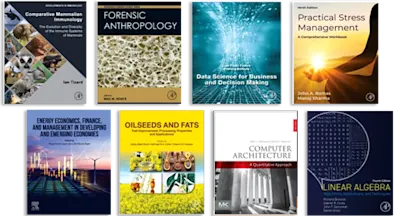
Lees' Loss Prevention in the Process Industries
Hazard Identification, Assessment and Control
- 4th Edition - August 3, 2012
- Imprint: Butterworth-Heinemann
- Author: Frank Lees
- Language: English
- Hardback ISBN:9 7 8 - 1 - 8 5 6 1 7 - 7 7 7 - 1
- Hardback ISBN:9 7 8 - 0 - 1 2 - 3 9 7 1 8 9 - 0
- eBook ISBN:9 7 8 - 0 - 0 8 - 0 9 6 2 3 1 - 3
- eBook ISBN:9 7 8 - 0 - 1 2 - 3 9 7 7 8 2 - 3
Safety in the process industries is critical for those who work with chemicals and hazardous substances or processes. The field of loss prevention is, and continues to be, of supr… Read more
Purchase options
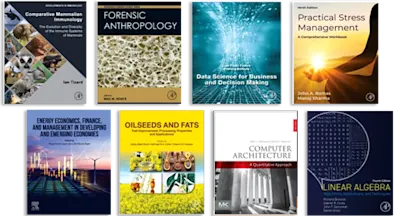
- The process safety encyclopedia, trusted worldwide for over 30 years
- Now available in print and online, to aid searchability and portability
- Over 3,600 print pages cover the full scope of process safety and loss prevention, compiling theory, practice, standards, legislation, case studies and lessons learned in one resource as opposed to multiple sources
Dedication
Preface to Fourth Edition
Preface to Third Edition
Preface to Second Edition
Preface to First Edition
Acknowledgements
Terminology
Notation
Use of References
List of Contributors
Volume 1
Chapter 1. Introduction
1.1 Management Leadership
1.2 Industrial Safety and Loss Trends
1.3 Safety and Environmental Concerns
1.4 Loss Prevention – 1
1.5 Large Single-Stream Plants
1.6 Loss Prevention – 2
1.7 Total Loss Control
1.8 Quality Assurance
1.9 Total Quality Management
1.10 Risk Management
1.11 Safety-Critical Systems
1.12 Environment and Sustainable Development
1.13 Responsible Care
1.14 Academic and Research Activities
1.15 Overview
Chapter 2. Incidents and Loss Statistics
2.1 The Incident Process
2.2 Standard Industrial Classification
2.3 Injury Statistics
2.4 Major Disasters
2.5 Major Process Hazards
2.6 Fire Loss Statistics
2.7 Fire and Explosion
2.8 Causes of Loss
2.9 Down-Time Losses
2.10 Trend of Injuries
2.11 Trend of Losses
2.12 Case Histories
Chapter 3. Legislation and Law
3.1 US Legislation
3.2 US Regulatory Agencies
3.3 Codes and Standards
3.4 Occupational Safety and Health Act 1970
3.5 US Environmental Legislation
3.6 US Toxic Substances Legislation
3.7 US Accidental Chemical Release Legislation
3.8 US Transport Legislation
3.9 US Security Legislation
3.10 US Developing Legislation
3.11 EU Legislations
3.12 Other Legislation
3.13 Regulatory Support
3.14 US Chemical Safety Board
Chapter 4. Major Hazard Control
Foreword by Jerry Havens
4.1 Superstar Technologies
4.2 Hazard Monitoring
4.3 Risk Issues
4.4 Risk Perception
4.5 Risk Management
4.6 Hazard Control Policy
4.7 Nuclear Hazard Control
4.8 Process Hazard Control: Background
4.9 Process Hazard Control: Advisory Committee on Major Hazards
4.10 Process Hazard Control: Major Hazards Arrangements
4.11 Process Hazard Control: Planning
4.12 Process Hazard Control: European Community
4.13 Process Hazard Control: USA
Chapter 5. Economics and Insurance
5.1 Economics of Loss Prevention
5.2 Cost of Losses
5.3 Cost of Prevention
5.4 Level of Loss Prevention Expenditure
5.5 Insurance of Process Plant
5.6 Property Insurance
5.7 Individual Insurance
5.8 Business Interruption Insurance
5.9 Other Insurance Aspects
5.10 Notation
Chapter 6. Management and Management Systems
6.1 Management Attitude
6.2 Management Commitment and Leadership
6.3 Management Organization
6.4 Competent People
6.5 Systems and Procedures
6.6 Project Safety Reviews
