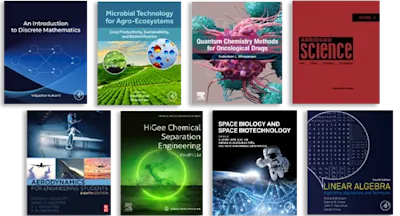
Manufacturing Processes for Advanced Composites
- 1st Edition - December 18, 2003
- Editor: Flake C Campbell Jr
- Language: English
- Paperback ISBN:9 7 8 - 0 - 4 4 4 - 5 5 1 7 2 - 6
- Hardback ISBN:9 7 8 - 1 - 8 5 6 1 7 - 4 1 5 - 2
- eBook ISBN:9 7 8 - 0 - 0 8 - 0 5 1 0 9 8 - 9
• One of very few books available to cover this subject area.• A practical book with a wealth of detail.This book covers the major manufacturing processes for polymer matrix com… Read more
Purchase options
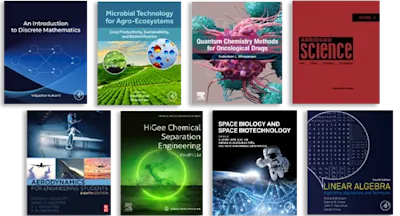
• A practical book with a wealth of detail.
This book covers the major manufacturing processes for polymer matrix composites with an emphasis on continuous fibre-reinforced composites. It covers the major fabrication processes in detail.
Very few books cover the details of fabrication and assembly processes for composites. This book is intended for the engineer who wants to learn more about composite processing: any one with some experience in composites should be able to read it. The author, who has 34 years experience in the aerospace industry, has intentionally left out mathematical models for processes so the book will be readable by the general engineer.
It differs from other books on composites manufacturing in focussing almost solely on manufacturing processes, while not attempting to cover materials, test methods, mechanical properties and other areas of composites.
Laminates
Fibers
Matrices
Product Forms
Overview of Fabrication Processes
Advantages and Disadvantages of Composites
Applications
Summary
Acknowledgement
References
Chapter 2 - Fibers and Reinforcements
Fiber Terminology
Glass Fibers
Aramid Fibers
Ultra-High Molecular Weight Polyethylene (UHMWPE) Fibers
Carbon and Graphite Fibers
Woven Fabrics
Reinforced Mats
Chopped Fibers
Prepreg Manufacturing
Summary
References
Chapter 3 - Thermoset Resins
Thermosets
Polyester Resins
Epoxy Resins
Bismaleimide Resins
Cyanate Ester Resins
Polyimide Resins
Phenolic Resins
Toughening Approaches
Physiochemical Characterization and Quality Control
Chemical Testing
Rheological Testing
Thermal Analysis
Glass Transition Temperature
Summary
References
Chapter 4 - Cure Tooling
General Considerations
Thermal Management
Tool Fabrication
Summary
References
Chapter 5 - Ply Collation
Prepreg Control
Tool Preparation
Manual LayUp
Ply Collation
Flat Ply Collation and Vacuum Forming
Automated Tape Laying
Filament Winding
Fiber Placement
Vacuum Bagging
Summary
References
Chapter 6 - Curing
Cure of Epoxy Composites
Theory of Void Formation
Hydrostatic Resin Pressure Studies
Chemical Composition Variables
Net and Low Flow Resin Systems
Resin and Prepreg Variables
LayUp Variables
Debulking Operations
Caul Plates and Pressure Intensifiers
Condensation Curing Systems
Residual Curing Stresses
Exotherm
In-Process Cure Monitoring
Cure Modeling
Summary
References
Chapter 7 - The Interaction of Chemical Composition and Processing on Laminate Quality
Prepreg Physical Properties
Chemical Properties
Thermal Properties
Rheological Properties
Laminate Evaluations
Summary
References
Chapter 8 - Adhesive Bonding and Integrally Cocured Structures
Adhesive Bonding
Advantages of Adhesive Bonding
Disadvantages of Adhesive Bonding
Theory of Adhesion
Joint Design
Adhesive Testing
Surface Preparation
Epoxy Adhesives
Bonding Procedures
Sandwich Structures
Honeycomb Core
Honeycomb Processing
Balsa Wood
Foam Cores
Syntactic Core
Inspection
Integrally Cocured Structure
Summary
References
Chapter 9 - Liquid Molding
Preform Technology
Fibers
Woven Fabrics
Three-Dimensional Woven Fabrics
Knitted Fabrics
Stitching
Braiding
P4A Process
Random Mat
Preform Advantages
Preform Disadvantages
Integral Structures Made by Textile Processes
Preform Lay-Up
Resin Injection
Curing
RTM Tooling
Resin Transfer Molding Defects
Resin Film Infusion
Vacuum Assisted Resin Transfer Molding
Summary
References
Chapter 10 - Thermoplastic Composites
The Case for Thermoplastic Composites
Thermoplastic Composite Matrices
Product Forms
Consolidation
Thermoforming
Joining
Summary
References
Chapter 11 - Commercial Processes
Lay-Up Processes
Compression Molding
Injection Molding
Structural Reaction Injection Molding
Pultrusion
Summary
References
Chapter 12 - Assembly
Trimming and Machining Operations
General Assembly Considerations
Hole Drilling
Fastener Installation
Sealing
Painting
Summary
References
Chapter 13 - Nondestructive Inspection and Repair
Nondestructive Inspection
Visual Inspection
Ultrasonic Inspection
Portable Equipment
Radiographic Inspection
Thermographic Inspection
Repair
Fill Repairs
Injection Repairs
Bolted Repairs
Bonded Repairs
Summary
References
Appendix A - Metric Conversions
- Edition: 1
- Published: December 18, 2003
- Language: English
FC