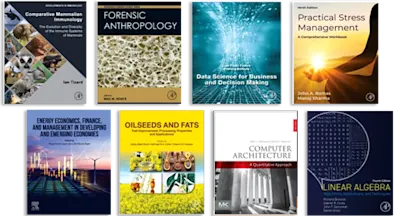
Photoelasticity for Designers
International Series of Monographs in Mechanical Engineering
- 1st Edition - September 3, 2013
- Imprint: Pergamon
- Author: R. B. Heywood
- Editors: D. J. Silverleaf, G. Blackburn
- Language: English
- Paperback ISBN:9 7 8 - 1 - 4 8 3 1 - 1 9 5 3 - 3
- eBook ISBN:9 7 8 - 1 - 4 8 3 1 - 5 1 9 5 - 3
Photoelasticity for Designers covers the fundamental principles and techniques of photoelasticity, with an emphasis on its value as an aid to engineering design. This book is… Read more
Purchase options
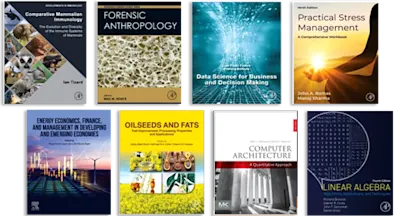
Photoelasticity for Designers covers the fundamental principles and techniques of photoelasticity, with an emphasis on its value as an aid to engineering design. This book is divided into 12 chapters, and begins with an introduction to the essential optical effects necessary for an understanding of the photoelastic phenomena. The next chapters describe the concept and features of polariscopes; the characterization of photoelastic materials; the formulation and testing of two-dimensional models of photoelasticity; and the application of model stresses to prototypes for the analysis of stresses occurring in the plane of the model, effectively of uniform thickness. These topics are followed by a discussion of the frozen stress technique and a comparison of the various materials that can be used for models in the technique. The ending chapters deal with the principles and application of the birefringent coating and distorted model techniques. This book will prove useful to photoelasticians, design engineers, and students.
Preface
Definitions
List of Symbols
Conversion Table
Multiplying Factors
1 Behavior of Light in Plane Polariscope
1.1. Nature of Light
1.2. Polaroid Polarizers
1.3. Polarization by Reflection or Refraction
1.4. Nicol Prism
1.5. Simple Polariscope
1.6. Determination of Polarization Axis
1.7. Effect of Stressed Transparent Model in Plane Polariscope
1.8. Stress- and Strain-Optical Coefficients Expressed in Terms of Relative Retardation
1.9. Derivation of Stress-Optical Coefficient
1.10. Fringe-Stress and Fringe-Strain Coefficients Expressed in Terms of the Fringe Order
1.11. The Brewster Unit
1.12. Three-Dimensional Effects
1.13. Summary of Photoelastic Effect
1.14. Effect of Plastic Strain
1.15. Comparison of Fringe-Stress and Strain Coefficients
1.16. Analysis by Light Vectors
1.17. Intensity of Light Emerging from Polariscope
1.18. Photoelastic Effect Using White Light
1.19. Isoclinics
1.20. Lines of Principal Stress
2 Behavior of Light in Circular Polariscope
2.1. Circularly Polarized Light
2.2. Polariscope Arrangements
2.3. Features of the Circular Polariscope
2.4. White Light in Circular Polariscope
2.5. λ/4 plates
2.6. Effect of a Stressed Model in Circular Polariscope
2.7. Compensators
3 Polariscopes
3.1. Diffusion Polariscope
3.2. Lens Polariscope
3.3. Parallel Light
3.4. Length of Polariscope
3.5. Two Lenses in System
3.6. Comparison of Diffusion and Lens-Type Polariscopes
3.7. Reflection Polariscopes
3.8. Examination of Fringes
3.9. Quality of Lenses for Polariscopes
3.10. Light Source
3.11. Photography
3.12. Camera
4 Photoelastic Materials
4.1. History
4.2. Measurement of Fringe-Stress and Strain Coefficients
4.3. Values of the Fringe-Stress and Strain Coefficients
4.4. Mechanical Properties
4.5. Choice of Material
4.6. Materials Available
4.7. Epoxy Resins
4.8. Catalin 61 893
4.9. Catalin 800 and Marblette
4.10. Columbia Resin CR 39
4.11. Celluloid
4.12. Gelatin
4.13. Polycarbonate
4.14. Urethane Rubber
4.15. Temperature Effects on the Fringe-Stress and Strain Coefficients
4.16. Effect of Creep on the Fringe-Stress and Strain Coefficients
4.17. Photoelastic Dispersion
4.18. Time-Edge Effects