6.7 Management of Change
6.8 Standards and Codes of Practice
6.9 Pressure Systems
6.10 Documentation
6.11 Audit System
6.12 Independent Checks
6.13 Major Hazards
6.14 Quality Management
6.15 Safety Management
6.16 Policy
6.17 Organization
6.18 Planning
6.19 Measurement
6.20 Control
6.21 Audit
6.22 Process Knowledge
6.23 Safety Strategies
6.24 Human Factors
6.25 Contractors
6.26 Safety Management Systems
6.27 Process Safety Management
6.28 CCPS Management Guidelines
6.29 Regulatory Control
6.30 STATAS
Chapter 7. Reliability Engineering
7.1 Development of Reliability Engineering
7.2 Reliability Engineering in the Process Industries
7.3 Definition of Reliability
7.4 Meanings of Probability
7.5 Some Probability Relationships
7.6 Some Reliability Relationships
7.7 Failure Distributions
7.8 Reliability of Some Standard Systems
7.9 Reliability of Complex Systems
7.10 Markov Models
7.11 Joint Density Functions
7.12 Monte Carlo Simulation
7.13 Availability
7.14 Bayes’ Theorem
7.15 Renewal Theory
7.16 Replacement Models
7.17 Models of Failure: Strength–Load Interaction
7.18 Models of Failure: Some Other Models
7.19 Failure Behavior and Regimes
7.20 Failure Data Analysis
7.21 Reliability in Design
7.22 Reliability Prediction
7.23 Reliability Growth, Testing, and Demonstration
7.24 Maintainability
7.25 Maintenance Activities and Policies
7.26 Reliability-Centered Maintenance
7.27 Life Cycle Costing
7.28 Notation
Chapter 8. Hazard Identification
8.1 Safety Audits
8.2 Management System Audits
8.3 Checklists
8.4 Materials Properties
8.5 Pilot Plants
8.6 Hazard Indices
8.7 Hazard Studies
8.8 What If? Analysis
8.9 Event Tree and Fault Tree Analysis
8.10 Bow-Tie Method
8.11 Preliminary Hazard Analysis
8.12 Screening Analysis Techniques
8.13 Hazard and Operability Studies
8.14 Failure Modes, Effects, and Criticality Analysis
8.15 Sneak Analysis
8.16 Computer HAZOP
8.17 Human Error Analysis
8.18 Scenario Development
8.19 Consequence Modeling
8.20 Process Safety Review System
8.21 Choice of Method
8.22 Filtering and Follow-up
8.23 Safety Review Systems
8.24 Hazard Ranking Methods
8.25 Hazard Warning Analysis
8.26 Plant Safety Audits
8.27 Other Methods
8.28 Quality Assurance
8.29 Quality Assurance: Completeness
8.30 Quality Assurance: QUASA
8.31 Standards
8.32 Notation
Chapter 9. Hazard Assessment
9.1 Background
9.2 Hazard Analysis
9.3 Risk Assessment
9.4 Event Data
9.5 Fault Trees
9.6 Event Trees
9.7 Bow-Tie Diagrams
9.8 Cause–Consequence Diagrams
9.9 Dependent Failures
9.10 Expert Judgment
9.11 Rare Events and External Threats
9.12 Human Factors and Human Error
9.13 Management Aspects
9.14 Hazard Model Systems
9.15 Population Characteristics
9.16 Modification of Exposure
9.17 Injury Relations
9.18 Presentation of Results
9.19 Confidence in Results
9.20 Risk Criteria
9.21 Guide Assessments
9.22 Hazard Impact Model
9.23 Simplified Assessment Methods
9.24 Decay Relations
9.25 Hazard Warning
9.26 Computer Aids
9.27 Risk Assessment Debate
9.28 Overview
Chapter 10. Plant Siting and Layout
10.1 Plant Siting
10.2 Plant Layout
10.3 Layout Generation
10.4 Layout Techniques and Aids
10.5 Layout Planning and Development
10.6 Site Layout Features
10.7 Plot Layout Considerations
10.8 Equipment Layout
10.9 Piping Layout
10.10 Storage Layout
10.11 Separation Distances
10.12 Hazardous Area Classification
10.13 Hazard Assessment
10.14 Hazard Models
10.15 Fire Protection
10.16 Effluents
10.17 Drain Systems
10.18 Blast-Resistant Structures
