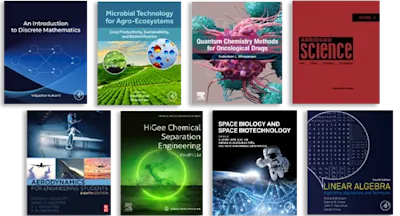
Nanomechanics for Coatings and Engineering Surfaces
Test Methods, Development Strategies, Modeling Approaches, and Applications
- 1st Edition - November 13, 2024
- Editors: Ben Beake, Tomasz Liskiewicz
- Language: English
- Paperback ISBN:9 7 8 - 0 - 4 4 3 - 1 3 3 3 4 - 3
- eBook ISBN:9 7 8 - 0 - 4 4 3 - 1 3 3 3 5 - 0
Nanomechanics for Coatings and Engineering Surfaces: Test Methods, Development Strategies, Modeling Approaches, and Applications provides readers with an array of best practices… Read more
Purchase options
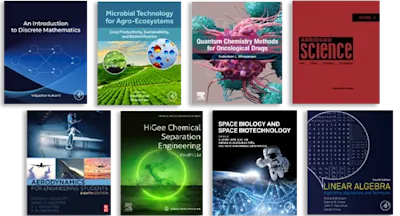
Nanomechanics for Coatings and Engineering Surfaces: Test Methods, Development Strategies, Modeling Approaches, and Applications provides readers with an array of best practices for nanoindentation measurements as well as related small-scale test methods and how to translate test results into the development of improved coatings. A core theme of the book is explaining to readers exactly how, when, and why the nanomechanical properties of engineered surfaces relate to their wear resistance.
The book starts with chapters that introduce the development and importance of nanomechanical testing and linkages between wear resistance and the mechanical properties of coatings before moving into discussions of various experimental methods and techniques, such as nanoindentation, continuous stiffness measurements, nano-scratch methods, high-temperature testing, nano-impact testing, and more. Other sections discuss modeling approaches such as finite element analysis, atomistic and molecular dynamics, and analytical methods. Design strategies and industrial applications are covered next, with a final section looking at trends and future directions.
- Provides best practices in nanoindentation measurements and related small-scale test methods
- Demonstrates how to use test results to develop improved coatings
- Outlines modeling approaches and numerical simulations
- Highlights selected applications for metallic nanocomposites, tribological coatings, solid lubricants, and aerospace coatings
- Shows future directions for simulation of complex wear scenarios
1. Development of nanomechanical testing
2. Development of additional nano-scale wear test techniques
3. Linking coating mechanical properties and wear resistance
Section 2: Experimental Methods/Techniques
4. Nanoindentation - strategies for reliable measurements on coated systems
5. Indentation Energy-based Analysis Methods
6. Nano-scratch testing
7. Reciprocating Nano- and Micro-scale Wear Testing
8. AFM nano-wear
9. Nano-impact testing
10. Micro and Nano-mechanics to understand the effects of residual stress on a coating's performance
11. Multi-sensing Approaches
12. High temperature testing
Section 3: Modelling Approaches
13. Analytical methods
14. Numerical simulation and Finite Element Analysis
15. Atomistic and Molecular Dynamics
Section 4: Coating and Engineering Surfaces: design strategies and industrial applications
16. H/E Revisited
17. Thin protective coatings on silicon for MEMS
18. DLC on steel for automotive applications
19. High speed machining
20. Nuclear materials
21. Aerospace coatings
22. Solid lubricants
23. Nanomechanics of Tribologically Transformed Surfaces
24. Microtribology Experiments for Hard Metals
Section 5: Summary
25. Trends and future directions
- Edition: 1
- Published: November 13, 2024
- Language: English
BB
Ben Beake
TL