure [2,3]
Procedure 2-8: Design of Intermediate Heads [1,3]
Procedure 2-9: Design of Flat Heads [1,2,4,5,6]
Procedure 2-10: Design of Large Openings in Flat Heads [1]
Procedure 2-11: Calculate MAP, MAWP, and Test Pressures
Procedure 2-12: Nozzle Reinforcement
Procedure 2-13 Find or Revise the Center of Gravity of a Vessel
Procedure 2-14: Minimum Design Metal Temperature (MDMT)
Procedure 2-15: Buckling of Thin Wall Cylindrical Shells [21]
Procedure 2-16: Optimum Vessel Proportions [16-20][16-20]
Procedure 2-17: Estimating Weights of Vessels and Vessel Components
Procedure 2-18: Design of Jacketed Vessels
Procedure 2-19: Forming Strains/Fiber Elongation
References
3. Flange Design
Introduction
Procedure 3-1: Design of Flanges [1–4]
Procedure 3-2: Design of Spherically Dished Covers
Procedure 3-3: Design of Blind Flanges with Openings [1,4]
Procedure 3-4: Bolt Torque Required for Sealing Flanges [5–7]
Procedure 3-5: Design of Studding Outlets
Procedure 3-6: Reinforcement for Studding Outlets
Procedure 3-7: Studding Flanges
Procedure 3-8: Design of Elliptical, Internal Manways
Procedure 3-9: Through Nozzles
References
4. Design of Vessel Supports
Introduction: Support Structures
Procedure 4-1: Wind Design Per ASCE [1]
Procedure 4-2: Seismic Design – General
Procedure 4-3: Seismic Design for Vessels [2]
Procedure 4-4: Seismic Design – Vessel on Unbraced Legs [4–7]
Procedure 4-5: Seismic Design – Vessel on Braced Legs
Procedure 4-6: Seismic Design – Vessel on Rings [4,5,8]
Procedure 4-7: Seismic Design – Vessel on Lugs [5,8–13]
Procedure 4-8: Seismic Design – Vessel on Skirt [1,2,3]
Procedure 4-9: Seismic Design – Vessel on Conical Skirt
Procedure 4-10: Design of Horizontal Vessel on Saddles [1,3,14,15]
Procedure 4-11: Design of Saddle Supports for Large Vessels [4, 15–17,20]
Procedure 4-12: Design of Base Plates for Legs [20,21]
Procedure 4-13: Design of Lug Supports
Procedure 4-14: Design of Base Details for Vertical Vessels – Shifted Neutral Axis Method [4,9,13,17,18]
Procedure 4-15: Design of Base Details for Vertical Vessels – Centered Neutral Axis Method
Procedure 4-16: Design of Anchor Bolts for Vertical Vessels
Procedure 4-17: Properties of Concrete
References
5. Vessel Internals
Procedure 5-1: Design of Internal Support Beds
Procedure 5-2: Design of Lattice Beams
Procedure 5-3: Shell Stresses due to Loadings at Support Beam Locations
Procedure 5-4: Design of Support Blocks
Procedure 5-5: Hub Rings used for Bed Supports
Procedure 5-6: Design of Pipe Coils for Heat Transfer [1-9][1-9]
Procedure 5-7: Agitators/Mixers for Vessels and Tanks
Procedure 5-8: Design of Internal Pipe Distributors
Procedure 5-9: Design of Trays
Procedure 5-10: Flow Over Weirs
Procedure 5-11: Design of Demisters
Procedure 5-12: Design of Baffles [10]
Procedure 5-13: Design of Impingement Plates
References
6. Special Designs
Procedure 6-1: Design of Large-Diameter Nozzle Openings [1]
Large Openings—Membrane and Bending Analysis
Procedure 6-2: Tower Deflection [3]
Procedure 6-3: Design of Ring Girders [4–8]
Procedure 6-4: Design of Vessels with Refractory Linings [9–12]
Procedure 6-5: Vibration of Tall Towers and Stacks [13–23]
Procedure 6-6: Underground Tanks & Vessels
Procedure 6-7: Local Thin Area (LTA) [2]
References
7. Local Loads
Procedure 7-1: Stresses in Circular Rings [1–6]
Procedure 7-2: Design of Partial Ring Stiffeners [7]
Procedure 7-3: Attachment Parameters
Procedure 7-4: Stresses in Cylindrical Shells from External Local Loads [7,9,10,11]
Procedure 7-5: Stresses in Spherical Shells from External Local Loads [11–13]
References
8. High Pressure Vessels
1.0 General
2.0 Shell Design
3.0 Design of Closures
4.0 Nozzles
5.0. References
9. Related Equipment
Procedure 9-1: Design of Davits [1,2]
Procedure 9-2: Design of Circular Platforms
Procedure 9-3: Design of Square and Rectangular Platforms
Procedure 9-4: Design of Pipe Supports
Procedure 9-5: Shear Loads in Bolted Connections
Procedure 9-6: Design of Bins and Elevated Tanks [3–9]
Procedure 9-7: Field-Fabricated Spheres
References
10. Transportation and Erection of Pressure Vessels
Procedure 10-1: Transportation of Pressure Vessels
Procedure 10-2: Erection of Pressure Vessels
Procedure 10-3: Lifting Attachments and Terminology
Procedure 10-4: Lifting Loads and Forces
Procedure 10-5: Design of Tail Beams, Lugs, and Base Ring Details
Procedure 10-6: Design of Top Head and Cone Lifting Lugs
Procedure 10-7: Design of Flange Lugs
Procedure 10-8: Design of Trunnions
Procedure 10-9: Local Loads in Shell Due to Erection Forces
Procedure 10-10: Miscellaneous
11. Materials
11.1 Types of Materials
11.2 Properties of Materials
11.3 Bolting
11.4 Testing & Examination
11.5 Heat Treatment
Appendices
Appendix A Guide to ASME Section VIII, Division 1
Appendix B Design Data Sheet for Vessels
Appendix C Joint Efficiencies (ASME Code) [3]
Appendix D Properties of Heads
Appendix E Volumes and Surface Areas of Vessel Sections
Appendix F Vessel Nomenclature and Definitions
Appendix G Useful Formulas for Vessels [1,2]
Appendix H Metric Guidelines and Conversions
Appendix I Allowable Compressive Stress for Columns, FA
Appendix J Design of Flat Plates
Appendix K Time Required to Drain Vessels
Appendix L Vessel Surge Capacities and Hold-Up Times
Appendix M Minor Defect Evaluation Procedure
Appendix N Tolerances
Appendix O Guideline for Application of Pressure Relief Values (PRVs)
Index
- Edition: 4
- Published: December 26, 2012
- Imprint: Butterworth-Heinemann
- Language: English
DM
Dennis R. Moss
MB