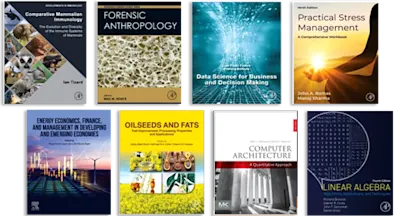
Practical E-Manufacturing and Supply Chain Management
- 1st Edition - October 4, 2004
- Imprint: Newnes
- Authors: Gerhard Greeff, Ranjan Ghoshal
- Language: English
- Paperback ISBN:9 7 8 - 0 - 7 5 0 6 - 6 2 7 2 - 7
- eBook ISBN:9 7 8 - 0 - 0 8 - 0 4 7 3 8 5 - 7
New technologies are revolutionising the way manufacturing and supply chain management are implemented. These changes are delivering manufacturing firms the competitive advantage… Read more
Purchase options
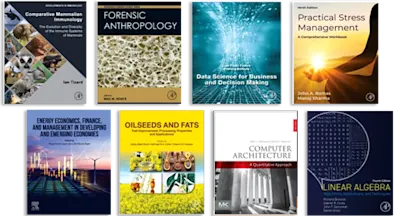
Preface
Disclaimer
Acknowledgements
Who is Altech Informatics?
Chapter 1: Introduction to e-manufacturing systems
1.1 Preamble
1.2 E-manufacturing definition
1.3 Background
1.4 E-manufacturing strategy
1.5 E-manufacturing challenges
1.6 E-manufacturing benefits
1.7 E-manufacturing and supply chain
Chapter 2: History of business automation
2.1 Introduction
2.2 Evolution of measurement instrumentation
2.3 Evolution of control systems
2.4 Evolution of process visualization systems
2.5 The evolution of accounting systems
2.6 Evolution of computers
2.7 Evolution of networks
2.8 Evolution of the Internet
2.9 Development of supply-chain management systems
2.10 Evolution of manufacturing execution systems
Chapter 3: System hierarchies and components
3.1 Introduction
3.2 Programmable logic controllers
3.3 Distributed control system
3.4 SCADA System
3.5 DCS and SCADA/PLC comparison
3.6 Hybrid control systems
3.7 Manufacturing execution systems
3.8 Enterprise resource planning systems
3.9 ERP and SCM relationship
3.10 Supply chain management
3.11 Operation management systems
3.12 Holonic manufacturing system
3.13 Collaborative manufacturing management systems
Chapter 4: Business process design models and concepts used in operations systems
4.1 Introduction
4.2 Theory of constraints
4.3 The supply-chain operation reference model
4.4 The ready, execute, process, analyze, coordinate model
4.5 Introduction to the IEC (6)1131-3 standard
4.6 S88 batch control standard
4.7 S95 Enterprise-Control System Integration Standard
4.8 Code of Federal Regulation (CFR) Title 21 part 11
4.9 Continuous improvement (Kaizen)
Chapter 5: Business process and system modeling tools and packages
5.1 Introduction
5.2 Generic BMTs
5.3 IDEF0
5.4 Unified modeling language
5.5 Computer-aided software engineering tools
5.6 ARIS
5.7 VISIO
5.8 Oracle Designer
5.9 Bpwin
Chapter 6: Enterprise planning and supply-chain interaction
6.1 Introduction
6.2 Logistics planning and optimization
6.3 E-fulfillment
6.4 Business process optimization
6.5 Procurement management
6.6 Supplier relationship management
6.7 Customer relationship management
6.8 Material returns management
Chapter 7: Product and plant knowledge management
7.1 Introduction
7.2 Product life cycle management
7.3 Quality management
7.4 Laboratory information management systems
7.5 Document management
Chapter 8: Production capability management
8.1 Introduction
8.2 Labor management
8.3 Equipment management
8.4 Material storage and availability management
8.5 Lean manufacturing
Chapter 9: Production scheduling, management and control
9.1 Introduction
9.2 Enterprise scheduling
9.3 Finite capacity scheduling
9.4 Dispatching production units
9.5 Resource allocation
9.6 Process management
9.7 Production systems collaboration
Chapter 10: Production data collection and performance analysis
10.1 Introduction
10.2 Changing face of manufacturing strategies
10.3 Performance analysis strategies
10.4 Performance analysis systems
10.5 Performance analysis concepts
10.6 Outcome metrics
10.7 Product tracking and genealogy
10.8 Data collection/acquisition
Chapter 11: Project motivation and benefit quantification
11.1 Introduction
11.2 Project portfolio
11.3 Project motivation
11.4 Potential benefits
11.5 Benefits of IT architecture components
11.6 Benefit quantification
11.7 Benefits and architectural levels
11.8 Extended benefit analysis
11.9 Benefits of an extended business case
11.10 Benefit examples
11.11 Measurement examples
Chapter 12: System integration models and concepts
12.1 Purpose of integration and interfacing
12.2 The gap between ERP and PMC
12.3 ERP–MES integration
12.4 MES within an enterprise – data flow diagram
12.5 Integration architectures evolution
12.6 Eight systems architecture alternatives
12.7 Integration data identification
12.8 Common communication protocol
Chapter 13: Product and vendor evaluation methodology
13.1 Software vendor functional scope
13.2 Software selection trends
13.3 Product landscape
13.4 Solution design assumptions
13.5 Proposed approach
13.6 Design revisit
13.7 System functionality and architecture design
13.8 Evaluation and selection teams
13.9 Visits to reference sites (if required)
13.10 Vendor survey form example
Chapter 14: Software project management
14.1 Development life cycle
14.2 Risk minimization
14.3 Solution design requirements
14.4 Software development life cycle
14.5 Life cycle components
14.6 Critical chain project management
Chapter 15: Change management
15.1 Organizational readiness
15.2 Reason for change
15.3 Strategies for change
15.4 Requirements for effective change
15.5 Change during system implementation
15.6 The three phases of change adoption
Chapter 16: Conclusion
16.1 Manufacturing future
16.2 Establishing leadership
16.3 Success dependencies
16.4 Synchronization vision
Appendix A: Practical exercises
Appendix B: Model answers
Glossary of terms
Bibliography
Index
- Edition: 1
- Published: October 4, 2004
- Imprint: Newnes
- Language: English
GG
Gerhard Greeff
His working career includes periods working as a plant supervisor, foreman and manager, quality manager, safety, health and environmental manager, change implementer and business consultant. He is currently employed as Divisional Manager: Consulting at Altech Informatics (Pty) Ltd, and is in charge of a group of consultants responsible for the design of manufacturing management software solutions, including SCADA, MES, SCM and others.
Gerhard has published various papers and articles related to production management, safety, health, environment and quality, as well as the implementation of change, software solution design and MES.
Gerhard fervently believes that software solutions should only be implemented to drive behavior, support business and physical processes, and to assist the company in achieving more value from these processes, not for any other reason. He believes that most of the concepts, tools and solutions explored in this book can be coordinated, synchronized and can add tremendous value to any manufacturer. He feels that the extent to which a company exploits their IT investment in this domain is only limited by economic factors and the individuals' imagination.
RG