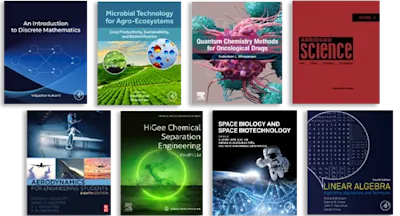
Non-Crimp Fabric Composites
Manufacturing, Properties and Applications
- 1st Edition - August 19, 2016
- Editor: Stepan V Lomov
- Language: English
- Hardback ISBN:9 7 8 - 1 - 8 4 5 6 9 - 7 6 2 - 4
- Paperback ISBN:9 7 8 - 0 - 0 8 - 1 0 1 7 0 5 - 0
- eBook ISBN:9 7 8 - 0 - 8 5 7 0 9 - 2 5 3 - 3
Non-crimp fabric (NCF) composites are reinforced with mats of straight (non-crimped) fibres, giving them such advantages as strength, ease of handling and low manufacturing costs.… Read more
Purchase options
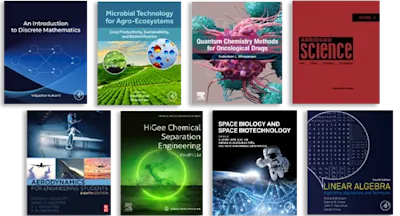
- Provides a comprehensive review of the use of NCF composites, their manufacture and applications in engineering
- Reviews the manufacture of non-crimp fabrics, including also topics such as structural stitching and automated defect analysis
- Examines the properties of NCF composites considering stiffness and strength, damage progression and fatigue
Contributor contact details
Introduction
Part I: Manufacturing of non-crimp fabrics
Chapter 1: Production of non-crimp fabrics for composites
Abstract:
1.1 Introduction
1.2 Warp-knitted non-crimp fabric (NCF)
1.3 Weft-knitted NCF
1.4 Non-crimp woven fabrics
1.5 3D woven and non-interlaced NCF
1.6 Fixation by adhesion
1.7 Comparison of production technologies
1.8 Future trends
1.9 Acknowledgments
Chapter 2: Standardisation of production technologies for non-crimp fabric composites
Abstract:
2.1 Introduction
2.2 Classification and standardisation of non-crimp fabric (NCF) production methods
2.3 Outstanding patents of existing machines for the production of NCFs
2.4 The ‘Hexcel patent’ – EP 0972102 B1
2.5 Product patents in the production of NCFs
2.6 Immobilisation of adhesive on the surface of semi-finished textile products (DE 102008004112 A1)
Chapter 3: Structural stitching of non-crimp fabric preforms for composites
Abstract:
3.1 Introduction
3.2 Threads for structural stitching technology
3.3 Stitching technology and sewing machines
3.4 Quality aspects for structural stitching
3.5 Applications and future trends
Chapter 4: Understanding and modelling the effect of stitching on the geometry of non-crimp fabrics
Abstract:
4.1 Introduction
4.2 General parameters of the fibrous plies
4.3 Geometry of the stitching
4.4 Distortions of fibres in the plies
4.5 Change of the geometry after shear
4.6 A geometrical model of NCF
4.7 Conclusion
Chapter 5: Automated analysis of defects in non-crimp fabrics for composites
Abstract:
5.1 Motivation
5.2 Quality characteristics of non-crimp fabric (NCF)
5.3 Quality analysis of NCF by digital image analysis
5.4 Future trends
Part II: Manufacturing of non-crimp fabric composites
Chapter 6: Deformability of textile performs in the manufacture of non-crimp fabric composites
Abstract:
6.1 Introduction
6.2 Shear
6.3 Biaxial tension
6.4 Compression
6.5 Bending
6.6 Conclusion
Chapter 7: Modelling the deformability of biaxial non-crimp fabric composites
Abstract:
7.1 Introduction
7.2 Behaviour of fabric architecture on the shear and draping behaviour of non-crimp fabrics (NCFs)
7.3 Modelling strategies for NCF forming
7.4 Energy-based kinematic mapping
7.5 Finite element modelling of forming for NCFs
7.6 Future trends
7.7 Further information and advice
Chapter 8: Permeability of non-crimp fabric preforms
Abstract:
8.1 Introduction
8.2 Experimental permeability results
8.3 Geometric effects
8.4 Deformation and permeability
8.5 Conclusions
8.6 Acknowledgements
8.8 Appendix: nomenclature
Chapter 9: Understanding variability in the permeability of non-crimp fabric composite reinforcements
Abstract:
9.1 Introduction
9.2 Material characterisation
9.3 Permeability measurement
9.4 Modelling and simulation
9.5 Future trends
Chapter 10: Modelling of the permeability of non-crimp fabrics for composites
Abstract:
10.1 Introduction
10.2 Numerical simulation
10.3 Experimental validation
10.4 Parametric study
10.5 Influence of shear
10.6 Conclusion
10.7 Acknowledgements
Part III: Properties of non-crimp fabric composites
Chapter 11: Mechanical properties of non-crimp fabric (NCF) based composites: stiffness and strength
Abstract:
11.1 Introduction
11.2 Materials and composite production
