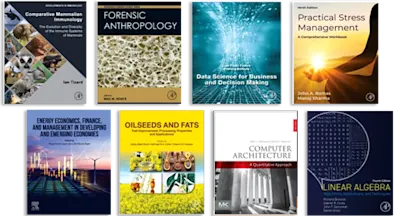
Multiscale Textile Preforms and Structures for Natural Fiber Composites
- 1st Edition - June 27, 2023
- Imprint: Woodhead Publishing
- Editors: Mohamad Midani, Tamer Hamouda, Ahmed H. Hassanin, Abdel-Fattah M. Seyam
- Language: English
- Paperback ISBN:9 7 8 - 0 - 3 2 3 - 9 5 3 2 9 - 0
- eBook ISBN:9 7 8 - 0 - 3 2 3 - 9 5 3 3 0 - 6
Textile reinforcement forms (preforms) play an important role in determining the properties of the final composite and product. The preform formation process provides precise co… Read more
Purchase options
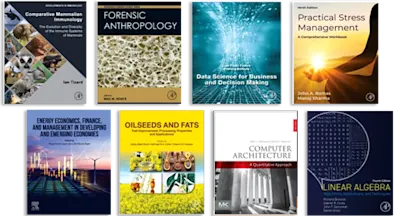
Textile reinforcement forms (preforms) play an important role in determining the properties of the final composite and product. The preform formation process provides precise control of the fiber architecture and orientation using a suitable textile manufacturing technique. While the techniques employed for preparing glass and carbon preforms are well-known, there is still a gap in understanding on how to prepare natural preforms for composite reinforcements.
Multiscale Textile Preforms and Structures for Natural Fiber Composites will bridge this gap by presenting unified knowledge on the relevant preform preparation techniques and resulting fiber architectures. Emphasis is on the structural parameters of each preform and their effect on the final composite properties. This book assembles information and knowledge on natural fiber reinforcement forms, including conventional forms, such as spun yarn, woven, knitted, nonwoven, braided, and comingled. These are illustrated and classified into one-, two-, and three-dimensional reinforcements. This book also includes information on nonconventional preform formation techniques such as unidirectional tapes, pre-impregnated preforms, spread tows, and tailored fiber placement.
- Covers all relevant textile processing technology for natural fiber preforms
- Provides academic researchers with a better understanding of recent practices in preparing textile reinforcements for natural fiber composites
- Helps practitioners determine how to use natural fiber reinforcements in producing new sustainable and innovative composites
Section I: Natural Fiber Reinforced Composites
1. Natural Fiber Reinforcements: Classification, Extraction, Treatment, and Properties
2. Natural Fiber Composite Features, Applications and Markets
Section II: One-dimensional Reinforcements
3. Natural Fiber Spun Yarn, Folded, and Blended Yarn
4. Natural Fiber: Twistless and Core Spun Yarn
Section III: Two-dimensional Reinforcements
5. Woven Natural Fiber Preforms
6. Nonwoven Natural Fiber Preforms
7. Knitted and Multiaxial Natural Fiber Preforms
8. Braided Natural Fiber Preforms
Section IV: Three-dimensional Reinforcements
9. 3D Woven Natural Fiber Preforms
10. 3D Braided Natural Fiber Preforms
Section V: Non-conventional Textile Reinforcements
11. Natural Fiber Unidirectional Tapes and Spread Tows
12. Pre-Impregnated Natural Fiber Preforms
13. Commingled Natural Fiber-Thermoplastic Preforms
14. Natural Fiber Tailored Fiber Placement
- Edition: 1
- Published: June 27, 2023
- Imprint: Woodhead Publishing
- Language: English
MM
Mohamad Midani
TH
Tamer Hamouda
AH
Ahmed H. Hassanin
AS