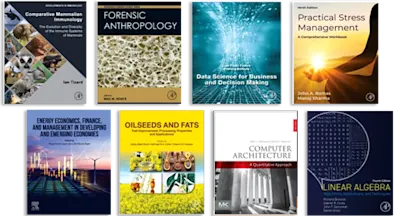
Palladium Membrane Technology for Hydrogen Production, Carbon Capture and Other Applications
Principles, Energy Production and Other Applications
- 1st Edition - October 10, 2014
- Imprint: Woodhead Publishing
- Editors: A Doukelis, K Panopoulos, A Koumanakos, E Kakaras
- Language: English
- Paperback ISBN:9 7 8 - 0 - 0 8 - 1 0 1 5 2 2 - 3
- Hardback ISBN:9 7 8 - 1 - 7 8 2 4 2 - 2 3 4 - 1
- eBook ISBN:9 7 8 - 1 - 7 8 2 4 2 - 2 4 1 - 9
Thanks to their outstanding hydrogen selectivity, palladium membranes have attracted extensive R&D interest. They are a potential breakthrough technology for hydrogen produc… Read more
Purchase options
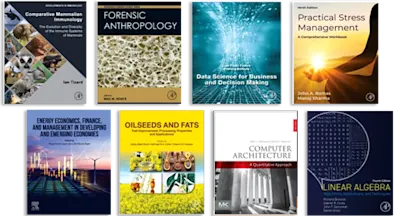
- Review of manufacture and design issues for palladium membranes
- Discussion of the applications of palladium membrane technology, including solar steam reforming, IGCC plants, NGCC plants, CHP plants and hydrogen production
- Examples of the technology in operation
1: Introduction to palladium membrane technology
- 1.1 Introduction
- 1.2 Current palladium membrane technology and research
- 1.3 Principles and types of palladium membrane
- 1.4 Separation mechanisms
- 1.5 Palladium-based membranes
- 1.6 Manufacturing of palladium membranes
- 1.7 Applications of palladium membranes
- 1.8 Palladium membrane technology scale-up issues
Part One: Membrane fabrication and reactor design
2: Fabrication of palladium-based membranes by magnetron sputtering
- 2.1 Introduction
- 2.2 Membrane fabrication by magnetron sputtering
- 2.3 Membrane and module design
- 2.4 Conclusions
- Acknowledgements
3: The use of electroless plating as a deposition technology in the fabrication of palladium-based membranes
- 3.1 Introduction
- 3.2 Electroless plating
- 3.3 Industrial electroless plating applications
- 3.4 Other deposition techniques and their pros/cons
- 3.5 Important process parameters in scaling up electroless plating
4: Large-scale ceramic support fabrication for palladium membranes
- 4.1 Introduction
- 4.2 Tubular porous ceramic substrates
- 4.3 Flat porous ceramic substrates
- 4.4 Macro- and mesoporous membrane layers made by slurry coating
- 4.5 Mesoporous ceramic membrane layers made by the sol-gel process
- 4.6 Special demands on palladium-supporting ceramic ultra-filtration (UF) membranes
- 4.7 Mass production of ceramic membranes for ultra-filtration (UF)
- 4.8 Strategies for reducing ceramic membrane production costs
- 4.9 Conclusions
5: Fabrication of supported palladium alloy membranes using electroless plating techniques
- 5.1 Introduction
- 5.2 Preparation of palladium membranes by electroless plating (ELP)
- 5.3 “Pore-fill” palladium membranes
- 5.4 Preparation of an ultra-thin Pd-Ag alloy membrane supported on a YSZ-γ-Al2O3 nanocomposite
- 5.5 High temperature Pd-based supported membranes
- 5.6 Conclusion
6: Development and application of self-supported palladium membranes
- 6.1 Introduction
- 6.2 Properties of hydrogenated Pd-Ag
- 6.3 Dense Pd-Ag membranes
- 6.4 Applications: membrane reactors
- 6.5 Conclusions
7: Testing palladium membranes: methods and results
- 7.1 Introduction: key parameters in scaling up membrane technology
- 7.2 The KT – Kinetics Technology membrane assisted steam reforming plant
- 7.3 Membrane modules
- 7.4 Testing membrane module stability and durability
- 7.5 Conclusions
8: Criteria for palladium membrane reactor design: architecture, thermal effects and autothermal design