4.19. Effect of Various Liquids on Plastics
4.20. Distribution of Surface Stresses in Notched Parts
4.21. Liquids Causing Damage to Plastics
4.22. Annealing
5 Two-Dimensional Models: Their Preparation and Testing
5.1. Making the Model
5.2. Machining of Plastics
5.3. Grinding and Polishing the Faces of Models
5.4. Loading Frames
5.5. Tension
5.6. Compression
5.7. Bending
5.8. Load Application and Measurement
5.9. Significance of Fringes
5.10. Thickness of Model
5.11. Boundary Stresses
5.12. Counting the Fringes
5.13. Self-Calibrating Models
6 Model Stresses Applied to Prototypes
6.1. Plane Stress and Plane Strain
6.2. Effect of Elastic Constants—Two-Dimensional
6.3. Effect of Elastic Constants—Three-Dimensional
6.4. Interpretation of Model Stresses to the Prototype
6.5. Notches
6.6. Comparison of Designs
6.7. St. Venant's Principle
7 Separation of Stresses within Two-Dimensional Model
7.1. When Separation Needs to be Undertaken
7.2. Transverse Stress Just Below Free Boundary
7.3. Principal Stresses On Axis of Symmetry
7.4. Separation of Principal Stresses by the Oblique Incidence Method
7.5. Frocht's Shear Difference Method
7.6. Lateral Extensometer
7.7. Filon's graphical method
7.8. Evaluation of Stress Sum from Laplace'S Equation
8 Frozen Stress Technique for Three-Dimensional Analysis
8.1. Three-Dimensional Techniques
8.2. Development and Theory of the Frozen Stress Method
8.3. Heat Treatment
8.4. Oven
8.5. Slicing the Model
8.6. Examination of Slice
8.7. Double Slice or Subslice Method of Examination
8.8. Post's Core Method of Examination at a Free Boundary
8.9. Examination of Slice by the Oblique Incidence Method
8.10. Immersion Fluid
8.11. Counting the Fringes
8.12. Determination of Fringe-Stress Coefficient
8.13. Distortion
8.14. Advantages of Distortion
8.15. Effect of Poisson's Ratio
Applications
8.16. Turbine Disk
8.17. Poppet Valve
8.18. Crankshaft
8.19. Gear Wheel
8.20. Dynamic Applications
8.21. Gravitational Fields
8.22. Quenching Stresses
9 Materials for Frozen Stress Analysis
9.1. General Comparison of Material Properties
9.2. Epoxy Resins
9.3. Catalin 61 893
9.4. Fosterite
9.5. Catalin 800 (Phenolic Resin)
9.6. Marco Resin SB 28C
9.7. Castolite
9.8. Columbia Resin CR 39
9.9. Kriston
9.10. Gelatin
10 Birefringent Coating Technique
10.1. Description of Method
10.2. Stress and Strain in the Prototype
10.3. Technique
10.4. Coating Errors
10.5. Fringe Multiplication
10.6. Techniques with Examination Parallel to Surface
10.7. The Photoelastic Strain Gauge
11 Improvement of Designs
11.1. Nature's Designs
11.2. Perfection in Design
11.3. Design Procedures
11.4. Streamline, Ideal or Neutral Fillets
11.5. Technique for Ascertaining the Ideal Contour
11.6. Improving the Shape of Fillets
11.7. Shape of Streamline Fillets
11.8. Size of Streamline Fillets
11.9. General Conclusions as to the Shape of Streamline Fillets
Examples of Streamline Fillets
11.10. Streamline Fillets in Flanged Parts
11.11. Streamline Fillets in Connecting Rods
11.12. Streamline Fillets in Loaded Projections
11.13. Streamline Fillets in Shouldered Shafts
11.14. Comparison of Fillet Shapes
11.15. Machining Considerations
11.16. Elliptical Fillets
11.17. Undercut Fillets
11.18. Removal of External Corners
12 New Distorted Model Technique for the Improvement of Designs
12.1. Outline
12.2. Basis of Method
12.3. Distortion at Stress Concentrations
12.4. General Distortion
12.5. Effect of Poisson's Ratio
12.6. Model Tests
Examples
12.7. Grooved Specimens
12.8. Shouldered Specimens
12.9. Holes
12.10. Miscellaneous Designs
12.11. Association of Distorted Model Technique with Photoelasticity
12.12. Three-Dimensional Models
Bibliography
Author Index
Subject Index
- Edition: 1
- Published: September 3, 2013
- Imprint: Pergamon
- Language: English
Read Photoelasticity for Designers on ScienceDirect