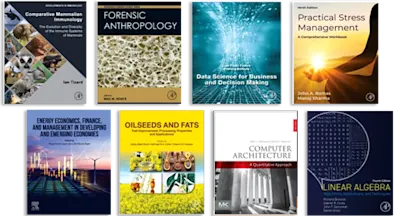
Manual of Engineering Drawing
Technical Product Specification and Documentation to British and International Standards
- 4th Edition - June 29, 2012
- Imprint: Butterworth-Heinemann
- Authors: Colin H. Simmons, Dennis E. Maguire
- Language: English
- Paperback ISBN:9 7 8 - 0 - 0 8 - 0 9 6 6 5 2 - 6
- eBook ISBN:9 7 8 - 0 - 0 8 - 0 9 6 6 5 3 - 3
Manual of Engineering Drawing is a comprehensive guide for experts and novices for producing engineering drawings and annotated 3D models that meet the recent BSI and ISO standa… Read more
Purchase options
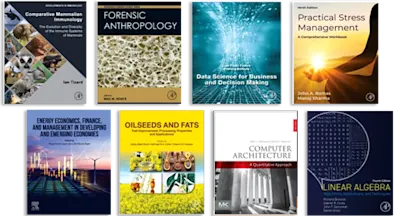
- Expert interpretation of the rules and conventions provided by authoritative authors who regularly lead and contribute to BSI and ISO committees on product standards
- Combines the latest technical information with clear, readable explanations, numerous diagrams and traditional geometrical construction techniques
- Includes new material on patents, copyrights and intellectual property, design for manufacture and end-of-life, and surface finishing considerations
Chapter 1. Drawing Office Management and Organization
Engineering Drawing Practices
Drawing Practice and the Computer (CAD: Computer Aided Draughting and Design)
Why Introduce BS 8888 and Withdraw BS 308?
Chapter 2. Product Development and Computer Aided Design
Computer Aided Draughting and Design
Technical Product Documentation
Access into the Computer Network
Quality Assurance
Chapter 3. Design for Manufacture to End of Life
Chapter 4. Intellectual Property and Engineering Design
Patents
Designs
Trademarks
Important Points to Remember
Chapter 5. CAD Organization and Applications
Computer and Software Purchase
Project Development
Size of Computer
Parametric Design
Sheet Metalwork Application
Pipework Systems
Communicating Design Concepts
Materials Options
Typical CAD Drawings and 3D Models
Chapter 6. Principles of First and Third Angle Orthographic Projection
First Angle Projection
Third Angle Projection
Projection Symbols
Drawing Procedure
Reading Engineering Drawings
Projection Exercises
Chapter 7. Linework and Lettering
Drawing Paper Sizes
Presentation
Types of Line and Their Application
Chain Lines
Coinciding Lines
Lettering
Minimum Character Height for Capital Letters and Numerals
Drawing Modifications
Care and Storage of Original Drawings
Chapter 8. Three-dimensional Illustrations Using Isometric and Oblique Projection
Isometric Projection
Oblique Projection
Chapter 9. Drawing Layouts and Simplified Methods
Single-part Drawing
Collective Single-part Drawings
Assembly Drawings
Collective Assembly Drawing
Design Layout Drawings
Combined Detail and Assembly Drawings
Exploded Assembly Drawings
Simplified Drawings
Machine Drawings
Drawing Scales
Scale Used in Geometric Construction
Abbreviations
Chapter 10. Sections and Sectional Views
Half Sections
Revolved Sections
Removed Sections
Sections through Thin Material
Local Sections
Components Not Drawn in Section
Successive Sections
Sections in Two Parallel Planes
Chapter 11. Geometrical Constructions and Tangency
To Bisect a Given Angle AOB (Fig. 11.1)
To Bisect a Given Straight Line AB (Fig. 11.2)
To Bisect a Given Arc AB (Fig. 11.3)
To Find the Centre of a Given Arc AB (Fig. 11.4)
To Inscribe a Circle in a Given Triangle ABC (Fig. 11.5)
To Circumscribe a Circle Around Triangle ABC (Fig. 11.6)
To Draw a Hexagon, Given the Distance Across the Corners
To Draw a Hexagon, Given the Distance Across the Flats (Fig. 11.8)
To Draw a Regular Octagon, Given the Distance Across Corners (Fig. 11.9)
To Draw a Regular Octagon, Given the Distance Across the Flats (Fig. 11.10)
To Draw a Regular Polygon, Given the Length of the Sides (Fig. 11.11)
Tangency
To Draw a Tangent to a Point A on the Circumference of a Circle, Centre O (Fig. 11.13)
To Draw a Tangent to a Circle From Any Given Point A Outside the Circle (Fig. 11.14)
To Draw an External Tangent to Two Circles (Fig. 11.15)
To Draw an Internal Tangent to Two Circles (Fig. 11.16)
To Draw Internal and External Tangents to Two Circles of Equal Diameter (Fig. 11.17)
