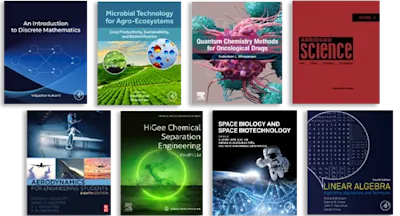
Laser Additive Manufacturing of Metallic Materials and Components
- 1st Edition - December 9, 2022
- Author: Dongdong Gu
- Language: English
- Paperback ISBN:9 7 8 - 0 - 1 2 - 8 2 3 7 8 3 - 0
- eBook ISBN:9 7 8 - 0 - 1 2 - 8 2 4 1 8 3 - 7
Laser Additive Manufacturing of Metallic Materials and Components discusses the current state and future development of laser additive manufacturing technologies, detailing… Read more
Purchase options
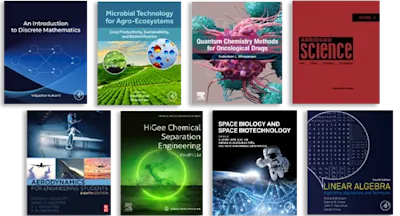
Laser Additive Manufacturing of Metallic Materials and Components discusses the current state and future development of laser additive manufacturing technologies, detailing material, structure, process and performance. The book explores the fundamental scientific theories and technical principles behind the elements of laser additive manufacturing, touching upon scientific and technological challenges faced by laser additive manufacturing technology. This book is suitable for those who want to further “understand” and “master” laser additive manufacturing technology and will expose readers to innovative industrial applications that meet significant demand from aeronautical and astronautical high-end modern industries for low-cost, short-cycle and net-shape manufacturing of structure-function integrated metallic components.
With the increasing use of industrial applications, additive manufacturing processes are deepening, with technology continuing to evolve. As new scientific and technological challenges emerge, there is a need for an interdisciplinary and comprehensive discussion of material preparation and forming, structure design and optimization, laser process and its control, microstructure and performance characterization, and innovative industrial applications, hence this book covers these important aspects.
- Highlights an integration of material, structure, process and performance for laser additive manufacturing of metallic components to reflect the interdisciplinary nature of this technology
- Covers cross-scale structure and performance coordination mechanisms, including micro-scale material microstructure control, meso-scale interaction between laser beam and particle matter, and macro-scale precise forming of components and performance control
- Explores fundamental scientific theories and technical principles behind laser additive manufacturing processes
- Provides innovation elements and strategies for the future sustainable development of additive manufacturing technologies in terms of multi-materials design, novel bio-inspired structure design, tailored printing process with meso-scale monitoring, and high-performance and functionality of printed components
Part I. Designed Multi-materials for Additive Manufacturing
2. Nanoscale ceramic reinforced Al-based nanocomposites by laser additive manufacturing
3. Novel carbonaceous nanomaterial (Carbon nanotubes/ Graphene) reinforced Ti- and Al-based nanocomposites by laser additive manufacturing
4. Ceramic particle reinforced Ni-based composites with gradient reinforcement/matrix interface by laser additive manufacturing
5. In-situ ceramic toughened Ti–Ni/ Ti-Al intermetallics-based composites by laser additive manufacturing
6. Hard-to-process W-based material modified by nanoparticles processed by laser additive manufacturing
Part II. Tailored Processes for Additive Manufacturing AM
7. How powder particles are deposited before AM
8. How powder particles absorb laser energy during AM
9. How powder particles are melted by laser during AM
10. How the molten pool is formed during AM
11. How the melt flows and solidifies during/after AM
Part III. Novel Structures for Additive Manufacturing AM
12. Laser AM of lightweight reticulated shell structure with elevated compressive property inspired by diving bell of water spider
13. Laser AM of novel porous structure with highly expanded helicoidal organization and high strength and toughness inspired by Cancer Pagurus’s claw
14. Laser AM of bi-directionally corrugated panel structure with shock absorption and resistance function inspired by mantis shrimp
15. Laser AM of gradient porous structure with thermal management and protection function inspired by Norway spruce stem
16. Laser AM of novel lattice structure with compression-induced-twisting (CIT) function inspired by front wing of beetle
Part IV. High-performance/Multi-functionality and High-end Applications of Additive Manufacturing
17. Forming accuracy property: Stress, deformation and dimensional accuracy control for selective laser melted Ti- and Al-based light-alloy components
18. Strength and toughness property
19. Corrosion performance
20. Oxidation performance
21. High-end applications and case studies
22. Summary and outlook of future directions and perspectives for additive manufacturing research and development
- Edition: 1
- Published: December 9, 2022
- Language: English
DG