- 8.1 Introduction
- 8.2 Design and modelling of an isothermal, single reaction, single reactor
- 8.3 Design and modelling of an isothermal, single reaction, distributed system
- 8.4 Modelling multiple reactions
- 8.5 Modelling thermal effects
- 8.6 Conclusions
- Acknowledgement
9: Simulation of palladium membrane reactors: a simulator developed in the CACHET-II project
- 9.1 Introduction
- 9.2 Reactor configurations investigated during the CACHET-II project
- 9.3 Model development
- 9.4 Sub-models
- 9.5 Calculation of physical properties
- 9.6 Implementing the model: reactor modules
- 9.7 Use of the program
- Nomenclature
- Greek symbols
Part Two: Application of palladium membrane technology in hydrogen production, carbon capture and other applications
10: Palladium membranes in solar steam reforming
- 10.1 Introduction: what is steam reforming?
- 10.2 The use of solar energy in steam reforming
- 10.3 The use of palladium membranes in solar steam reforming
- 10.4 Examples of solar steam reforming technology using palladium membranes
11: Using palladium membranes for carbon capture in integrated gasification combined cycle (IGCC) power plants
- 11.1 Introduction
- 11.2 Integrated gasification combined cycle (IGCC) plants
- 11.3 Handling sulphur in IGCC membrane plants
- 11.4 Palladium membranes for IGCC applications
- 11.5 Thermodynamic performance of IGCC plants using palladium membranes
- 11.6 Effect of the membrane operating conditions on plant performance
- 11.7 Economic assessment
- 11.8 Conclusions
- Appendix: nomenclature
12: Using palladium membranes for carbon capture in natural gas combined cycle (NGCC) power plants: process integration and techno-economics
- 12.1 Introduction
- 12.2 Design of key components for the optimum operation of the power plant
- 12.3 Design of water gas shift (WGS) reactors and membrane reactors (MRs)
- 12.4 Purification, compression and recirculation
- 12.5 Determining optimum operating parameters
- 12.6 Optimized case study
- 12.7 Economic evaluation
- 12.8 Conclusions
13: Using palladium membrane reformers for hydrogen production
- 13.1 Introduction
- 13.2 KT – Kinetics Technology reformer and membrane module (RMM) pilot plant
- 13.3 RMM operation mode
- 13.4 RMM performance
- 13.5 Conclusions
14: Operation of a palladium membrane reformer system for hydrogen production: the case of Tokyo Gas
- 14.1 Introduction
- 14.2 Membrane reformers (MRFs): key principles
- 14.3 Performance of the MRF system: hydrogen production and carbon capture
- 14.4 Durability of the membrane module
- 14.5 Long-term operation of the MRF system
- 14.6 Conclusions
- Acknowledgements
15: Using palladium membrane-based fuel reformers for combined heat and power (CHP) plants
- 15.1 Introduction
- 15.2 Current micro-CHP systems
- 15.3 Membrane reactor fuel processing for fuel cell-based micro-CHP systems
- 15.4 Comparison between fixed and fluidized bed membrane reactors for micro-CHP systems
- 15.5 Conclusions and future trends
- Note for the reader
16: Review of palladium membrane use in biorefinery operations
- 16.1 Introduction
- 16.2 Pure H2 production
- 16.3 Main chemicals production
- 16.4 Fuel upgrading
- 16.5 By-products recovery through reforming
- 16.6 Further considerations for potential uses
- 16.7 Conclusions
- Edition: 1
- Published: October 10, 2014
- Imprint: Woodhead Publishing
- Language: English
AD
A Doukelis
KP
K Panopoulos
AK
A Koumanakos
EK