10.19 Control Buildings
10.20 Portable Buildings
10.21 Toxics Protection
10.22 Modular Plants
10.23 Notation
Chapter 11. Process Design
11.1 The Design Process
11.2 Conceptual – Front End Design
11.3 Detailed Engineering
11.4 Design Assessments
11.5 Licensors, Vendors, and Contractors
11.6 Inherently Safer Design
11.7 Unit Processes
11.8 Unit Operations and Equipments
11.9 Operating Conditions
11.10 Utilities
11.11 Particular Chemicals
11.12 Particular Processes and Plants
11.13 Operational Deviations
11.14 Impurities
11.15 CCPS Engineering Design Guidelines
11.16 Integration of Safety into the Process Design
Chapter 12. Pressure System Design
12.1 Pressure Systems
12.2 Pressure System Components
12.3 Steels and Their Properties
12.4 Pressure Vessel Design
12.5 Joining, Fastening, and Welding
12.6 Pressure Vessel Standards and Codes
12.7 Pipework and Valves
12.8 Heat Exchangers
12.9 Fired Heaters and Furnaces
12.10 Process Machinery
12.11 Insulation
12.12 Overpressure Protection
12.13 Overpressure Protection: Pressure Relief Devices
12.14 Overpressure Protection: Relief System Design
12.15 Overpressure Protection: Fire Relief
12.16 Overpressure Protection: Vacuum and Thermal Relief
12.17 Overpressure Protection: Special Situations
12.18 Overpressure Protection: Disposal
12.19 Overpressure Protection: Pressure Relief Valves
12.20 Overpressure Protection: Bursting Discs
12.21 Overpressure Protection: Installation of Relief Devices
12.22 Flare and Vent Systems
12.23 Blowdown and Depressuring Systems
12.24 Pressure Containment
12.25 Containment of Toxic Materials
12.26 Pressure Systems for Chlorine
12.27 Failure in Pressure Systems
12.28 Fracture Mechanics
12.29 Probabilistic Fracture Mechanics
12.30 Failure of Vessels, Equipment, and Machinery
12.31 Computer-Aid Pressure and Pressure Protection System Design
Chapter 13. Control System Design
13.1 Process Characteristics
13.2 Control System Characteristics
13.3 Instrument System Design
13.4 Process Computer Control
13.5 Control of Batch Processes
13.6 Control of Particular Units
13.7 Computer Integrated Manufacturing
13.8 Instrument Failure
13.9 Trip Systems
13.10 Interlock Systems
13.11 Programmable Logic Systems
13.12 Programmable Electronic Systems
13.13 Software Engineering
13.14 Safety-Related Instrument Systems
13.15 CCPS Safe Automation Guidelines
13.16 Emergency Shut-Down Systems
13.17 Level of Automation
13.18 Toxic Storage Instrumentation
13.19 Notation
Chapter 14. Human Factors and Human Error
14.1 Aims of Human Factors
14.2 Role of the Process Operator
14.3 Human Factors in Process Control
14.4 Process Operator Functions
14.5 Process Operator Studies
14.6 Allocation of Function
14.7 Human Information Processing
14.8 Case Studies in Human Error
14.9 Definition of Human Error
14.10 Human Factor Approaches to Assessing Human Error
14.11 Quantitative Human Reliability Analysis (HRA)
14.12 Success Likelihood Index Method (SLIM)
14.13 Human Error Assessment and Reduction Technique (HEART)
14.14 Dougherty and Fragola Method (D&F)
14.15 CCPS Method
14.16 Other Methods
14.17 Human Factor Approaches to Mitigating Human Error
14.18 Alarm Systems
14.19 Human Error and Plant Design
14.20 Fault Administration
14.21 Malfunction Detection
14.22 Computer-Based Aids
14.23 Job Design
14.24 Personnel Selection
14.25 Training
14.26 CCPS Guidelines for Preventing Human Error in Process Safety
14.27 Notation
Chapter 15. Emission and Dispersion
15.1 Emission
