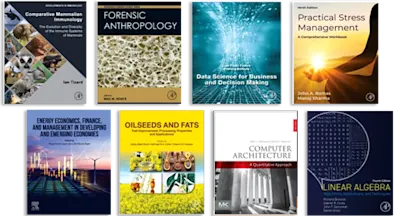
Ludwig's Applied Process Design for Chemical and Petrochemical Plants Incorporating Process Safety Incidents
Volume 1B
- 5th Edition - July 11, 2024
- Imprint: Elsevier Science
- Author: A. Kayode Coker
- Language: English
- Hardback ISBN:9 7 8 - 0 - 4 4 3 - 3 0 1 1 4 - 8
- eBook ISBN:9 7 8 - 0 - 4 4 3 - 3 0 1 1 5 - 5
Ludwig’s Applied Process Design for Chemical and Petrochemical Plants Incorporating Process Safety Incidents is ever evolving starting with the first edition some 60 years ago. T… Read more
Purchase options
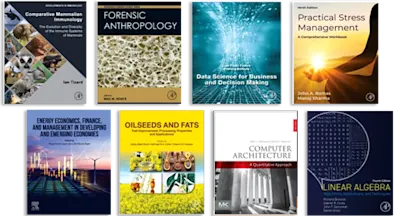
Ludwig’s Applied Process Design for Chemical and Petrochemical Plants Incorporating Process Safety Incidents is ever evolving starting with the first edition some 60 years ago. The volumes in this fifth edition provide improved techniques and fundamental design methodologies to guide the practicing engineer in designing process equipment and applying chemical processes to the properly detailed hardware. As indicative of the new title, process safety incidents are incorporated in many of the chapters, reviewing the root causes, and how these could be mitigated in future. Like its predecessor, this new edition continues to present updated information for achieving optimum operational and process conditions and to avoid problems caused by inadequate sizing and lack of internally detailed hardware. The volumes provide both fundamental theories where applicable and direct application of these theories to applied equations essential in the design effort. This approach in presenting design information is essential for troubleshooting process equipment and in executing system performance analysis. Volume 1B continues to cover mixing of liquids, process safety and pressure[1]relieving devices, metallurgy and corrosion, and process optimization. It builds upon Ernest E. Ludwig’s classic text to further enhance its use as a chemical engineering process design manual of methods and proven fundamentals. This new edition includes new content on three-phase separation, mixing of liquids, ejectors, and mechanical vacuum systems, process safety and pressure-relieving devices, metallurgy and corrosion, and optimization of chemical process/blending. Some chapters review pressure-relieving devices and provide case studies for process safety incidents, which are well illustrated from US Chemical Safety Hazard Investigation Board (www.csb.gov). Finally, this book contains a glossary of Petroleum and Petrochemical Terminologies and Physical and Chemical Characteristics of Major Hydrocarbons.
- Provides improved design manual for methods and proven fundamentals of process design with related data and charts
- Covers complete range of basic day-to-day petrochemical operation topics
- Extensively revised with new material added on three-phase separation, metallurgy, and corrosion
- Process safety management/HAZOP and hazard analyses, and optimization of chemical process/blending
- Presents many examples using Honeywell UniSim Design software, developed and executable computer programs, and Excel spreadsheet programs
- Includes case studies of process safety incidents, guidance for troubleshooting, and checklists
- Includes Software of Conversion Table and 30+ process data sheets in excel format
Chemical Engineers, Engineering Students/graduates, Professionals and Technologists
1. Mixing of liquids
2. Ejectors and mechanical vacuum systems
3. Process safety and pressure-relieving devices
4. Metallurgy and Corrosion
5. Process Safety Management/HAZOP and Hazard Analyses
6. Optimization of Chemical Process/Blending
2. Ejectors and mechanical vacuum systems
3. Process safety and pressure-relieving devices
4. Metallurgy and Corrosion
5. Process Safety Management/HAZOP and Hazard Analyses
6. Optimization of Chemical Process/Blending
- Edition: 5
- Published: July 11, 2024
- Imprint: Elsevier Science
- Language: English
AC
A. Kayode Coker
A. Kayode Coker PhD, is Engineering Consultant for AKC Technology, an Honorary Research Fellow at the University of Wolverhampton, U.K., a former Engineering Coordinator at Saudi Aramco Shell Refinery Company (SASREF) and Chairman of the department of Chemical Engineering Technology at Jubail Industrial College, Saudi Arabia. He has been a chartered chemical engineer for more than 30 years. He is a Fellow of the Institution of Chemical Engineers, UK (C. Eng., FIChemE), and a senior member of the American Institute of Chemical Engineers (AIChE). He holds a B.Sc. honors degree in Chemical Engineering, a Master of Science degree in Process Analysis and Development and Ph.D. in Chemical Engineering, all from Aston University, Birmingham, UK, and a Teacher’s Certificate in Education at the University of London, UK. He has directed and conducted short courses extremely throughout the world and has been a lecturer at the university level. His articles have been published in several international journals. He is an author of ten books in chemical and petroleum engineering, a contributor to the Encyclopedia of Chemical Processing and Design, Vol. 61, and a certified train – the mentor trainer. A Technical Report Assessor and Interviewer for chartered chemical engineers (IChemE) in the UK. He is a member of the International Biographical Centre in Cambridge, UK (IBC) as Leading Engineers of the World for 2008. Also, he is a member of International Who’s Who for ProfessionalsTM and Madison Who’s Who in the US.
Affiliations and expertise
Engineering Coordinator, Saudi Aramco Shell Refinery Company, Saudi ArabiaRead Ludwig's Applied Process Design for Chemical and Petrochemical Plants Incorporating Process Safety Incidents on ScienceDirect