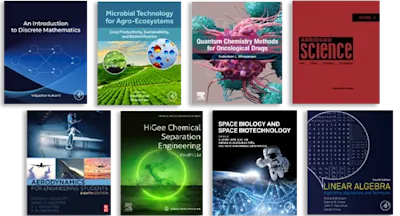
Metal Fatigue Testing and Analysis
Theory and Practice
- 1st Edition - January 29, 2025
- Imprint: Elsevier
- Author: Yung-Li Lee
- Language: English
- Paperback ISBN:9 7 8 - 0 - 4 4 3 - 2 6 6 6 5 - 2
- eBook ISBN:9 7 8 - 0 - 4 4 3 - 2 6 6 6 6 - 9
Metal Fatigue Testing and Analysis: Theory and Practice provides the theoretical knowledge and practical skills required to design durable metallic structures and compon… Read more
Purchase options
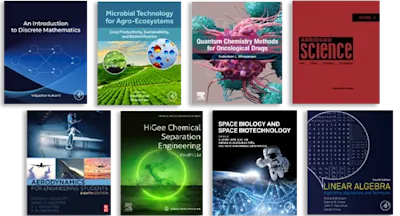
Metal Fatigue Testing and Analysis: Theory and Practice provides the theoretical knowledge and practical skills required to design durable metallic structures and components. The book thoroughly reviews fatigue and reliability theories for product durability designs, analyses, and validations, highlighting the latest advances and identifying key challenges. It is structured to guide readers in how to design targets from mission profile data, which is crucial in ensuring that structures (vehicle, systems, and components) meet the specific requirements of their applications. Insight is provided on how to analyze and design structures based on established targets, with practical insights and methodologies for structure designs provided.
Readers are guided through the development of validation tests to assess the durability of their designs, with emphasis placed on the importance of implementing reliability demonstration tests to ensure that test structures meet the design targets.
Readers are guided through the development of validation tests to assess the durability of their designs, with emphasis placed on the importance of implementing reliability demonstration tests to ensure that test structures meet the design targets.
- Reviews fatigue and reliability theories for product durability designs, analyses, and validations, highlighting the latest advances and identifying key challenges
- Guides readers on how to design targets from mission profile data, which is crucial in ensuring that structures (vehicle, systems, and components) meet the specific requirements of their applications
- Outlines the development of validation tests to assess the durability of their designs, emphasizing the importance of implementing reliability demonstration tests to ensure that test structures meet design targets
Academic researchers and professional engineers and material scientists, in particular those in mechanical engineering and/or the automotive industry
1. Fatigue damage theories
2. Rainflow cycle counting methods
3. Stress-based fatigue life estimation methods
4. Strain-based fatigue life estimation methods
5. Multiaxial fatigue theories
6. Theories of plasticity
7. Structural dynamics
8. Spectral fatigue damage estimation methods
9. Vibration fatigue test target development
10. Fatigue analysis of spot-welded and seam-welded joints
11. Thermomechanical fatigue damage – the neo-sehitoglu model
12. Reliability demonstration test methods
13. Durability test target development
2. Rainflow cycle counting methods
3. Stress-based fatigue life estimation methods
4. Strain-based fatigue life estimation methods
5. Multiaxial fatigue theories
6. Theories of plasticity
7. Structural dynamics
8. Spectral fatigue damage estimation methods
9. Vibration fatigue test target development
10. Fatigue analysis of spot-welded and seam-welded joints
11. Thermomechanical fatigue damage – the neo-sehitoglu model
12. Reliability demonstration test methods
13. Durability test target development
- Edition: 1
- Published: January 29, 2025
- Imprint: Elsevier
- Language: English
YL
Yung-Li Lee
Fatigue Expert and Technical Fellow at Chrysler Group LLC, Michigan, USA.
Affiliations and expertise
Chrysler Group LLC, Michigan, USARead Metal Fatigue Testing and Analysis on ScienceDirect