To Draw a Curve of Given Radius to Touch Two Circles when the Circles Are Outside the Radius (Fig. 11.18)
To Draw a Curve of Given Radius to Touch Two Circles When the Circles Are Inside the Radius (Fig. 11.19)
To Draw a Radius to Join a Straight Line and a Given Circle (Fig. 11.20)
To Draw a Radius Which is Tangential to Given Straight Lines (Fig. 11.21)
Chapter 12. Loci Applications
Methods of Drawing an Ellipse
The Involute
Archimedean Spiral
Right-hand Cylindrical Helix
Right-hand Conical Helix
The Cycloid
The Epicycloid
The Hypocycloid
Chapter 13. True Lengths and Auxiliary Views
Chapter 14. Conic Sections and Interpenetration of Solids
To Draw an Ellipse from Part of a Cone
To Draw a Parabola from Part of a Cone
To Draw a Rectangular Hyperbola from Part of a Cone
Interpenetration
Chapter 15. Development of Patterns from Sheet Materials
Chapter 16. Dimensioning Principles
Dimensioning of Features not Drawn to Scale
Chain Dimensioning and Auxiliary Dimensioning
Parallel Dimensioning
Running Dimensioning
Staggered Dimensions
Dimensioning Circles
Dimensioning Radii
Dimensioning Spherical Radii and Diameters
Dimensioning Curves
Dimensioning Irregular Curves
Unidirectional and Aligned Dimensions
Angular Dimensions
Tapers
Dimensioning Tapers
Dimensioning Two Mating Tapers
Dimensioning Chamfers
Dimensioning Squares or Flats
Dimensioning Holes
Dimensioning Counterbores
Dimensioning Countersunk Holes
Dimensioning Spotfaces
Dimensioning for Manufacture
Chapter 17. Screw Threads and Conventional Representations
Screw Threads
ISO Metric Threads
Unified Threads
Threads for Power Transmission
Draughting Conventions Associated with Threads
Multiple Threads
The Application of Thread Conventions
Tapping Drill
Clearance Drill
Chapter 18. Nuts, Bolts, Screws, and Washers
Drawing Nuts and Bolts
Approximate Construction for Nuts and Bolts (Figs 18.2 and 18.3)
Socket Head Screws Manufactured to BS EN ISO 4762 and BS 3643-2
ISO Metric Socket Cap Screws (Dimensions in Table 18.2)
ISO Metric Hexagon Socket Shoulder Screws (Dimensions in Table 18.3)
ISO Metric Hexagon Socket Button Head Screws (Dimensions in Table 18.4)
ISO Metric Socket Countersunk Head Screws (Dimensions in Table 18.5)
ISO Metric Hexagon Socket Set Screws (Dimensions in Table 18.6)
Machine Screws
‘Posidriv’ Machine Screws, Countersunk and Raised Countersunk Head (Dimensions in Table 18.7)
‘Posidriv’ Machine Screws, Pan Head (Dimensions in Table 18.8)
Slotted Machine Screws, Countersunk and Raised Countersunk Head (Dimensions in Table 18.9)
Slotted Machine Screws, Pan Head (Dimensions in Table 18.10)
Slotted Machine Screws, Cheese Head (Dimensions in Table 18.11)
Machine Screw Nuts
Wing Nuts
Locking and Retaining Devices
Slotted Nuts and Castle Nuts
Simmonds Locknut
Spring Washers
Shakeproof Washers
Wire Locking
Tab Washers
Locking Plates
Taper Pins and Parallel Pins
Split Cotter Pins
Locking by Adhesives
Peening
Thread-cutting Screws
Chapter 19. Keys and Key Ways
Sunk Keys
Woodruff Keys
Dimensioning Keyways (Parallel Keys)
Chapter 20. Worked Examples in Machine Drawing
Bushed Bearing Bracket
Drill Table
Cam Operated Clamp
Plug Cock
Air Engine
Toolbox
Solution Notes
Chapter 21. Limits and Fits
Elements of Interchangeable Systems (Fig. 21.9)
Unilateral and Bilateral Limits
Bases of Fits
Selected ISO Fits – Hole Basis (Extracted from BS 4500)
Interpretations of Limits of Size in Relation to Form
Chapter 22. Geometrical Tolerancing and Datums
Geometrical Tolerances
Applications
Advantages
General Rules
Theoretically Exact Dimensions (TEDs)
Definitions
Method of Indicating Geometrical Tolerances on Drawings
Methods of Applying the Tolerance Frame to the Toleranced Feature
Procedure for Positioning Remarks which are Related to Tolerance
The Application of Tolerances to a Restricted Length of a Feature
Tolerance Zones
Projected Toleranced Zone
Datums and Datum Systems
Datums
Methods of Specifying Datum Features
Datum Systems
Common Datums
Datum Targets
Dimensioning and Tolerancing Non-rigid Parts
Chapter 23. Application of Geometrical Tolerances