15.2 Two-phase Flow
15.3 Two-phase Flow: Fauske Models
15.4 Two-phase Flow: Leung Models
15.5 Vessel Depressurization
15.6 Pressure Relief Valves
15.7 Vessel Blowdown
15.8 Vessel Rupture
15.9 Pipeline Rupture
15.10 Vaporization
15.11 Dispersion
15.12 Meteorology
15.13 Topography
15.14 Dispersion Modeling
15.15 Passive Dispersion
15.16 Passive Dispersion: Models
15.17 Passive Dispersion: Dispersion over Particular Surfaces
15.18 Passive Dispersion: Dispersion in Particular Conditions
15.19 Passive Dispersion: Dispersion Parameters
15.20 Dispersion of Jets and Plumes
15.21 Dispersion of Two-phase Flashing Jets
15.22 Dense Gas Dispersion
15.23 Dispersion of Dense Gas: Source Terms
15.24 Dispersion of Dense Gas: Models and Modeling
15.25 Dispersion of Dense Gas: Modified Conventional Models
15.26 Dispersion of Dense Gas: Van Ulden Model
15.27 Dispersion of Dense Gas: British Gas/Cremer and Warner Model
15.28 Dispersion of Dense Gas: DENZ and CRUNCH
15.29 Dispersion of Dense Gas: SIGMET
15.30 Dispersion of Dense Gas: SLAB and FEM3
15.31 Dispersion of Dense Gas: HEGADAS and Related Models
15.32 Dispersion of Dense Gas: DEGADIS
15.33 Dispersion of Dense Gas: SLUMP and HEAVYGAS
15.34 Dispersion of Dense Gas: Workbook Model
15.35 Dispersion of Dense Gas: DRIFT and Related Models
15.36 Dispersion of Dense Gas: Some Other Models and Reviews
15.37 Dispersion of Dense Gas: Field Trials
15.38 Dispersion of Dense Gas: Thorney Island Trials
15.39 Dispersion of Dense Gas: Physical Modeling
15.40 Dispersion of Dense Gas: Terrain, Obstructions, and Buildings
15.41 Dispersion of Dense Gas: Validation and Comparison
15.42 Dispersion of Dense Gas: Particular Gases
15.43 Dispersion of Dense Gas: Plumes from Elevated Sources
15.44 Dispersion of Dense Gas: Plumes from Elevated Sources – PLUME
15.45 Concentration and Concentration Fluctuations
15.46 Flammable Gas Clouds
15.47 Toxic Gas Clouds
15.48 Dispersion over Short Distances
15.49 Hazard Ranges for Dispersion
15.50 Transformation and Removal Processes
15.51 Infiltration into Buildings
15.52 Source and Dispersion Modeling: CCPS Guidelines
15.53 Vapor Release Mitigation: Containment and Barriers
15.54 Vapor Cloud Mitigation: CCPS Guidelines
15.55 Fugitive Emissions
15.56 Leaks and Spillages
15.57 Classification of Models
15.58 Notation
Chapter 16. Fire
16.1 Fire
16.2 Flammability of Gases and Vapors
16.3 Combustion Phenomena
16.4 Flammability of Aerosols
16.5 Ignition Sources
16.6 Self-Heating
16.7 Static Electricity
16.8 Electrical Equipment
16.9 Hazardous Area Classification
16.10 Ignition Models
16.11 Fire in Process Plant
16.12 Flames
16.13 Radiant Heat Transfer
16.14 Vapor Cloud Fires
16.15 Fireballs
16.16 Fireballs from Explosives
16.17 Pool Fires
16.18 Flares
16.19 Jet Flames
16.20 Engulfing Fires
16.21 Effects of Fire: Damage
16.22 Effects of Fire: Injury
16.23 Fire Protection of Process Plant
16.24 Passive Fire Protection
16.25 Fire Fighting Agents
16.26 Fire Protection Using Water: Extinguishment and Control
16.27 Fire Protection Using Water: Exposure Protection
16.28 Fire Protection Using Foam
16.29 Fire Protection Using Dry Chemicals
16.30 Fire Protection Using Vaporizing Liquids
16.31 Fire Protection Using Inert Gas
16.32 Fire Protection Using Special Methods
16.33 Fire Protection Using Portable Extinguishers
16.34 Fire Protection Applications
16.35 Firefighting in Process Plant
16.36 Fire and Fire Protection in Buildings
16.37 Fire Protection in Transport
16.38 Fire Hazard
