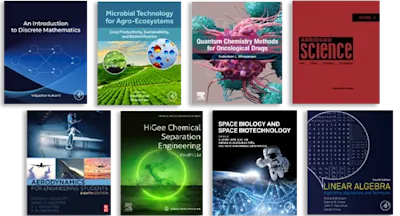
Offshore Pipelines
Design, Installation, and Maintenance
- 2nd Edition - August 26, 2013
- Authors: Boyun Guo, Shanhong Song Ph.D., Ali Ghalambor, Tian Ran Lin PhD
- Language: English
- Hardback ISBN:9 7 8 - 0 - 1 2 - 3 9 7 9 4 9 - 0
- eBook ISBN:9 7 8 - 0 - 1 2 - 3 9 8 4 9 2 - 0
The development of oil and gas fields offshore requires specialized pipeline equipment. The structures must be strong enough to with stand the harshest environments, and ensure th… Read more
Purchase options
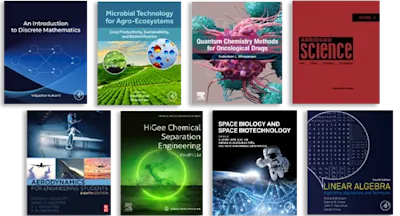
The development of oil and gas fields offshore requires specialized pipeline equipment. The structures must be strong enough to with stand the harshest environments, and ensure that production is not interrupted and remains economically feasible. However, recent events in the Gulf of Mexico have placed a new importance on maintenance and reliability. A new section; Condition Based Maintenance (CBM), introduces the subject of maintenance, written by Tian Ran Lin, Queensland University of Technology, and Yong Sun, CSIRO Earth Science and Resource Engineering.
Two of the main objectives of CBM is maximizing reliability while preventing major or minor equipment malfunction and minimizing maintenance costs. In this new section, the authors deal with the multi-objective condition based maintenance optimization problem. CBM provides two major advantages: (1) an efficient approach for weighting maintenance objectives, and (2) a method for specifying physical methods for achieving those objectives. Maintenance cost and reliability objectives are calculated based on proportional hazards model and a control limit CBM replacement policy.
Written primarily for engineers and management personnel working on offshore and deepwater oil and gas pipelines, this book covers the fundamentals needed to design, Install, and commission pipeline projects. This new section along with a thorough update of the existing chapters represents a 30% increase in information over the previous edition.
- Covers offshore maintenance and maintenance support system
- Provides the fundamentals needed to design, Install, and commission pipeline project
- Methods and tools to deliver cost effective maintenance cost and system reliability
- New section on Condition-Based Maintenance written by Tian Ran Lin, Queensland University of Technology, and Yong Sun, CSIRO Earth Science and Resource Engineering ([email protected])
Preface
Chapter 1. Introduction
1.1 Overview
1.2 Pipeline Design
1.3 Pipeline Installation
1.4 Pipeline Operations
References
Part I: Pipeline Design
Part I. Pipeline Design
Chapter 2. General Design Information
2.1 Introduction
2.2 Design Data
References
Chapter 3. Diameter and Wall Thickness
3.1 Introduction
3.2 Design Procedure
3.3 Design Codes
References
Chapter 4. Hydrodynamic Stability of Pipelines
4.1 Introduction
4.2 Analysis Procedure
4.3 Methodology
4.4 Partially Buried Pipelines
References
Further Reading
Chapter 5. Pipeline Span
5.1 Introduction
5.2 Problem Description
5.3 Design Considerations
5.4 Design Criteria
5.5 Fatigue Analysis Guideline
References
Further Reading
Chapter 6. Operating Stresses
6.1 Introduction
6.2 Operating Forces
6.3 Stress-Analysis-Based Design
References
Chapter 7. Pipeline Riser Design
7.1 Introduction
7.2 Design Procedure
7.3 Load Cases
7.4 Wall Thickness
7.5 Allowable Stress Criteria
7.6 Dynamic and Fatigue Analysis
7.7 Corrosion Control Consideration
7.8 Riser Bends
7.9 Riser Clamps
Chapter 8. Pipeline External Corrosion Protection
8.1 Introduction
8.2 External Pipe Coatings
8.3 Cathodic Protection
Further Reading
Chapter 9. Pipeline Insulation
9.1 Introduction
9.2 Insulation Materials
9.3 PIP Insulation
9.4 General Requirements
9.5 Heat Transfer Analysis—An Example
References
Further Reading
Chapter 10. Introduction to Flexible Pipelines
10.1 Introduction
10.2 Flexible Pipe Manufacturers
10.3 Basics of Flexible Riser Analysis and Design
Further Reading
Part II: Pipeline Installation
Part II. Pipeline Installation
Chapter 11. Pipeline Installation Methods
11.1 Introduction
11.2 Lay Methods
11.3 Tow Methods
Further Reading
Chapter 12. Installation Bending Stress Control
12.1 Introduction
12.2 Lay Stresses
References
Further Reading
Chapter 13. Pipeline On-Bottom Stability Control
13.1 Introduction
13.2 Hydrodynamic Parameters
13.3 Soil Parameters
13.4 Stability Analysis Guidelines
13.5 Trenching/Jetting
References
Further Reading
Part III: Pipeline Commissioning and Operations
Part III. Pipeline Commissioning and Operations
Chapter 14. Pipeline Testing and Precommissioning
14.1 Introduction
14.2 Pipeline Precommissioning
References
Further Reading
Chapter 15. Flow Assurance
15.1 Introduction
15.2 Fluid Sampling and Characterizations
15.3 Impacts of Produced Water on Flow Assurance
15.4 Gas Hydrates
15.5 Wax Depositions
15.6 Asphaltene Depositions
15.7 Inorganic Precipitates—Scales
15.8 Corrosion
15.9 Severe Slugging
References
Further Reading
Chapter 16. Pigging Operations
16.1 Introduction
16.2 Pigging System
16.3 Selection of Pigs
16.4 Major Applications
16.5 Pigging Procedure
Reference
Further Reading
Part IV: Condition-Based Maintenance
Chapter 17. An Introduction to Condition-Based Maintenance
17.1 Introduction
17.2 Condition Monitoring
17.3 Condition-Based Asset Health Prediction Models and Methods
17.4 CBM Decision Making
References
Chapter 18. Pipeline Vibration and Condition Based Maintenance
18.1 Introduction
18.2 Pipeline Vibration
18.3 Condition Based Maintenance
References
Appendix A. Gas–Liquid Multiphase Flow in Pipeline
A.1 Introduction
A.2 Multiphase Flow Concepts
A.3 Flow Regime Classifications
A.4 Horizontal Gas–Liquid Flow Regime Maps
A.5 Flow Regime Transitions in Horizontal Gas–Liquid Flow
A.6 Modeling of Multiphase Flow in Horizontal Pipeline
Appendix B. Steady and Transient Solutions for Pipeline Temperature
B.1 Assumptions
B.2 Governing Equation
B.3 Solutions
Appendix C. Strength De-Rating of Old Pipelines
C.1 Introduction
C.2 Classification of Cavities
C.3 Analytical SCF Model for Medium Cavity
C.4 Analytical SCF Model for Shallow Cavity
C.5 Analytical SCF Model for Deep Cavity
C.6 Illustrative Example
References
Index
- Edition: 2
- Published: August 26, 2013
- Language: English
BG
Boyun Guo
SS
Shanhong Song Ph.D.
AG
Ali Ghalambor
TL