Straightness
Flatness
Circularity (Roundness)
Cylindricity
Profile Tolerance of a Line
Profile Tolerance of a Surface
Parallelism
Perpendicularity (Squareness)
Angularity
Circular Run-out
Total Run-out
Position
Concentricity and Coaxiality
Symmetry
Chapter 24. Maximum Material and Least Material Principles
Maximum Material Condition (MMC)
Least Material Condition (LMC)
Maximum Material Condition Related to Geometrical Form
Maximum Material Condition Applied to Straightness
Maximum Material Condition Applied to Squareness
Maximum Material Condition Applied to Position
Maximum Material Condition Applied to Coaxiality
Maximum Material Condition and Perfect Form
The Application of Maximum Material Condition and its Relationship with Perfect Form and Squareness
The Application of Maximum Material Condition and its Relationship with Perfect Form and Coaxiality
The Application of Maximum Material Condition to Two Mating Components
Chapter 25. Positional Tolerancing
Theoretically Exact Dimensioning (TED) (True-position)
Typical Product Requirement
Chapter 26. Surface Texture
Graphical Symbols to Indicate Surface Texture
Expanded Graphical Symbols
Complete Graphical Symbols
‘All Surfaces Around a Workpiece’ Graphical Symbol
Composition of Complete Graphical Symbols for Surface Texture
Mandatory Positions for Complementary Requirements
Chapter 27. Surface Finish and Corrosion of Metals
Surface Finish
Corrosion of Metals
Design Considerations to Minimize the Effects of Corrosion
Chapter 28. 3D Annotation
Axis or Median Feature
Projected Tolerance Zone
Indicating a Tolerance Zone Between Two Points
Unilateral and Unequal Profile Tolerance
Indicating the Direction of Tolerance Zones
Chapter 29. The Duality Principle – the Essential Link Between the Design Intent and the Verification of the End Product
Introduction
Design Specification and Verification
Advantages of the Duality Principle
Chapter 30. Differences between American ASME Y 14.5M Geometric Dimensioning and Tolerancing (GD&T) and ISO/BS 8888 Geometrical Tolerancing Standards
Applicability of Standards
Symbology
Specification of Datums
Exclusion of Surface Texture
Tolerancing Principle
Features of Size
Chapter 31. Cams and Gears
Cam Followers
Cam Follower Motions
Case 1 (Fig. 31.6)
Case 2 (Fig. 31.7)
Case 3 (Fig. 31.8)
Case 4 (Fig. 31.9)
Case 5 (Fig. 31.10)
Case 6 (Fig. 31.11)
Dimensioning Cams
Spur Gears
Spur-gear Terms (Fig. 31.15)
Involute Gear Teeth Proportions and Relationships
Typical Example Using Professor Unwin's Approximate Construction
Helical Gears
Bevel Gears
Worm Gearing
Chapter 32. Springs
Plain-carbon Steels
Alloy Steels
Stainless Steels
High-nickel Alloys
Copper-base Alloys
Compression Springs
Flat Springs
Torsion Springs
Leaf Springs
Helical Extension Springs
Disc Springs
Spring Specifications
Wire Forms
Corrosion Prevention
Fatigue Conditions
Chapter 33. Welding and Welding Symbols
The Indication and Application of Welding Symbols on Drawings
Dimensioning of Welds
Chapter 34. Engineering Diagrams
General Engineering Graphical Symbols
Engineered Systems
Heating, Ventilation and Air Conditioning Systems
Refrigeration Systems and Energy-saving Applications
Pneumatic Systems
Pneumatics and Electronics
Chapter 35. Bearings and Applied Technology
Plain Bearings
Ball and Roller Bearings
Chapter 36. Engineering Adhesives
Designing for Adhesives
The Bond Line
Typical Bonded Joints
Engineering Applications
Instant Adhesives
Structural Applications
Chapter 37. Related Standards
The British Standards Institution
BSI Knowledge Centre
Technical Information Group
Foreign Standards and Translations
PLUS – Private List Updating Service
Perinorm
DISC
British Standards Online and CD-ROM
The Standards-making Process
International Organization for Standardization (ISO)
Chapter 38. Production Drawings
Further Standards for Design, Project and Risk Management of Interest to Engineers and Manufacturers
Chapter 39. Drawing Solutions
- Edition: 4
- Published: June 29, 2012
- Imprint: Butterworth-Heinemann
- Language: English
CS
Colin H. Simmons
DM