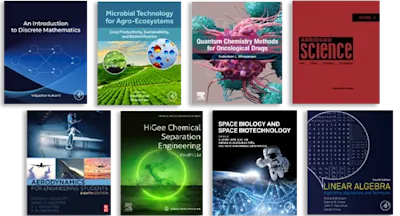
Practical Guide to Rotational Moulding
- 3rd Edition - October 14, 2021
- Authors: Roy J Crawford, Mark P Kearns
- Language: English
- Paperback ISBN:9 7 8 - 0 - 1 2 - 8 2 2 4 0 6 - 9
- eBook ISBN:9 7 8 - 0 - 3 2 3 - 8 5 8 1 6 - 8
Practical Guide to Rotational Moulding, Third Edition, takes a step-by-step approach to rotomoulding, covering applications, moulds, machinery, materials, and design. This thir… Read more
Purchase options
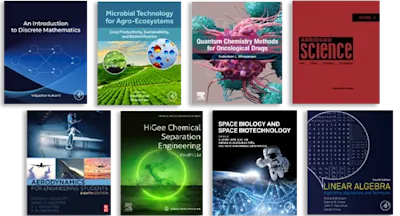
Practical Guide to Rotational Moulding, Third Edition, takes a step-by-step approach to rotomoulding, covering applications, moulds, machinery, materials, and design. This third edition has been thoroughly revised to include the latest advances, including novel materials and moulds, new products, and automation.
The book begins with a chapter that introduces the rotational moulding process, analyses advantages and disadvantages, and explores common applications for rotomoulded products. The subsequent chapters provide detailed, methodical coverage of moulds, machinery, materials, and design for functionality, supported by clear illustrations and diagrams. Finally, challenges and future developments are discussed.
This hands-on technical guide helps engineers, designers and practitioners to understand all aspects of rotomoulding, with the aim of producing performant end products and parts, with uniform wall thickness and potentially in complex shapes. The book is also of great interest to professionals across the plastics industry, as well as researchers and advanced students in plastics engineering, industrial design, mechanical engineering, chemical engineering, and materials science and engineering.
- Provides a strong fundamental understanding of all aspects of the rotational moulding process, from material to finished product
- Offers a highly practical combination of technical content and clear illustrations
- Covers the latest developments in rotomoulding, including novel materials and moulds, new products, and automated systems
1. Introduction to the rotational moulding process
2. Rotational moulding moulds and tooling
3. Rotational moulding machinery
4. Materials for rotational moulding
5. Rotational moulding design for functionality
6. Rotational moulding industry - the future
- Edition: 3
- Published: October 14, 2021
- Language: English
RC
Roy J Crawford
MK