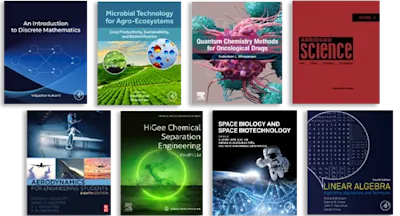
Metallurgical Failure Analysis
Techniques and Case Studies
- 1st Edition - January 8, 2018
- Author: Kannadi Palankeezhe Balan
- Language: English
- Paperback ISBN:9 7 8 - 0 - 1 2 - 8 1 4 3 3 6 - 0
- eBook ISBN:9 7 8 - 0 - 1 2 - 8 1 4 3 3 7 - 7
Metallurgical Failure Analysis: Techniques and Case Studies explores how components fail and what measures should be taken to avoid future failures. The book introduces the subje… Read more
Purchase options
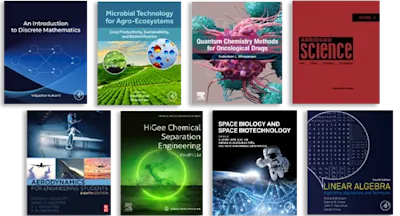
Metallurgical Failure Analysis: Techniques and Case Studies explores how components fail and what measures should be taken to avoid future failures. The book introduces the subject of failure analysis; covers the fundamentals and methodology of failure analysis, including fracture and fractography of metals and alloys and the tools and techniques used in a failure investigation; examines 37 case studies on high performance engineering components; features experimental results comprised of visual-, fractographic-, or metallographic- examination, hardness measurements and chemical analysis; includes illustrations and evidence obtained through test results to enhance understanding; and suggests suitable remedial measures when possible.
The various case studies are classified according to the major causes of failures. The case studies pertain to: Improper Material Selection, Manufacturing Defects, Casting Defects, Overload, Fatigue, Corrosion Induced Failures, Hydrogen Embrittlement and Stress Corrosion Cracking, Wear and Elevated Temperature Failures. The book contains information gathered over three decades of the author’s experience handling a variety of failure cases and will go a long way toward inspiring practicing failure analysts. The book is designed for scientists, metallurgists, engineers, quality control inspectors, professors and students alike.
- Explores the fundamentals and methodology of failure analysis
- Examines the major causes of component failures
- Teaches a systematic approach to investigation to determine the cause of a failure
- Features 37 case studies on high performance engineering components
Practicing failure analysts, Scientists, metallurgists, engineers, quality control inspectors, professors and students of mechanical, material science and metallurgical engineering courses
Part1- Fundamentals and Methodology
1 Introduction
2 Fracture
2.1 Ductile and Brittle Fractures
2.2 Fractography of Ductile and Brittle Fractures
2.3 Fatigue Fracture
2.4 Fractography of Fatigue Fracture
3 Tools and Techniques Used in Failure Analysis
3.1 Acquisition of Background Data
3.2 Selection of Samples
3.3 Photographic Records
3.4 Preliminary Examination
3.5 Non-Destructive Testing
3.6 Chemical Analysis
3.7 Fractography, Microscopy and Energy Dispersive Analysis
By X-Ray (EDAX) Using Scanning Electron Microscope
3.8 Optical Microscopy
3.9 Electron Probe Micro Analysis (EPMA)
3.10 X-Ray Diffraction
3.11 Evaluation of Mechanical Properties
Part2 - Case Studies
4 Improper Material Selection
4.1 Failure of Hip-joint prosthesis
4.2 Failure of Firing pin of 120mm Low Range Mortar
4.3 Failure of Shaft of a Gearbox
4.4 Failure of 7.62mm Cartridge Cases
4.5 Failure of Fin Mounting Nuts
5 Manufacturing Defect
5.1 Failure of Track Pins of Track Link
5.2 Failure of Track Shoe of an Infantry Combat Vehicle
5.3 Failure of Control Lever of Fuel Metering Unit of an
Aero Engine
5.4 Failure of Drill Rods for Mining
5.5 Failure of Lifting Lugs of a Missile
5.6 Failure of Breech Block of Light Machine Gun
5.7 Failure of Titanium Sponge Cutting Ring
6 Casting Defects
6.1 Failure of Exhaust Outer Cone of an Aero Engine
6.2 Failure of Sealing Rings of Centrifugal Breather of
an Aero Engine.
6.3 Failure of Grinding Rolls of Bowl Mill of a Thermal Power
Station.
7 Overload
7.1 Failure of Mounting Bolt of Emergency Changeover Valve
7.2 Failure of Steam Pipe in Unit-VI of a Thermal Power Station
7.3 Failure of Body of Saddle Assembly
7.4 Failure of Boiler Tube of a Thermal Power Station
8 Fatigue
8.1 Failure of Wheel Hub of an Aircraft
8.2 Failure of Bolts of Flapjack Mounting Bracket of an Aircraft
8.3 Failure of Compressor Rotor Blades of an Aero Engine
8.4 Failure of Bearing Cage of an Aero Engine
9 Corrosion Induced Failures
9.1 Failure of Nipple of Fuel Pipe Line
9.2 Failure of Condenser Tubes of Thermal Power Station
9.3 Failure of High Pressure Air and Hydraulic Pipes
9.4 Failure of Detonator of a Grenade
10 Hydrogen Embrittlement and Stress Corrosion Cracking
10.1 Failure of Fin Mounting Screws
10.2 Failure of Differential Valve Cover of Fuel Metering Unit
10.3 Failure of Lever Assembly of Main Undercarriage of an
Aircraft
10.4 Failure of Cartridge Seat Ejection Secondary of an Aircraft
11 Wear
11.1 Failure of Inter-Rotor Bearing of an Aero Engine
11.2 Failure of Low Temperature Super Heater Tube of
a Thermal Power Station
11.3 Failure of Main Landing Gear Assembly of an Aircraft
11.4 Failure of Coupling Shaft and Bevel Gear of an Aero Engine
12 Elevated Temperature Failures
12.1 Failure of a Bolt of Nozzle Guide Vane of an Aero Engine
12.2 Failure of Vanes of Front Nozzle Diaphragm Assembly of an
Aero Engine
12.3 Failure of Centre Main Bearing of an Aircraft Engine
12.4 Failure of Jet Nozzle Casing of an Aero Engine.
12.5 Failure of Turbine Stator Vanes of an Aero Engine
13 Bibliography
- Edition: 1
- Published: January 8, 2018
- Language: English
KP