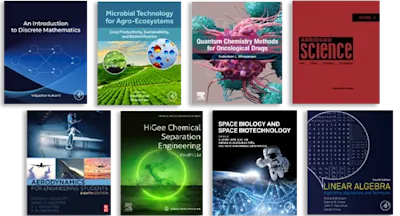
Plant and Process Engineering 360
- 1st Edition - December 3, 2009
- Author: Mike Tooley
- Language: English
- Hardback ISBN:9 7 8 - 1 - 8 5 6 1 7 - 8 4 0 - 2
- eBook ISBN:9 7 8 - 1 - 8 5 6 1 7 - 8 4 1 - 9
Plant and Process Engineering 360 will be the backbone of any plant, chemical, or process engineer’s library. This is a broad area in which engineers need to be familiar with a wi… Read more
Purchase options
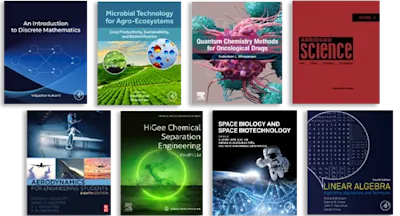
Plant and Process Engineering 360 will be the backbone of any plant, chemical, or process engineer’s library. This is a broad area in which engineers need to be familiar with a wide array of techniques, technologies and equipment. Its focus on providing a broad introduction to key systems make the book the first point of reference for engineers who are involved with designing, specifying, maintaining or working with plant, process and control technologies in many sectors, including manufacturing, chemical process, and energy.
- A single-source of plant and process equipment information for engineers, providing a 360 degree view of the critical equipment engineers encounter
- Enables readers to get up to speed with unfamiliar topics quickly with an overview of important but disparate technologies that are specific to plant engineering
- Covers the systems and processes that drive effective and efficient plants and processes
- Drawn from authoritative Elsevier resources, this book is a ‘first port of call’ with breadth and depth of content, from leading figures in the field.
Cluster E-brochure, trade shows and conferences, online display ads, 2x-Email blast to in-house subscribers, e-newsletters, and web feature
- Section One: Introduction
- Chapter 1.1: Instrumentation and transducers
- 1.1.1 Introduction
- 1.1.2 Temperature
- 1.1.3 Flow
- 1.1.4 Pressure
- 1.1.5 Level transducers
- 1.1.6 Position transducers
- 1.1.7 Velocity and acceleration
- 1.1.8 Strain gauges, load cells and weighing
- 1.1.9 Fieldbus systems
- 1.1.10 Installation notes
- Chapter 1.2: Control systems
- 1.2.1 Introduction
- 1.2.2 Laplace transforms and the transfer function
- 1.2.3 Block diagrams
- 1.2.4 Feedback
- 1.2.5 Generally desirable and acceptable behaviour
- 1.2.6 Stability
- 1.2.7 Classification of system and static accuracy
- 1.2.8 Transient behaviour
- 1.2.9 Root-locus method
- 1.2.10 Frequency-response methods
- 1.2.11 State-space description
- 1.2.12 Sampled-data systems
- 1.2.13 Some necessary mathematical preliminaries
- 1.2.14 Sampler and zero-order hold
- 1.2.15 Block diagrams
- 1.2.16 Closed-loop systems
- 1.2.17 Stability
- 1.2.18 Example
- 1.2.19 Dead-beat response
- 1.2.20 Simulation
- 1.2.21 Multivariable control
- 1.2.22 Dealing with non-linear elements
- 1.2.23 Disturbances
- 1.2.24 Ratio control
- 1.2.25 Transit delays
- 1.2.26 Stability
- 1.2.27 Industrial controllers
- 1.2.28 Digital control algorithms
- 1.2.29 Auto-tuners
- 1.2.30 Practical tuning methods
- Chapter 1.3: Programmable controllers
- 1.3.1 Introduction
- 1.3.2 The programmable controller
- 1.3.3 Programming methods
- 1.3.4 Numerics
- 1.3.5 Distributed systems and fieldbus
- 1.3.6 Graphics
- 1.3.7 Software engineering
- 1.3.8 Safety
- Chapter 1.4: Control systems interfacing
- 1.4.1 Actuator–sensor (as) interface
- 1.4.2 Industrial control system interface devices
- 1.4.3 HMI in industrial control
- 1.4.4 Highway Addressable Remote Transducer (HART) field communications
- Chapter 1.1: Instrumentation and transducers
- Section Two: Motors and drives
- Chapter 2.1: Electromechanical systems
- 2.1.1 Principles of automation
- 2.1.2 Machine tools
- 2.1.3 Robots
- 2.1.4 Other applications
- 2.1.5 Motion-control systems
- 2.1.6 Summary
- Chapter 2.2: Analysing a drive system
- 2.2.1 Rotary systems
- 2.2.2 Linear systems
- 2.2.3 Friction
- 2.2.4 Motion profiles
- 2.2.5 Assessment of a motor–drive system
- 2.2.6 Summary
- Chapter 2.3: Motors, motor control and drives
- 2.3.1 Introduction
- 2.3.2 The direct current motor
- 2.3.3 The cage induction motor
- 2.3.4 The slipring induction motor
- 2.3.5 The ac synchronous motor
- 2.3.6 The brushless servomotor
- 2.3.7 The reluctance motor
- 2.3.8 The switched reluctance motor
- 2.3.9 Mechanical and duty cycle considerations
- 2.3.10 Drive power circuits
- 2.3.11 Effects of semiconductor power converters
