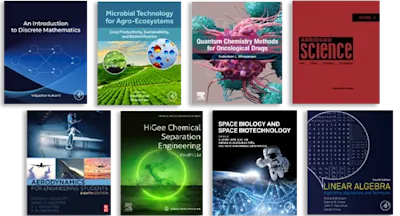
Machining Principles for Shape Generation of Metals
- 1st Edition - August 28, 2024
- Imprint: Elsevier
- Author: Yuji Furukawa
- Language: English
- Paperback ISBN:9 7 8 - 0 - 4 4 3 - 2 3 5 3 8 - 2
- eBook ISBN:9 7 8 - 0 - 4 4 3 - 2 3 5 3 9 - 9
Machining Principles for Shape Generation of Metals explains the basics of machining techniques and metal cutting, as well as the Laplace transform and how it can be applied to… Read more
Purchase options
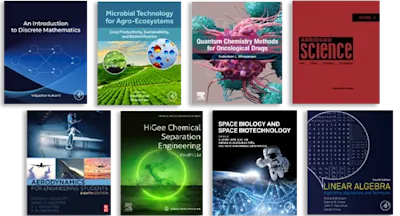
Machining Principles for Shape Generation of Metals explains the basics of machining techniques and metal cutting, as well as the Laplace transform and how it can be applied to understand complex machining processes. The book provides an overview of all machining processes from a geometric perspective, with an emphasis on producing superior parts. Mechanics, vibration control, processing mechanics, thermal deformation, and numerical control principles for metal cutting are each reviewed, with details on the principle of cutting away, forced and self-excited vibration, and the physical properties of workpiece and tool materials. Common questions and answers are provided throughout the book to reinforce learning of key concepts.
- Provides solutions to problems encountered when cutting metals
- Emphasizes the application of the Laplace transform and provides closed-loop diagrams of machining systems
- Explains the principles of creating planes, pseudo-cylinders, and pseudo-circular holes
Researchers, professional engineers, machinists, and graduate students working on the development of machine tools, cutting tools, factory planning, Advanced undergraduate students
SECTION I Shape generation principle
1. Virtual principles of geometry and creation principles of physics
2. Creation principle of planes
3. Principle of creation of objects with constant diameter
4. Cylindrical shape (pseudo-cylinder) creation principle
5. Principle of creating a circular hole
6. Generation principle of an involute tooth profile
SECTION II Principle of shape creation by removal processing
7. Principle of physical characteristics of work material
8. Principles of physical properties of tool materials
9. Machine tool motion and surface creation principle
10. Removal principle of cutting
11. Principle of cutting residue
SECTION III Disturbances to the created shape and the principle of countermeasures
12. Principle of forced vibration
13. Generation mechanism of primary self-excited chatter vibrations and their countermeasures
14. Generation principle of self-excited chatter vibration by workpiece-waviness regenerative effect
15. Thermal deformation principle of processing systems
SECTION IV Current state of Numerical Control and future manufacturing system
16. Numerical Control principle of processing machines
17. Configuration principle of processing system (cell to FMS)
18. Science, technology and engineering of manufacturing
1. Virtual principles of geometry and creation principles of physics
2. Creation principle of planes
3. Principle of creation of objects with constant diameter
4. Cylindrical shape (pseudo-cylinder) creation principle
5. Principle of creating a circular hole
6. Generation principle of an involute tooth profile
SECTION II Principle of shape creation by removal processing
7. Principle of physical characteristics of work material
8. Principles of physical properties of tool materials
9. Machine tool motion and surface creation principle
10. Removal principle of cutting
11. Principle of cutting residue
SECTION III Disturbances to the created shape and the principle of countermeasures
12. Principle of forced vibration
13. Generation mechanism of primary self-excited chatter vibrations and their countermeasures
14. Generation principle of self-excited chatter vibration by workpiece-waviness regenerative effect
15. Thermal deformation principle of processing systems
SECTION IV Current state of Numerical Control and future manufacturing system
16. Numerical Control principle of processing machines
17. Configuration principle of processing system (cell to FMS)
18. Science, technology and engineering of manufacturing
- Edition: 1
- Published: August 28, 2024
- Imprint: Elsevier
- Language: English
YF
Yuji Furukawa
Yuji Furukawa is Professor Emeritus, Polytechnic University of Japan, and Professor Emeritus, Tokyo University of Agriculture and Technology. He most recently held positions of President of Myanmar Vocational Technical College, Visiting Professor of Tianjin University of Technology and Education, and Visiting Professor of Shanghai Jiao Tong University. He is currently an Emeritus Member of the Japan Society for Precision Engineering; Japan Society for Abrasive Technology; and Council of International Research Production (CIRP).
Affiliations and expertise
Professor Emeritus, Polytechnic University of Japan, Tokyo, Japan.Professor Emeritus, Tokyo University of Agriculture and Technology, JapanRead Machining Principles for Shape Generation of Metals on ScienceDirect