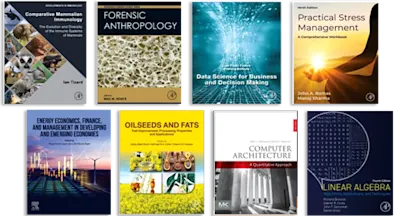
Molecular Dynamics Simulation of Nanocomposites using BIOVIA Materials Studio, Lammps and Gromacs
- 2nd Edition - May 30, 2025
- Imprint: Elsevier
- Author: Sumit Sharma
- Language: English
- Paperback ISBN:9 7 8 - 0 - 4 4 3 - 2 6 7 0 4 - 8
- eBook ISBN:9 7 8 - 0 - 4 4 3 - 2 6 7 0 5 - 5
Molecular Dynamics Simulation of Nanocomposites using BIOVIA Materials Studio, Lammps and Gromacs, Second Edition introduces the three major software packages essential for the mo… Read more
Purchase options
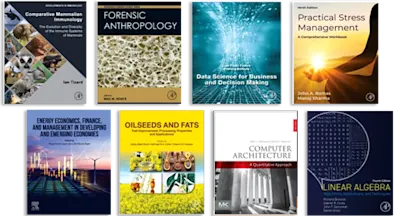
Molecular Dynamics Simulation of Nanocomposites using BIOVIA Materials Studio, Lammps and Gromacs, Second Edition introduces the three major software packages essential for the molecular dynamics simulation of nanocomposites, providing detailed instructions on utilizing each. This content is accompanied by real-world examples that illustrate when each should be applied. Numerous case studies demonstrate how each software package predicts various properties of nanocomposites, encompassing metal-matrix, polymer-matrix, and ceramic-matrix based nanocomposites. Explored properties include mechanical, thermal, optical, and electrical characteristics. This is a valuable resource for students, researchers, and scientists working in the field of molecular dynamics simulation.
All chapters have been fully updated to reflect the latest developments in the field, and this new edition has been enriched with additional chapters covering Al composites, machine learning, polymer coatings, and graphene-based materials and carbon nanotubes.
All chapters have been fully updated to reflect the latest developments in the field, and this new edition has been enriched with additional chapters covering Al composites, machine learning, polymer coatings, and graphene-based materials and carbon nanotubes.
- Provides a detailed explanation on the basic commands and modules of Materials Studio, Lammps, and Gromacs
- Demonstrates how these materials predict the mechanical, thermal, electrical, and optical properties of nanocomposites
- Introduces coding in LAMMPS, explaining modeling using Materials Studio and LAMMPS
- Utilizes case studies to illustrate the appropriate software for solving various nanoscale modeling problems
Materials scientists and mechanical engineers interested in nanoscale computational modelling
1. Introduction to Molecular Dynamics
1.1 Molecular Dynamics
1.2 Monte Carlo Simulation
1.3 Brownian Dynamics
1.4 Dissipative Particle Dynamics
1.5 Lattice Boltzmann Method
1.6 Basic Concepts
1.7 Molecular Dynamics Methodology
1.8 Molecular potential energy surface
2. Overview of Biovia Materials Studio, LAMMPS and GROMACS
2.1 Overview of Biovia Materials Studio
2.2 Overview of LAMMPS
2.3 Overview of GROMACS
3. Molecular Dynamics Simulation of Metal-Matrix Composites Using Biovia Materials Studio, LAMMPS and GROMACS
3.1 Prediction of Mechanical Properties of Graphene/Silicon Carbide Reinforced Aluminium Composites Using Biovia Materials Studio
3.2 Prediction of Mechanical Properties of Graphene/Copper Nanolayered Composites Using LAMMPS
3.3 Molecular Dynamics Simulation of Lithium Metal/Polymer Electrolyte Interfacial Properties Using GROMACS
4. Molecular Dynamics Simulation of Polymer-Matrix Composites Using Biovia Materials Studio, LAMMPS and GROMACS
4.1 Molecular Dynamics Simulation of Carbon Nanotubes and Polymer/Carbon Nanotube Composites
4.2 Molecular Dynamics Simulation of Functionalized SWCNT/Polymer Composites Using Lammps