- 2.3.12 The commercial drive
- 2.3.13 Standards
- Chapter 2.4: Variable speed drives
- 2.4.1 The need for variable speed drives
- 2.4.2 Fundamental principles
- 2.4.3 Torque–speed curves for variable speed drives
- 2.4.4 Types of variable speed drives
- 2.4.5 Mechanical variable speed drive methods
- 2.4.6 Hydraulic variable speed drive methods
- 2.4.7 Electromagnetic or ‘eddy current’ coupling
- 2.4.8 Electrical variable speed drive methods
- Chapter 2.5: Induction motors
- 2.5.1 Introduction
- 2.5.2 Basic construction
- 2.5.3 Principles of operation
- 2.5.4 The equivalent circuit
- 2.5.5 Electrical and mechanical performance
- 2.5.6 Motor acceleration
- 2.5.7 AC induction generator performance
- 2.5.8 Efficiency of electric motors
- 2.5.9 Rating of AC induction motors
- 2.5.10 Electric motor duty cycles
- 2.5.11 Cooling and ventilation of electric motors (IC)
- 2.5.12 A Degree of protection of motor enclosures (IP)
- 2.5.13 Construction and mounting of AC induction motors
- 2.5.14 Anti-condensation heaters
- 2.5.15 Methods of starting AC induction motors
- 2.5.16 Motor selection
- Chapter 2.1: Electromechanical systems
- Section Three: Electronic drive control
- Chapter 3.1: Electronic circuits and devices
- 3.1.1 Introduction
- 3.1.2 Diode converters
- 3.1.3 Active devices
- 3.1.4 Principles of switching circuits
- 3.1.5 High-frequency power supplies
- 3.1.6 Standards
- Chapter 3.2: Electronic converters
- 3.2.1 Introduction
- 3.2.2 Definitions
- 3.2.3 Power diodes
- 3.2.4 Power thyristors
- 3.2.5 Commutation
- 3.2.6 Power electronic rectifiers (AC/DC converters)
- 3.2.7 Gate-commutated inverters (DC/AC converters)
- 3.2.8 Gate-controlled power electronic devices
- 3.2.9 Other power converter circuit components
- Chapter 3.1: Electronic circuits and devices
- Section Four: Power transmission
- Chapter 4.1: Power transmission
- 4.1.1 Gearboxes
- 4.1.2 Lead and ball screws
- 4.1.3 Belt drives
- 4.1.4.Bearings
- 4.1.5 Couplings
- 4.1.6 Shafts
- 4.1.7 Linear drives
- 4.1.8 Review of motor–drive sizing
- 4.1.9 Summary
- Chapter 4.2: Gears and gearboxes
- 4.2.1 Configuration
- 4.2.2 Performance
- 4.2.3 Installation
- 4.2.4 Operating methods
- Chapter 4.1: Power transmission
- Section Five: Hydraulic and pneumatic systems
- Chapter 5.1: Hydraulic fundamentals
- 5.1.1 Introduction
- 5.1.2 Basic hydraulics
- 5.1.3 Forces in liquids
- 5.1.4 Hydraulic pumps
- 5.1.5 Hydraulic fluids
- 5.1.6 Reservoirs, strainers, filters, and accumulators
- 5.1.7 Actuators
- 5.1.8 Control valves
- 5.1.9 Lines, fittings, and seals
- Chapter 5.2: Pneumatic fundamentals
- 5.2.1 Introduction
- 5.2.2 Characteristics of compressed air
- 5.2.3 Generation of pressure
- 5.2.4 Compressors
- 5.2.5 Air dryers
- 5.2.6 Dried air systems
- 5.2.7 Air reservoir (receivers)
- 5.2.8 Safety valves
- 5.2.9 Coolers
- Chapter 5.3: Pump types and characteristics
- 5.3.1 Applications
- 5.3.2 Pump types
- 5.3.3 Reciprocating pumps
- 5.3.4 Rotary pumps
- 5.3.5 Centrifugal pumps
- Chapter 5.4: Centrifugal pump design
- 5.4.1 Impellers
- 5.4.2 Pump casings
- 5.4.3 Wearing rings
- 5.4.4 Shaft
- 5.4.5 Stuffing boxes
- 5.4.6 Mechanical seals and seal housings
- 5.4.7 Bearing housing/bearing isolators
- 5.4.8 Couplings
- Chapter 5.5: Pump hydraulics
- 5.5.1 Specific gravity
- 5.5.2 Viscosity
- 5.5.3 Vapor pressure
- 5.5.4 Flow
- 5.5.5 Head
- 5.5.6 System resistance
- 5.5.7 Pump efficiency
- 5.5.8 Hydraulic power
- 5.5.9 Pump characteristic curve
- 5.5.10 Curve corrections
- 5.5.11 Specific speed
- 5.5.12 Cavitation, recirculation, and net positive suction head (NPSH)
- 5.5.13 Suction-specific speed
- 5.5.14 Performance calculation procedure
- Chapter 5.6: Hydraulic pumps and pressure regulation
- 5.6.1 Pressure regulation
- 5.6.2 Pump types
- 5.6.3 Loading valves
- 5.6.4 Filters
- 5.6a Air compressors, air treatment and pressure regulation
- 5.6a.1 Compressor types
- 5.6a.2 Air receivers and compressor control
- 5.6a.3 Air treatment
- 5.6a.4 Stages of air treatment
- 5.6a.5 Filters
- 5.6a.6 Air dryers
- 5.6a.7 Lubricators
- 5.6a.8 Pressure regulation
- 5.6a.9 Service units
- Chapter 5.7: Actuators
- 5.7.1 Linear actuators
- 5.7.2 Seals
- 5.7.3 Rotary actuators
- 5.7.4 Application notes
- 5.7.5 Bellows actuator
- Chapter 5.1: Hydraulic fundamentals
- Index
- Physical Constants in SI Units
- Edition: 1
- Published: December 3, 2009
- Language: English
MT