16.39 Hazard Range of Fire
16.40 Notation
Volume 2
Chapter 17. Explosion
17.1 Explosion
17.2 Detonation
17.3 Explosives
17.4 Explosion Energy
17.5 Deflagration Inside Plant
17.6 Detonation Inside Vessels and Pipes
17.7 Explosions in Closed Vessels
17.8 Explosions in Buildings
17.9 Explosions in Large Enclosures
17.10 Explosion Prevention
17.11 Explosion Protection
17.12 Explosion Venting of Vessels
17.13 Explosion Venting of Ducts and Pipes
17.14 Explosion Relief of Buildings
17.15 Explosion Relief of Large Enclosures
17.16 Venting of Reactors
17.17 Venting of Reactors and Vessels: DIERS
17.18 Venting of Reactors and Vessels: Vent Flow
17.19 Venting of Reactors and Vessels: Vent Sizing
17.20 Venting of Reactors and Vessels: Leung Model
17.21 Venting of Reactors and Vessels: ICI Scheme
17.22 Venting of Reactors: Relief Disposal
17.23 Venting of Reactors: CCPS Work
17.24 Venting of Storage Vessels
17.25 Explosive Shock in Air
17.26 Condensed Phase Explosions
17.27 Vessel Burst Explosions
17.28 Vapor Cloud Explosions
17.29 Boiling Liquid Expanding Vapor Explosions
17.30 Explosions in Process Plant
17.31 Effects of Explosions
17.32 Explosion Damage to Structures
17.33 Explosion Damage to Housing
17.34 Explosion Damage by Missiles
17.35 Explosion Damage to Plant by Missiles
17.36 Explosion of a Cased Explosive
17.37 Explosion of an Explosive Load
17.38 Explosion Injury to Persons Outdoors
17.39 Explosion Injury to Persons Indoors
17.40 Explosion Injury from Flying Glass
17.41 Explosion Injury from Penetrating Fragments
17.42 Explosion Injury from Penetrating Fragments: Model of Gilbert, Lees, and Scilly
17.43 Dust Explosions
17.44 Dust Explosibility Characteristics
17.45 Dust Ignition Sources
17.46 Dust Explosion Prevention
17.47 Dust Explosion Protection
17.48 Dust Explosion Venting
17.49 Dust-Handling Plants
17.50 Dust Fires
17.51 Explosion Hazard
17.52 Hazard Range of Explosions
17.53 Notation
Chapter 18. Toxic Release
18.1 Toxic Effects
18.2 Toxic Substances
18.3 Toxicity Assessment
18.4 Control of Toxic Hazard: Regulatory Controls
18.5 Hygiene Standards
18.6 Hygiene Standards: Occupational Exposure Limits
18.7 Carcinogens
18.8 Dusts
18.9 Metals
18.10 Emergency Exposure Limits
18.11 Gas Toxicity
18.12 Gas Toxicity: Experimental Determination
18.13 Gas Toxicity: Physiological Factors
18.14 Gas Toxicity: Toxicity Data
18.15 Gas Toxicity: Vulnerability Model
18.16 Gas Toxicity: Major Industrial Gases
18.17 Gas Toxicity: MHAP Studies
18.18 Gas Toxicity: Chlorine
18.19 Gas Toxicity: Green Book Relations
18.20 Gas Toxicity: Probit Equations
18.21 Gas Toxicity: HSE Dangerous Dose
18.22 Gas Toxicity: Combustion Gases
18.23 Ultratoxic Substances
18.24 Plant Design for Toxic Substances
18.25 Toxic Gas Detection
18.26 Toxic Release Response
18.27 Toxic Release Case Histories
18.28 Toxic Release Risk
18.29 Chlorine Hazard Assessment
18.30 Other Chemicals Hazard Assessment
18.31 Hazard Assessment Methodology
18.32 Notation
Chapter 19. Plant Commissioning and Inspection
19.1 Plant Commissioning
19.2 Plant Inspection
19.3 Pressure Vessel Inspection
19.4 Pressure Piping Systems Inspection
19.5 Non-Destructive Testing
19.6 Materials Verification
19.7 Pressure Testing
19.8 Leak Testing and Detection
19.9 Plant Monitoring
19.10 Performance Monitoring
19.11 Condition Monitoring
19.12 Vibration Monitoring
19.13 Corrosion Monitoring
19.14 Acoustic Emission Monitoring
19.15 Plant Monitoring: Specific Equipment
