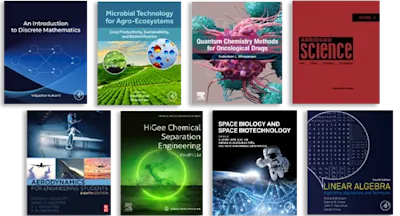
Making Common Sense Common Practice
Models for Manufacturing Excellence
- 3rd Edition - May 7, 2004
- Author: Ron Moore
- Language: English
- Paperback ISBN:9 7 8 - 0 - 7 5 0 6 - 7 8 2 1 - 6
- eBook ISBN:9 7 8 - 0 - 0 8 - 0 4 9 1 7 3 - 8
Presenting the best practices of the best manufacturing companies in the world, this book presents proven models for achieving world-class performance. Using a case study of a… Read more
Purchase options
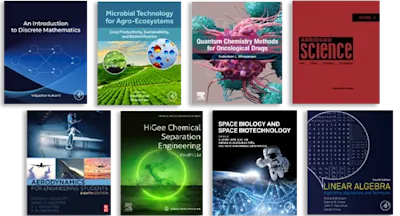
- Third edition features updating plus new sections on innovation, change management, and leadership
- Presents proven models for achieving world-class performance based on real-life case histories
- Highly readable, concrete style brings the key points to life through a case study of a fictitious organization, Beta International, which runs throughout the book, based on real case histories
Chapter 1 The Scene1. The Players 3. Integrating the Manufacturing and Marketing Strategy 5. Becoming the Low-Cost Producer 8. Application of Increased Capacity 11. Beta’s Beaver Creek Plant—RoNA vs. Uptime 13. A Model for Becoming the Low-Cost Producer 13. Measuring Losses from Ideal 17. Sample Calculation of Batch Plant OEE 23. Discussion of Sample Measurement 28. A Special Case—Beta’s Dwale Plant 29. Hiding Behind Excess Capacity (The Hidden Plant) 30. Differences Between Batch and Continuous Manufacturers 33. Lean Manufacturing, Six Sigma, and Focused Factories 34. Summary 39. References 40.
Chapter 2 Benchmarks, Bottlenecks, and Best Practices Benchmarking—Finding Benchmarks and Best Performers 43. Making the Comparison 46. Bottlenecks—A Dynamic View 54. Manufacturing Uptime Improvement Model 58. References 65.
Chapter 3Aligning the Marketing and Manufacturing StrategiesBeta’s Pracor Division 68. Market/Product Success Factors 69. Volume and Market Growth Analysis 72. Manufacturing Capability for Supporting Market/Volume Goals 73. Performance by Plant and by Product Line 74. The Plan 77. Revised Pricing Strategy 78. Plant Performance Requirements 79. Other Actions Required 80. The Expected Results 81. Effect of Product Mix on Manufacturing Performance 85. Beta’s Leets Division—Rationalizing Customers and Markets 91. Summary 94. References 95.
Chapter 4 Plant Design and Capital Project Practices 96 The Design Process 99. Design Objectives 100. Key Questions 101. Operations and Maintenance Input 105.Estimating Life-Cycle Costs 107. Additional Case Histories 108. Payback Analysis—Too Simple and TooExpensive—Payback Is Hell! 110. Summary 114. References 114.
Chapter 5 Procurement Practices 115 A Model for Developing Strategic Alliances—Goose Creek Plant 117. Supplier Selection 120. Process for Improved Specifications for Equipment Reliability—Mossy Bottom Plant 122. Improving Supplier Reliability—A Case Study 131. Supply Chain Principles—A Strategic Approach 134. References 137.
Chapter 6 Stores/Parts Management Practices 138 What Are Stores? 139. The “Cost” of Stores 140. What Stores Are Needed—Kind and Quantity 140. Standardization 143. The Store 144. Contracting the Stores Function 147. Key Performance Indicators 148. Beta’s Wheelwright Plant 150. Spare Parts Criticality Ranking Model 155. Summary 157. References 158.
Chapter 7 Installation Practices 159 Follow Existing Standards and Procedures 161. Verify and Use Appropriate Manufacturer Recommendations 161. Installation and Commissioning of Rotating Machinery 162. Flange and Joint Installation 164. Workshop Support 164. Housekeeping 165. Use of the Pre-Destruction Authorization 165. Summary 166. References 167.
Chapter 8 Operational Practices 168 Improving Operating Practices to Reduce Maintenance Costs 169. Consistency of Process Control 172. Control Loops 173. Process Conformance for Operational Excellence 175. Operator Basic Care 179. Establishing Operator Care/Ownership 180. Shift Handover Process 181. Production Planning 182. Advanced Process Control Methods 183. Summary 184. References 187.
Chapter 9 Maintenance Practices 189 Going from Reactive to Proactive 189. Beta’s Repair Culture 195. Maintenance Practices 196. Preventive Maintenance 202. Predictive Maintenance 204. Beta’s Current Predictive Maintenance Practices 208. Beta’s Predictive Maintenance Deployment Plan 209. Proactive Maintenance 210. Focused Factories and Maintenance Practices: Centralized vs. Decentralized Maintenance 216. The Need for Integrating Preventive, Predictive, and Proactive Practices 219. Life Extension Program 222. Maintenance Practices and Safety Performance 223. Summary 224. References 226.
Chapter 10 Optimizing the Preventive Maintenance Process 229 First Things First 230. Creating Equipment Histories from “Scratch” 231. The Model 232. Some Examples 234. Case Histories 235. Mechanical Integrity 237. Summary 238. References 238.
Chapter 11 Implementing a Computerized Maintenance Management System 239 Case History 242. Reference 248.
Chapter 12 Effective Use of Contractors in a Manufacturing Plant 249 The Reliability Improvement Program 249. Consolidating Maintenance Contractors 251. What Happened? 257. Lessons Learned 261. Best Use of Contractors 263. Summary 268. References 269.
Chapter 13 Total Productive and Reliability-Centered Maintenance 270 Total Productive Maintenance Principles—TPM 271. Reliability-Centered Maintenance Principles—RCM 275. Case Study 278. Some Additional Benefits 283. Summary 284. References 286.
Chapter 14 Implementation of Reliability Processes 287 Whamadyne’s Journey to Manufacturing Excellence 292. Whamadyne’s Reliability Improvement Plan 296. Results— World-Class Performance 302. References 304.
Chapter 15 Leadership and Organizational Behavior & Structure 305 Leadership 305. Organizational Issues 309. Empowerment 309.Empowerment as a Disabler 311. The Reliability Process—A Better Way 315. Reliability Improvement Teams 317.Organizational Structure 324. Mission Statements 328. Communication of Performance Expectations 329. Implementing Reliability and Manufacturing Excellence in a Union or Non-Union Plant 330. Compensation 331. Summary 332. References 333.
Chapter 16 Training 334 The Strategic Training Plan 336. Boss as Trainer 337. Training Versus Learning 338. Training for Pay 339. Training in Appropriate Methodologies 340. Multi-skilling and Cross-functional Training 341. Intellectual Capital 342. Closing 344. References 345.
Chapter 17 Performance Measurement 346 Return on Net Assets or Return on Replacement Value 355. Plant Age and Reliability 355. Measure for Weaknesses 355. References 356. Chapter 18 Epilogue 357 Beta’s 10-Point Plan 358. Appendix A World-Class Manufacturing: A Review of Several Key Success Factors 364 Appendix B Reliability Manager/Engineer Job Description 375
- Edition: 3
- Published: May 7, 2004
- Language: English
RM