4.3 Prediction of Tribological Properties of Carbon Nanotube Reinforced Natural Rubber Composites Using GROMACS
5. Molecular Dynamics Simulation of Ceramic-Matrix Composites Using Biovia Materials Studio, LAMMPS and GROMACS
5.1 Molecular Dynamics Simulation of Carbon Nanotube Reinforced Silicon Carbide Composites Using Biovia Materials Studio
5.2 Molecular Dynamics Simulation of Al/Al2O3 Metal-Ceramic Composite Using LAMMPS
5.3 Molecular Dynamics Simulation of Co-axial Boron Nitride/Carbon Nanotubes Using GROMACS
6. Scripting in Molecular Dynamics
6.1 Working with scripts in Materials Visualizer
6.2 Running scripts on server
6.3 Sample scripts
6.4 Scripting in LAMMPS
6.5 Scripting in GROMACS
7. Applications of BIOVIA Materials Studio, LAMMPS and GROMACS in Various Fields of Science and Engineering
7.1 Applications of Biovia Materials Studio
7.2 Applications of LAMMPS
7.3 Applications of GROMACS
8. Molecular dynamics modeling of 2D materials
8.1 Atomistic modeling of pentagraphene
8.2 Atomistic modeling of phagraphene
8.3 Atomistic modeling of C3N and N-doped boron carbide nanosheets
9. Vibrational behavior of carbon nanotubes and graphene
9.1 Introduction
9.2 Computational approach
9.3 MD modeling
9.4 Vibrational behavior of CNTs
9.5 Vibrational behavior of graphene
9.6 Effect of chirality, aspect ratio and defects
10. Wear of CNT reinforced Al composites
10.1 Introduction
10.2 Methodology
10.3 Modeling of 3-layer system
10.4 Tribological properties of CNT-Al composites
11. Machine learning and Molecular Dynamics
11.1 What is machine learning?
11.2 Application of ML in MD
11.3 Mathematical models
11.4 Effect of defects in graphene
11.5 ML procedure
12. Polymer coatings of metallic substrate
12.1 Methodology
12.2 Modeling of adhesion of polymer coatings
12.3 Modeling of diffusion of polymer coatings
13. Modeling of graphene oxide and reduced graphene oxide
13.1 Introduction
13.2 Modeling strategy
13.3 Mechanical behavior
13.4 Creep study
14. Effect of functionalization and defects in CNT on mechanical properties and creep behavior of nitrile butadiene rubber composites
14.1 Introduction
14.2 Methodology
14.3 Effect of functionalization
14.4 Effect of defects
14.5 Mechanical behavior
14.6 Creep analysis
15. The effect of chirality and defects on mechanical properties of carbon nanotube reinforced polycarbonate composites
15.1 Introduction
15.2 Modeling procedure
15.3 Effect of chirality
15.4 Effect of defects
15.5 Mechanical properties of composites
16. Structure of nanomaterials and composites
17. Machine learning with MD 18. Applications of MD in different fields
1.1 Molecular Dynamics
1.2 Monte Carlo Simulation
1.3 Brownian Dynamics
1.4 Dissipative Particle Dynamics
1.5 Lattice Boltzmann Method
1.6 Basic Concepts
1.7 Molecular Dynamics Methodology
1.8 Molecular potential energy surface
2. Overview of Biovia Materials Studio, LAMMPS and GROMACS
2.1 Overview of Biovia Materials Studio
2.2 Overview of LAMMPS
2.3 Overview of GROMACS
3. Molecular Dynamics Simulation of Metal-Matrix Composites Using Biovia Materials Studio, LAMMPS and GROMACS
3.1 Prediction of Mechanical Properties of Graphene/Silicon Carbide Reinforced Aluminium Composites Using Biovia Materials Studio
3.2 Prediction of Mechanical Properties of Graphene/Copper Nanolayered Composites Using LAMMPS
3.3 Molecular Dynamics Simulation of Lithium Metal/Polymer Electrolyte Interfacial Properties Using GROMACS
4. Molecular Dynamics Simulation of Polymer-Matrix Composites Using Biovia Materials Studio, LAMMPS and GROMACS