19.16 Pipeline Inspection and Monitoring
19.17 Notation
Chapter 20. Plant Operation
20.1 Inherently Safer Design to Prevent or Minimize Operator Errors
20.2 Operating Discipline
20.3 Good Operating Practices
20.4 Operating Procedures and Instructions
20.5 Emergency Procedures
20.6 Handover and Permit Systems
20.7 Operator Training
20.8 Plant Patrols
20.9 Modifications to the Process
20.10 Operation and Maintenance
20.11 Start-up and Shut-Down
20.12 Start-up of Refinery Units
20.13 Shut-down of Refinery Units
20.14 Operation of Fired Heaters
20.15 Operation of Driers
20.16 Operation of Storage
20.17 Operational Activities and Hazards
20.18 Sampling
20.19 Trip Systems
20.20 Identification Measures
20.21 Exposure of Personnel
20.22 Security
20.23 Notation
Chapter 21. Equipment Maintenance and Modification
21.1 Management of Maintenance
21.2 Hazards of Maintenance
21.3 Preparation for Maintenance
21.4 Isolation
21.5 Purging
21.6 Cleaning
21.7 Confined Spaces
21.8 Permit Systems
21.9 Maintenance Equipment
21.10 Flanged Joints
21.11 Hot Work
21.12 Tank Cleaning, Repair and Demolition
21.13 On-Line Repairs
21.14 Maintenance of Particular Equipment
21.15 Equipment Removal
21.16 Deteriorated Equipment
21.17 Some Maintenance Problems
21.18 Major Shut-Downs
21.19 Maintenance Information Systems
21.20 Spares Inventory
21.21 Computer Systems
21.22 Modifications to Equipment
21.23 Software and Network Maintenance
21.24 Managing Change
21.25 Some Modification Problems
21.26 Major Plant Expansions
21.27 Maintenance Optimization
21.28 Maintenance Personnel Training
21.29 Notation
Chapter 22. Storage
22.1 General Considerations
22.2 API Standards
22.3 Petroleum Product Storage
22.4 Storage Tanks and Vessels
22.5 Selection of Materials for Storage Tanks
22.6 Storage Layout
22.7 Venting and Relief
22.8 Fire Prevention and Protection
22.9 LPG Storage
22.10 LPG Storage: Pressure Storage
22.11 LPG Storage: Refrigerated Storage
22.12 LNG Storage
22.13 LNG Storage: Refrigerated Storage
22.14 Hydrogen Storage
22.15 Toxics Storage
22.16 High Toxic Hazard Materials: CCPS Guidelines
22.17 Chlorine Storage
22.18 Ammonia Storage
22.19 Ammonia Storage: Pressure Storage
22.20 Ammonia Storage: Refrigerated Storage
22.21 Ammonia Storage: Stress Corrosion Cracking
22.22 Other Chemicals Storage
22.23 Bunds
22.24 Underground Storage Tanks
22.25 Glass Reinforced Plastic Storage
22.26 Filling Ratio
22.27 Loading and Unloading Facilities
22.28 Loading and Unloading Facilities: Particular Chemicals
22.29 Drum and Cylinder Storage
22.30 Warehouses
22.31 Warehouses: Particular Chemicals Storage
22.32 Storage Case Histories
22.33 Storage Risk
22.34 LPG Storage Hazard Assessment
22.35 LNG Storage Hazard Assessment
22.36 Ammonia Storage Hazard Assessment
22.37 Storage Tanks Protection from Terrorism
22.38 Notation
Chapter 23. Transport
23.1 General Considerations
23.2 International Codes
23.3 Classification, Packaging, and Labeling
23.4 Transport Containers
23.5 Road Transport
23.6 Road Transport Environment
23.7 Rail Transport
23.8 Rail Transport Environment
23.9 Road and Rail Tunnels
23.10 Waterway Transport
23.11 Pipeline Transport
23.12 Marine Transport: Shipping
23.13 Marine Transport: Regulatory Controls
23.14 Marine Transport: Ports and Harbors
23.15 Marine Transport: Shipboard Fire and Fire Protection
23.16 Marine Transport: Liquefied Flammable Gas
23.17 Marine Transport: Chemicals
23.18 Marine Transport Environment
23.19 Air Transport
