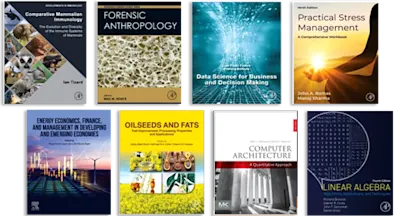
Manufacturing Assembly Handbook
- 1st Edition - November 13, 2013
- Imprint: Butterworth-Heinemann
- Author: Bruno Lotter
- Language: English
- Hardback ISBN:9 7 8 - 0 - 4 0 8 - 0 3 5 6 1 - 3
- Paperback ISBN:9 7 8 - 1 - 4 8 3 1 - 3 0 9 6 - 5
- eBook ISBN:9 7 8 - 1 - 4 8 3 1 - 6 3 3 8 - 3
Manufacturing Assembly Handbook identifies the possibilities for the rationalization of assembly in relation to the production rate and the product design. This book is based on… Read more
Purchase options
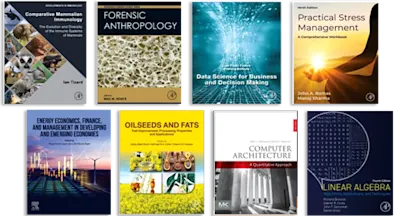
Manufacturing Assembly Handbook identifies the possibilities for the rationalization of assembly in relation to the production rate and the product design. This book is based on practical experience for practical application and will give experts in the field of rationalization guidelines for the solution of rationalization problems. Topics discussed in the text include the determination of the economic efficiency of assembly concepts, modules for the automation of assembly processes, design of assembly machines, and design of flexible-assembly systems. The integration of parts manufacturing processes into assembly equipment or of assembly operations into parts production equipment, planning and efficiency of automated assembly systems, and the operation of automated assembly systems are covered as well. Production engineers and managers and students of production technology will find the book very useful.
PrefaceForeword1. Introduction 1.1 Assembly 1.2 Status of Assembly in the Production Operation2. Product Design as a Requirement for Economic Assembly 2.1 Product Design 2.1.1 Base Part 2.1.2 Number of Parts 2.2 Assembly-Extended ABC Analysis 2.2.1 Fundamental Question 1: Price of Individual Parts and their Manufacturing Costs 2.2.2 Fundamental Question 2: Supply Condition 2.2.3 Fundamental Question 3: Ease of Handling 2.2.4 Fundamental Question 4: Assembly Direction and Ease of Assembly 2.2.5 Fundamental Question 5: Assembly Methods 2.2.6 Fundamental Question 6: Quality 2.2.7 Fundamental Question 7: Assembly Costs 2.2.8 Organizational Implementation of the Assembly-Extended ABC Analysis3. Manual Assembly 3.1 Introduction 3.2 Principles of Work-Point Arrangement 3.3 Organizational Forms of Manual Assembly 3.3.1 Single-Point Assembly 3.3.2 Line Assembly4. Primary-Secondary Analysis - An Aid for the Determination of the Economic Efficiency of Assembly Concepts 4.1 Introduction 4.2 Definition of the Efficiency of Assembly Operations 4.3 Field of Application 4.3.1 Basic Analysis 4.3.2 Fine Analysis of Single Assembly Work Points in Terms of Primary and Secondary Processes 4.4 Application Example of Assembly Analysis by Primary and Secondary Activity 4.4.1 Single Assembly Work Point with Provision of Parts in Manual Parts Dispensers 4.4.2 Single Assembly Work Point with Parts Provision by a Parts Paternoster 4.4.3 Single Assembly Work Point, Parts Provision Partly by Manual Parts Dispensers and Partly by Vibratory Spiral Conveyors 4.4.4 Linking of Three Single Assembly Work Points to Form a Line Assembly with Manual Transfer of the Assembled Part 4.4.5 Linking of Three Single Assembly Work Points to Form a Line Assembly with Mechanical Transfer of the Assembled Part in Workpiece Carriers 4.4.6 Summary and Efficiency Consideration 4.4.7 Primary-Secondary Fine Analysis for the Handling and Assembly of a Single Part 4.5 Extended Analysis in Terms of Primary and Secondary Requirements for the Total Sequence of an Assembly Operation 4.6 Practical Examples 4.6.1 Example 1: Switch Assembly 4.6.2 Example 2: Switch Element 4.6.3 Example 3: Headlight Assembly5. Modules for the Automation of Assembly Processes 5.1 Introduction 5.1.1 Handling 5.2 Feeder Units 5.2.1 Feeder Units for Parts with One Arrangement Feature 5.2.2 Feeder Units for Parts with Several Arrangement Criteria 5.2.3 Electronic Position Identification of Parts 5.2.4 The Feed of Interlocking Parts 5.3 Handling Equipment 5.3.1 Positioning Units 5.3.2 Industrial Robots 5.4 Transfer Equipment 5.4.1 Cycled Transfer Equipment 5.4.2 Non-Cycled Transfer Equipment 5.5 Screw-Inserting Units 5.6 Riveting Units 5.6.1 Press-Riveting 5.6.2 Rotating-Mandrel Riveting 5.7 Welding Units 5.7.1 Resistance Welding 5.7.2 Laser Welding Equipment 5.8 Soldering Equipment 5.9 Bonding6. Design of Assembly Machines 6.1 Introduction 6.2 Single-Station Assembly Machines 6.3 Multi-Station Assembly Machines 6.3.1 Design of Parts Feed Stations 6.3.2 Checking Stations 6.3.3 Design of Pneumatically Operated Multi-Station Assembly Machines 6.3.4 Design of Electric-Motor Driven Multi-Station Assembly Machines 6.3.5 Assembly Machine Systems 6.4 Combining Assembly Machines