11.3 Test procedures
11.4 Mechanical properties of non-crimp fabric (NCF) composites
11.5 Mechanical properties of composites based on sheared MMCF
11.6 Damage development in B2 (0°/90°) laminates
11.8 Damage initiation in non-sheared and sheared materials
11.9 Conclusions
Chapter 12: Damage progression in non-crimp fabric composites
Abstract:
12.1 Introduction
12.2 Damage progression in non-crimp fabric (NCF) composites due to in-plane loading
12.3 Damage progression in impacted NCF composites
12.4 Conclusions
Chapter 13: Fatigue in non-crimp fabric composites
Abstract:
13.1 Introduction
13.2 Fatigue in non-crimp fabric (NCF) composites
13.3 Post-fatigue residual properties
13.4 Conclusions and open questions
13.6 Appendix
Chapter 14: Mechanical properties of structurally stitched non-crimp fabric composites
Abstract:
14.1 Introduction
14.2 Materials and stitching configurations
14.3 Characterisation of structurally stitched NCF laminates
14.4 Simulation of mechanical behaviour of structurally stitched laminates
14.5 Conclusions and future trends
Chapter 15: Predicting the effect of stitching on the mechanical properties and damage of non-crimp fabric composites: finite element analysis
Abstract:
15.1 Introduction
15.2 Representative volume element (RVE) of noncrimp fabric (NCF) composites
15.3 Elastic analysis
15.4 Damage accumulation in NCF composites
15.5 Conclusions
Chapter 16: Modelling drape, stress and impact behaviour of non-crimp fabric composites
Abstract:
16.1 Finite element (FE) methods for drape, stress and impact analysis
16.2 Laminate analysis and FE stiffness for non-crimp fabric (NCF)
16.3 FE methods for infusion analysis
16.4 Draping and FE simulation
16.5 Infusion simulation
16.6 Stiffness and failure
16.7 Impact and failure
Chapter 17: Modelling stiffness and strength of non-crimp fabric composites: semi-laminar analysis
Abstract:
17.1 Introduction
17.2 Stiffness models
17.3 Strength models for non-crimp fabric (NCF) composites
17.4 Conclusions
Part IV: Applications of non-crimp fabric composites
Chapter 18: Aerospace applications of non-crimp fabric composites
Abstract:
18.1 Introduction
18.2 Aeronautic requirements
18.3 Application examples
18.4 Future trends
Chapter 19: Non-crimp fabric: preforming analysis for helicopter applications
Abstract:
19.1 Introduction
19.2 Preform techniques for non-crimp fabrics (NCFs)
19.3 Main NCF deformation mechanism observed during preforming
19.4 Preforming defect analysis
19.5 Conclusion and future trends
Chapter 20: Automotive applications of non-crimp fabric composites
Abstract:
20.1 Introduction
20.2 Applications of non-crimp fabrics (NCF) in the automotive industry
20.3 Research and development for the use of NCF in automotive applications
20.4 Future trends
20.5 Conclusion
Chapter 21: Non-crimp fabric composites in wind turbines
Abstract:
21.1 Introduction
21.2 Development of non-crimp fabric (NCF) composites in wind energy
21.3 NCF materials used in nacelle construction
21.4 Future trends
Chapter 22: Cost analysis in using non-crimp fabric composites in engineering applications
Abstract:
22.1 Introduction
22.2 Costing methodologies: current approaches
22.3 Technical cost modelling
22.4 Case study: 40 m wind turbine blade shell
22.5 Acknowledgements
Index
- Edition: 1
- Published: August 19, 2016
- Language: English
SL
Stepan V Lomov
Prof. Stepan V. Lomov graduated with an M.S. in Physics-Mechanics from Leningrad Polytechnic Institute (1978) and then went on to complete his PhD in1985. He was awarded his Dr. Hab. on textile materials science in 1995, from St. Petersburg State University of Technology and Design. Since 1999, Professor Lomov has been working at KU Leuven, Belgium, in the Department of Materials Engineering. He was coordinator of the Composite Materials Group from 2013 to 2020. He was holder of the Toray Chair in Composite Materials at KU Leuven between 2013 to 2022 and has been an Emeritus Professor since 2020. His research areas include composites and textiles science and engineering: internal structure, manufacturing, in-service mechanical behaviour, nanocomposites, experimental damage mechanics, micro- and meso-level geometrical and mechanical models.