23.20 Transport Emergency Planning and Spill Control
23.21 Transport Case Histories
23.22 Transport Risk
23.23 Transport Risk Assessment
23.24 Road Transport Risk Assessment
23.25 Rail Transport Risk Assessment
23.26 Tunnel Transport Risk Assessment
23.27 Pipeline Transport Risk Assessment
23.28 Marine Transport Risk Assessment
23.29 Transport Hazard Assessment: Comparative Risks
23.30 Security Issues
23.31 Notation
Chapter 24. Emergency Planning
24.1 Introduction
24.2 On-site Emergency Planning
24.3 Resources and Capabilities
24.4 Developing an Emergency Plan
24.5 Training
24.6 Essential Functions and Nominated Personnel
24.7 Declaration and Communication of the Emergency
24.8 Evacuation
24.9 Cooperation and Drills
24.10 Public Relations
24.11 Off-Site Emergency Planning
24.12 Transport Emergency Planning
24.13 Emergency Planning for Disasters
24.14 Spectators
24.15 Emergency Incidents
24.16 Recovery
24.17 Regulations and Standards
Appendix A NFPA Publications
Chapter 25. Personal Safety
25.1 Human Factors
25.2 Occupational Health
25.3 Occupational Hygiene
25.4 COSHH Regulations 1988
25.5 Dust Hazards
25.6 Asbestos Dust
25.7 Ventilation
25.8 Skin Disease
25.9 Physico-Chemical Hazards
25.10 Ionizing Radiation Hazards
25.11 Non-Ionizing Radiation Hazards
25.12 Machinery Hazards
25.13 Electricity Hazards
25.14 Other Activities and Hazards
25.15 Personal Protective Equipment
25.16 Respiratory Protective Equipment
25.17 Rescue and First Aid
25.18 Ergonomics
25.19 Notation
Chapter 26. Accident Research
26.1 Definition of Accidents
26.2 Classification of Accidents
26.3 Accident Causation
26.4 Accident Models
26.5 Accident Proneness
26.6 Human Error
26.7 Social Factors
26.8 Impact of Safety Culture
26.9 Safety Training
26.10 Major Hazards Research
Chapter 27. Information Feedback
27.1 The Learning Process
27.2 Incident Reporting
27.3 Operation Monitoring
27.4 Accident Models
27.5 Accident Investigation
27.6 Fire Investigation
27.7 Explosion Investigation
27.8 Accident Investigation: CCPS Guidelines
27.9 Public Accident Inquiries
27.10 Organizational Memory
27.11 Case Histories
27.12 Information Exchange
27.13 Accident Databases
27.14 Safety Performance Measurement
27.15 Safety Performance Monitoring
27.16 Near Miss Reporting
27.17 Education
27.18 Teaching Aids
27.19 Notation
Chapter 28. Safety Management Systems
28.1 Safety Culture
28.2 Safety Organization
28.3 Safety Policy Statement
28.4 Safety Representatives
28.5 Safety Committees
28.6 Safety Adviser
28.7 Safety Training
28.8 Safety Communication
28.9 Safety Auditing
28.10 Safety Rating
28.11 Management Procedure to Implement Required Changes to Establish Proper Safety
28.12 Use of Tools for Better Safety Management Systems
Chapter 29. Computer Aids
29.1 Expert Systems in Process Engineering
29.2 Combination of Process Safety with Design and Optimization
29.3 Computer Aided Process Engineering
29.4 Pipework and Fluid Flow
29.5 Unit Operation and Equipment
29.6 Databases, Bibliographies, and Indexes
29.7 Compliance Management
29.8 Computational Fluid Dynamics
29.9 Hazard Identification
29.10 Pressure Relief Devices Sizing
29.11 Hazard Assessment Systems
29.12 Virtual Training
29.13 Transport
Chapter 30. Artificial Intelligence and Expert Systems
30.1 Knowledge Representation
30.2 Databases
30.3 Prepositional Logic
30.4 Predicate Logic
30.5 Non-Deductive Inference
30.6 Production Rules
30.7 Non-classical Logics
30.8 Uncertainty and Inconsistency
30.9 Probabilistic Reasoning
