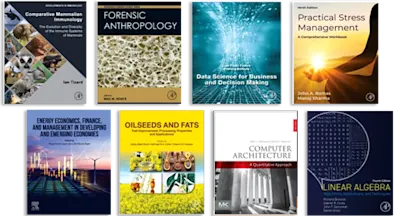
Permeability Properties of Plastics and Elastomers
- 3rd Edition - September 8, 2011
- Imprint: William Andrew
- Author: Laurence W. McKeen
- Language: English
- Hardback ISBN:9 7 8 - 1 - 4 3 7 7 - 3 4 6 9 - 0
- eBook ISBN:9 7 8 - 1 - 4 3 7 7 - 3 4 7 0 - 6
Permeability properties are essential data for the selection of materials and design of products across a broad range of market sectors from food packaging to Automotive ap… Read more
Purchase options
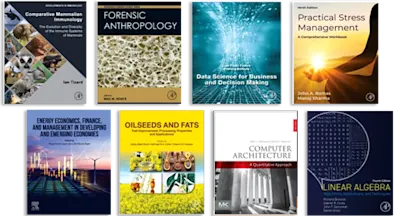
Permeability properties are essential data for the selection of materials and design of products across a broad range of market sectors from food packaging to Automotive applications to Medical Devices. This unique handbook brings together a wealth of permeability data in a form that enables quick like-for-like comparisons between materials.
The data is supported by a full explanation of its interpretation, and an introduction to the engineering aspects of permeability in polymers.
The third edition includes expanded explanatory text which makes the book accessible to novices as well as experienced engineers, written by industry insider and author Larry McKeen (DuPont), and 20% new data and major new explanatory text sections to aid in the interpretation and application of the data.
- A unique collection of permeability data designed to enable quick like-for-like comparisons between different materials
- Third edition includes 20% new data and expanded explanatory text, which makes the book accessible to novices as well as experienced engineers
- Essential reference for materials engineers, design engineers and applications engineers across sectors including packaging, automotive and medical devices
Plastics Engineers, Product Design Engineers, Materials Engineers, Application Engineers in Packaging (films), Automotive, Medical Device, Pharmaceutical, Food, Cosmetics etc. industries. Polymer and Coatings Chemists, users of film packaging products and containers, coatings manufacturers and users, users of polymer membranes and films for other applications (such as solar panels, fuel cells), designers of automotive components that are exposed to fuels, oils, fluids and other liquids
Dedication
Series Page
Preface
1. Introduction to Permeation of Plastics and Elastomers
1.1. History
1.2. Transport of Gases and Vapors through Solid Materials
1.3. Multiple-Layered Films
1.4. Permeation of Coatings
1.5. Permeation and Vapor Transmission Testing
1.6. Summary
2. Introduction to Plastics and Polymers
2.1. Polymerization
2.2. Copolymers
2.3. Linear, Branched, and Cross-Linked Polymers
2.4. Polarity
2.5. Unsaturation
2.6. Steric Hindrance
2.7. Isomers
2.8. Inter- and Intramolecular Attractions in Polymers
2.9. General Classifications
2.10. Plastic Compositions
2.11. Summary
3. Production of Films, Containers, and Membranes
3.1. Extrusion
3.2. Blown Film
3.3. Calendering
3.4. Casting Film Lines
3.5. Post Film Formation Processing
3.6. Web Coating
3.7. Lamination
3.8. Orientation
3.9. Membrane Production
3.10. Molding of Containers
3.11. Fluorination
3.12. Coatings
3.13. Summary
4. Markets and Applications for Films, Containers, and Membranes
4.1. Barrier Films in Packaging
4.2. Containers
4.3. Automotive Fuel Tanks and Hoses
