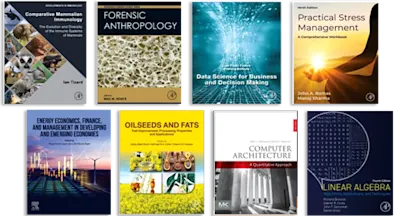
Modeling Damage, Fatigue and Failure of Composite Materials
- 2nd Edition - September 26, 2023
- Imprint: Woodhead Publishing
- Editors: Ramesh Talreja, Janis Varna
- Language: English
- Paperback ISBN:9 7 8 - 0 - 4 4 3 - 1 8 4 8 9 - 5
- eBook ISBN:9 7 8 - 0 - 4 4 3 - 1 8 4 8 8 - 8
Modeling Damage, Fatigue and Failure of Composite Materials, Second Edition provides the latest research in the field of composite materials, an area that has attracted a wealth of… Read more
Purchase options
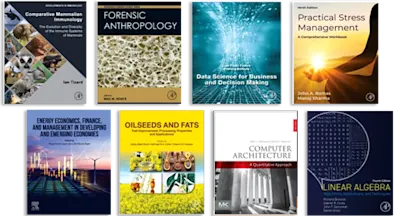
Modeling Damage, Fatigue and Failure of Composite Materials, Second Edition provides the latest research in the field of composite materials, an area that has attracted a wealth of research, with significant interest in the areas of damage, fatigue, and failure. The book is fully updated, and is a comprehensive source of physics-based models for the analysis of progressive and critical failure phenomena in composite materials. It focuses on materials modeling while also reviewing treatments for analyzing failure in composite structures. Sections review damage development in composite materials such as generic damage and damage accumulation in textile composites and under multiaxial loading.
Part Two focuses on the modeling of failure mechanisms in composite materials, with attention given to fiber/matrix cracking and debonding, compression failure, and delamination fracture. Final sections examine the modeling of damage and materials response in composite materials, including micro-level and multi-scale approaches, the failure analysis of composite materials and joints, and the applications of predictive failure models.
- Provides a comprehensive source of physics-based models for the analysis of progressive and critical failure phenomena in composite materials
- Assesses failure and life prediction in composite materials
- Discusses the applications of predictive failure models such as computational approaches to failure analysis
- Covers further developments in computational analyses and experimental techniques, along with new applications in aerospace, automotive, and energy (wind turbine blades) fields
- Covers delamination and thermoplastic-based composites
Industrial and academic researchers working in composite materials, aeronautic, automotive and energy applications and the development of technical textiles
1. Composite materials: constituents, architecture, and generic damage2. Fatigue damage mechanisms3. Damage accumulation in textile composites4. Damage accumulation under multiaxial fatigue loading5. Matrix and fiber–matrix interface cracking in composite materials6. Fiber–matrix debonding in composite materials: Transverse loading7. Fiber–matrix debonding in composite materials: Axial loading8. Evolution of multiple matrix cracking9. Fiber failure and debonding in composite materials/10. Compression failure of composite laminates11. Delamination fractures in composite materials12. Thermoelastic constants of damaged laminates: COD- and CSD-based methods13. Microlevel approaches to modeling of damage in composite materials: Generalized plane strain analysis14. A multiscale approach to modeling of composite damage15. Multiscale failure assessment of composite laminates16. Modeling the crack initiation in unidirectional laminates under multiaxial fatigue loading17. Incorporating manufacturing defects in damage and failure analysis18. Damage simulations in composite structures in the presence of stress gradients19. Failure models for composite joints: An approach based on singular stress states20. Computational analysis of notched composites21. Variational approach to modelling of damage
- Edition: 2
- Published: September 26, 2023
- Imprint: Woodhead Publishing
- Language: English
RT
Ramesh Talreja
JV