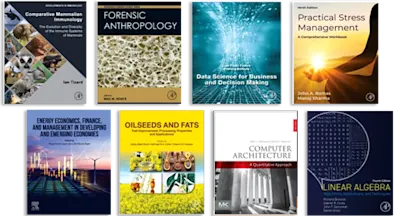
Manufacturing Process Selection Handbook
- 1st Edition - May 21, 2013
- Imprint: Butterworth-Heinemann
- Authors: K. G. Swift, J. D. Booker
- Language: English
- Hardback ISBN:9 7 8 - 0 - 0 8 - 0 9 9 3 6 0 - 7
- eBook ISBN:9 7 8 - 0 - 0 8 - 0 9 9 3 5 7 - 7
Manufacturing Process Selection Handbook provides engineers and designers with process knowledge and the essential technological and cost data to guide the selection of manufactu… Read more
Purchase options
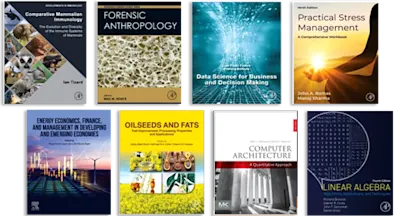
Manufacturing Process Selection Handbook provides engineers and designers with process knowledge and the essential technological and cost data to guide the selection of manufacturing processes early in the product development cycle.
Building on content from the authors’ earlier introductory Process Selection guide, this expanded handbook begins with the challenges and benefits of identifying manufacturing processes in the design phase and appropriate strategies for process selection. The bulk of the book is then dedicated to concise coverage of different manufacturing processes, providing a quick reference guide for easy comparison and informed decision making.
For each process examined, the book considers key factors driving selection decisions, including:
- Basic process descriptions with simple diagrams to illustrate
- Notes on material suitability
- Notes on available process variations
- Economic considerations such as costs and production rates
- Typical applications and product examples
- Notes on design aspects and quality issues
Providing a quick and effective reference for the informed selection of manufacturing processes with suitable characteristics and capabilities, Manufacturing Process Selection Handbook is intended to quickly develop or refresh your experience of selecting optimal processes and costing design alternatives in the context of concurrent engineering. It is an ideal reference for those working in mechanical design across a variety of industries and a valuable learning resource for advanced students undertaking design modules and projects as part of broader engineering programs.
- Provides manufacturing process information maps (PRIMAs) provide detailed information on the characteristics and capabilities of 65 processes in a standard format
- Includes process capability charts detailing the processing tolerance ranges for key material types
- Offers detailed methods for estimating costs, both at the component and assembly level
Preface
Acknowledgements
Notation
List of Terms
Units
Abbreviations – General
Abbreviations – Manufacturing Processes
Manufacturing Process Key (for Chapter 12)
Materials Key (for Plastics Processing)
Chapter 1. Introduction to the Handbook
1.1 The Economic Case for Manufacturing Process Selection
1.2 Manufacturing Process Information for Designers
1.3 This Handbook, its Objectives and Strategy
References
Chapter 2. Process Selection Strategies and Case Studies
2.1 Manufacturing Process Selection
2.2 Rapid Prototyping Process Selection
2.3 Surface Engineering Process Selection
2.4 Assembly System Selection
2.5 Joining Process Selection
References
Chapter 3. Casting Processes
3.1 Sand Casting
3.2 Shell Moulding
3.3 Gravity Die Casting
3.4 Pressure Die Casting
3.5 Centrifugal Casting
3.6 Investment Casting
3.7 Ceramic Mould Casting
3.8 Plaster Mould Casting
3.9 Squeeze Casting
Chapter 4. Forming Processes
4.1 Forging
4.2 Rolling
4.3 Drawing
4.4 Cold Forming
4.5 Cold Heading
4.6 Swaging
4.7 Superplastic Forming
4.8 Sheet-metal Shearing
4.9 Sheet-metal Forming
4.10 Spinning
4.11 Powder Metallurgy
4.12 Metal Injection Moulding
4.13 Continuous Extrusion (Metals)
Chapter 5. Plastics and Composites Processing
5.1 Injection Moulding
5.2 Reaction Injection Moulding
5.3 Compression Moulding
5.4 Resin Transfer Moulding
5.5 Vacuum Forming
5.6 Blow Moulding
5.7 Rotational Moulding
5.8 Contact Moulding
5.9 Pultrusion
5.10 Continuous Extrusion (Plastics)
Chapter 6. Machining Processes
6.1 Turning and Boring
6.2 Milling
6.3 Planing and Shaping
6.4 Drilling
6.5 Broaching
6.6 Reaming
6.7 Grinding
6.8 Honing
6.9 Lapping
Chapter 7. Non-traditional Machining Processes
7.1 Electrical Discharge Machining (EDM)
7.2 Electrochemical Machining (ECM)
7.3 Electron Beam Machining (EBM)
7.4 Laser Beam Machining (LBM)
7.5 Chemical Machining (CM)
7.6 Ultrasonic Machining (USM)
7.7 Abrasive Jet Machining (AJM)
Chapter 8. Rapid Prototyping Processes
8.1 Stereolithography (SLA)
8.2 3D Printing (3DP)
8.3 Selective Laser Sintering (SLS)
8.4 Laminated Object Manufacturing (LOM)
8.5 Fused Deposition Modelling (FDM)
Chapter 9. Surface Engineering Processes
9.1 Carburising
9.2 Nitriding
9.3 Ion Implantation
9.4 Anodising
9.5 Thermal Hardening
9.6 Shot Peening
9.7 Chromating
9.8 Chemical Vapour Deposition (CVD)
9.9 Physical Vapour Deposition (PVD)
9.10 Electroless Nickel
9.11 Electroplating
9.12 Hot Dip Coating
9.13 Thermal Spraying
Chapter 10. Assembly Systems
10.1 Manual Assembly
10.2 Flexible Assembly
10.3 Dedicated Assembly
Chapter 11. Joining Processes
11.1 Tungsten Inert-gas Welding (TIG)
11.2 Metal Inert-gas Welding (MIG)
11.3 Manual Metal Arc Welding (MMA)
11.4 Submerged Arc Welding (SAW)
11.5 Electron Beam Welding (EBW)
11.6 Laser Beam Welding (LBW)
11.7 Plasma Arc Welding (PAW)
11.8 Resistance Welding
11.9 Solid-state Welding
11.10 Thermit Welding (TW)
11.11 Gas Welding (GW)
11.12 Brazing
11.13 Soldering
11.14 Thermoplastic Welding
11.15 Adhesive Bonding
11.16 Mechanical Fastening
Chapter 12. Component Costing
12.1 Introduction
12.2 Basic Processing Cost (Pc)
12.3 Relative Cost Coefficient (Rc)
12.4 Material Cost (Mc)
12.5 Model Validation
12.6 Case Studies
12.7 Bespoke Costing Development
References
Chapter 13. Assembly Costing
13.1 Introduction
13.2 Assembly Costing Model
13.3 Assembly Structure Diagram
13.4 Case Studies
References
Appendices
Appendix A – Guidelines for Design for Manufacture (DFM)
Appendix B – Guidelines for Design for Assembly (DFA)
Appendix B1 – Functional Analysis
Appendix C – Weld Joint Design Configurations
Appendix D – Blank Component Costing Table
Appendix E – Blank Assembly Costing Table
Bibliography
Index
- Edition: 1
- Published: May 21, 2013
- Imprint: Butterworth-Heinemann
- Language: English
KS
K. G. Swift
JB