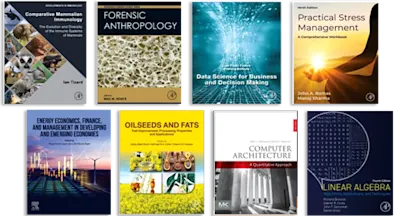
Non-destructive Testing of Impact Damage in Fiber-reinforced Polymer Composites
Fundamentals and Applications
- 1st Edition - August 8, 2024
- Imprint: Woodhead Publishing
- Editors: Milad Saeedifar, Mohamed Nasr Saleh
- Language: English
- Paperback ISBN:9 7 8 - 0 - 4 4 3 - 1 4 1 2 0 - 1
- eBook ISBN:9 7 8 - 0 - 4 4 3 - 1 4 1 2 1 - 8
Non-destructive Testing of Impact Damage in Fiber-reinforced Polymer Composites: Fundamentals and Applications provides detailed knowledge on the fundamentals and applicati… Read more
Purchase options
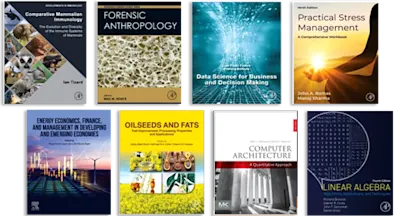
Non-destructive Testing of Impact Damage in Fiber-reinforced Polymer Composites: Fundamentals and Applications provides detailed knowledge on the fundamentals and applications of frequently used nondestructive testing (NDT) techniques utilized to assess impact damage in composite structures.
This book starts with an introduction to impact damage in composite structures, each subsequent chapter focuses on evaluating damage using specific NDT methods. Chapters 2–4 concentrate on vision-based NDT methods such as visual inspection, digital image correlation, and digital shearography. Following this, Chapters 5–6 delve into ultrasound-based methods, including acoustic emission and phased-array ultrasonic inspection. Radiation-based methods, micro-CT, and thermography are discussed in Chapters 7 and 8, while Chapters 9 and 10 elucidate microwave inspection and electrical impedance tomography.
This book is a useful reference for both academia and industry and covers the fundamentals, practical tips, case studies, and applications, as well as current research trends and future possibilities, for each technique.
- Insights into the diverse damage levels in composite materials resulting from low-velocity impact, ranging from micro matrix cracks to severe delamination and fiber breakage
- Covers a broad range of NDT techniques, including recently developed NDT techniques, suitable for detecting impact damage in composite materials
- Serves as a valuable reference for both academia and industry, providing comprehensive coverage of fundamental principles, practical insights, applications, case studies, current research trends, and future prospects for each NDT technique
Academic and industrial researchers in mechanical, aeronautical, electronic and measurement engineering, materials scientists, and civil engineers and all those who work with NDT and evaluation techniques in composite structures, PhD students, and postgraduate students
Mohamed Saleh, Changze Sun
2. Visual inspection of impact damage in composite materials
Mohammad Fotouhi , Sakineh Fotouhi, Ali Tabatabaeian
3. Impact damage analysis of composite structures using digital image correlation
Gustavo Quino
4. Assessment of impact damage of composite structures using digital shearography
Hernani Lopes, José Viriato Araújo dos Santos
5. Barely visible impact damage evaluation of composite laminates using acoustic emission
Milad Saeedifar
6. Integrity assessment of impacted thick composite laminates using phased array ultrasonic testing
Roger Groves, Ali Nokhbatolfoghahai
7. X-ray computed tomography for assessing impact damage in composites
Arief Yudhanto, Gilles lubineau
8. Impact damage assessment in composite laminates using infrared thermography
Stefano Sfarra, Mathias Kersemans, Morteza Moradi, Dimitrios Zarouchas
9. Microwave non-destructive testing techniques for detection and evaluation of impact damage in composites
Constantinos Soutis, Zhen Li, Andrew Gibson
10. Investigation of the impact damage in composites using electrical impedance tomography
Nataša Tomić
- Edition: 1
- Published: August 8, 2024
- Imprint: Woodhead Publishing
- Language: English
MS
Milad Saeedifar
Dr. Milad Saeedifar earned his Ph.D. in Mechanical Engineering from Amirkabir University of Technology, Iran, graduating with honors (summa cum laude). During a noteworthy three-year postdoctoral tenure at the Faculty of Aerospace Engineering at Delft University of Technology in the Netherlands, he actively contributed to extensive collaborative projects within the European Union, focusing on the nondestructive evaluation of composite and hybrid structures. In 2021, Dr. Saeedifar assumed the role of Assistant Professor at the Faculty of New Technologies and Aerospace Engineering at Ministry of Science, Research, and Technology (SBU), Iran. His primary research expertise lies in the non-destructive evaluation and health monitoring of composite structures. Presently, he serves as the director of the Laboratory of Structural Health Monitoring of Aerospace Structures. Dr. Saeedifar has authored over 50 research publications in the field of Non-Destructive Testing (NDT) and Structural Health Monitoring (SHM) of composite structures, with an h-index of 21. He is a distinguished researcher in his university and is listed in “2023 Stanford-Elsevier List of World Top 2% Scientists”.
MN
Mohamed Nasr Saleh
Dr. Mohamed Nasr Saleh is the Lead of the High temperature thermoplastic composites group at the Advanced Materials Research Centre (AMRC) as part of the Technology Innovation Institute (TII), UAE. With a PhD degree in Composite Materials from University of Manchester, Dr. Mohamed has 10+ years of experience in the field of composites and adhesives. Prior to joining TII in 2021, he held various research positions in the Netherlands (Delft University of Technology), and United Kingdom (AMRC with Boeing-University of Sheffield & National Composites Certification and Evaluation Facility-University of Manchester) during which he was involved in many large-scale collaborative projects with industrial partners in the automotive, maritime, and aerospace sectors. He has over 40 research publications in the field of damage mechanics of composite materials, multi-scale modelling of 3D woven composites and structural health monitoring of composites and adhesively bonded joints, with a continuous focus on industrial applications.