30.10 Fuzzy Logic
30.11 Programming Languages
30.12 Structured Knowledge
30.13 Search
30.14 Matching and Pattern Recognition
30.15 Problem-Solving and Games
30.16 Vision
30.17 Natural Language
30.18 Planning
30.19 Learning
30.20 Inductive Learning
30.21 Neural Networks
30.22 Graphs, Trees, and Networks
30.23 Directed Graphs
30.24 Expert Systems
30.25 Expert Systems: Some Systems and Tools
30.26 Qualitative Modeling
30.27 Engineering Design
30.28 Process Applications
30.29 Project Aids
30.30 Process Modeling
30.31 DESIGN-KIT
30.32 Process Synthesis
30.33 Plant Design: Synthesis
30.34 Plant Design: Analysis
30.35 Expert Systems: Some Process Systems
30.36 Fault Propagation
30.37 Hazard Identification
30.38 Hazard Identification: HAZID
30.39 Hazard Identification: Enhancements
30.40 Fault Tree Analysis
30.41 Fault Tree Synthesis
30.42 Fault Tree Synthesis: FAULTFINDER
30.43 Operating Procedure Synthesis
30.44 Process Monitoring
30.45 Fault Administration
30.46 Malfunction Detection
30.47 Notation
Chapter 31. Incident Investigation
31.1 Preface
31.2 General Investigation Concepts
31.3 Evidence Issues
31.4 The Investigation Team
31.5 Identifying Root Causes
31.6 Recommendations, Reports, and Lessons Learned
31.7 Management System for Investigations
Chapter 32. Inherently Safer Design
32.1 Introduction
32.2 Definitions
32.3 History of Inherently Safer Design
32.4 Strategies for Process Risk Management
32.5 Inherently Safer Design Strategies
32.6 Inherently Safer Design Conflicts
32.7 Measuring Inherent Safety Characteristics of a Process
32.8 Inherently Safer Design and the Process Life Cycle
32.9 Implementing Inherently Safer Design
32.10 Inherent Safety and Chemical Plant Security
32.11 Inherently Safer Design References
Chapter 33. Reactive Chemicals
33.1 Background
33.2 Technical
33.3 Program Management
Chapter 34. Safety Instrumented Systems
34.1 Introduction
34.2 Examples of SIS
34.3 SIS Standards
34.4 Layers of Protection Analysis (LOPA)
34.5 Level of Automation
34.6 Design
34.7 Verify
34.8 Operate
34.9 Maintain
34.10 Test
34.11 Special Applications
Chapter 35. Chemical Security
35.1 Introduction
35.2 Security Management System
35.3 Security Strategies
35.4 Countermeasures and Security Risk Management Concepts
35.5 SVA Methodologies
35.6 Defining the Risk to be Managed
35.7 Overview of an SVA Methodology
35.8 Chemical Facility Anti-Terrorism Standards (CFATS)
35.9 Chemical Security Assessment Tool (CSAT)
35.10 Inherently Safer Technology (IST)
Chapter 36. Safety Culture
36.1 Introduction
36.2 Definition of Safety Culture
36.3 Developments in Safety Culture
36.4 Evaluating Safety Culture
36.5 Implementing Safety Culture
36.6 Conclusion
Chapter 37. Metrics and Performance Measurements
37.1 Introduction
37.2 Different Types of Metrics
37.3 Choosing Useful Metrics
37.4 Implementing the Selected Metrics
37.5 Application of Metrics with Examples
37.6 Future Efforts for Generating Industry-Wide Metrics
37.7 Conclusion
Chapter 38. Benchmarking in the Process Industry
38.1 Introduction
38.2 Benchmarking Outline
38.3 Possible Barriers and Resolutions for Benchmarking
38.4 Examples of Benchmarking Activities
Chapter 39. Liquefied Natural Gas
39.1 LNG Properties
39.2 LNG Industry
39.3 LNG Hazards
39.4 LNG Spills Experiments and Modeling
39.5 Safety Measures in LNG Facilities
39.6 Regulatory Authorities and Regulations
Chapte
- Edition: 4
- Published: August 3, 2012
- Imprint: Butterworth-Heinemann
- Language: English
FL