to Form Assembly Lines 6.5 Integration of Manual Work Points in Automated Assembly Lines 6.5.1 Manual Work Points for Parts Provision 6.5.2 Manual Assembly Work Points 6.6 Uncycled Assembly Lines Including Manual Work Points 6.7 Availability of Assembly Systems 6.7.1 Parameters of the Operational Characteristic 6.7.2 Utilization 6.7.3 Factors of Influence on the Availability of Assembly Systems 6.7.4 Summary7. Design of Flexible-Assembly Systems 7.1 Introduction 7.2 Primary-Secondary Fine Analysis with the Application of Assembly Robots 7.2.1 Reaching 7.2.2 Gripping 7.2.3 Collecting 7.2.4 Assembly 7.2.5 Release 7.3 Working Space 7.4 Gripper 7.5 The Design of Flexible Single-Station Assembly Cells 7.5.1 Semi-Automatic Flexible-Assembly Cells 7.5.2 Automatic Flexible-Assembly Cells 7.6 Assembly Lines with Flexible-Assembly Cells, Interconnected by Manual Work Points 7.6.1 Solution Examples 7.6.2 Summary8. Stored Program Controllers [46] 8.1 Introduction 8.2 Design of Stored Program Controllers 8.2.1 Input Modules 8.2.2 Signal Processing Modules 8.2.3 Output Modules 8.2.4 Network Modules 8.2.5 Program 8.3 Programming Equipment 8.4 Modules 8.5 Operating System 8.6 Programming of SPCs 8.7 Ease of Maintenance 8.8 Availability 8.9 Data Exchange9. Practical Examples 9.1 Assembly Machines 9.1.1 Example 1: Rocker 9.1.2 Example 2: Valve Plate 9.1.3 Example 3: Spray Nozzle-Spray Head 9.1.4 Example 4: Terminal Block 9.1.5 Example 5: High-Pressure Nozzle 9.1.6 Example 6: Audio Cassettes 9.1.7 Example 7: Car Fan Motor 9.2 Flexible-Assembly Systems 9.2.1 Example 1: Switch Block 9.2.2 Example 2: Assembly of Clips on Car Headlights 9.2.3 Example 3: Domestic Appliance Drive 9.2.4 Example 4: Equipping of Printed Circuit Boards 9.2.5 Example 5: Auxiliary Contact Block10. The Integration of Parts Manufacturing Processes into Assembly Equipment of Assembly Operations into Parts Production Equipment 10.1 Introduction 10.2 Integrated Parts Production 10.3 The Production Machining of Parts in Assembly Equipment 10.4 Practical Example: Assembly System with Integrated Parts Production 10.5 The Integration of Assembly Processes into Parts Production Processes 10.6 The Integration of Parts Production into Assembly Equipment within the Concept of Just-in-Time Production 10.7 Limits for the Integration of Production Processes11. Planning and Efficiency of Automated Assembly Systems 11.1 Introduction 11.2 Requirement List 11.3 Product Analysis 11.4 Assembly Sequence Analysis 11.4.1 Product Design and Assembly Situation 11.4.2 Assembly Sequence 11.5 Workpiece Carrier Design 11.5.1 Introduction 11.5.2 Design Examples of Workpiece Carriers 11.6 Function Analysis 11.7 Determination of Cycle Time 11.8 Layout Planning 11.8.1 Principles of Layout Planning 11.8.2 Layout Examples 11.9 Determination of Personnel Requirement 11.10 Determination of Availability 11.10.1 Parts Quality 11.10.2 Number of Stations 11.10.3 Availability of Individual Stations 11.10.4 System Structure 11.10.5 Initial Operation Characteristics 11.10.6 Personnel Qualifications 11.11 Assembly Systems 11.11.1 Cycle Time 11.11.2 System Structure - Integration of Necessary Manual Operations 11.11.3 Conditions on the Periphery of Automatic Assembly 11.11.4 Summary 11.12 Investment Calculations 11.13 Evaluation And Selection 11.13.1 Machine Hourly Rate 11.13.2 Personnel-Related Costs 11.13.3 Work-Point Cost Calculation 11.14 Optimized Overall Solution 11.15 Computer-Aided Planning of Automated Assembly Systems 11.15.1 CAD Layout Planning 11.15.2 Simulation Technique12. Practical Example: Planning and Realization of an Automated Assembly System 12.1 Introduction 12.2 Planning Procedure 12.2.1 Requirement List 12.2.2 Product Analysis 12.2.3 Assembly Sequence Analysis 12.2.4 Function Analysis 12.2.5 Determination of Cycle Time 12.2.6 Layout Planning 12.2.7 Determination of Personnel Requirement 12.2.8 Determination of Availability 12.3 Detailed Planning of Assembly System 12.3.1 Introduction 12.3.2 Machine I 12.3.3 Machine II 12.3.4 Machine III 12.3.5 Machine IV 12.3.6 Machine V 12.3.7 Machine VI 12.3.8 Machine VII 12.3.9 Machine VIII 12.3.10 Machine IX 12.4 Investment Calculations 12.5 Evaluation and Selection/Work Point Cost Comparison 12.6 Investment Risks13. The Operation of Automated Assembly Systems 13.1 Prerequisites for Initial Running 13.1.1 Parts Quality 13.1.2 Functional Reliability of the System 13.1.3 Practical Example of Fault Time Determination by MANALYS on an Automatic Assembly System 13.2 Payment 13.3 Maintenance 13.4 Work Safety14. Outlook15. References16. Index
- Edition: 1
- Published: November 13, 2013
- Imprint: Butterworth-Heinemann
- Language: English
Read Manufacturing Assembly Handbook on ScienceDirect