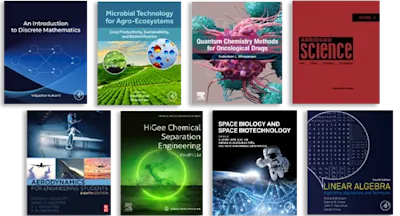
Motion and Path Planning for Additive Manufacturing
- 1st Edition - November 22, 2023
- Authors: Alex C. Roschli, Michael C. Borish, Abby K. Barnes, Thomas A. Feldhausen, Peter Wang, Eric MacDonald
- Language: English
- Paperback ISBN:9 7 8 - 0 - 4 4 3 - 1 5 2 8 6 - 3
- eBook ISBN:9 7 8 - 0 - 4 4 3 - 1 5 2 8 7 - 0
Motion and Path Planning for Additive Manufacturing takes a deep dive into the concepts and computations behind slicing software – the software that uses 3D models to generate… Read more
Purchase options
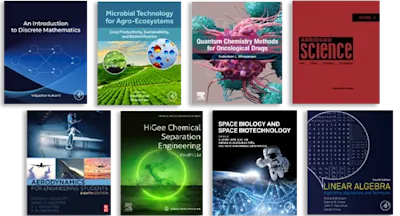
Motion and Path Planning for Additive Manufacturing takes a deep dive into the concepts and computations behind slicing software – the software that uses 3D models to generate the commands required to control the motion of a 3D printer and ultimately construct objects.
Starting with a brief review of the different types of motion in additive systems, this book walks through the steps of the path planning process and discusses the different types of toolpaths and their corresponding function in additive manufacturing. Planar, non-planar, and off-axis path planning are examined and explained. This book also presents pathing considerations for different types of 3D-printers, including extrusion, non-extrusion, and hybrid systems as well as 3- and 5-axis systems.
Engineers, researchers, and designers in the additive manufacturing field can use this book as a reference for every step of the path planning process, as well as a guide that explains the computations underlying the creation and use of toolpaths.
- Outlines the entire toolpath planning process required to go from a computer-aided design (CAD) model to G-code that a 3D printer can then use to construct a part
- Defines the terms and variables used in slicing and other path-planning software
- Highlights all the available kinematic arrangements for motion systems in additive manufacturing as well as the advantages and risks of each method
- Discusses the nuances of path planning for extrusion, non-extrusion, and hybrid process as well as 3- and 5-axis additive systems
- Provides an up-to-date explanation of advancements in toolpath planning and state-of-the-art slicing processes that use real-time data collection
1. Introduction to AM
2. Kinematics of Motion
3. Motion Platforms
4. Geometry Data Storage
5. Cross-sectioning
6. Closed-Loop Toolpath Generation
7. Space Filling Toolpath Generation
8. Open-Loop Toolpath Generation
9. Support, Raft, Brim, and Skirt Pathing
10. Path Modifiers
11. Travels, Optimizations, and Ordering
12. Pathing Considerations for Extrusion: Pellet, Filament, Concrete and Thermoset
13. Pathing Considerations for DED: Arc Welding and Laser Welding
14. Planar Slicing for Non-Extrusion AM Processes
15. Nonplanar Slicing
16. Pathing Considerations for 5-Axis Planar AM
17. Pathing Considerations for Hybrid AM
18. The G-Code File
19. Closing The Loop
- Edition: 1
- Published: November 22, 2023
- Language: English
AR
Alex C. Roschli
His current focus is software development for toolpath generation in additive manufacturing. This includes slicing, printing, motor and extrusion control, and closed loop data feedback. Alex manages development of ORNL Slicer 2, a novel toolpath generation software produced at ORNL.
MB
Michael C. Borish
Dr. Michael Borish is a research staff member in the Manufacturing Demonstration Facility (MDF) at Oak Ridge National Laboratory (ORNL), having joined in 2017. At the MDF, he engages in a wide range of disciplines within Computer Science as they relate to industrial additive manufacturing. This research encompasses visualization, augmented reality, path planning, and computer vision, to name a few. He hopes to expand the boundaries of what we define as manufacturing technology. He is also interested in altering established paradigms of operation particularly as it relates to slicing and path planning and has been developing custom slicing software to that end. He has also built an open-source community around slicing software to advance the state of the art in path planning for industrial additive manufacturing.
AB
Abby K. Barnes
TF
Thomas A. Feldhausen
PW
Peter Wang
EM
Eric MacDonald
Eric MacDonald, Ph.D. is Professor of Aerospace and Mechanical Engineering and Murchison Chair at the University of Texas at El Paso, and serves as the Associate Dean of Research and Graduate Studies for the College of Engineering. Dr. MacDonald received his doctoral degree in Electrical and Computer Engineering from the University of Texas at Austin in 2002. He worked in industry for 12 years at IBM and Motorola and subsequently co-founded a start-up specializing in CAD software, which was subsequently acquired by a firm in Silicon Valley. Dr. MacDonald held faculty fellowships at NASA’s Jet Propulsion Laboratory, US Navy Research and was awarded a US State Department Fulbright Fellowship in South America. His research interests include 3D printed multi-functional applications and process monitoring in additive manufacturing with instrumentation and computer vision for improved quality and yield.