4.4. Coatings
4.5. Gloves
4.6. Membranes
5. Styrenic Plastics
5.1. Acrylonitrile–Butadiene–Styrene Copolymer
5.2. Acrylonitrile–Styrene–Acrylate
5.3. Polystyrene
5.4. Styrene–Acrylonitrile Copolymer
6. Polyesters
6.1. Liquid Crystalline Polymers
6.2. Polybutylene Terephthalate (PBT)
6.3. Polycarbonate (PC)
6.4. Polycyclohexylene-dimethylene Terephthalate
6.5. Polyethylene Naphthalate
6.6. Polyethylene Terephthalate (PET)
7. Polyimides
7.1. Polyamide–Imide
7.2. Polyetherimide
7.3. Polyimide
8. Polyamides (Nylons)
8.1. Amorphous Polyamide (Nylon)
8.2. Polyamide 6 (Nylon 6)
8.3. Polyamide 11 (Nylon 11)
8.4. Polyamide 12 (Nylon 12)
8.5. Polyamide 66 (Nylon 66)
8.6. Polyamide 66/610(Nylon 66/610)
8.7. Polyamide 6/12 (Nylon 6/12)
8.8. Polyamide 666 (Nylon 666 or 6/66)
8.9. Polyamide 6/69 (Nylon 6/6.9)
8.10. Polyarylamide
8.11. Polyphthalamide/High Performance Polyamide
9. Polyolefins, Polyvinyls, and Acrylics
9.1. Polyethylene
9.2. Polypropylene
9.3. Polybutadiene
9.4. Polymethylpentene
9.5. Cyclic Olefin Copolymer
9.6. Ethylene–Vinyl Acetate Copolymer
9.7. Ethylene–Vinyl Alcohol Copolymer
9.8. Polyvinyl Butyral
9.9. Polyvinyl Chloride
9.10. Polyvinylidene Chloride
9.11. Polyacrylics
9.12. Acrylonitrile–Methyl Acrylate Copolymer
9.13. Ionomers
Chapter 10. Fluoropolymers
10.1. Polytetrafluoroethylene (PTFE)
10.2. Fluorinated Ethylene Propylene (FEP)
10.3. Perfluoroalkoxy (PFA)
10.4. Hexafluoropropylene, Tetrafluoroethylene, Ethylene Terpolymer (HTE)
10.5. Tetrafluoroethylene, Hexafluoropropylene, Vinylidene Fluoride Terpolymer (THV™)
10.6. Amorphous Fluoropolymer (AF)—Teflon AF®
10.7. Polyvinyl Fluoride (PVF)
10.8. Polychlorotrifluoroethylene (PCTFE)
10.9. Polyvinylidene Fluoride (PVDF)
10.10. Ethylene–Tetrafluoroethylene Copolymer (ETFE)
10.11. Ethylene–Chlorotrifluoroethylene Copolymer (ECTFE)
11. High-Temperature and High-Performance Polymers
11.1. Polyether Ether Ketone
11.2. Polysiloxane
11.3. Polyphenylene Sulfide
11.4. Polysulfone
11.5. Polyethersulfone
11.6. Polybenzimidazole
11.7. Parylene (poly(p-xylylene))
11.8. Polyoxymethylene (POM or Acetal Homopolymer)/Polyoxymethylene Copolymer (POM-Co or Acetal Copolymer)
12. Elastomers and Rubbers
12.1. Thermoplastic Polyurethane Elastomers (TPU)
12.2. Olefinic TPEs (TPO)
12.3. Thermoplastic Copolyester Elastomers (TPE-E or COPE)
12.4. Thermoplastic Polyether Block Polyamide Elastomers (PEBA)
12.5. Styrenic Block Copolymer (SBC) TPEs
12.6. Ethylene Acrylic Elastomers (AEM)
12.7. Bromobutyl Rubber
12.8. Butyl Rubber
12.9. Chlorobutyl Rubber (Polychloroprene)
12.10. Ethylene–Propylene Rubbers (EPM, EPDM)
12.11. Epichlorohydrin Rubber (CO, ECO)
12.12. Fluoroelastomers (FKM)
12.13. Natural Rubber
12.14. Acrylonitrile–Butadiene Copolymer (NBR)
12.15. Styrene–Butadiene Rubber (SBR)
13. Environmentally Friendly Polymers
13.1. Cellophane™
13.2. Nitrocellulose
13.3. Cellulose Acetate
13.4. Ethyl Cellulose
13.5. Polycaprolactone
13.6. Poly(Lactic Acid)
13.7. Poly-3-Hydroxybutyrate
14. Multilayered Films
14.1. Metalized Films
14.2. Silicon Oxide Coating Technology
14.3. Co-continuous Lamellar Structures
14.4. Multilayered Films
Appendix A. Conversion Factors
Appendix B. Reference Fuel Compositions
Appendix C
Index
- Edition: 3
- Published: September 8, 2011
- Imprint: William Andrew
- Language: English
LM