4.1 Molecular Dynamics Simulation of Carbon Nanotubes and Polymer/Carbon Nanotube Composites
4.2 Molecular Dynamics Simulation of Functionalized SWCNT/Polymer Composites Using Lammps
4.3 Prediction of Tribological Properties of Carbon Nanotube Reinforced Natural Rubber Composites Using GROMACS
5. Molecular Dynamics Simulation of Ceramic-Matrix Composites Using Biovia Materials Studio, LAMMPS and GROMACS
5.1 Molecular Dynamics Simulation of Carbon Nanotube Reinforced Silicon Carbide Composites Using Biovia Materials Studio
5.2 Molecular Dynamics Simulation of Al/Al2O3 Metal-Ceramic Composite Using LAMMPS
5.3 Molecular Dynamics Simulation of Co-axial Boron Nitride/Carbon Nanotubes Using GROMACS
6. Scripting in Molecular Dynamics
6.1 Working with scripts in Materials Visualizer
6.2 Running scripts on server
6.3 Sample scripts
6.4 Scripting in LAMMPS
6.5 Scripting in GROMACS
7. Applications of BIOVIA Materials Studio, LAMMPS and GROMACS in Various Fields of Science and Engineering
7.1 Applications of Biovia Materials Studio
7.2 Applications of LAMMPS
7.3 Applications of GROMACS
8. Molecular dynamics modeling of 2D materials
8.1 Atomistic modeling of pentagraphene
8.2 Atomistic modeling of phagraphene
8.3 Atomistic modeling of C3N and N-doped boron carbide nanosheets
9. Vibrational behavior of carbon nanotubes and graphene
9.1 Introduction
9.2 Computational approach
9.3 MD modeling
9.4 Vibrational behavior of CNTs
9.5 Vibrational behavior of graphene
9.6 Effect of chirality, aspect ratio and defects
10. Wear of CNT reinforced Al composites
10.1 Introduction
10.2 Methodology
10.3 Modeling of 3-layer system
10.4 Tribological properties of CNT-Al composites
11. Machine learning and Molecular Dynamics
11.1 What is machine learning?
11.2 Application of ML in MD
11.3 Mathematical models
11.4 Effect of defects in graphene
11.5 ML procedure
12. Polymer coatings of metallic substrate
12.1 Methodology
12.2 Modeling of adhesion of polymer coatings
12.3 Modeling of diffusion of polymer coatings
13. Modeling of graphene oxide and reduced graphene oxide
13.1 Introduction
13.2 Modeling strategy
13.3 Mechanical behavior
13.4 Creep study
14. Effect of functionalization and defects in CNT on mechanical properties and creep behavior of nitrile butadiene rubber composites
14.1 Introduction
14.2 Methodology
14.3 Effect of functionalization
14.4 Effect of defects
14.5 Mechanical behavior
14.6 Creep analysis
15. The effect of chirality and defects on mechanical properties of carbon nanotube reinforced polycarbonate composites
15.1 Introduction
15.2 Modeling procedure
15.3 Effect of chirality
15.4 Effect of defects
15.5 Mechanical properties of composites
16. Structure of nanomaterials and composites
17. Machine learning with MD 18. Applications of MD in different fields
- Edition: 2
- Published: May 30, 2025
- Imprint: Elsevier
- Language: English
SS
Sumit Sharma
Dr Sumit Sharma is Assistant Professor in the Department of Mechanical Engineering at Dr BR Ambedkar National Institute of Technology Jalandhar, India. Before joining this institute, he worked as an Assistant Professor in the School of Mechanical Engineering in Lovely Professional University, India. Dr Sharma’s interests are related to both theoretical and experimental aspects of mechanics and dynamics of nanomaterials and structures.
Affiliations and expertise
Assistant Professor, Dr. B R Ambedkar National Institute of Technology Jalandhar, IndiaRead Molecular Dynamics Simulation of Nanocomposites using BIOVIA Materials Studio, Lammps and Gromacs on ScienceDirect